Additive manufacturing (AM) has been getting a lot of attention over the years, with its use in construction a recurring theme. Generally this brings to mind massive 3D printers that are carted to construction sites and assemble entire homes on the spot. That’s the perspective with which a recent ZDNet article by [Rajiv Rao] opens, before asking whether AM in construction is actually solving any problems. As [Rajiv] notes, the main use of such on-site AM construction is for exclusive, expensive designs, such as ICON’s House Zero which leans into the extruded concrete printing method.
Their more reasonable Wolf Ranch residential homes in Texas also use ICON’s Vulcan II printer to print walls out of concrete, with a roof, electrical wiring, plumbing, etc. installed afterwards. Prices for these Wolf Ranch 3 to 4 bedroom houses range from about $450,000 to $600,000, and ICON has been contracted by NASA to work a way to 3D print structures on the Moon out of regolith.
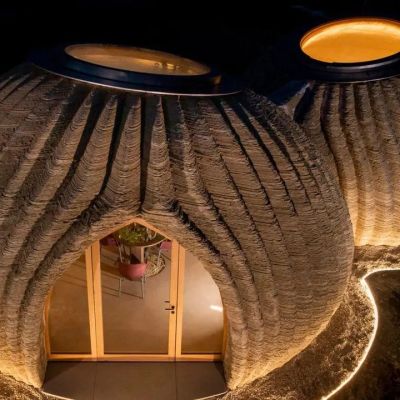
Naturally, none of these prices are even remotely in the range of the first-home buyers, or the many economically disadvantaged who make up a sizable part of the population in the US and many other nations in the Americas, Africa, etc. To make AM in construction economically viable, it would seem that going more flatpack and on-site assembly is the way to go, using the age-old pre-fabrication (prefab) method of constructions.
This is the concept behind the University of Maine’s BioHome3D, which mainly uses PLA, wood fiber and similar materials to create modules that contain insulation in the form of wood fiber and cellulose. These modules are 3D printed in a factory, after which they’re carted off to the construction site for assembly, pretty much like any traditional prefab home, just with the AM step and use of PLA rather than traditional methods.
Prefab is a great way to speed up construction and already commonly used in the industry, as modules can have windows, doors, insulation, electrical wiring, plumbing, etc. all installed in the factory, with on-site work limited to just final assembly and connecting the loose bits. The main question thus seems to be whether AM in prefab provides a significant benefit, such as in less material wasted by working from (discarded) wood pulp and kin.
While in the article [Rajiv] keeps gravitating towards the need to use less concrete (because of the climate) and make homes more affordable through 3D printing, AM is not necessarily the panacea some make it out to be, due to the fact that houses are complex structures that have to do much more than provide a floor, walls and a roof. If adding a floor (or two) on top of the ground floor, additional requirements come into play, before even considering aspects like repairability which is rarely considered in the context of AM construction.
What is the actual problem that they are trying to solve with 3D printed houses?
Concrete slabs aren’t that expensive .. and only small part of budget what goes building a house.
It’s just tech fetishism
It’s tech fetishism and concrete companies trying to sell more concrete.
Homes in the UK are already built by AM, brick by brick.
AM? The malevolent AI in I Have No Mouth, and I Must Scream?
Rising lumber costs
Cutting, framing, hanging drywall, taping, plastering, sanding.
Thats a lot of labor cost, a significant percentage of what goes into building a house.
I dont think extruded concrete is the answer though.
Automated minecraft houses using mortarless Cement Stabilized Compressed Earth Blocks is where I think its at.
https://youtu.be/-ltWsDYjYeo?si=42h_tek7kOWfIJSb&t=132
HadrianX is using a different block type than the lego like MyIB blocks I prefer but Id much rather live in their constructions than the cement extrusions so popularly shown when talking 3d printed houses.
https://youtu.be/xDDbc-Kwn_U?si=KzoriJvgfgcZApAp
doesn’t help when a government wont let you log in a place where saplings pop up like dandelions. because of the environment. lets ignore the fact that wood structures are a good way to sequester carbon.
Time is a big bad wolf. The sprawling suburbs of america were designed to crumble under its breath. We do not build for longevity, We build for the constant and continued profit of Fat Cat developers and the construction industry.
The second hand housing industry in america has become an investors paradise of flippers buying up worn down modest homes of deteriorating condition, sinking tens of thousands into rebuilding them, and selling them for hundreds of thousands more than they were originally worth. Wash rinse repeat.
Traditional stick-built homes have a lifespan of around 50-60 years. Brick structures are built to last 100 years or more depending on their maintenance. Research undertaken by Adrian Bown from Leeds Metropolitan University found that brick structures can have a lifespan of 500 years or more. Cement stabilized compressed earth blocks remove bricks main maintenance requirement, repointing, or the removal and replacement of degrading mortar.
I lived in Japan for a while, it was crazy every single building was solid concrete or brick. No wood structures.
I actually stayed in a place that was built before WWII
“Time is a big bad wolf.”
You have no idea how accurate this saying is, or do you? 😮
When I hear of different construction types, I always have to think of the story of the three little pigs and the big bad wolf.
There was a straw house (tent), a wooden house and a brick house. And all houses but the brick house had been blown away. Literaly.
I couldnt edit, Thanks HAD.
My sister just informed me that according to the condo associations notice that the repointing that was done earlier this summer was NOT the third, it was only the second.
In the UK wood construction (as in 4×2 stick framed houses, not the more advanced stuff) is for sheds, outhouses and garden offices. Not the actual house.
If the structure price is a small portion and doesn’t matter, then why americans building and living in cardboard houses?
“I dont think extruded concrete is the answer though.”
Me neither, I think that concrete as such is not the final solution.
It’s just that western world hasn’t cone up with something better yet.
Steel-concrete has a flaw in its structure, and it degenerates over time until it collapses with little to no warning.
Especially if temperature changes occur, like by the different seasons each year.
By comparion, stone or brick houses can last for generations.
They may seem expensive, but that’s relative considering their longevity. Some of these buildings last longer than their country.
The structure is being stabilized by the outer walls, also, which is better than the concept of steel/concrete buildings that use an single inner structure for this.
The fact that traditional buildings can carry their own weight makes them more robust. Damages on the outer walls can be spotted and be repaired more easily. An inner core can’t really be fixed, because it’s always being under pressure. I’m merely speaking as layman here, of course.
Never seen a structure that’s not carrying its own weight. Maybe because the resistance of materials usually show that a material supports more compressive forces than traction forces.
A concrete + steel rod can live for centuries, but you have to pay for that, by using stainless steel rod and not plain oxidizing steel. There are bridges over the sea with those that costed 30% more expensive to build but unlike the other that collapsed, are still perfectly fine (so in the end, they saved 70% of the cost of rebuilding a new one).
Stainless steel still exhibits stress corrosion cracking and galvanic corrosion, and welding it drives off the chromium and other additives from the heat affected zone turning it more like regular steel or worse. It’s a difficult material to work with and design with correctly because you can too easily ruin its properties.
https://www.machinemfg.com/stainless-steel-corrosion/
Depends on the concrete. Look at the pantheon in Rome, which as far as I can recall is concrete but has some volcanic particulates which have helped it stay up for 1900 years.
But having said that there are buildings with high mica content that aren’t lasting 5 years.
The concrete used in Roman Empire is special.
It’s very good, better than we have now in some ways. And it doesn’t depend on extra steel rods, either.
Researchers are still trying to figure out the recipe for the ancient concrete mixture.
The Pantheon is also wider at the base than the crown (oculus).
For the roof they also used lighter stones in the concrete mix (pumice?).
No doubt the last houses to be 3d printed will be done so with an improved process from the first.
Even if it never turns out to be a practical improvement, having followed that path and learned what there is to learn from it is a benefit.
The cost of construction workers, and the lack of construction workers (you would think the first problem would solve the second problem eventually but there’s a general lack of good workers).
Concrete (extruded) is cheap, bricks are not cheap and are currently limited in supply in the UK which is trying to increase to 300,000 houses a year, primarily brick skin construction.
The lack of affordable housing doesn’t need techbro solutions, the answer is obvious. Change zoning laws in areas experiencing shortages to allow for more multifamily and dense new housing construction!
Or you know don’t import 10% of the population every four years
Or live together as a family instead of leaving home as soon as you turn 18, having kids and then splitting up and using twice as many houses, and dumping your parents in care.
the rest of the world
Look up what a reverse mortgage is sometime. Might also be a good idea to prevent hedge funds from going around systematically buying up all properties on the market as well.
“The American dream is bad actually, live with your parents forever and then of course we’ll make fun of you for living in your mom’s basement”
Okay fine I won’t vote for people who talk like this and just flat out tell me that my living standards should continue to decline, why should I go against my own interests? YIMBYs GFY
The US is one of the very few countries in the world where you don’t have to be a citizen to buy property…..
Think how much availability that would free up without people from China buying houses/apartments in NY they never set foot in solely as a means to move money away from the CCP reach. (Not to mention Russia and everyone else.)
@Sword
https://www.marketplace.org/2024/02/09/foreign-investors-are-cooling-on-u-s-commercial-real-estate/
To be fair, that “American dream” really is just what it is, a dream.
Back when I was little, I had been fascinated by this great land far, far away. Like so many kids from here.
Most of our pop culture, western principles seemed to have stemt from there.
But as I grew older, this fassade seemed to become more and more brittle.
That’s why I shelved the idea of visiting the US. The reality would probably break my heart.
Everything is centered around profits and paying bills to merely being able to survive in this country.
It’s very far away from that “American dream”; sense for justice and freedom that we heard about. America is rather a company, like Disney, it seems.
It produces content, but doesn’t believe in it. It just makes things up that sell well.
And everything that is social, human friendly is seemingly being seen as a form of socialism or communism.
Which for us living here in other countries is a strange thought.
We don’t want any form of dictatorship, after all, but rather live a peaceful life in our countries.
Also, we have a different understanding of freedom, it seems.
Here in old Europe, we think of freedom as having human rights and not being under dictatorship, rather than the personal freedom.
The latter seems to be a big thing in America. Everything starts with “I”. I have the right to do this, this is my something etc.
While the duties seem to be secondary, somehow.
I rarely see comments on the net were Americans tell that they have a certain duty as a citizen.
Like for example, having the duty to help others in an emergency.
Or having the duty to provide first aid to a wounded citizen.
I can’t recall reading such things.
Hm. This self-centerism is maybe also a part of US nature, not sure.
Here in Europe, it’s not about the individual being “succesful”, but rather society moving forward.
I mean, okay, we have careers and some of us work hard for them.
But what we really seek is happiness in life.
Money is more of an instrument to make things real and to get away with the financial worries.
But the US is different here, maybe. It’s not bad people, but pressure from society.
The country believes that the individual success of each person is the answer to a great nation. Each to his own. Eye for eye, tooth for tooth.
So if a child moves back home to mama and papa, it’s shameful, it’s seen as a failure.
That’s what I have learnt from internet, at least.
Here in Europe it’s not like this per se. Not that we don’t have this concept, but it feels not that that strong maybe, I would say.
The neighborhood doesn’t judge you if you moved back, I mean.
All in all, society in Europe is more like “one for all and all for one”, as the musketeers said. That’s how the healtcare system works in principle.
The Swiss even has it as an motto sort of. Unus pro omnibus, omnes pro uno.
Also, moving back isn’t same thing as never moving out. If you come back, it’s not seen or felt as failure.
Because you had made it one time before, at least.
Also, just because you moved back now doesn’t mean that you can possibly never move out again.
To society, it’s just seen as a temporarily phenomenon at first moment. It’s not being judged so hard, thus. It simply happens, rather.
Some parents are even happy if they seen their grown children again.
It helps them to overcome loneliness and the problems of age.
Sometimes it’s vice versa, even. Parents move to their grown children and they may take care of the grandchildren in return.
Which is great, because children often miss out on having grandparents or seing them on regulary basis.
Having friendly grandparents is good for their mental health and their development.
In reverse, grandchildren keep the old people young both at heart and physically.
In Japan, it’s even more common that parents live with their children together.
Living space is rare and costly, so that even succesful children decide to stay at their parent’s.
If they can stand each others, there’s no problem. There isn’t that feeling of shame.
Disclaimer: Speaking under correction.
In fiscal year (FY) 2020, ~628,300 immigrants became lawful permanent residents. With a population of 329.5 million
In fiscal year (FY) 2021, ~809,000 immigrants became lawful permanent residents. With a population of 332 million million
In fiscal year (FY) 2022, ~969,380 immigrants became lawful permanent residents. With a population of 333.3 million
In fiscal year (FY) 2023, ~878,500 immigrants became lawful permanent residents. With a population of 343.47 million
Might want to double check your beliefs they are off by an order of magnitude.
And before you argue thats only Legally naturalized citizens, various groups estimate that the TOTAL population of undocumented immigrants in the U.S. ranges from only 10.9 million to 16.8 million.
As of 2022, the foreign-born population consisting of anyone living in the United States who was not a U.S. citizen at birth, including naturalized U.S. citizens, lawful permanent residents (immigrants), temporary migrants such as foreign students, humanitarian migrants such as refugees and asylees, and unauthorized migrants TOTALLED 45.3 million or 13.7% of the nation’s population,
Thats ALL pretty far from your claim of 10% every 4 years.
How many new houses were built in that time that these people could afford?
Housing costs are what the market can bear and the market depends upon whether one wants to live in a particular location, what kind of employment one can obtain, and the cost of living in an area which is also related to those factors. Via a channel on YouTube that visits large to very small towns in our (huge) great plains and similar areas, I’ve seen beautiful homes that cost one third of what they’d cost where I live.
“What the market can bear” is somewhat elusive, given that people and companies buy houses on loans they can or will never pay back. That’s what caused the housing bubble last time around, and it’s no different today either – they debt is just passed on and tossed around like a hot potato until someone defaults.
I think using additive manufacturing at the factory to make pre-fab modules makes more sense than trying to use it at the construction site. With the latter, you essentially have to move the entire factory to the site. This might make sense if you’re building many buildings, but probably not for building a single one.
Now, whether using additive manufacturing vs. other methods at the factory is better is a more difficult question. If the blueprints call for rectangles, then perhaps AM doesn’t have much advantage. However, if you want Gehry-like structures, probably AM can shine.
This only makes any sense if (as in the lunar example) the materials are sourced locally.
As for cost – woah, a 3-4 bed home is too expensive for a first time buyer? Wow, what a surprise. Those are family homes. And those costs in the article are less than many conventional 3-4 bed homes in the UK – and definitely less than a new build. (Though I suspect if they were built here they’d cost more). The cost of housing is mostly based on the land, not the house cost. It’s a supply and demand issue.
Asides from the funky shapes and novelty I don’t see a point. It’s not usually the walls of a house that makeup the biggest part of the price, it’s the equipment: electrical, plumbing, finishing, windows etc. This doesn’t really solve a problem, but introduces the need for a pretty high precision foundation to print on (like a level print bed).
Bingo. That’s why it costs so much more to redo a kitchen or a bathroom compared to a bedroom – way more infrastructure involved.
Forst layer, as in first brick layed by?
The assumption is labour costs are lowered having a 3D concrete robot do the fabrication. (cue magical unicorn).
The reality is finishing work and basics for electrical and plumbing, like Thomas says- are the major expense.
They need to create a Lego block standard for house construction. Only then would there be innovation and competition giving cost improvements.
But new house construction is a mega industry, billion$ so nobody wants that at the builder-level.
Using seacans is out there but not popular because, well, it’s a steel box.
it doesn’t matter how you build your house if people still cant afford them.
What about hire-purchase? You pay a rent for 30 years or so and afterwards it’s your property or the property of your family.
You children and grand children might still consider living in that house after you, err, have moved.
I think you mispronounced ‘mortgage’
No, that’s the filthy commie socialist model.
The government builds the housing, you rent it. If you rent it for 30 years you get to keep it.
“Civilised” countries of course stopped doing this years ago, if indeed they ever started.
Haha, I suppose that was meant in a humorous way.
If not, please let me explain.
“No, that’s the filthy commie socialist model.”
Hm. It’s rather a model used in countries with social democraties.
Socialist/communist countries didn’t like the idea of private property.
Everything was owned “by the people” or the regime.
Which wasn’t much of a difference in practice, maybe.
I’m thinking here about E. Germany mainly, which was socialist on paper mostly.
In reality, the citizens living there were maybe more capitalist than citizens from other Germany.
That’s at least how it looks like, I haven’t spoken to many of them yet to draw a final conclusion.
““Civilised” countries of course stopped doing this years ago, if indeed they ever started.”
From point of view of Europe or rest world, the US is not a role model for a first-world country and barely “civilised”.
If it was, human life would be valued over money and things like public transport and healtcare would matter. Guns would be limited to soldiers and police who are properly trained to handle them.
That country maybe once was leading about fifty to hundred years ago, but it hadn’t kept up with progress very well.
It’s rather the opposite now. Many concepts and the condition of the country is something we would associate with a third world.
Or fourth world, maybe, if the rating would go as low.
The condition of the infrastructure, health care, education, public transport and so on is way behind China or NK.
And then there’s the privately operated media which is just silly, with little content of useful information.
People watching TV or listening to radio apparently get little information about what really moves the world.
Here in my country, the TV and radio landscape is completely different. It’s not perfect and leaves a lot to be desired, but forms of propaganda are actively being prevented, also because of history.
In many way, me and others feel genuinely sad for this place.
It’s seemingly all about money and labour, with little life quality.
The cheaply made houses and infrastructure rots away, because it has a life expectancy of merely 50-60 years. So things built in the 60s now begin to fall apart. Everywhere, simultanously.
Japan has a similar problem with its work culture maybe, except that the people living there know how to build houses and things.
They never sacrified quality by contrast. They take pride in doing things right. That’s why they don’t tip, for example.
It would be an affront to take money for good sevice, because it should be just natural to give your best. We all should learn from this, I think.
Disclaimer: Speaking under correction here. Everything was written with best intentions and to best knowledge, but to err is human.
With houses that are built to last only 40-50 years, your children will inherit a worthless dump.
It does matter figuring out why building a house has such high costs nowadays.
Of course it’s all the fat from the home builders and tradesmen. It makes up a big part of the economy for many ountries.
I have to laugh, they try to upsell you on flooring, appliances etc. – even electrical outlets “You want Decora? Oh that costs extra” and it’s cheaper to go to Home Depot and buy the fancy light fixtures, switches and outlets yourself. A total ripoff from the home builder. They’ll add +30% markup on top of the contractor’s +30% markup.
This is an entire construction ecosystem. Home Depot stock is a steady ramp up to the moon.
It would be basic math to calculate the savings with 3D printing a house. It sounds promising but has a lot of resistance to it.
I was quoted £3000 including 2 weeks labour to have fitted wardrobes in my bedroom. Cost me £500 from ikea and took me 4 days.
Their labour costs vs what they pay labourers is eyewatering but hey, got to keep the company director’s boat shiny!
I am not against IKEA at all, but fitted wardrobes vs not-exactly-fitting IKEA stuff is the game changer. Unless the builders and furniture retailers agree on some size standards the on-demand built things could be expansive.
And you got Ikea quality rather than actual custom built-ins. There is a huge difference. Actual wood vs particle board for starters.
for 3q it was also ikea ;) do not dream :D
STL?
Hm. This company is from Houston, Texas?
If so it might be worth a try, actually, considering how the average house in the US is said to be built.
Because, it might be a better alternative to these “dog house” constructions they normally use (if that information is true; are crossbeams a thing yes/no?).
A 3D printed house might be not on par to a traditional brick/wood house construction from Germany here,
but still better than building a contraption using huge tooth bricks, plasterboards and a stapler. Stability wise, I mean. PS: Please excuse my ignorance here, it’s hard to separate facts from stereotypes here.
I wonder if all these materials used will end up like the albatrosses known as wind turbine blades.
If we’re looking for sustainable affordable housing, may I propose the humble mud hut? It can be built from local materials, releases no CO2 into the atmosphere (unless the thatched roof burns down), and requires few enough skills to maintain that the average homeowner could (probably) manage it. Think about it: after millions of years of evolution, the human species can finally advance to the level of being able to construct our own shelter. The birds, beavers, and ants will be so proud of us.
And again I propose mortarless Compressed Earth Blocks. Stabilizing with 5-10% cement will add durability and weather resistance in rainy climates.
https://youtube.com/shorts/nU68HSXII_g?si=mYDvzgthRMYv3Ujp
You made a serious reply to a joke post, but I’ll bite. Cement-stabilized dirt is just really weak concrete. I’ve made it, gotten excited about it, etc., but then I left it outside for a year and now it’s pockmarked from weathering and covered in moss. Seeing that, I wouldn’t like to build my house from it. Furthermore, with the energy required to make 10% of the weight of the building from cement, you could instead fire the remaining 90% of the dirt into proper bricks (at a much lower temperature than a cement kiln) and just use those with lime mortar (also fired at relatively low temperatures) as people have already been doing for millennia. If you’re still really excited about stacking giant legos, you can even make the bricks self-aligning. The mortar is still important though, it stops the bugs from getting in.
You clearly dont know about CSEB blocks. While you are correct stabilized mud is poor concrete, CEB blocks hold their own without cement due to high compression. This technologt is more similar to bite sized rammed earth construction. The addition of cement spares you the hassle of having to facecoat the wall to protect the blocks in areas that experience high rainfall.
5-10% cement, which isnt always necessary, is not going to be more energy intensive than firing a house full of bricks, nor the significantly larger amount of cement in the mortar used to bind them.
Cseb blocks use a clay slip or a bead of adhesive neither of whch suffer the effects of weathering that fat mortar joints do, nor do they require costly repointing, solving your imagined insect issue.
There are mud houses that are over 100 years old; it’s no problem; just put a roof on top of it. I helped a friend renovate one a few years back. If no water will go to dry mud bricks then it will be fine. It is that easy …. no need to reinvent the wheel
Hard to find copius suitable mud in downtown Los Angeles
Imagine if a young Henry Ford went to investors and said he wanted to construct a factory at a person’s home, then build a car for them in that factory, then disassemble that factory and bring it to another person’s home and do it again.
Investors would’ve laughed him out the door.
As they should with dreams of doing the same with homes, when they could be built on an assembly line and shipped around the country for a fraction of the cost.
Modular homes, on average, cost anywhere from $90-$120 per square foot. Site built homes, on average, cost about $150-$250 per square foot. So you arent wrong about there being a savings.
However they arent really “shipped around the country”, For the most part, the markets that modular home manufacturers serve are limited in their proximity to the supplier’s factory. Shipping modules over distances longer than a couple of hundred miles runs the risk of damaging the product, and can be prohibitively expensive.
Edison did! 3 thousand plus parts for the mold and one big pour. Whole house made on site. 60 some still extant in Gary Indiana. He went gaga for concrete and mono-form design.
House Zero at 1700 Riverview St. Austin, TX:
https://maps.app.goo.gl/7YFMLUjp6yHd7UC38
with more details on street view.
Nice looking, but I won’t buy a flat roofed house.
This is a solution looking for a problem – why not design them with AI and sell them on the blockchain for the ultimate TechBro pointlessness.
Pre-fabricated or factory built houses are a much more practical solution, those who have watched a bit of Grand Designs will have seen multiple versions go up over the years and it’s always fast – usually the groundworks are prepared in advance (which you have to do for any house) and then a couple of trucks turn up & the parts are craned off & into place in a matter of hours, it’s not unusual for a 2-storey house to go up in a couple of days.
A lot of stuff can be pre-installed at the factory (faster & easier than on a building site) and then just hooked up in-situ and you’ve got less (or certainly no more) fettling & finishing to do than any other construction method.
You have a load of stuff that can be done by machine in a factory – sections pre-cut, aligned on jigs, etc. – as well as the rest of it being done more easily by folks who aren’t working outdoors in the weather or up ladders etc.
dopóki nie będziemy drukowac ścian razem z instalacjami, z kanalizacją, prądem, gazem, internetem , wywietrznikami i mnóstwem rzeczy które sa potrzebne dopóty nic z tego nie będzie.
drukowanie może zakładac elementy prefabrykowane, ale musi dawać nowa jakość. łatwiejsze budowanie piwnic (np. kilka kondygnacji z wyjazdami) łatwiejszą integrację i wymianę dachu, łatwiejsze instalowanie mediów. Bez tego to jest po prostu bzdurka bez żadnego znaczenia.
I want to see a 6 axis pick&place brick-laying machine. Something that can build stuff that is too intricate for humans to do quickly.
Perhaps something that could insert rebar and electrical or plumbing fixtures and windows as appropriate?
Something that actually makes a house, instead of just a shell.
Something that makes something that justifies the technology, instead of just existing to put humans out of work…