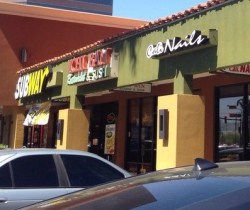
Like most hackers, I’ve run into a part that looks like it might do what I want, but the only documentation came from a company so thoroughly defunct their corporate office is now a nail salon and a Subway.
So, as any hacker who’s wandered through a discount store with a spare twenty, at one point I bought a Chinese caliper. Sure it measures wrong when the battery is low, the temperature has changed, if I’ve held it in my hand too long, the moon is out, etc. but it was only twenty dollars. Either way, how do I get accurate measurements out of it? Well, half-wizardry and telling yourself educated lies.
There are two golden rules to getting accurate measurements by telling lies. It may be obvious to some, but it took me quite a bit of suffering to arrive at them.
- Engineers are lazy. So lazy. Most things are going to be even numbers, common fractions, and if possible standard sizes. If sheets and screws come in 2 and 3mm then you bet you’re going to see a lot of 2mm and 3mm features. Also, even though the metric world is supposedly pure, you’re still going to see more 0.25 (1/4) mm measurements than you are .333333 (1/3) mm measurements. Because some small fractions are easier to think about than decimals.
- Your eyes lie. If it matters, measure it to be sure.
Stupid Caliper Tricks
Using a caliper should be straightforward. After all, it’s just two parts that slide against each other and a means of measuring how far it’s travelled. Nonetheless, between three measurement surfaces and a few tricks to use each one, it’s worth looking into.
The Flat Bit and the Wedgey Bit
The caliper has two types of surfaces on its jaws — a flat portion near the readout, and a wedgey region that gets thin toward the tips. Use the flat bit when you want an average measurement, and the wedgy bit when you want a point measurement.
For example, if you want to know how big to make a hole for a screw to fit through, use the flat bit. (But if you want to measure the minor diameter of the screw — the diameter inside the threads — use the wedges.) Usually, you’ll measure diameters with the flat bit. Even after measuring, though, you’ll want to use your head. Screws are usually a bit smaller than the size written on it, so an M3 screw will read 2.95 mm on the caliper. The extra play will make it pass easily through a 3 mm hole.
If you want to measure a delicate or fragile material, you also use the flat bit. The caliper should be made out of fairly hard steel. (It gets an extra point on the hardness scale for every ten dollars you spent on it.) So if you try to measure something delicate it will damage or indent the surface. This is especially true for plastic parts. For plastic parts the wedge applies a point load and deforms the surface, throwing off your measurement.
Don’t drag your calipers across surfaces when you’re done measuring. This is a pet peeve of mine. I had a coworker who would use his 250 dollar calipers to measure the width of a circuit board, and then draaaag it off the edge. The wedge is a thin, precision, hardened surface. You’re either damaging the calipers or the thing you’re measuring. Open your calipers, then remove them.
The Caliper Has Math Functions Built In
Using the zero button you can do simple addition and subtraction. Imagine that you wanted to measure the distance between the center of two holes. You could measure the distance between the outsides of the holes and then subtract off each hole’s radius to get the center distance. Or you can use the zero function when the two holes are the same size. Measure the diameter of a hole, then click zero. Now measure the outside to outside points of the holes. That will be your center to center distance — the diameter (two radii) is automatically subtracted away. Neat!
The zero function is also useful when trying to decide if something will fit into something else. What if you want to know if a shaft will fit into a hole? You could measure one, then measure another and subtract the difference to get the clearance. With calipers? Measure the shaft, click zero, then measure the hole. The value on the screen is the clearance.
The same trick is used to check the difference between two similar measurements on different parts. Measure one, press zero, and then measure the other. I also use this feature to measure how much printer filament has been extruded with a tool I made.
A Example Application
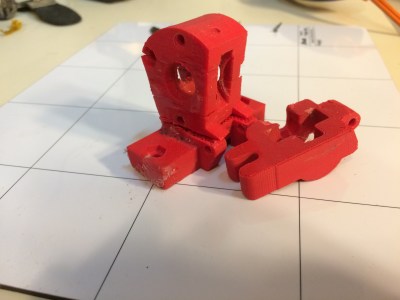
With these basics and a few tricks, we can reverse engineer a thing accurately. Our victim is the new cold-end from E3D. The cold-end on my printer broke, and I needed a new one. Since I was thoroughly in an egg-chicken situation, I hoped to get someone to print me a new one at MRRF. I told them about my plight at MRRF, and they agreed to give me one of their prototypes if I designed a sled for the Prusa i2.
I started off by figuring out just exactly which measurements I needed to take: where the case and the nozzle are in relation to the stepper motor. This positions the nozzle and gives me rough outlines of the cold-end so nothing collides into anything. The rest of the features of the cold-end and their locations are not needed. You don’t need to model the whole part — just the bits that impact the part you’re building.
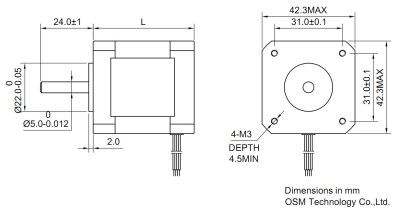
It looks like we have a mount for a stepper motor on the back. Since all steppers are built to a standard, we can apply Rule 1 right away. A quick search shows us the pattern for a NEMA 17 motor is a square hole spacing of 3mm holes at 31mm with a 27mm hole in the middle. We haven’t even taken the calipers out yet.
Okay, so let’s get the outside dimensions of the cold end. I’m getting 43.97 and 46.44. I’m going to translate that to 44mm and 46.5 via Rule 1. Likewise, I’m getting 24.67 for the depth, so 25mm it is.
Now, some of the more experienced of you will say, but Gerrit, what about draft angles? The bottom of the part is a whole 0.75mm smaller than the top. Well, again, Rule 1, but on myself this time. It really doesn’t matter. I’m only interested in this measurement to know when the part will hit something, so the biggest dimension with do.
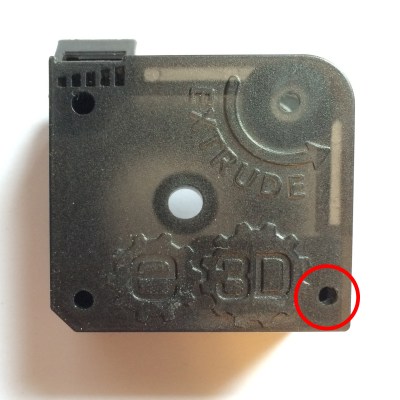
Now the next thing is an application of Rule 2. It looks like the shaft is sitting right in the middle of the box, which means that the stepper pattern should be right in the middle of the box. However, with a second glance it becomes apparent that the centricity is an optical illusion caused by that offset screw in the bottom right corner. It’s an important dimension, so I’m going to measure it to be sure that it’s centered.
To start, I picked the easiest corner to measure. I can assume via Rule 1 that nothing is rotated and that the stepper pattern is going to be perfectly square with everything. Even if there was some unknown advantage to rotating a stepper hole pattern, CAD software really hates that sort of thing. If I find the offset of one hole, the rest can be determined. So I simply measure the distance from the edge to the inside of a hole, and then add one half of the hole diameter to it. If the math were harder, I could have done this using the zero-offset trick.
Last, we have to get the offset from the stepper shaft to the center of the nozzle assembly that slides into the cold end. There’s no good way to get this measurement, but by combining all the skills up till now it’s fairly easy to get a good guess. Though if forced to be honest, I would throw an error of +/-1 mm on this.
So, I’ll measure the widest point of the slot. I’ll cut that measurement in half and set my caliper to that. Then I’ll set it against the side of the slot closest to the shaft. Now I’ll mentally (or with a crayon) mark the point where the other edge of the caliper sits. That’s the center of the slot. Then I’ll use a piece of paper to draw a line from the middle of the shaft to the edge I’m measuring. Now I have one measurement! 11mm.
To get the offset from the back of the cold-end to the center of the nozzle, I can apply Rule 2. I know by the documentation for the nozzle that fits into this that it’s http://wiki.e3d-online.com/wiki/E3D-v6_Documentation going to be a hole of 16mm or bigger for it to work. So, on a hunch, I look and see if the arc is 8mm tall, making it a 16mm circle. If that’s the case then I can measure from the lowest point of the arc to the back and then just add 8mm to get the offset. It ends up being 13mm from the back. Which is, just slightly forward of the center of the assembly. Thanks Rule 2!
While we’re at it, let’s get the depth of the hole that the nozzle fits into. I didn’t mention the stick thing that comes out the back of the caliper because it usually doesn’t work, but that’s what it’s there for. A quick measurement to the mating surface gives us 12.1, or 12 mm. And there we have it.
After a bit of CAD, we have a model that for all practical purposes lets us design this part into an assembly. You can see it/download it here. After a bit more work, I used it to design the promised sled. I had some other issues with the first iteration of the design, but as far as the clearances for and locations determined by the cold-end, I had no problems at all. A few iterations later, I had a final design that works pretty well!
When I got started with this sort of stuff I would always agonize over getting the model exactly right. I would make a lot of paper drawings and keep tables of measurements. As I went on I realized that a bit of cleverness and familiarity with the tools are just as good as a 3D scanner for practical purposes, and certainly a lot quicker. I wouldn’t recommend using these tricks to do a quality inspection at your job, but to get a good model with the least agony it works pretty well. Do you all have measurement tricks to share?
Well, at least you had a choice between a foot long and sushi! ;-)
Digital readout calipers….meh…learn to read a real pair of vernier calipers. I’m astounded at how may science and engineering folks never learned how a vernier works and how to read one.
I can read one of those just fine. But it’s SO much faster and easier with a digital readout. Added benefit: you don’t have to have the area lit up like the surface of the sun to be able to see those tiny little lines.
I bought a set with a dial instead. I got sick of replacing the batteries on the digital ones because they would always die while in the case when unused (even when off).
Yep, plus the dials seem to have repeatable accuracy and even the $500 digital one I have will be off by 0.001 every 5 times I remeasure the exact same thing. the analog dial , dead on every singe time.
You bet. Quite possibly my favorite measuring tool. Only requires minimal thinking, and it’s “good enough” for most reverse-engineering work..
Not to mention that the dial is moveable, so you can ‘zero’ the measurement just like you would with digital.
Definitely better when you are looking at a basket of 500 small parts and a work order demanding 100% inspection – after the first few you don’t have to think about the numbers anymore.
“Analog” “Dead on” hahahaha
Exactly. I started thinking about thermal expansion, and how an inch-big object could be easily changing size by 0.001 just from you holding it in your hand for five measurements. However, if the calipers expand the same amount by holding in your hand… makes it look accurate when it isn’t.
A meter long bar of aluminium will change 22 millionths of a meter per Kelvin. That’s 0.022 mm per degree, and when you heat it up in your hand from room temperature, it’s going to stretch 0.22 mm per meter, or if you have an inch-block it it’s going to grow and shrink by about 5 thou.
If I got the conversions right.
Yes well obviously you don’t know what a vernier is then because a vernier is far more “dead on” than a digital display, it’s called reputability. The only moving part on a vernier is the actual slide! My vernier is has about 15 cm range, Divided into cm, mm, mm/10 and you can proportion the lat mm/100 to at least 0.05mm or 0.02mm
Just more logical fallacy as always on HAD, it’s pretty obvious who the old timers are when they appeal to tradition.
I’ll take 4 digit mitutoyo’s over an analog caliper anyday. The last digit is mostly noise but so is guessing where the needle is pointing between lines.
The dial calipers aren’t as accurate the digital ones, according to the factory specifications.
The 150mm mitutoyo digital calipers have a +/- 0.02mm accuracy, while the 150mm dial caliper is +/- 0.03mm.
I suspect your error in measurement comes down to technique. You need to apply exactly the same pressure each time, Even a speck of dust can throw your measurement out.
Good micrometers have a ratchet that stops movement at the same force (and stops you from using it as a G-Clamp)
0.02mm is a common accuracy for low end vernier calipers. What people here seem to me missing is that *IF* you know *how* to read a vernier *properly* then it is a highly accurate instrument with greater accuracy then a dial caliper, better repeatability than a digital caliper, better temperature stability than both, higher reliability (can be dropped countless times) and doesn’t need batteries.
A mitiutoyo caliper will last a couple years on a single battery, I have a couple pairs and I rarely replace them. Even though the cheap chinese ones have an on/off switch it only turns off the display and the rest of the innards keep running at a good chunk of the “on” power. Mitutoyos dont.
AvE covered this in one of his videos…
https://www.youtube.com/watch?v=E8oopG2GpF0
The real problem with the cheap chinese calipers is when the battery gets low, there is no warning, and the measurements start going screwey.
One way or the other everyone using this tool should have, or have access to at least one gage block to check it.
I agree – I had a (cheap) set of digital calipers, and when they gave up the ghost I got a nice vernier one (OK, by ‘nice’ I mean in the $50ish range, not the $250ish, but it’s still very good quality from my point of view). I love it! Sure it takes a bit longer to read, but it is just as accurate if you are careful.
Just out of interest, why do you love it better than the digital ones? Is it just the higher price = better quality?
I love my vernier calipers because you can actually see what is going on. You know how digital calipers–especially the inexpensive ones I imagine–jump around and never seem to zero out perfectly? There is none of that with manual verniers. While you wouldn’t measure tenths with them you can at least see where the measurement is landing without that unnerving 5 tenths jumping about.
On top of all that the verniers are beautiful in their simplicity.
Verniers are nice but ones that are any good are expensive.
I don’t own a pair of digital calipers that jump around and don’t zero out properly, and I do have calipers going down to the $30 kind, the ones where you want to remove batteries because they’re terrible on batteries. If you’re buying verniers the same kind of place you bought those calipers, then I doubt you have a very nice vernier.
I can read them just fine. I don’t like parallax errors. I like having a clear number on mine that takes my mental state out of the mix. As an aside, If I could have any caliper it would be the Mitutoyo Absolute Digimatic IP67. That’s a nice pair that won’t skip steps, that’s temperature compensated, etc. I used to want a pair of Starrett calipers, but they’re turning into import city, sadly.
I learnt in grade three (Si units and measurement) si I am sure an adult should be able to learn.
“learn to read a real pair of vernier calipers”
That’s a problem when most of the verier calipers are fakes.
Good article on the measuring, this is definitely an art that takes time to learn. A couple other tips on reverse engineering –
1. Add fit clearance, don’t try to replicate the part dead on, create one with slightly looser fits than the original to account for measuring error and 3d printing errors.
2. If there are a lot of tiny or unusually shaped features that you can’t get a caliper on, take a picture of the item next to a ruler or some known-length object. stand far away and zoom in to remove perspective effects. Scale the image in your cad program based on the ruler and then trace out all of the stuff based on the image. This technique works really well, I did this for a remote control housing with a hundred buttons whose location could not be caliper measured.
If the object is sufficiently flat, do the same trick with a scanner. You can get 4800 DPI flatbed scanners for under $100.
Even if it isn’t flat, you can usually hang the object just above the bed and still get a good picture.
The cheap digital calipers seem to use up the battery when off and battery in place. Take the battery out of the device when not in use. LR44 batteries for this unit.
AvE did a tear down of a decently made clone and the current draw when off was approx 10x (16uA vs 1.8uA) the name brand expensive calipers
I appreciate that 1.8uA is better than 16uA, but the fact that mine is undoubtedly also a clone yet I don’t seem to have much of a problem made me wonder – a back of the envelope calculation based on the 150mAh capacity an LR44 is supposed to have results in about a year of stand-by. I find that entirely sufficient, I really don’t need callipers to stay functional with ten years between uses. Considering my box has a pocket to hold a second battery (which I always replace soon after switching out a depleted cell), the difference in consumption has exactly zero implications for me.
“Also, even though the metric world is supposedly pure, you’re still going to see more 0.25 (1/4) mm measurements than you are .333333 (1/3) mm measurements. ”
That’s gonna bite you in the ass if the part is built to precision and you take a pick between the two when the part is really supposed to be 0.3 mm to fit a slot or something, and you make it 0.25 on the assumption that they wouldn’t have picked 1/3 mm.
In fact fractional millimeters isn’t how you’re supposed to work in metric. What seem to be fractional millimeters are usually because the part is made to approximate the old standard, like plywood thickness which is still in imperial although it’s sold in metric – so they don’t have to cut two different sizes for two different markets.
I think the argument is that someone designing a part is more likely to choose a 1/4 than 1/3 for a given matching dimension. Not that they’re just going to arbitrarily round down a part they’re building for an existing piece of equipment.
Just as they’re more likely to use an existing screw size than design their own thread pitch and shank diameter.
But that negates the whole point of metric.. metric doesn’t DO fractional. You don’t often hear of measurements of 1/4 millimeter: it’s 250 microns or get out. This is the one thing that has always driven me crazy about the english system.
The argument IS valid in that often the designer used whole numbers, but the direct analogy between this kind of ‘fractional’ measurement is a bit off.
But .25 is fine in decimal and fractional.
Basically any fraction based on the factors of 5s and 2s is fine. (Due to base 10=2*5) 3rds or other fractions don’t make sense at all. (Nevermind that there’s not much of a point to them, even with inches, at that point even the imperial system starts using decimals with ‘thou’.)
1/4 is not the same as 0.25 though. One is exact, the other is not.
With 1/4 you don’t know whether it means 0.25 or 0.250 – or whether you can assume the part is to be manufactured to within 10 microns or within 1 micron unless other tolerances are specified. A 1/4 should in theory be interpreted as 0.25000… whereas the decimal notation is always within the rounding error of how many digits you have.
@Dax: I would count 1/4 as the same as 0,25 as the same as 0,250. If tolerances matter, you should give them. I think it would be dangerous in general to assume the tolerances the way you did.
That’s completely besides the point. With metric you don’t -use- fractions. Doesn’t matter where it comes from.
“Metric is fractions”
You’re arguing semantics there. Completely besides the point.
Like Medix said: you won’t find metric parts designed in fractional meters. It just isn’t done.
If you’ve got a part that’s manufactured to such a fine size as to make a difference between 1/4 and 1/3 mm, then you’re talking about a part that is made to a tolerance that is finer than 0.1 mm (100µm) and you really shouldn’t be guessing about fractions at that point. Furthermore, you’re not likely to be able to produce said part in a 3D printer anyways because the layer size is right at your tolerance requirements and your printer just isn’t that linear.
Agreed. I never – repeat, never – use fractions with anything metric. I grew up with imperial and have been through a metrication in both of the countries I’ve lived in; I reckon that using fractions is a horrible idea that works to diminish the advantages of the system.
“Metric is fractions.”
The SI is explicit about using the decimal notation, and not fractions. It says “don’t do it”.
Yes OK. we all know that imperial uses common fractions and metric could be said to use decimal fractions, but common usage is that common fractions are called fractions and the term ‘decimal fractions’ is a curiosity (or technicality if you prefer). Whatever – the smaller than 1 portion of a metric measurement is never written with a denominator.
I thought that’s what I said. Yes you can write a fraction of a number using all those notations, including a fraction (the type with a denominator), but it simply isn’t done that way (with metric) ’cause it’s a pointless complication without any useful purpose.
Hmm, two different meanings for fractions are being used here –
A fraction where the divisor is an exponent of ten eg
1/10, 0.1, deci
1/100, 0.01, centi
1/1000, 0.001, milli
A fraction other than above
1/2
1/4
5/16
9/32
Metric is fractions and usually 1/2, 1/5 and 1/10 and multiples of that are used.
Just that no metric person is writing it like that EVER.
They write 0.5, 0.2 or 0.1 or multiples of that like 0.3 or 0.8.
If they get below 0.1 (1/10) they just step down one decade and keep on going 0.05, 0.02, 0.01 (which equals 1/20, 1/50 and 1/100) and multiples.
You will find 0.25 (=1/4) in metric a lot as well, but this can be expressed as 0.2 + 0.05 (1/5 + 1/20).
This is different to the imperial world., where you stay within 1 and keep dividing it. You never encounter something similar to a decade. It’s just not existent: 1/2, 1/4, 1/8, 1/16, 1/32, 1/64, 1/128, …
Metrics don’t go below 1/10 for fractions, if they have to they step down a decade – that’s the difference.
Also if there is accuracy involved it can’t be derived from the points after the comma.. that’s not how it’s done.
Usually for symmetrical maximum deviations in their most simple form this sign ± or +/- is used followed by the deviation.
So it’s perfectly possible to see 0.2 mm +/- 0.001 mm as a measurement.
Or 0.015 mm ± 0.01 mm.
The other non-fractional thing being that in metric whenever you read something looking approximately like 0.333333… chances are it’s actually 0.30 (or maybe 0.35) rather than a fraction like “a third”…
I know this may not be the right time or place, but along with a caliper I use a flat bed scanner. You can’t to z accurately, but if you have a mostly planar object (PCB) you can actually find the locations of Mount holes, components. Test points, and borders. Scanners make 1-1 images meaning all you need to do is import it to inkscape and draw lines, then export the dxf.
It is way faster than any other technique I have used.
It’s exactly the right time and place! A great trick! I’ve used it to get exact mounting locations for panels and circuit boards!
You assume the scanner head is precisely orthogonal to the direction of movement. You should check that first.
I am assuming that the software in the scanner corrects for mechanical imperfections. I have done this trick dozens of times, it produces better results than my 3d printer.
Isn’t a scanner limited by it’s resolution across the bar with it’s “hyper” resolution along the track?
I mention this because I just realized that it might work to examine the “flat side” of a pure SMT PCB and I won’t have to use a microscope to examine the components.
Modern scanners have 3000+ DPI if not much more.
In theory. In actuality the resolution of the scanner is about 300-600 DPI across the paper and the higher resolutions are accomplished by moving the scan head really slowly. Problem is, that’s not very accurate because the head sticks and slips on its rails and the belts stretch and vibrate etc. so the high 3000 DPI figure is kinda like the PMPO of a boombox that says 2000 Watts on the side of a stereo powered by D batteries – it’s a completely imaginary number.
http://www.scantips.com/chap3c.html
“A 1200 dpi CCD sensor really cannot do anything else but scan at 1200 dpi. This rating does not mean that it can resolve 1200 lpi in a test target, but instead, the CCD simply reads 1200 samples per inch. Nyquist sampling theory says the image can never resolve more than 1/2 of that detail level, and in the real world, a little less.”
“The larger dpi number is the possible positioning of the carriage stepping motor.”
Hence, a scanner that says something like 1200×2400 DPI can actually resolve at about 600 DPI max real detail in square dimensions.
Rating: 2000 Watts PMPO for 1.2 ns
Someone’s getting mighty smart throwing around big names like Nyquist (in the original material – present company excluded of course). Yes if I’d have black bars on white background, an 1200 dpi scanner could resolve a (theoretical) maximum of 600 bars per inch before it all just starts washing out as grey goo. That doesn’t mean though you’re not getting all 1200 distinct values of colour per line when you’re scanning a photo…
I WANT that metal box…
Anyone knows anything about it?
That’s a spray painted plastic box. I have the same box sitting next to me right now. The link below is not the same calipers, but it is the same CHINA case that many of the cheaper calipers come in. Look at the pattern on the inside of the lid.
https://www.mscdirect.com/product/details/76367135
Oh. Thanks! I tried to spray paint it with orange paint because I kept losing the black box, but did it early on before I knew what surface prep was. (I’ve had these since early highschool) It didn’t work, but it ended up looking awesome. I also flocked the inside of the box because it makes me feel fancy. Haha. https://www.flockit.com/
Really must stop using my caliper as a scribe…
I’m mixed on that. I kinda do it too, but only to scrape away bluing. I see a lot of machinists on youtube do the same thing. It is a hardened point, and it’s not a surface used commonly for measuring. Anyone have a more definitive opinion and reasoning on this?
If it’s a high quality set, then the hardness is likely REALLY hard, so unless you’re working with unbotanium, then you probably don’t have to worry. I’ve noticed the guy who makes the clickspring (clock-making) videos uses this method quite frequently to lay out parts on the lathe for turning. Since he’s using softer materials (i.e. generally brass), it should be ok. I’ve since started doing the same as I mostly work with aluminum. All you really need to do is make a mark on the layout dye anyway, and that doesn’t require much force.
Scribing with calipers is very common for professional machinists. Calipers have very hard jaws, and if you’re relying on calipers for anything other than cursory inspection you’re in for a lot of trouble.
I don’t know if available for purchase, but I got a set of calipers that have a scribe pin and a roller installed where the inside measurements jaws were located. They have been custom made 30 years ago, but the idea must have been come from somewhere.
I use that for scratching marks into metals (steel, stainless, aluminium, etc..)
http://i66.tinypic.com/2zqdjeh.jpg
I do it on soft material like plastic, alu or painted surface.
I don’t see anything wrong with it, but i have seen people wince. Also I couldn’t see anything about using the other end of the caliper for depth measurements.
I’d be more worried about damaging the part than the calipers. I do use the tips to scribe, and generally avoid making measurements with the very tips anyway.
One trick not mentioned:
To properly measure a drill bit, measure the shank (the unfluted part of the drill body) in an area not mauled up by the chuck.
That is not so proper. Twist drill flutes are typically at least a few thousandths over the shank. I have sorted 1-60 number drill sets by aligning the flute portion inline between the flats on the jaws.
you measure the tip at its widest point… You cannot rely on the shank diameter to determine drill size, although probably 70% of drills are the same as the shanks.
One thing useful about the shank…. it’s normally machined -.0002″ to -.0004″ If the shank is in good condition, you can use it as a gage pin for genereal purpose work. I used to make solid carbide drills for a living… so i can probably give a few tips…
also…. do not attempt to measure drill diameter anywhere else but the tip… the fluted body is backtapered… typically somewhere between a few .0001″s to a few .001″s per inch…. not going to make an accurate measure
Regardless of the shank to flute relationship or guestimates as to the manufactured diameter…
1. Drill a hole with the bit.
2. Buy a pin gauge set and measure the hole.
3. ?
The drill size is defined by the cutting edges at the tip. The actual hole that it makes in the part varies by the material and drilling technique.
Two things if I might add.
1.) Use your Starrett Card.
http://img0105o.psstatic.com/155227514_new-starrett-inch-metric-tap-drill-sizes-decimal-.jpg
2.) Hold bit at 90′ and turn the bit COUNTER-CLOCK wise (cutting edge to NOT catch caliper – keep in mind what orientation you are holding the bit) to get the biggest number. Refer to the chart. That is the true bit size.
I’ve come across calipers with conical jaws- specially designed for measuring distances between holes when digital calipers were not a thing yet.
Well I have several slide calipers.
I have several plastic (pretend verniers) that I use in the dirty oily car garage where I am expecting any measurement to be whole units of metric mm.
I have a imperial dial vernier that was expensive and is very high quality but I have never used it. It’s still in the box.
On my desk I have a strip if Veroboard that have been cut off the side of a Veroboard that I use for measuring whole quantities of 0.1 inch.
Then My main use slide caliper is a reasonable quality vernier. I can drop it and it works, I can drop it again because I only has one moving part (the actual slide). In fact I can drop it many times over and over and it is still in cal – needs no batteries – has both metric and imperial – doesn’t need re-zeroing – is consistent over a fair temperature range as both bits of metal expand at the same rate.
So I am very happy with my slide vernier, so much so that I don’t bother to use a high quality dial slider and I would never bother with electronic.
The plastic ones are not that bad, dimensional electroplaters love them because they can do rough measurements on a wet item over the tank without killing a metal one.
I’m happy with my 6 inch digitial Mitutoyo. Granted it rounds in the tenth (of hundred thousandths). Then again I also have a 10 inch digitial, 16 inch dial and a Micrometer as well.
Thermal expansion of the calliper may well be negligible for your particular use case and if the measured piece and the calliper expand at the same rate and have the same temperature than they do indeed cancel out – but if you think the two pieces of your vernier being of the same material cancels their thermal expansion out automatically, you got it seriously wrong.
My – “is consistent over a fair temperature range as both bits of metal expand at the same rate.”
doesn’t really translate to your – “cancels their thermal expansion”
They’re cal at 25 Celsius. I was just saying that they are not as sensitive as dial calipers or digital.
Another thing the temp effects the offset but not the vernier as a vernier is a ratio 11:10 if you stretch a verier to twice it’s size then it’s still going to be 11:10
I mostly use a digital fiberglass caliper, even after have tried a vernier analog, and cheap ABS calipers. To me any caliper that can do 0.05mm precision is good enough. As said before most objects are man made, so if it reads 2.98 and i know that the caliper has -+0.05mm the datasheet would probably list 3mm.
Not mentioned is using a loupe to magnify the fine vernier lines. Engineers with normal eyesight never thought about problems reading this fine instrument.
I didn’t notice anyone say to be gentle with the tips as they will blunt, and become inaccurate with much use.
As a machinist, I have a B&S dial caliper that is pretty repeatable +/- .001 over the length after 13 yrs semi-daily use.
I have gage blocks to prove it to… not guessing based on the rack and pinion being true.
(my measurement in INCHES)
Re: Digital calipers battery consumption.Anyone else notice that if you turn them off, pull the jaws apart and turn them back on, that the reading is already there. So it’s just the display that gets powered off. Despite that… the calculated ‘in use’ life of the battery is longer than the actual shelf life. …depending on the battery chemistry/quality. When I go to put a new battery in, the replacement is almost always dead too.
They’re absolute reading. The zero etc is built into the strip on the body under the plastic cover. Poking the zero button just offsets the reading. Open the jaws, pull the battery then put it back in and turn it on. If it doesn’t come on at zero it’s absolute reading.
There are also incremental reading digital calipers which always turn on at zero no matter their position.
If you move the jaw with it off, poke zero then turn it on and it reads zero, then it’s only turning off the display.
Harbor Freight’s newest 6″ digital caliper has inch fractions to the nearest 128th along with decimal inch and metric. It has auto-on, just move it and it turns on. But it also uses less power when off. The mode and zero buttons do nothing when it’s off.
By your logic (Which I believe to be sound), it’s incremental but only turns off the display. If I take out the battery, it comes back on with a random number like 1147.24, well beyond it’s actual range.
Do you, or anyone, know how to use the serial port opposite the battery hatch? I didn’t even know it was there until it popped off while sliding the battery cover on.
There a few couple of different protocols. Google will help. Mitutoyo has SPC. Starret, I have read, is rs232. I think the cheap chinese calipers are different again.
Have a look here. Some google fu will help to.
http://www.instructables.com/id/Reading-Digital-Callipers-with-an-Arduino-USB/
Most digital calipers are incremental because the most common sensor is a capacitive quadrature strip.
Putting the battery back in and getting something else than zero doesn’t necessarily mean it’s absolute – it can and probably will glitch, or the memory just hasn’t blanked in that short a time.
Agreed, and that was what I was getting at. If it were absolute it would probably have given a more appropriate reading on power-up. B-)
Mine even turns itself “on” if I move the slider more then 0,1mm
“Engineers are lazy. So lazy.” Hey Bud, you’re lucky I’m not there in person – otherwise this Engineer would teach you a thing or two about calling us “Lazy”. We’re Efficient – Not Lazy!
Hah, I know my people. Lazy perfectionists.
The whole world is metric, the USA isn’t fully converted yet, but atleast they are getting there inch by inch, not mm by mm….
The favourite joke of any old fart teaching science…
FYI there are 2 MORE ways to use a Jaw Caliper (Digital, Dial & Vernier).
1.) Hole depth – (Not really recommended).
http://g01.a.alicdn.com/kf/HTB1S06gHVXXXXbtXFXXq6xXFXXX9/Digital-Micrometer-Real-Mitutoyo-Digital-Caliper-Precisely-Calibrated-0-150mm-Oil-Standard-Electronic-Vernier-Stainless-Steel.jpg
2.) Using the BACK of the bottom jaw – (Not really recommended) unless you can hold the Caliper at a proper 90′ on the “work piece”
Here is a Caliper that uses the “back”
https://cdn.shopify.com/s/files/1/0891/2526/products/1144-150_large.jpg?v=1439943669
In any event, As a machinist you have to realize some materials that you’ll work on are expensive and the machinist must get the spec right. Measuring 4 to 6 times is normal. Set to zero/Absolute/Tare after twice reading is common.
Finally, It is a precision tool. Clean and maintain it as you would a precision tool.
Hobbes 9 & 3 in 1 oil. On the other side of the pond? The old timers will tell you Hemp(aka Rope) oil. (Fun fact All vegetable oils go rancid hemp also goes rancid but doesn’t smell like something died and has the proper “smoke” point for older high close to end of life machines.)
Amazon selling 200mm solar-powered mitutoyos for under $70: https://t.co/29wiENoznR
Mitutoyo’s are constantly knocked-off. Shamelessly, they even have a false “Made in Japan” sticker, but the fakes are no better than the 10 dollar calipers you can buy. I would not buy one from amazon (unless it’s direct from amazon.com). https://www.youtube.com/watch?v=KnDype-j3hk
If you are measuring often get a set of quality calipers, my Mitutoyo’s were ~300$ but I wouldn’t hesitate to buy them again. Once you use quality calipers you will never be able to go back to HarborFreight stuff. The action on them is superb and they are always dead on. I have checked them against gage blocks many times. Just make sure you don’t buy a knockoff pair, if the price is too low then they are for sure a Chinese copy.
For those saying that a analog caliper is better I can agree if you are making quick measurements and want to compare how far the dial swings, kind of like you use an indicator. Otherwise the digital read out beats everything in my book. Huge added bonus is adding a data cable with a foot operated switch. You can measure parts using both hands at your desk then hit the switch and the measurement is entered into your CAD program without any typing. I think Mitutoyo also offers a wireless data link.
Calipers are nice, but Micrometers are where it’s at for measuring all things external. Filament, sheet metal thickness, or anything else you can get it around. If you’re using calipers to measure your filament diameter then you’re gonna have a bad time.
While on the subject of measuring, lets talk tools for marking/assembling. A ruler us good, a T square is better, a marking ruler is incredible. a decent set of machinist squares help make the right angles. Get feeler gauges for checking all sorts of things. There are thread pitch gauges as well.
Oh, and e3d released the drawings for their extruder. I like your design, simple and light. I would like to see a review on that extruder, I’m very interested in buying one, but I’m holding out to see how it handles in the real world.
I like a mike for measuring small parts best too, mostly because I like the way it fits in the hand. To me they are more ergonomic than calipers below the 2″ range
Micrometers are nice, but I suspect using them to measure filament is like measuring lumber with calipers. Most filament brands allow for ±0.05mm and that can vary through the spool.
I haven’t measured filament in many months, and really gave up the habit a year or so ago. I just set a the nominal diameter as a starting point and watch how the bead lines pack next to each other, and if necessary, adjust the flow rate so the beads pack decently with a slight margin to avoid overpacking.
Micrometers are nice, but real mean measure using notepad.
HAHA…this dbag lost me at being lazy. Yeah, I am so lazy that I would ask you things like what material it is, what type of process it went through and so on. What a complete dbagger. Typical Millenial pot smoker. He wouldn’t know a caliper from a micrometer, except you can burn a roach on both.
You NEVER hand measure anything, unless absolutely necessary. It sounds like the Subway and the nail salon is where his “college” or “institute of technology” used to be. If you measure some critical dimension on a part at 0.126 and two of those weird squiggly things as those smart arse in the now HAD authors call them, also known as “, chances are the dimension is 0.125”.
Next, find out what it is and how it was made. Oh wait, I am a lazy engineer, so I won’t look at it, and say it is cheap china ABS made off a cheap china injection molded die, with two many bad radii so that they need extra “pushy point” to get that plastic thingy off the metal thingy, oh if I would have just worked in an injection molding factory, but I had a trust fund…pffft.
I would bet an optical comparator would blow this newbies mind.
Never call an engineer a slacker. I work hard to be recognized as a Hank Rearden…
‘Nuff said. Peace out.
1. Useless to know for this application.
2. Caliper is sufficient for this application.
3. Hand measuring is sufficient for this application.
4. Since the part is designed for installation into a 3D printed subassembly it can be safely assumed that nothing measured will come near a tolerance of 0.001″.
5. The materials and methods used for the construction are again vaguely useless to know, except for letting us know that the precision needed can be covered by hand measuring.
6. An optical comparator is overkill for this application, and not easily accessible.
Rule 1.
And you sneer at pot smokers? Seems better than whatever you are on. What is it anyway? some new LSD derivative? Maybe a Ritalin/LSD mixture?
Whatever it is I don’t project you to ever completely recover.
As an American engineer who has mostly worked at German-owned companies… good luck with your assumptions.
If we plan to fabricate it here, it is in inches… over in China, it will be metric. Fitting to a purchased component? Well, now it depends on where IT came from, regardless of the source for the material I plan on making the fabricated part the mounts it.
Sometimes I round. For instance, 3/4″ is 19.05, but becomes 19mm quite often. 5/16″ is 7.9375, but my drawing has it as 7.94 due to dimensional rounding. I’m collaborating with my Canadian colleagues… you’re screwed because I design in metric, and they design in inches, so those numbers can be literally anywhere.
There isn’t time enough in my day to try to standardize anything to one system or another… as is the way with custom machinery.
One thing as a reminder (especially for the cheap Chinese digital calipers) – don’t let any cutting fluid fall on the caliper, a lot of the cheaper calipers will start generating random figures. I have to keep reminding my machinist students of this all the time. If any coolant does fall onto the caliper, just rub off the coolant until the caliper is absolutely dry.