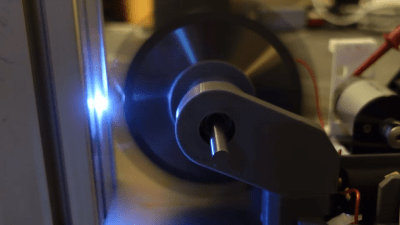
Combat robots come in all shapes and sizes, with regulating authorities often using weight limits to create a level playing field for competitors. [Hans Jørgen Grimstad] is building a robot to compete in a 4 kg class, and made some interesting design decisions to that end.
4 kg is not a lot of weight to play with. When considering the motors needed to propel the robot and the batteries needed to run everything, there’s then precious little weight left for weapons systems and armor plating.
Thus, in an effort to make the most of the weight limitations, [Hans] decided to use carbon fiber for the robot’s outer shell. The method used is a simple wet layup in a mold. We’d be supremely interested to see how this armor holds up in competition, versus more typical choices like aluminium and steel.
Other interesting features include a belt-driven saw, which [Hans] tests with his hands mere inches away and the robot’s motors powered up. Don’t do this if you value your fingers. This is paired with a high-voltage discharge taser module. When the saw gets close to another robot, it may cause sparks to jump to the enemy, damaging its electronics in the process. It’s something we haven’t seen too often, as such measures are actually banned in some contests.
Diehard enthusiasts in the battle robot community will likely have fierce opinions on many points of the design; have it out in the comments. It’s certainly not the first carbon-fiber bot, but it’s nice to see the fancy material being thrown in the ring.
We’ve seen other designers innovate, too, such as this remarkably successful walking robot build. Video after the break.
I don’t think CFC is a good choice for armour like that. It’s not the greatest in terms of shatter/impact resistance. I think possibly a layup including one or more layers of aramid fibers would probably be stronger (but then you probably lose some of the weight advantage over a simple Alu skin). The design with very square corners (and badly impregnated in those corners at that) also isn’t a great choice for a composite part imho.
With this very nice square box, it might be possible to get a better impregnation by adding a layer of peel ply, then plastic, sticking a large balloon in there, putting on a lid and inflating the balloon to distribute the resin better. The mold would probably need reinforcing to prevent it bowing out, but it might work as a sort of poor mans alternative to a vacuum rig.
In terms of just battle-bot-ness, it seems to me this bot would be very prone to being disabled by getting tipped onto it’s side or back. And once it’s tipped, it’s done.
Small correction (brain fart, need coffee). Not peel ply (as you wouldn’t be bonding anything to it so you don’t need the surface roughening, but a layer that will absorb excess resin (like a thin felt).
Didn’t see your comment about the aramid before I posted, but good to know I wasn’t the only one thinking that.
I’m not sure aramid fibers are the way to go with combat robots either. I’m reminded of a BattleBot called “Aegis” that had a large, shield shaped Kevlar armor piece covering most of the robot. It was literally shredded by its opponent within moments.
https://www.youtube.com/watch?v=1E91NVVNZfU
It wouldn’t need much pressure to squish the carbon fiber fully into the resin. A problem with using a balloon is that latex rubber causes cure inhibition with some resins so a compatibility test of spreading some mixed resin on a deflated balloon would be needed.
I’d make the mold box a full box. No need to have the cutout on one side, cut that out later to precision fit around the weapon parts.
Rounding the corners to a fairly large radius would help fend off attacks from horizontal bar spinners, and also increase corner strength.
For impact resistance the resin should have some flex so that the robot can be bounced away from weapon strikes rather than the armor cracking. Attaching the shell to flexible mounts would prevent breaking it free from the frame, which would likely include breaking parts off the frame.
PLA is not a good choice for the frame because it is too rigid. Very strong but will snap instead of flexing any. PETG might be a better choice.
Hi !
I’m fully aware of the fact that a cube is not an optimal design for such a bot, but the arena is tiny and also riddled with traps. Keeping the footprint of the bot small increases manoeuvrability (I used a hemisperical shell the last time)
I agree with you regarding the danger of getting flipped, though. If it encounters a wedge bot from any other direction than head on, the probability of getting flipped is pretty big.
The hand laminated carbon fiber shell is almost indestructable in this type of event and in this weight class. The carbon shell is flexible and is able to absorb rather nasty impacts without cracking (I used a similar type shell in the previous event)
Anyway, – win or lose, the build and the carnage of the competition is 90% of the fun in these informal events. I’m not worried. If it gets flipped within 30 seconds, I’ll grab a cocktail in the next room and start planning for the next event :)
Nice build and hope you have fun :)
I recall that at one point Formula-1 used layer(s) of aramid fiber sheets between the carbon fiber sheets, in the cockpits of their cars. This was done to provide structural integrity in the event of a crash because where brittle carbon fiber would essentially explode into a mess of fibers, the aramid would still maintain some level of structural integrity. Think of it like laminated glass, where the plastic keeps the two layers of glass together when the glass fails. Except in this case the glass is carbon fiber, and the plastic is aramid.
I say all this because I wonder if even a single layer of aramid has the potential to possibly provide some increase of structural integrity to this design. Maybe on the exterior even provide initial abrasion resistance as well.
Get rid of the taser and use EMP