It’s a common sight in the farming areas of the world — a group of enterprising automotive hackers take a humble economy car, and saw the roof off, building a convertible the cheapest way possible. Being the city dwelling type, I always looked on at these paddock bashing antics with awe, wishing that I too could engage in such automotive buffoonery. This year, my time would come — I was granted a hatchback for the princely sum of $100, and the private property on which to thrash it.
However, I wasn’t simply keen to recreate what had come before. I wanted to take this opportunity to build a solution for those who had suffered like me, growing up in the confines of suburbia. Surrounded by houses and with police on patrol, it simply isn’t possible to cut the roof off a car and drive it down to the beach without getting yourself in altogether too much trouble. But then again, maybe there’s a way.
The goal was to build the car in such a way that its roof could be cut off, but remain attached by removable brackets. This would allow the car to be driven around with the roof still attached, without raising too much suspicion from passing glances. For reasons of legality and safety, our build and test would be conducted entirely on private property, but it was about seeing what could be done that mattered.
To achieve our goal, it was decided to use a series of off-the-shelf steel brackets with M10 bolts to hold the roof on. Two would be placed between the top of the windscreen and the roof, and one each would be placed on the C-pillars of the car. To cut the car apart, we ended up sourcing a reciprocating saw, with a variety of other hand tools helping to remove the car’s trim and interior panels.
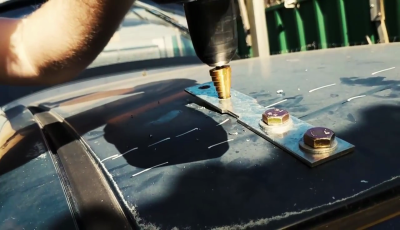
Before making any cuts, we lined the brackets up on the car to drill the mounting holes. With the brackets taped in place, I broke out the cordless drill to make way for the M10 bolts that would hold the roof on. After drilling pilot holes with a regular bit, a Christmas Tree bit was great for enlarging the holes. If you’re not familiar, they’re a great way to drill holes up to 30mm with a regular handheld drill, without having to buy expensive individual bits. However, once we’d drilled all the holes and put the bolts through, we hit a snag.
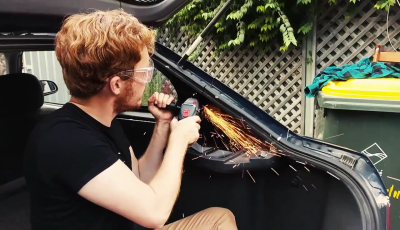
The C-pillar of the car has both an interior and exterior metal skin, meaning that when we fed the bolts through from the outside, we couldn’t actually attach the nuts on the back of them. This was solved with a quick run down to the hardware store to source a grinder and cutting wheels. With some judicious slicing and dicing, we created plenty of sharp edges, and just enough room to get the nuts on without slashing one’s hands to pieces.
The windshield brackets had a simpler problem — the roof liner was in the way. Kudos to the Hyundai Motor Company where they are due. After 16 years the roof liner was still taut, clean and presentable… until the box cutter came out.
Our plan all along was to get the brackets mounted and bolted in place prior to starting the cutting. Modern monocoque cars lose a lot of strength and rigidity when the roof is removed. If we’d cut the roof away, it would be inordinately difficult to hold it all in place while we then tried to drill holes for brackets to mount it back on. By installing the brackets first, we’d get some semblance of an original fit after cutting.
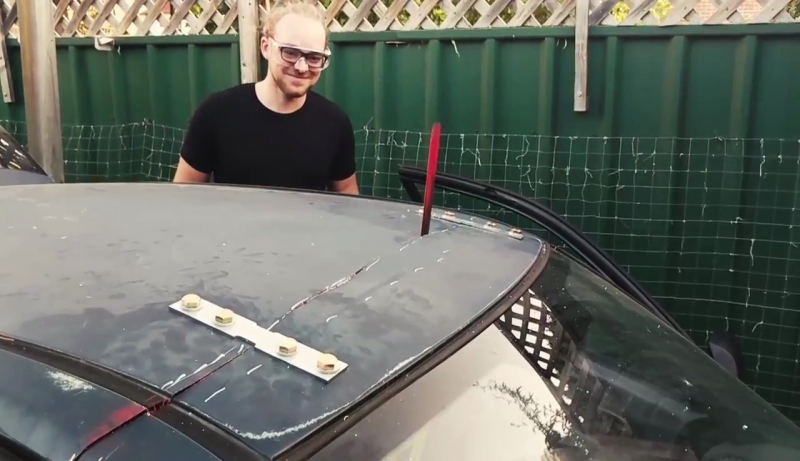
With the brackets bolted on, we could now commence hacking the roof off. With the reciprocating saw fired up, we began to slice along the C-pillars and the windshield. Brackets were only unbolted one at a time as we cut past them, which made cutting much easier, as the car wasn’t falling apart as we worked. Reciprocating saws can be surprisingly effective and powerful — just be wary of what the blade might catch on the other side of your panel. We were careful to make sure we avoided any wiring, fuel, or hydraulic lines — hitting one could easily spell disaster. Nevertheless, we got the job done without any major mishaps and the roof was now cut free, but bolted in place.
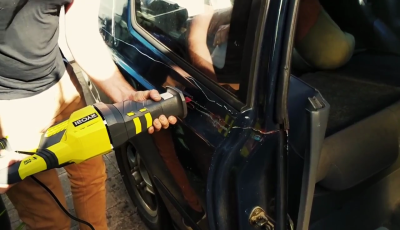
Those of you with a mechanical inclination are probably asking some questions about our methods here. Truth be told, putting bolts through holes in thin sheet steel isn’t great for longevity. The shock and vibration loads of the automotive environment will tear the steel apart in relatively short order. In our case, it didn’t matter — our Hyundai was here for a good time, not a long time.
With the major cutting work done, it was time to up the stealth factor. Shiny steel brackets were far too obvious for our tastes, never mind the gaping cuts in the body work. A can of black spray paint and a roll of duct tape allowed us to cover the worst of the modifications. From 30 feet or so, the casual gaze would just see a beaten-up old hatchback, and that’s precisely what we wanted. But would it be drivable?
The short answer — surprisingly so. On the rural property’s smooth tarmac roads, the car was barely worse than stock. There was some additional wind noise, but by and large the car didn’t feel a whole lot different. Upon hitting the rough dirt roads, things changed pretty quickly. The bumpy surface was making the rough-cut panels rub and squeal against each other and overall it was a rather horrible experience. We slowed to a crawl as we made our way out to our secret test paddock.
We arrived to a sandy wasteland, where nothing much grew, and the ground was just firm enough thanks to some recent rain. We broke out the spanners in the dark and attempted to remove the bolts holding the roof on without nicking an artery — thankfully, our convertible antics did not become a blood sport. It took four of us, but we managed to prise the roof free, dump it on the ground, and then climbed into our glorious steed for the evening.
The events that followed were exactly what you’d expect — a series of wild weaving, handbrake turns, and the inevitable bogging in wet sand. It turns out our convertible Hyundai handles just fine, at least for one night. In regular use I’m more than certain that the chassis would quickly flex and fall apart. There’s no feeling quite like tearing along beneath a clear night sky, with the wind in your hair and a jagged metal edge perilously close to your right elbow. We had some good times, and the Hyundai served us well.
Feeling exhausted, it was time to pack up – and to our surprise, the roof actually bolted back on the car successfully. Had we the means, we likely could have used the car for further antics, though the necessities of real life meant that after one brief evening in the moonlight, our humble sister from Seoul was destined for the scrap heap.
I consider the project to be a success — we built a convertible that didn’t fall apart, and was stealthy enough that it could pass through the average neighbourhood without raising too many eyebrows. It was also our aim to do this cheaply, and I broke down the costs below.
- 2001 Hyundai Accent – $100
- Grinder + Cutting Discs – $40
- Reciprocating Saw – $150
- Fasteners and Brackets – $30
- Fried Chicken – $30
All up, I was in for $350 which, for any sort of automotive experiment, is extremely affordable in my book. There’s a certain freedom that comes when working with a car that’s headed for the crusher. While our Hyundai was falling apart, we were able to give it one last crowning glory, and have an absolute blast doing it. Check out the video below, and start planning your own madcap build today!
For some reason, I’ve wanted to get a car like a Crown Victoria with one of those half-padded roofs, and modify it so the padded section lifts out as a removable hardtop. Thus making the car actually be half a convertible as it was pretending to be. Only I’d want to add a suitable mating flange and some better retaining hardware to make it look like it was some sort of deranged factory option.
Google removable carson top
Why is a fake and padded convertible style roof treatment called a Carson top? No idea.
Crown vic is Frame based car so body flex will not be a problem.
“The design was invented by Bob Houser in 1935 when he worked for Amos Carson at Carson Top Shop in Los Angeles, USA”
A quick google confirmed my recollection. Called a Carson top name after the shop that one of the first to produce them.
Don’t forget to properly disable the SRS while doing something so drastic to a vehicle.
My limited experience with this kind of tomfoolery is tat the SRS automatically reminds you that you haven’t diabled it and then promptly disables itself, loudly!
It can happen. That scene in one of those terrible Final Destination films is based on multiple instances of real accidents.
And those “curtain airbags” add another possibility of an activation.
Very good advice, something I definitely should have considered more carefully before cutting into the car.
Wait… why/where is this illegal?
Everywhere. They cut the roof off a unibody car. The stamped sheet metal shell of the car is the structural “frame” (of which the roof is an integral part), that replaces the frames on trucks and old cars. You can do basically anything you want to old cars with frames, you cannot modify unibody cars.
Well, you can, but you have to put a lot more care and love into bracing and the like than was done above. I mean things like underbody and side panel bracing with serious steel tubes/box section, real mounting and retaining hardware, and seals. It would definitely end up being more than the $350 spent on this particular endeavor though.
When you cut a roof you will loose at least 2/3 of body rigidity. Bracing bottom of car will help but not that much. If car is designed with a convertible variant from a factory, there is a chance, that your car contains these bracings too. Othervise it is not worth it. My friend used to have Nissan 200SX S13 (240sx for us readers) with company made T top. Cars flex and paint on roof was cracking a lot.
Yes you can and no it’s not illegal.
Simply add some structural enhancements to under the car, It’s done all the time on modern convertible conversions.
It’s not illegal to do it, but it is illegal to drive such a car on public roads in most/all civilized countries which have some kind of a need for type approval (or individual approval) of cars.
Exactly! It’s probably legal in most of the USA.
I know for a fact that this would not pass the yearly safety inspection required in my US state. In fact, it would probably get impounded by the first police officer who saw it on the road.
Depends on how stiff the unibody is. This guy hacked off huge chunks of a Prius V and is in the process of grafting the shell of a restued beyond restoration Firebird convertible to it. http://ecomodder.com/forum/showthread.php/firebrid-hybrid-convertible-project-prius-platform-swap-33459.html
Besides various safety issues… cut off the top, the bottom half usually warps. Sometimes undrivable.
The car, as manufactured by Hyundai, meets Australian Design Rules, and this is necessary for the car to be legal to sell in Australia.
Making significant modifications to a car like this requires the car pass an engineering inspection and certification process, to verify that it is safe to drive. As other commenters have said, it would require structural bracing, and of course, removal of all the sharp edges.
Obviously, as we did this on private property, we weren’t breaking any laws, but it would have been illegal (and dangerous!) to drive this on public roads.
Re-instal the roof panel and then (using, oh say 1″x1″ 1/8″wall, or nearest metric equiv) structural tubing, grab your Mig welder & build a frame around the outer perimeter of the coutout.
Webbed out & tied into the corners or pillars, This will add a nice amount of strength back to the body.
Now the obligatory link to the half car.
https://www.youtube.com/watch?v=IV007zPsRwA
Aaannnnd just to cover the (good natured) pedantic whining dept:
Since this -IS- Hackaday, When you reffered to the step bit a “Christmas Tree” bit,
you had my brain, briefly, wondering ” Oh boy ,wtf are they using the holiday decorations for”??
Hahaha, yes – I enjoy the colloquial name but stepped bit is more formal!
That video is hilarious.
FWIW, the proper name for a ‘Christmas tree bit’ is a step drill. Should help when googling, and yes, they’re great.
Let me just introduce you guys to https://www.reddit.com/r/Shitty_Car_Mods/
Because that’s where this is going…
Good stuff there.
That split~De-skinned hood/bonnet
is an interesting example of needing to watch for structural issues.
The green, double header truck was kinda interesting.
Having grown up in a beach town where roofs rusted out regularly, this sort of mod is quite common. Known as a “sawzall convertible”. Only to be done on frame vehicles. I had a 1972 Ford Station Wagon sawall convertible. Great fun until the engine blew.
What’s it like when done to a framed vehicle? I imagine there’s less issues with body flex. That said, the car handled fine and didn’t feel any less rubbish with the roof off. :P
No problem at all, except for the extreme draftiness on the freeway. Oh, and the need for drain holes in the floor (in case of rain).
We did this to a 1991 Subaru Legacy wagon when I was in my mid twenties. We opened the drivers door and couldn’t close it again without jacking up the rocker panel. The roof adds a shocking amount of structure to unibody vehicles
mighty car mods did a pretty decent cut roof mod on a subaru (ute, not convertible)
https://www.youtube.com/watch?v=NoBnwKu5g5U
One of my inspirations!
saw this on the Baja forums. I had an 07 turbo Baja trucklet.
Classic Red Green:
https://www.youtube.com/watch?v=LOeZAhaOgoE
Man, a week after this was filmed, I found a bus on sale for $1500 and contemplated doing exactly this. Not sure I would have topped it though. :P
Back in college in the early 90s there was a guy on campus from NYC who had an old Ford Falcon. It seems he wanted it to be a convertible, but he lived in NYC and probably didn’t want it to get messed with. Solution? He cut the skins out of the roof and welded on diamond grate to the roof frame. Then he installed snap fasteners all around it so he could snap on a oil cloth cover for when it rained. Of course, the whole car was then painted rattle can black. It was a f**king bad ass car.
A few decades back…. I saw an old, pusher chassis bus, that someone had sculpted into a long, giant, 1950’s styled car.
Each of rear fins were sculpted from an entire rear end of an actual automobile. They used the trunk/boot, fenders & tail light sections-rear clip(name?)
The operators cab was built from another, old car body that had been cut just below the window lines & then joined to roof line of the bus front.
The main floor was typical “Gutted Bus Chic” with assorted, derelict remnants of the galley, sleeping “ideas” & an ancient generator.
It was actually a rather well done job of body fitment. Framework looked reasonably thought out (for the era) and controls appeared to have all worked, when built.
Sadly, I no longer have the photos. :(
Alternative version:
https://www.youtube.com/watch?v=BziBqwkGxbE
I had a chop topped 91 Acura Integra for a while. I had it registered for years in Arizona without any problems until I got rid of it. I’ll have to try and find the photos of it. It was a fun car to drive, it removed a good amount of weight getting rid of the hatchback making a much better power to weight ratio.
That sounds awesome, Integras rule.
A couple of dunderheads in my hometown took everything off the top of a 64 Chevy 2 four door. They drove the thing like it was 24 hours of LeMans all the time, that poor little 6 cylinder screaming like it was getting branded on the nutsack. They ended up taking it boonie crashing and it broke in half behind the B pillar. They got the car as far as the gas station I worked at before the drivelin finally collapsed because they stopped. they just got out and left it where it died, I had to call the cops and a tow truck.
Something makes me think you may have seen the old way of touching car bumpers and then bridging the positive battery terminals to jump start a car.
Wow, had no idea the roof was quite so important structurally.
They should probably write that in a warning sticker somewhere. I don’t think I’d ever want to chop the roof off a car, but given our car had a warning sticker telling us things in the rear view mirror were behind us, I’m kinda surprised they left this out.
Also, you guys took far too long doing the conversion. I’ve seen a firemen demo where they took the roof off a car in under 30 seconds – and I think they had someone inside it, though it may have been a dummy.
Yeah, we could have cut the roof off in under 10 minutes without a problem. That wasn’t the aim here, though – we had to build the bracketry system here first to meet the aim of building it stealthy enough to avoid suspicion. That took much more time.
wont be long until the doors don’t open without effort and won’t close without a crowbar.
here it’s not illegal to cut half the support from a unibody vehicle, but still a bad idea.
Wanted to do the targa top build for my beat old Fiero but having to add a couple hundred pounds of bracing under a car already crippled by the Iron Puke 4 banger and autotragic transmission, wasn’t worth the effort.