[Stefan] from CNC Kitchen explored an unusual approach to a multi-material print by making custom PLA filament with a TPU core to make it super-tough. TPU is a flexible filament whereas PLA is hard almost to the point of being brittle. The combo results in a filament with some unusual properties, inviting some thoughts about what else is possible.
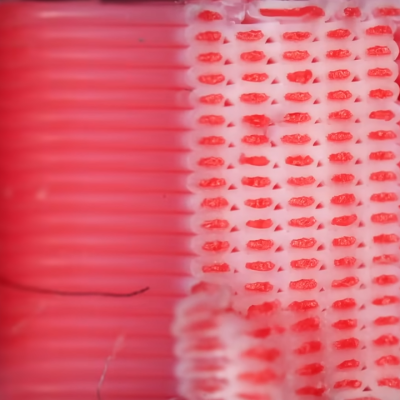
[Stefan]’s video covers a few different filament experiments, but if you’d like to see the TPU-PLA composite you can skip ahead to 18:15. He first creates the composite filament by printing an oversized version on a 3D printer, then re-forming it by running it through a Recreator to resize it down to 1.75 mm.
We have seen this technique of printing custom filaments before, which is useful to create DIY multi-color filaments in small quantities right on a 3D printer’s print bed with no special equipment required. This is an effective method but results in filament with a hexagonal profile, which works but isn’t really ideal. By printing his custom composite at 4 mm diameter then resizing the filament down to 1.75 mm, [Stefan] was able to improve overall printability.
That being said, TPU and PLA have very different characteristics and don’t like to adhere to one another so the process was pretty fiddly. TPU-cored PLA might be troublesome and uncooperative to make, but it can be done with some patience and fairly simple equipment.
Despite the difficulties, test prints were pretty interesting. PLA toughness was roughly doubled and under magnification one can see a lattice of TPU strands throughout the prints which are unlike anything else. Check it out in the video, embedded below.
The test used is called Charpy impact test https://en.wikipedia.org/wiki/Charpy_impact_test
And I’m not sure whether it’s result are very representative in this case. My first guess is that the PLA breaks first before the TPU starts elongating and absorbing energy. If you print a product, the PLA breaks, but the TPU still holds the pieces together, is your product then broken or not?
It probably depends on the product, but the Idea is at least interesting.
It’s an interesting safety mechanism like hickory ladder rungs.
https://iv.ggtyler.dev/watch?v=NXSoaeHG6B0
Similar but different… https://www.testronixinstruments.com/blog/what-is-the-difference-between-izod-and-charpy-impact-tester/#:~:text=As%20mentioned%20earlier%2C%20the%20main,test%20uses%20a%20heavier%20one.
Thought PLA+ / PLA Pro was a PLA and TPU mix.
Pla+ is kinda whatever.
Pla with pet? Pla+
Pla with tpu? Pla+
Pla with abs? Pla+
There’s no industry standard for what pla+ is.
What about filling the channel with something that can leave empty space after pulling, i.e. water-soluble filament, or compressed air, water or oil? One could make thin pipes in which water could circulate to make i.e. self-cooling clothes. Or, if one makes a core of transparent plastic, it could be fibre optics.
Seems like it should be reversed, no? TPU lattice and PLA cores?
like steel rebar embedded in concrete, except it seems to be the reverse, i.e., concrete cores embedded in steel lattice.
But PLA and TPU are probably more similar in flexibility/elongation than are steel and concrete.