It’s hard to reckon exactly when in history humans became a technological species. Part of that is because the definition of technology is somewhat subjective; if you think making a stick pointy enough to grub roots from the dirt or to poke enough holes in an animal to convince it to let you eat it is technology, then our engineered world goes back a long, long way indeed.
But something about pointy sticks just doesn’t seem transformative enough, in the sense of fundamentally changing a naturally occurring material, to really count as a technological line in the sand. To cross that line, it really seems like the use of metals should be part of the package. Even if that’s the case, our technological history still goes pretty far back. And copper ends up being one of the metals that started it all, about 11,000 years ago, when our ancestors discovered natural deposits of the soft, reddish metal and began learning how to fashion it into the tools and implements that lifted us out of the Stone Age.
Our world literally cannot run without copper, forming as it does not only the electric-motor muscles of civilization, but also the wires and cables that form the power and data grids that stitch us together. Ironically, we are just as dependent on copper now as we were when it was the only metal we could make tools from, and perhaps more so. We’ll take a look at what’s involved in extracting and purifying copper, and see how the methods we today use are not entirely different from those developed over seven millennia ago.
Shiny Rocks
As useful as copper was to early civilizations, and for as easily accessible as it was thanks to surface deposits of native copper sprinkled around the world, it was not the first metal to be discovered and worked. That honor falls to both gold and, strangely enough, meteoric iron. But neither of these metals was abundant enough to make anything but a token impact on technology, and mostly ended up enriching and ornamenting kings and princes.
Copper, however, was easily located and, perhaps more importantly, easily worked without the need to develop much infrastructure — at least at first. Lumps of copper could be pried from native copper deposits and cold-worked with stone tools into useful artifacts, thanks to copper’s malleability. It wasn’t long before copper’s relatively low melting point led to the discovery of casting, which led to more uses for the metal and increased demand.
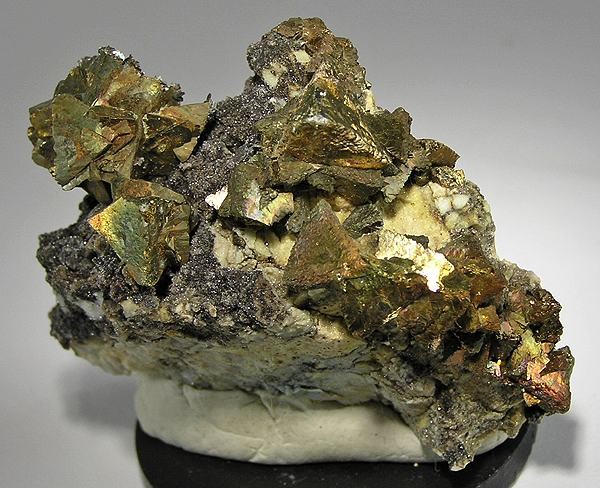
Eventually, supplies of native metal from easily exploited deposits couldn’t meet demand, and our ancestors discovered smelting from various copper-bearing ores. The most important ore for commercial copper production is called chalcopyrite, an iron-containing copper sulfide mineral with the chemical formula CuFeS2. Chalcopyrite deposits are found all over the world, with particular abundance in North and South America, as well as Africa and Australia. Other important ores occur as oxides and carbonates of copper, like azurite and cuprite.
Although some deep-shaft mining is done, most of the big copper mining operations are vast open-pit mines. The world’s most productive copper mine right now is the Minera Escondida in the Atacama Desert in Chile, which produced $10 billion worth of copper in 2007 and can output 1.2 million tons a year. While a pure sample of chalcopyrite is about 34% copper by weight, the mineral is usually associated with a host rock species that reduces the ore to a fraction of a percent of copper. This means that vast amounts of ore have to be processed to make a mining operation commercially viable. In some deposits, gold and silver are sparingly substituted for copper in the ore, making these precious metals a valuable side product that in some cases can actually pay for the entire cost of extraction of all the copper.
Extraction in open-pit mines begins with typical hard-rock mining methods, like blasting. Ore-bearing rock is loaded 200 to 300 tonnes at a time by enormous loaders and shovels into mammoth haul trucks, for the trip up out of the pit to the processing plant. There, enormous crushers reduce the car-sized boulders into smaller and smaller fractions, which are passed to ball mils for finer grinding. The goal is to reduce the physical contact between the ore minerals and the waste rock that surrounds it, which is called gangue.
What happens next is the extraction of the elemental copper from the ore minerals, but the method used depends upon which type of ore is present. For oxides and carbonates of copper, the copper is soluble in acid solutions, so a hydrometallurgical process is used. Details vary, but in leaching processes, typically the powdered ore is piled up in large pits lined with an impervious barrier. Dilute sulfuric acid is sprayed onto the piles and leaches copper sulfate from the ore minerals. The copper is stripped from the leachate with special extractants, which leaves the sulfuric acid clean and ready to be recycled for another round of leaching, plus a copper-rich solution ready for further purification.
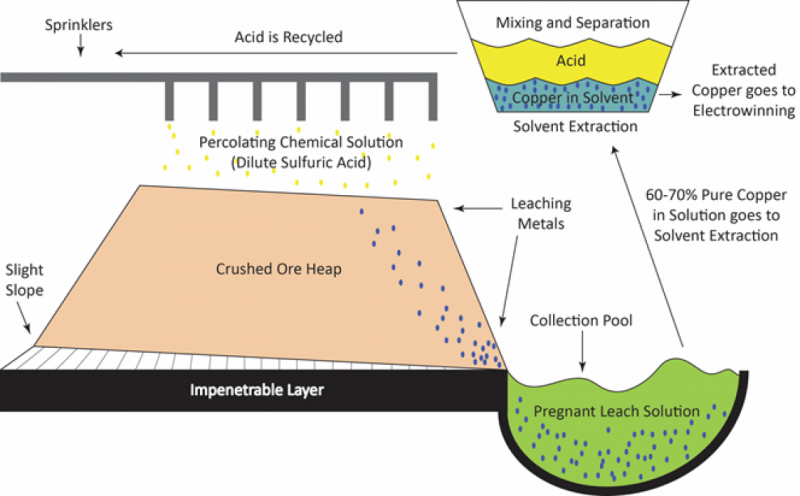
Floating to the Top
Copper sulfide ores are at a disadvantage when it comes to chemical methods of extraction, since the sulfides are barely soluble in acid. To free copper from these ores, refiners need to turn up the heat with pyrometallurgical methods. These begin with the same crushing and grinding steps as before, resulting in a fine powder that is mixed with water in large vats. To the slurry are added chemicals known as collectors, whose job it is to bind to the sulfide mineral particles. The collector molecules cover the sulfide particles and increase their hydrophobicity, or tendency to repel water, while leaving the waste rock particles alone. When air is bubbled through the solution, the now-hydrophobic sulfides attach to the air bubbles and form a froth at the surface of the vat, which is skimmed off the top and subjected to further rounds of this froth flotation method to increase the concentration of copper.
The output from this froth flotation process is then put through a thickening process, to remove as much water as possible. This is done by a combination of simple evaporation in open ponds, and by filtration using porous ceramic discs or cylinders. The filtration step is critical, as it lowers the moisture content to around 8% and results in a copper concentrate of about 20-30% enrichment that can be easily shipped to smelting plants.
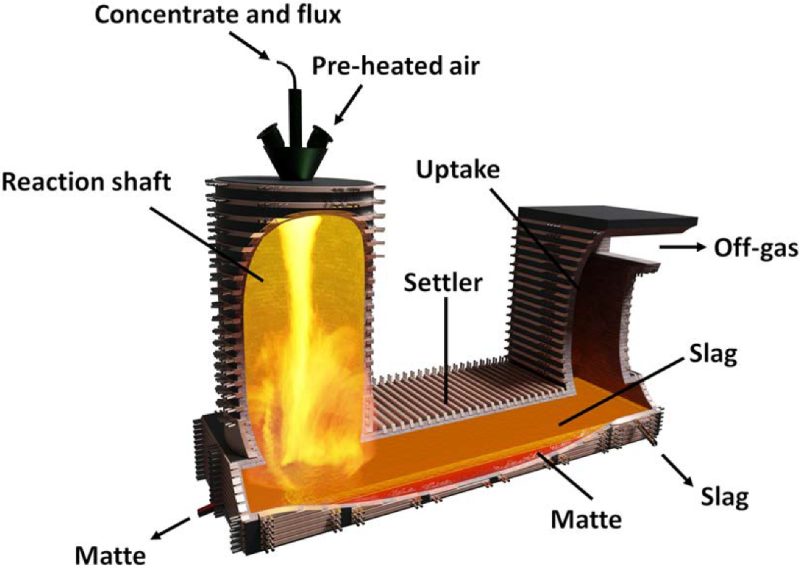
To extract the copper from the concentrate, a flash smelting process is used. Concentrate is sprayed into a reaction column in a flash furnace along with heated, oxygen-enriched air. The sulfide compounds in the concentrate melt instantly and fall to a collecting pool at the bottom of the furnace. There, the molten materials separate by density, with the molten copper, called matte copper, sinking to the bottom, while the iron and silicate slag floats to the top with the assistance of added fluxes.
Matte copper, now about 60% pure, is tapped off the bottom of the flash furnace for further purification through conversion, which is basically blowing hot air through the molten matte. The oxygen reacts with the remaining sulfur, leaving behind blister copper that’s about 98% pure.
Winning with Electricity
The final stage of purification for the end products of both hydrometallurgical and pyrometallurgical extraction is called electrowinning. This is simply electrolysis, albeit on a massive scale. For hydrometallurgical copper, the copper sulfate solution that comes from the leaching pit is used as the electrolyte, with lead anodes and thin stainless steel sheets for cathodes. Current is passed through the electrolyte, causing the copper in the solution to plate out onto the stainless steel cathodes. When about 100 pounds (45 kg) of copper have accumulated on the cathodes, they are removed, rinsed, and flexed to pop off the finished, 99.99% pure copper sheets.
For pyrometallurgical copper, the blister copper ingots serve as anodes for electrowinning. They are suspended in a tank filled with dilute copper sulfate mixed with sulfuric acid, interleaved with cathodes of either pure copper sheets or, again, stainless steel. Current is passed through the tank and the copper plates out on the cathodes, again reaching 99.99% purity in the finished process.
The waste product left behind in the electrowinning tanks is known as anode slime, and despite its unappealing name is a valuable product. Depending on the minerals present in the feedstock and the voltage used for electrowinning, the anode slime can contain gold, silver, selenium, tellurium, and possibly even platinum-group metals, along with a fair amount of copper that wasn’t recovered in the first go-around. Anode slime is generally sold off to specialty smelters for recovery of these valuable metals, using combinations of hydrometallurgical and pyrometallurgical processes that are customized to the blend of metals in the slime.
Banner image: “Native copper-replaced cross-bedded sedimentary rocks” by James St. John, CC BY 2.0
Fascinating read, thankyou for making it accessible and easy to follow.
For anyone in the UK I can recommend a visit to the ancient copper mines on The Great Orme hill/mountain in Llundudno, north Wales. First you take an original 1902 cable car up, and then find the site where the local council was going to build a car park. But they uncovered an ancient bronze age copper mine instead, going back 4000 years, all the tunnels filled in with the spoil from later tunnels. So far they have excavated 5 miles of tunnels all dug out of rock with bone and stone tools (they have found some of them) by candle light, some of the passages only just big enough for a child. Astonishing.
https://en.m.wikipedia.org/wiki/Great_Orme
That led me to a discussion of Welsh miners in the 1800’s and their lives. I thought it was interesting they only worked for 6 hours a day and when the mine owners tried to force them to work 8 they all quit and went back to farming and fishing. The System can’t grind you down when you have options!
One of the most interesting things I learnt about copper has to do with another metal: Copper is nearly impossible to remove from molten steel, once it found its way in. It can be done in lab environments but that’s not yet feasible for large scale production.
And as copper weakens most types of steel, it needs to be separated from the steel scrap in the recycling process before melting it. You can dilute the recycled and molten steel with purer forms of steel, though…
There’s a nice and open access article on that: https://doi.org/10.1007/s11663-019-01537-9
Escondida was a damn impressive hole when I saw it in the mid ’90s. It is heinously arid.
The story I was told goes:
When the american mining company was designing the mine, they asked how much rain. They were told 5mm, and the designers back at head office decided, that the pit could _just_ cope with 5mm of rain.
When they actually started making it, they discovered there had indeed been 5mm rain – in total – in the whole 150 years that records have been kept,
Inuit technology was non metal using,yet they indipendently
invented the screw thread for use in modular hunting spears,with
walrus ivory threads to hold points for hunting different animal
species,the spear shaft itself was the rare and valuble part 1000
kms north of the nearest tree.
This is just one of many examples of “technology” that pre date
the use of metal just by the humans living in the circum polar region of the planet.
But if smelting copper is your thing then I would recomend
the Kodo Zuroku,of which I am lucky enough to have a reprint of the original.
That or a coal forge,and a crucible and some borax for flux and whatever you can get for “ore”,scrap in my case, and a wax core,
which you dip in a slurry of durabond 90 drywall compound(many thin layers) in my case,sinter, melt, and cast.Works great.
I have access to copper ore and really want to recover the copper by smelting the ore, I wonder if you can share some information on how to do it effectively.
Kindly send to the following email address
Many thanks in advance.
fmakus@gmail.com
I’d say your Inuit technology examples go with the technology addressed in the first paragraph of the article. Spears, atlatls, bows, even the string to make the bow, they’re all technology of a kind but the beginning of the use of copper was a technological step change. There’s definitely a reason we separate stone age from bronze age.
Fascinating! And well-written. Thank you, Dan!
This part looks a little backwards: “Eventually, supplies of native metal from easily exploited deposits exceeded demand, and our ancestors discovered smelting from various copper-bearing ores.”
I’d not heard about people pulling out lumps of native copper before, but assuming that happened I’m pretty satisfied that it happened before smelting was discovered. Humans bashed enough stones together for enough years to notice the qualities of shiny stones that are easy to form into other shapes.
Oh, I’ve just come back here and re-read what you quoted. I thought you were talking about the discovery of smelting coming after the use of native metal, but now I see “supply … exceeded demand”. Yeah, I’m sure that’s wrong.
I believe it implies there was an excess that was used for experimentation rather than to meet need.
What about the “Hombre de Cobre” – the “Man of Copper” – pre-Hispanic copper miner who died in the 6th century in a copper mine in Chile and whose cadaver slowly turned to copper from dissolved copper salts over the centuries
https://youtu.be/DezcmnQ0-MA
If “fundamentally changing a naturally occurring material” is the requirement for something being technology, cooking fits even more than banging out a piece of naturally occurring metal (which is conceptually no different from sharpening a stick). Smoking meat to store, or cooking inedible stuff to get food/glue etc is very transformative, and I presume this predates metalworking. Predates smelting, definitely, no one would have access to fire and not use it for cooking for generations before smelting. :-)
I learned about copper has to do with another metal: once copper has gotten into molten steel, it’s nearly impossible to get it out. It can be done in a lab setting, but large-scale production is still a long way off.
Because copper weakens most forms of steel, it must be removed from the steel scrap before it is melted in the recycling process. However, you can use purer kinds of steel to dilute the recycled and melted steel…
There’s a good open-access article on the subject: https://techitour.com/