A decade ago, buying a custom-printed circuit board meant paying a fortune and possibly even using a board house’s proprietary software to design the PCB. Now, we all have powerful, independent tools to design circuit boards, and there are a hundred factories in China that will take your Gerbers and send you ten copies of your board for pennies per square inch. We are living in a golden age of printed circuit boards, and they come in a rainbow of colors. This raises the question: which color soldermask is most popular, which is most desirable, and why? Seeed Studio, a Chinese PCB house, recently ran a poll on the most popular colors of soldermask. This was compared to their actual sales data. Which PCB color is the most popular? It depends on who you ask, and how you ask it.
But first, let’s examine the rainbow of PCB options. Seeed’s Fusion PCB service offers six different colors of soldermask for every PCB order: white, black, red, blue, green, or yellow. These are the colors you’ll find at most board houses, and remain constant with few exceptions; OSH Park only offers purple, but you can get purple from a few other manufacturers. There are rumors of orange soldermask. Matte black and matte green are generally the seventh and eighth colors available from any PCB manufacturer. We’ve seen pink PCBs in the wild, as well.
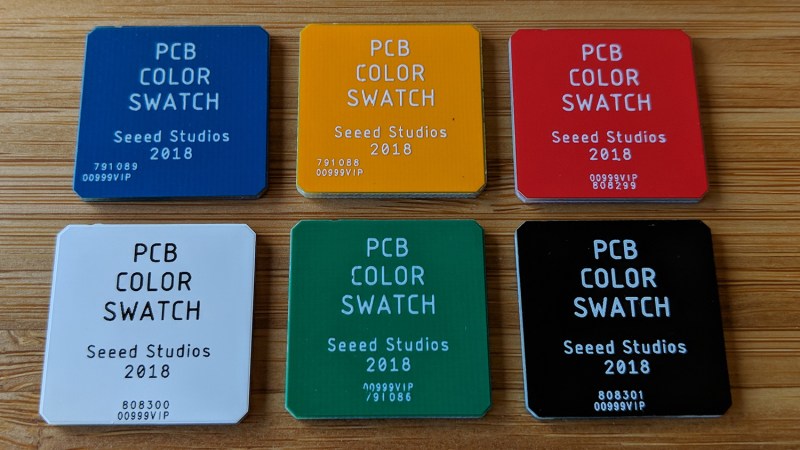
Seeed’s service, unlike most others, doesn’t include an upcharge for colors other than green, so in some sense it makes the ideal experiment. In their poll, Seeed asked customers what color soldermask was their favorite. Black soldermask topped the list, closely followed by blue. Green picked up third, red was a bit behind green, and white and yellow combined barely made a dent in the numbers. But when you look at actual Seeed Fusion PCB orders, a significant difference is revealed. By far, the most popular color of soldermask ordered on Seeed’s service is green, comprising nearly half of all orders. Black was the second-most popular color ordered, followed by blue, red, white, and yellow.
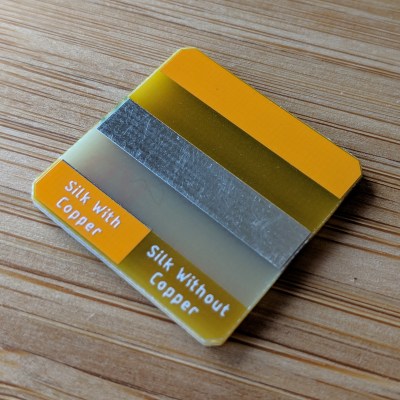
The fact that there’s a difference between what people say they want and what they will buy should come as no surprise to anyone. The reason for this difference is worthy of discussion, though. The traditional color for soldermask is green because it performs better and because ‘slightly different shades of green’ lend themselves better to visual inspection than other colors.
Green is also the default color when ordering through Seeed’s Fusion service, and if someone just wants a working PCB, they probably don’t care too much about the color. This would easily explain its higher rank among all orders, but its lower rank among people who had color preferences.
However, the popularity of green soldermask says nothing about the relative popularity of black and blue versus yellow soldermask. Why are blue and black soldermask so popular when white and yellow soldermask is so unpopular? While traces are exquisitely visible on yellow, I would suggest that the fact that Seeed’s yellow PCBs come with white silkscreen makes it difficult to read any names or part numbers on a yellow PCB. White soldermask, however, looks really good and provides a great contrast for the black silkscreen. It’s just nearly impossible to follow a copper trace.
So, we’re opening up the comments. What color do you use for your printed circuit boards? Do you go for pure performance, or do artistic concerns weigh in? If you’ve ever done anything artistic with yellow soldermask, what was it? Does picking green for your soldermask mean you’re lazy? This is an Ask Hackaday, so put your thoughts below.
a decades a bit of a stretch, in 2010, you could goto seeedstudio and get 10 pcs for 5$, maybe 20 years ago is more accurate…
*source: waybackmachine
i feel like PCBs started becoming inexpensive and easy to order right around the time BatchPCB came out, which looks like it was late 2005. https://web.archive.org/web/*/batchpcb.com
Why wold anyone pay a higher price for a cdifferen colored mask?
Never ordered anything else that green.
Brand recognition, for one. I buy all kinds of China-special boards but I can tell at a glance exactly which ones came from Sparkfun. They’re bright red!
Depends on purpose. Barobo robots use white soldermask because the white enclosures are partially transparent, so anything but white would be ugly for the final product. On an LED based board, you may want a black soldermask if the board is being used in a dark environment (like DJ/dancefloor lighting). And of course, as wartoaster mentioned, brand recognition. I have seen an orange board for a company with a brilliantly colored orange logo, so even though there board is never seen by the end customer, they made orange their standard mask color out of pride for their company.
When designing a battery management system, I used red for anything connected to the battery and green for isolated circuits. I have also used different colors for different revisions, to make it less likely I pick up a back level prototype board that might be on the bench.
I get a lot of them in purple.
If orange soldermask is real I think I may be obliged to find an idea that needs six boards so I can make a rainbow.
… or just stick to green (or purple if it’s OSH Park), it’s not really a big deal for most things.
I always thought that Aisler should do orange, instead of their weird olive shade of green.
It’s real, take a look at Freedom K82 board for example.
Black and gold are too sexy to have them enclosured hiding in box, so i am using laser plexiglass cuting service for making simple boxes with help of some black nylon spacers. Green one is for prototyping or for PCB fully enclosured in standard operating state.
I use red for non-production, development, or pre-production boards, green for production. That way I know at a glance whether a board is prod-ready or not.
I work for a company that does the same thing. Prototype revs start with red w/white solder mask, then go to blue w/white solder mask and so on and so forth. All production boards are always green w/white solder mask.
A minimal revision on the board, and instead of changing the PCB color, we change the solder mask color.
EDIT: Not solder mask… silk screen. Ouch.
Whatever you do, do don’t get purple. Whenever I open up a piece of gear and find a purple PCB there is a >90% chance that the design of the board is crap. To a lesser degree the same is true for black/white, chances are that if the EE team decided to make the board black with gold plating they are spending too much of their time trying to make the board look pretty and not enough time making it work correctly. I see a lot of that in audiophile type stuff, and a lot of ‘adafruit style’ dev boards.
I’d extend this and say if I find a purple PCB I know the producer is paying too much for PCBs and I got ripped off because they don’t know how to use a proper fab.
I think black and white just look bad. Interestingly though, I recently attended a conference and the badge was a PCB in white and the board layout was fairly poor.
Are you trying to say that picking a different color will magically improve your PCB design skills? I’m not sure it works that way.
>chances are that if the EE team decided to make the board black with gold plating they are spending too much of their time trying to make the board look pretty
Or the boss wanted the boards he shows investors to look pretty ;)
Could it simply be that a lot of purple boards are early iteration / amateur designs printed at OSH park?
For the Enigma Machine external lampfield I make it a point to order the boards from OshPark. The board price can be absorbed in the product price and American manufacturing is supported.
Blue for production runs, green for works in progress. Ostensibly green is the best color due to trace visibility.
Some day I will do matte black gold plated boards.
For trace visibility green is very good but definitely the best color is yellow.
Green was the traditional color and the most common so it’s usually the cheapest but from experience yellow is superior for pcb inspection.
With a yellow solder mask track visibility is excelent at any angle and even under component shadows and poor lighting.
And the solder mask opening silhouettes are still clearly delineated.
Really my first choice always is yellow when the price difference is small but if not green is always a good alternative.
The bonus with yellow solder mask is that both black or white silk screens work very well.
Depending of the manufacturer, and when the tones are light, red and blue also may be ok if you fancy them butthese colors usually are too dark. The rest are just, no.
Agreed. Before even reading the article, my first reaction to the picture at the top was that the yellow really made the traces stand out. Not sure white silkscreen is great on it, but it’s certainly readable. If I was making a badge I’d go with yellow mask and white silk.
I would like yellow more but I’m always a little disappointed by its lack of vibrancy. I wish it were brighter and more saturated.
You need to leave more copper on them — they are bright and vibrant where the copper is, and meh on the naked FR4. So make sure you pour those grounds, it will also make the board better electrically.
Also, I love yellow (with black silkscreen) because I can then add diagonal stripes everywhere…
Orange Soldermask is available from http://ragworm.eu
We use the following:
Red – Prototype
Green – Through Hole, Yes we still do Through hole
Blue – SMT
White – Specialty, Same size board and shape as another board, Just for a special application. I think we have 2 boards in White.
The colors help us identify what is on the line at any given time and also makes sure prototypes are not accidentally sent out to a customer.
I wish there was a brighter shade of blue available widely, something like the light blue bean uses. Also orange and bright green would be nice. Purple and transparent can be found sometimes, and there is also matte black.
Wondering if there is logic for best contrasting color schemes for most or is just a customary act event? https://en.wikipedia.org/wiki/Complementary_colors
Also, enjoying the learning curve (not) of the range of PCB’s having differences regarding the silk screening of the components layout info. Mainly, I’ve found that the different types of capacitors were… or are… still confusing though I might be grasping the logic for at least the electrolytic’s (SMD’s seem more confusing). Reading may be more of a designer mood for the situation. Say for instance some caps have a solid or striped half of a circle being the positive when there is no “+” sign silk screened. Though I’ve read where the opposite is true when the “+” sign is silk screened.
I’ve been salvaging components to practice desoldering and soldering… so I have a range of examples aiding in the experience.
I’m guessing maybe there is more logic like for decoupling versus coupling capacitors where maybe a polar electrolytic is used for decoupling and there is no polarity sign silk screened or maybe is like a mood thing noted elsewhere? Anyone have any examples or maybe the silk screening has a IEEE standard or an article regarding would be great… even for each component. :-)
Tantalum caps are like this:
https://en.m.wikipedia.org/wiki/File:Polarity-rectangular-chips.jpg
Diodes are the opposite.
LEDs are inconsistent.
In general: best practise is to set the marking according to the datasheet and package symbol.
Given what month it is, I’d like to find a place that offers pink, light blue, and white.
back in the olden days I used to get radio kids with the single sided brown PCBs made of phenolic paper, and had no solder mask on them. But they were silk screened on the back side in black.
I meant “radio kits”.
anyways I wonder if anyone still produces those ugly brown PCBs. Seems like they would still be really cheap to mass produce.
(to restate a misplaced reply in another post..)
Actually, I would like to take a moment to suggest Far Circuits to anyone who may be interested in having ready made PCB’s of popular projects for very very cheap. This isn’t for those folks in production of their own boards as much as folks interested in having access to a huge amount of boards from radio kits and projects dating back decades. It is an excellent resource that some may not be aware of. Thank you for bringing up your question, jonmayo, of the elegant old school.
Apparently those old brown PCBs were often FR1 or FR2, compared to modern FR4? Economies of scale might make it not actually cheaper.
I still see them in cheap toys.
FAR Circuits makes a ton of that stuff, still the same kits and quality and mimeographed documentation you would’ve gotten 30 years ago. Apparently they’re aiming at a clientele whose expectations haven’t advanced…
I seriously made the exact comment about far circuits but for some reason it didn’t show up…. I may have inhaled far too much solder fumes in my days… thanks for mentioning that great company! I’ve only made a single order with them in the past decade but they are exactly what came to my mind as well :)
That website! We don’t need/want any of this fancy images or colour or fonts. Cool kits though, and updated on the 2nd of June, so they must still be on the go. http://www.farcircuits.net
They are phenolic boards, still used in cheap stuff. These days, the holes are often punched rather than drilled.
Even 15+ years ago I worked at a small company that would order red for prototypes, yellow for pre-production, green for production, blue for tooling/utility boards. Black and white were still rare colors. Then James had to throw purple into the pop-culture mix…
Not sure how using Seeed Studio data is an accurate representation of soldermask usage/preference, but for the point of the article, I am glad “depends on who you ask” was included in the text. From a broader perspective, you are missing numerous colors.
Also, from a volume production perspective, there are many fab houses that do not charge additional cost for colors other than green. A fab house I use charges the same for green, blue, red, white, and black. They can also do yellow, pink, purple, and orange, but at an added cost unless the volume is high enough to justify their setup costs of the ink. They also routinely do two color boards. It is common for them on LED boards to do black/no silk on the LED side and green/white silk on the opposite side where the rest of the components are placed.
In places where clients have used multiple colors, the common theme is:
Red: Proto
Blue: Pre-prod or pilot
Green: Production
For specific markets, colors have been:
Automotive: Black
LED: White or Black depending on the final install environment
You can do multiple mask colors on one side but it can wreak havoc at your fab house so cost will go up considerably. I have always wanted to a board that looks like the American flag. Red and blue soldermask with white silk.
What place can you get orange done!??!?!
i think yellow is actually orange
Bay Area Circuits is the company that I know can do orange.
Not long after graduation (back when pterodactyls were used as drone platforms), employer told me to set up our internal board shop to use excess capacity for external customers. Other than two colors (yellow and green), we had no NRTL recognition for any other colors, so had to turn away some potential customers. A major appliance maker’s board order was rejected because we could not provide the required colors AND the required CTI, flame rating, etc. Later, the same appliance maker did a big recall (unusual for that era) for both fire and shock hazards. Root cause was the PCB.
While less common these days, you need to verify that ‘different’ colors are still NTRL-recognized PCB materials if your circuit exceeds the definition of an LPS (see NEC article 725, or UL1310, or CSA No.223).
This just gave me an idea to go and make some PCB coasters, I bet that would look splendid in black with enig finish :)
If you are using extremely fine pitch parts, just use green. We had weird problems with a micro-BGA part in development until we switched the soldermask to green per the chip manufacturer engineer’s recommendations. Apparently board houses can keep much better tolerances on the apertures with green soldermask. No idea why other than that’s what the most common color is so process wise it’s really dialed in.
https://www.youtube.com/watch?v=hpiIWMWWVco
I am partial to white soldermask / black silkscreen myself…
https://pbs.twimg.com/media/De4Yk3xVMAAPvIi.jpg
Me too
https://war.rui.nz/tmp/20170329_VIA-top-side.640.jpg
i prefer green because then its most easily recognised as a PCB
I think this is the thinking behind the prevalence of green soldermask. Everybody knows that “real” PCBs are green. I’ve never mistaken a PCB of any color for anything else, though, so I’m not sure what the point is.
What the heck is this sentiment against OSHPark? They produce quality boards at competitive prices. Where else can you get 2Oz 0,8mm boards with those via sizes and free shipping cheaper?
If I see an OSHPark board I see that the person appreciates quality.
It’s not anti-OSH, it’s anti-OSH-customer. Selling a product using PCBs that came from one of the more-expensive (especially for quantity) prototype houses speaks of amateurishness.
Every PCB I’ve done for personal use, I had no use for more than three copies. How many prototypes do you need? When I only need one or two, the other cheap fab aggregators beat the price only when you consider the price per copy – they cost the same or more for the minimum order. And that purple soldermask is just beautiful with ENIG traces and white silkscreen. It inspires me to carefully file off the breakoff tabs. I’d never bother with that for green boards.
All of that would change if I came up with a project that needed six or eight copies – I’m pretty cheap. I draw the line, though, at ordering from a place that calls themselves “dirtypcbs”. What does it say about the pride you take in your work, when you use a name like that? It tells me not to expect much.
I have to “defend” DirtyPCB, name will be clear when you know background. The allow you to panelize as many different design as you wish on single board, silkscreen color change doesn’t have additional fee. Plus additional services like 3d print or laser cut acrylic is prototype gold.
That said, OSHPark quality is unbeatable for now.
I like purple
Most of our production boards are green. In volume orders, it’s still a bit cheaper than any other color at our supplyer. And for automatic optical inspection it’s much better than some other colors to find real defects and have the least false positives. From what i’ve heard, black PCBs are a nightmare for AOI. We do have some boards in white tho, for lighting applications where we use the soldermask to bounce around some more photons.
Huh. Theoretically I like the idea of different colors for different production status. In reality, as a hobbyist (or at best an OSHW “publisher”), that’s “someone else’s department.” I like the way black and white *look*, but the visibility sucks if you’re debugging boards. I’ve used yellow several times, mostly for it’s “Different” look, but I’ve decided it’s actually pretty ugly :-(
Sparkfun took red. Green and Blue are just fine, are more often cheap, and they sort of make a statement: “Hey, it’s a PCB – what do I care what color it is!”
I’m waiting for a fab to offer two soldermask layers – multiple colors, or double black for when you want to really obscure things…
(It would be nice to be able pick silkscreen color independent of soldermask color. “Black on green/blue/red” would be a bit more subtle…)
This was my first board made in a board house, in 2007:
https://www.flickr.com/photos/svofski/1058464559/
It did cost money, but comparable to what I pay now. I think one of “a decade ago” or “a fortune” is a bit of exaggeration.
Love the curved traces!
“Yellow is a terrible soldermask color” – I disagree. For me yellow with black silk is the best combination for visibility. Also, black silk seems to be higher resolution in the fabs I used.
I always wonder HOW “default” things came to be “default”. Why green? Way back when the use of solder masks on PCBs began was there just one manufacturer of the solder mask liquid who only offered green which everyone then came to expect when others offered solder mask liquid for sale or was there some other reason?
Was it a milspec requirement for some reason since military/aerospace users are usually the first adopters of initially expensive technologies?
The answers to my question:
Why are printed circuit boards usually green?
https://www.quora.com/Why-are-printed-circuit-boards-usually-green
Some of the comments below that give what I suspect is are the best answers:
The original masks used a base resin that was a “brownish yellow” and a hardener that was a deeper muddy brown. When they were mixed together they created a honey brown color that apparently not very appetizing. They tried adding red pigments but it became a rusty adobe color and using blue simply made it a darker brown. None of them were very appealing colors. Since the laminate materials at the time had a green hue they tried adding more yellow and some blue and ended up with an acceptable green color. It became the standard color we are still using today.
… many lines of inspection still rely on workers to see with the eyes. Green doesn’t hurt your eyes.
… green is the best background color for contrast against white silk-screened text on the surface of the PCB in different environmental conditions.
… blue and black because they are doped with cobalt and carbon, has a certain conductivity, so there is a risk of short-circuit, green PCB more environmentally friendly, high temperature environment will not release toxic gases.
is it true that green is less toxic than other color PCB?
I’m surprised I haven’t seen any mention of different colored FR-4. I would say my favorite PCB aesthetic is black FR-4 with transparent solder mask. Sure, it isn’t as practical/affordable as good ol’ green, but it’s nice to see all the copper so clearly.
I remember reading about a study where subjects rated yellow pencils higher than other paint colors even though the paint color was the only difference. I can’t search up a citation though. The same might apply to green PCBs.
As for myself, I’m too cheap to spring for a different color if there’s an upcharge.
Still today I find white soldermask quality out of the prototyping fabs to be quite hit and miss. Yet my customers always want white pcbs for anything an investor might see. Mostly green is the best quality in my experience although I’m very impressed with the quality of some black and red Dev boards out of elecrow.
I noticed that specifying ENIG plating results in a better soldermask, so that might be a factor. For prototypes I hand solder I’ve switched to OSP finishing and seeing some very good boards out of allpcb recently. Superfast too.
You pay peanuts you should expect less than perfect.
even this is VERY old i’ll leave few words… :D
I’m into diy audio with a lot of red Wima and blue ero block capacitors, “gold” “green” and red electrolytic caps, blue TH 1% resistors and black op-amp ic’s soooo best Looking contrast to all these is WHITE soldermask with black silk!
I don’t care if i don’t see traces below white bcs I simply know that my PCB will work 100% ;)