I hope last week’s introduction to bulk material handling got you all thinking up amazing hacks, and we’ll soon be reporting on DIY Cap’n Crunch Robots galore. This week we’ll look at how to measure particle sizes, separate particles, and even grind them up when you need to.
Measuring Material Properties
Last week we talked about cohesive strength. Bulk material behaves somewhere between a solid and a liquid — if you’ve done your homework, it flows down the funnel just fine. But if you haven’t, it sticks together and holds up the rest of the material. Cohesive strength is the measure of how much weight the material at the bottom of the funnel can hold up.
You can get a rough measurement by packing material in a box with a square hole at the bottom. One side of the hole should have a retractable slide. Slowly withdraw the slide, making the hole rectangular. Material will bridge over, and then at some point a larger chunk will fall out. This is about the size of the minimum opening that will not arch, and a practical measure of the material’s cohesive strength.
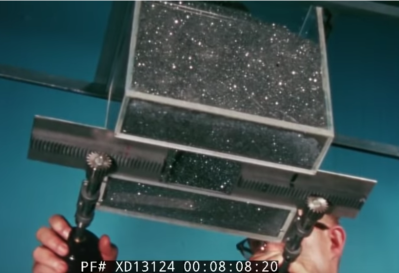
Many materials cohere better when wet. Dry a sample in a microwave to determine the percent moisture by weighing it before and after.
Cohesive strength is closely allied to shear strength. If you want to measure shear strength, cut two 1 cm wide rings of 5 cm diameter PVC pipe, stack them, pack with material, put a disk atop the material and load it, then drag the top ring off the bottom with a spring scale. The force per unit area is the shear strength at that pressure. If it starts packing you’ll see it in the curve.
Packing factor is another useful measurement. Gently shake material to fill a rigid container and weigh it. Now empty the container and refill, packing the material as hard as you can with a length of 1” dowel. Reweigh, and the ratio of the two weights tells you how well the material packs.
Real bulk material is almost always made up of particles of varying sizes, shapes, and compositions. Dirt is particles of different kinds of mineral and organic matter varying from outright rocks to sub micron clay particles. If you’re having problems, getting a graph of material size distribution can be helpful.
For particles above about 75 μM, you can measure the sizes with sieves. If you want to be fancy, they sell nice sets of metal sieves with wire mesh in the bottom. Screen assortments are cheaper. Below 75 μM, you have to use a hydrometer. This is messy and takes a while, but does work.
The idea is to mix the material with soapy water and then use a hydrometer from the auto parts store to measure the density. The particles fall out by Stokes law, big ones first. Stokes law is just that the drag force on a sphere is proportional to the square of the radius. Mass will go up as cube of the radius, so large particles fall faster than small ones. As they fall out, the density of the fluid decreases. This page describes how to do it, and this page has a handy calculator for interpreting the results.
Grinding
You can also change the size of particles in your mix. If particles are too large, they can be crushed or ground. You can separate by size and only grind some of the sizes or discard some of the material. There’s a whole science to grinding. The finer you grind, the harder it gets to grind. Cosmetics and pharmaceutical companies are full of grinding experts.
In general, there are three ways to make something smaller – crush it, cut it, or hit it.
Crushing is straightforward. Use rollers or jaws, a rolling pin or a rock crusher. Don’t overlook the vise. A jaw crusher only crushes particles larger than the jaw space, useful to make a certain size. Rock crushers have a complex motion (video) that should nonetheless be easily imitated by a hacker project. Amateur/hobby gold prospectors have an accessible community.
Crushing action in rollers only works until the particle is small enough that the surface of the roller deforms instead of the particle. Stones have been used to crush grain into flour for most of history.
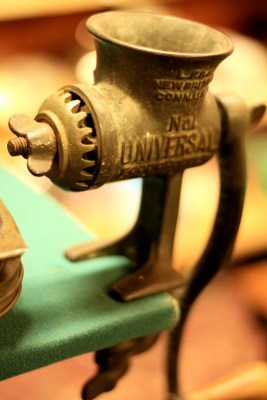
Cutting is best for soft things, like gummy worms, and tough things (video.). Make sure the cut material has an easy path out. Think of an old fashioned kitchen meat grinder. .
If you want small particles, you need an impact grinder. A coffee mill or blender works by striking the particle with a fast moving impactor. This can be a blade – useful if the material first needs to be cut up, as in a coffee mill – or blunt. Many industrial mills use two pivoting weights on a shaft, and this unit just uses chains (video).
Another impact mill is the ball mill. Rotate a drum on it’s side with steel balls and the material. The balls travel up the side, then fall back down, striking the material.
All these work by fracturing the material. What if you’re trying to powder something that doesn’t fracture, say rubber O rings? For that, there’s cryogenic grinding.
Many rubbery materials are really glasses — materials that are a gloppy liquid at a higher temperature, often brittle at a cool temperature, and soft in-between. The glass you’re probably thinking of is a brittle, breakable material at room temperature, but at high temperature is a liquid. The transition point is the ‘glass transition temperature’.
So what about our O rings? If they’re natural rubber their transition point is about -70° C. Below that temperature they’re brittle and can be ground up. Unfortunately, grinding is going to put heat back in. So consider grinding slowly – some labs grind biological materials like skin samples with a special mortar and pestle cooled beforehand with liquid nitrogen. Just be sure everything in contact with the material has been cooled, and use a thick walled container with lots of thermal mass.
Separating Wheat From Chaff
Sometimes you have a mix and need to separate it. Your roommate dumped all the gummy bears and all those weird ginger candies into a bowl or whatever. Last week we introduced particle segregation as a bad thing. But when you want to un-mix a mixture, it can be a good thing. Any of the techniques from last week can be an aid.
Sieves and screens work to separate by size. They clog unless the material keeps moving over them. One simple way to do this is to flow the material over sieves on a slanted board, finest sieve first. Another is to mechanically shake the screen. Paper filters are just fine screens, and do clog.
A trommel is a slowly turning cylinder with walls of different sized screens along it’s length. Material is fed into the fine screen end and slowly moves towards the other.
Stokes law provides another way to separate materials as we saw above. Make an upward air draft in a vertical pipe. Deliver the material into the pipe part way up. Materials with more drag than weight will go up, larger materials will go down. You can use the air speed to control the size of particle. An industrial machine called an air classifier does this with higher velocity air blowing material into the rim of a spinning set of blades.
It could be the air (or another gas) you want to remove. There are a couple ways to do it. The first is the cyclone familiar to wood shops. The second is even simpler – inject the air/material mix into the top of a tall, slender container with a tube that extends about halfway into the container. Let the air out from an outlet pipe in the roof. The air flow expands, slows down, and the material falls out.
You can just blow the material sideways – the age old system of threshing wheat works this way. Wheat comes from the plant with a husk, you beat it with a flail to loosen the husk, giving you wheat grains and chaff mixed. Put the mix on a blanket and have four peasants toss it repeatedly. The chaff blows away in the wind.
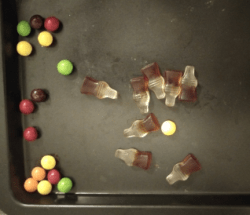
A very sensitive separation technique is inertial separation. Here’s a mix of gummy colas and jelly beans. We separated them by tilting and gently shaking the sheet. A material moves on a sheet by staying in place until the acceleration is more than some critical value. Then it rolls or slides.
If your material is dirt or such, run a magnet through it. There’s iron ore and bits of human generated iron in a lot of soil. It can get into motors and such. If you need it out run the material past magnets. An eddy current separator uses AC magnetic effects to do the same with nonferrous metals.
You can also segregate materials by dissolving them. A mixture of table salt and white sand would seem impossible, but if you stir it into water, then decant and boil off the water, the salt and sand can be recovered separately. But we think we’re veering into chemistry now, and we should stop.
Next time we’ll finish up by looking at controlling movement: building gates and contraptions that move your bulk material without clogging up.
Interesting stuff, thanks!
If you’re dealing with something like those cola bottles or rubber parts, you might just want to up and frigging cheat, and sprinkle a bunch of corn starch (cornflour) in there to stop the buggers sticking.
I feel like there’s so much material here (pun intended) that we could have articles about each of the subjects in here. For example ball mills. I had a coworker who wanted to make one to make finely powdered aluminum and iron oxide. Or how they are used in mining operations to turn mineral into powder prior to extraction things. I bet there’s been some neat homemade ball mills made over the years.
Aluminum powder and iron oxide powder? I assume not simultaneously.
The aluminum powder on it’s own is the real problem if fine enough, when it’s quite granular, it’s kinda hard to light. But super fine, could go up with a spark maybe.
What I want is a DIY device to separate out fine powder from sand and glass bead used in sand blasting and bead blasting. Keep the larger/unused particles and sort out the fine dust and blasted away dirt, rust, paint etc for disposal – without using a filter that constantly clogs.
couple ways:
Do the hydrometer separation thing on a large scale. Get a big drum, make a cone the diameter of the drum, and leading to a capped pipe inside (if it’s all inside you don’t need to make a water tight special shape container). Fill the drum with water + laundry detergent + material stirring like hell. Then let it sit quietly overnight. It’ll segregate, I bet. Drain the water, take the pipe cap off, slip out the wet slug, the beads will be in one layer. slice out that layer and discard the rest. Rinse the detergent out of the beads & dry.
Second way, pour material down a chute in front of a fan at chest height and onto a tarp. The reusable beads will end up at one place on the tarp, the trash all around.
Either method might need a couple repeats to get really clean bead media.
If it’s a mix of broken and unbroken bead media, inertial separation should work well. pour it down an inclined unfinished pine board. Adjust the slant of the board until the round beads roll down, the trash sticks.
I was almost finished with my Cap’n Crunch Robot but I had pulled an all-nighter working on it and I was getting hungry for breakfast. Unfortunately I had used all of the cereal building the robot and I was too tired to go to the store so I…well…ate the robot. Oh well. I’ll have to buy more next time but cereal is becoming such an expensive raw stock material.
Anyways, I do like articles like this that addresses basic techniques that aren’t always obvious.
https://en.m.wikipedia.org/wiki/Elutriation is a wonderful thing
Speaking of grinding, this flour milling technique was invented here locally at Washington State University: https://en.wikipedia.org/wiki/Unifine_mill
Coffee should be ground with a mill, not blades, to get a more consistent particle size. Otherwise the smaller particles overextract during brewing.
Many materials are also sensitive to heat – coffee and flour being two examples – and can be damaged by the high heat of some grinding methods.
And some are affected by static, or sensitive to sparks
There was another milling method that we looked into when I was in grad school (analytical chemistry), air impact or something like that. Streams of coarser material suspended in air impacted one another to make smaller particles. The reason we were interested is that there would be little or no change in composition of the material, which is what you want in analysis, and the material didn’t need to be suspended in a liquid.
Grinding by most other methods can change the composition of a material enough to skew the analysis, sometimes quite badly. But the air impact device was way too expensive for our program.
We did have a McCrone Micronizing Mill for small samples that could be suspended in water. It was an extremely efficient miniature ball mill. Particle size of grind-able material could be reduced from sand-size to a micrometer or so in about 15 minutes.
Oh, there’s also “atomizing” (bad name) to create fine particles. A stream of argon impinges on molten aluminum, magnesium, etc., to create tiny rounded particles—down to a few micrometers—that solidify and are then graded for size. That kind of aluminum is used widely as pigment in metallic paints and as filler for epoxies and the like.