From space, the most striking feature of our Pale Blue Dot is exactly what makes it blue: all that water. About three-quarters of the globe is covered with liquid water, and our atmosphere is a thick gaseous soup laden with water vapor. Almost everywhere you look there’s water, and even where there’s no obvious surface water, chances are good that more water than you could use in a lifetime lies just below your feet, and accessing it could be as easy as an afternoon’s work with a shovel.
And therein lies the rub for those who delve into the Earth’s depths for the minerals and other resources we need to function as a society — if you dig deep enough, water is going to become a problem. The Earth’s crust holds something like 44 million cubic kilometers of largely hidden water, and it doesn’t take much to release it from the geological structures holding it back and restricting its flow. One simple mineshaft chasing a coal seam or a shaft dug in the wrong place, and suddenly all the hard-won workings are nothing but flooded holes in the ground. Add to that the enormous open-pit mines dotting the surface of the planet that resemble nothing so much as empty lakes waiting to fill back up with water if given a chance, and the scale of the problem water presents to mining operations becomes clear.
Dewatering mines is a complex engineering problem, one that intersects and overlaps multiple fields of expertise. Geotechnical engineers work alongside mining engineers, hydrogeologists, and environmental engineers to devise cost-effective ways to control the flow of water into mines, redirect it when they can, and remove it when there’s no alternative.
An Old Problem
You’d be forgiven for thinking that dewatering mines is just about building and installing big pumps; that’s pretty much where I was when I started researching this article in the wake of Hurricane Helene’s recent unwelcome visit to Appalachia and the potential destruction of the quartz mines at Spruce Pine, North Carolina. The mines there are the world’s single source for ultra-pure natural quartz, and flooding from the two feet (60 cm) of rain Helene dumped there threatened to shut down the semiconductor industry, thanks to the lack of natural quartz needed for the crucibles that turn raw silicon into high-purity wafers via the Czochralski process.
Luckily, the Spruce Pine mines somehow dodged that bullet, but the whole thing got me thinking about dewatering. I knew that pumping water out of mines went back at least to the beginning of the Industrial Revolution, with getting rid of water from coal mines being one of the driving forces behind the invention of the steam engine. Thomas Newcomen’s atmospheric engines were put to use pumping out coal mines in the West Midlands of England and tin mines in Cornwall as early as 1712.
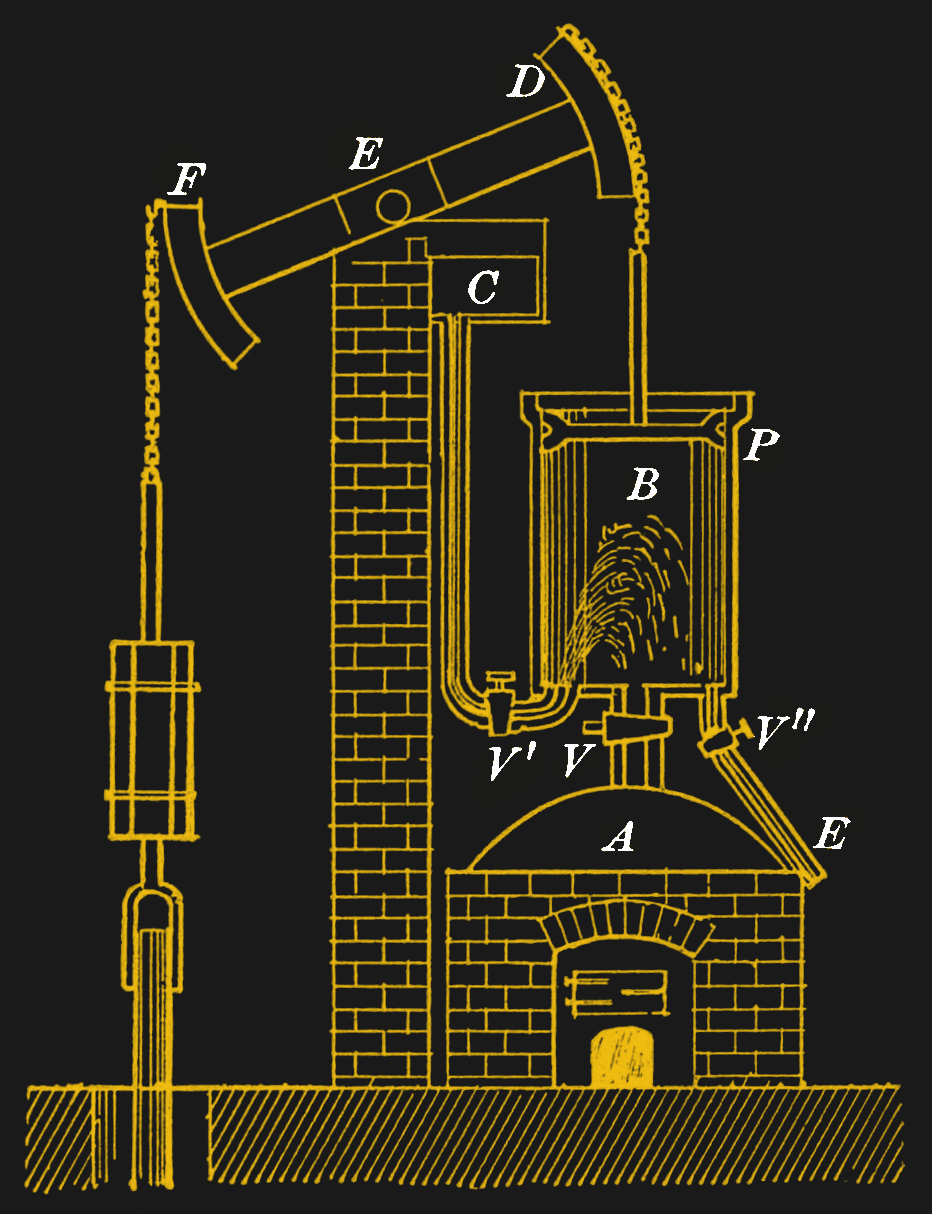
Early dewatering efforts were a brute-force affair, with the massive rocking arms of remarkably inefficient steam engines pulling pistons up and down inside pipes, lifting water to the surface and dumping it onto the ground to drain into streams and lakes. The pumps only needed to move water faster than it flowed into the mine, and woe betide the engineer who let his engine lag behind or fail completely so that the mine flooded. To make things worse, the water that was ejected from these mines was often quite polluted, especially in geological formations that resulted in the acidification of floodwaters. Spilling toxic and acidic tailings water onto the surface is famously destructive to the environment, a topic of much less concern back then.
Current dewatering processes are much more mindful of the environmental impact of pumping contaminated water onto the surface, and are also sensitive to the incredible costs of running pumps and water treatment plants around the clock. These days, a lot more effort goes into controlling and managing water before it ever gets into the mine’s workings, and passive methods of dewatering are favored wherever possible. It also matters very much what kind of mine is being dewatered; while the basic processes are similar for open-pit versus underground mines, there are important differences.
Underground mines generally have the advantage of penetrating below the local water table. If the mine’s workings are sufficiently far below the groundwater layer and the rock between them is relatively impervious, the mine might be naturally dry. That’s rarely the case, though, as the shafts and ramps that pass through the water table generally liberate water that then flows into the lower parts of the mine, eventually flooding it to the level of the water table. Sometimes it’s possible to mitigate this by drilling wells into the local water table further up the hydraulic grade; the clean water pumped from these wells causes a “cone of depression” in the local water table, lowering it enough to reduce the flow of water into the well to a manageable level.
In other cases, it may be possible to create an impervious barrier between the porous water-bearing rocks and the mine’s workings. The idea here is to redirect the water, preferably so that it finds other hydraulic paths of less resistance rather than flooding into the workings. Grouting mine workings can use cementitious materials like so-called “shotcrete,” a thin concrete that can be sprayed onto rock surfaces. Other grouting jobs are best accomplished with polymeric materials like urethane resins. No matter what material is used, water is kept from entering the workings thanks to drainage pipes and adits built between the water table rocks and the inside of the applied impervious barrier. The redirected water collects in local sumps, where large electric pumps send it out of the mine for processing.
Big Digs
One interesting way to mitigate the flow of water into workings that penetrate the water table is by freezing it. Ground freezing has been used to stabilize wet soils on construction sites for years, with the technique gaining fame during the Boston “Big Dig” megaproject, which buried sections of Interstates 90 and 93 in the saturated fill that most of Boston is built upon. Ground freezing uses massive refrigeration plants to circulate chilled brine in pipes buried in the wet soil, freezing it solid. In mine dewatering, ground freezing is often used around a shaft or ramp passing through the water table. The drawback to ground freezing is the need to operate a refrigeration plant around the clock, but in some instances, it’s more cost-effective than grouting or other passive methods.
Open-pit mines present their own dewatering challenges. By definition, open-pit mines are near the surface and therefore closer to the local water table, which tends to be within the first few hundred meters from the surface. Open-pit mines also tend to disrupt much more surface area of the water table, as opposed to the numerous but relatively small penetrations caused by underground shafts and tunnels. There’s also the compounding problem that open-pit mines are exposed to the elements, meaning that precipitation into the mine and runoff from the local catchment area can introduce massive amounts of water, all of which has to be managed.
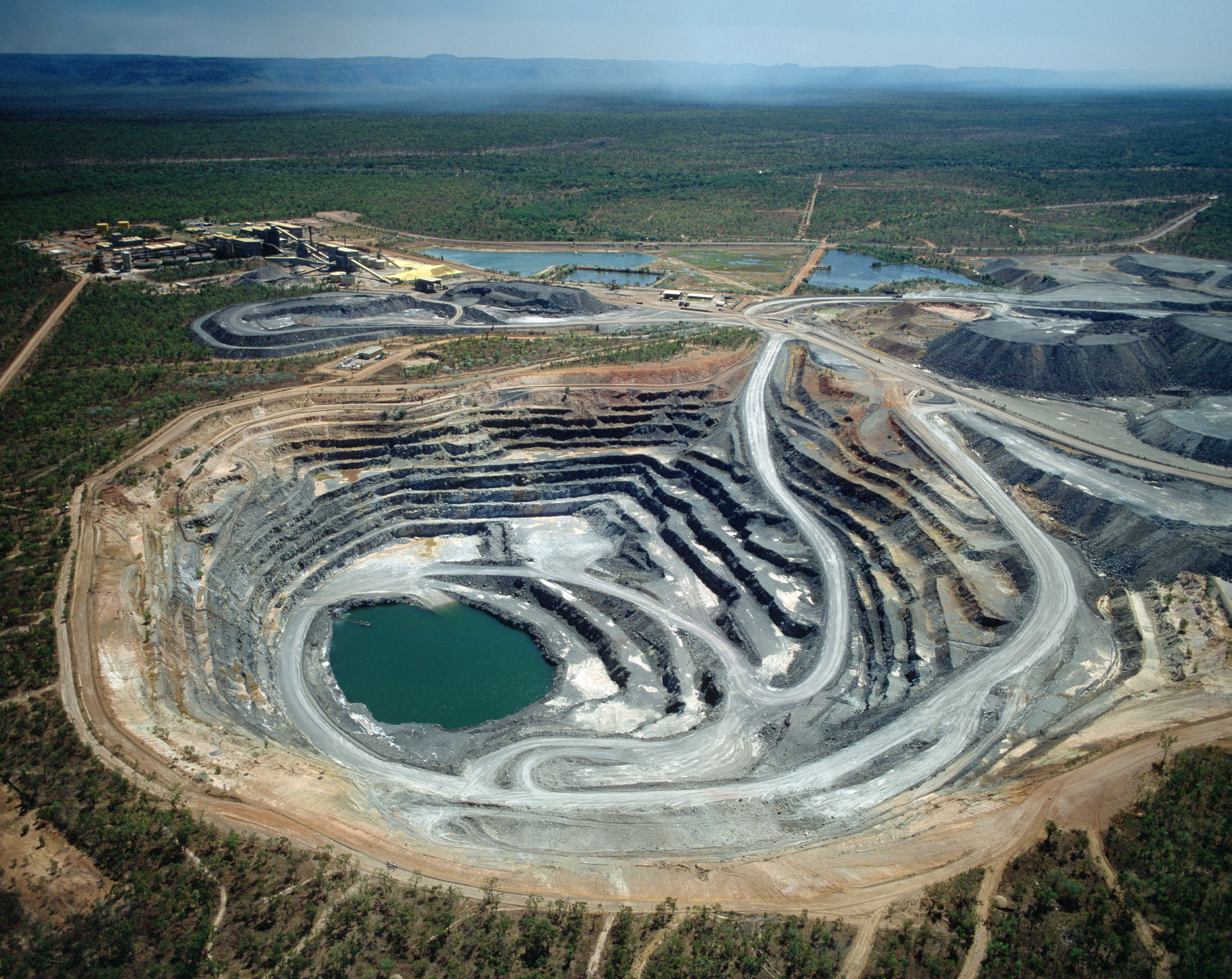
As with underground mining, dewatering open-pit mines starts with preventing as much water as possible from entering the workings in the first place. Surface berms and swales are often constructed around the perimeter of the mine to control and direct storm runoff into retention ponds, where water can evaporate naturally. Also, dewatering wells are often drilled vertically around the perimeter of the mine, and sometimes horizontally from the walls of the mine into the local water table, to intercept water flowing in the local water table before it enters the mine. Passive dewatering techniques are also used, such as filling cracks with grout or sealants.
The importance of removing water from open-pit mines can’t be overstated. Excess water is a real problem in terms of mine productivity; wet material is heavy, and the huge haulers that bring material up to the surface have to work harder to carry something the mine will make no profit from. Also, the pressure exerted by water in the soil tends to reduce the mechanical strength of the material, making it necessary to cut the walls at a shallower angle than in dry material. That results in removing far more overburden to get to the producing ore body, which might be the difference between a profitable mine and an expensive hole in the ground.
Underground Guitars
Monitoring pore pressure in the groundwater around a mine is one of the biggest parts of dewatering, so much so that mines will install far-flung networks of pressure sensors in and around their workings. The data gathered from these networks not only helps decide where to concentrate dewatering resources, but also serves to monitor how well those efforts are paying off, and to help redirect resources in case the hydrogeological environment changes over time, as it is likely to do.
The chief instrument used today for monitoring pore pressure in mining operations is the piezometer. From the name, one imagines these devices measure water pressure thanks to a piezoelectric transducer. And while there are piezometers that approach, the more common piezometers in use today are of the vibrating wire type. Vibrating wire piezometers, or VWPs, are similar to electric guitars. A thin steel wire is tensioned between a fixed point and a flexible diaphragm. The diaphragm is exposed to the environment, often through a filter to keep debris in the groundwater from getting packed against the diaphragm. The wire’s tension varies as the diaphragm is deflected by water pressure, which changes its resonant frequency. A coil of wire surrounding the steel wire serves to both excite it, like plucking a guitar string, and as a pickup for the resulting vibrations. The higher the pressure outside, the further the diaphragm deflects, which lowers the tension on the string and results in a lower “note” when excited.
VWPs are expected to operate under extreme conditions, so they’re built to last. Most are built from stainless steel cases that can survive inside deep boreholes, and some are even made to be driven into soil directly. Most VWPs include on-board thermistors to adjust pressure readings for the temperature of the water, as well as gas-discharge tubes to protect the sensors and the drivers they’re connected to from lightning strikes and other electrical discharges.
Love informative articles like this.
For some reason the engineering around water and the movement of it is of great fascination to me.
Thanks for compiling this information!
dewatering mines at scale is even older than the first steam engines (see https://en.wikipedia.org/wiki/Upper_Harz_Water_Regale#History for rabbit hole entrance and the dissertation of Richard Brüdern, 2018, about water wheels for a deep toss into this and adjacent rabbit holes)
Pumping water out of mines goes back to at least Roman times. This link goes to a documantary originally shown on Spanish TV, but now available in English. The presenter was a one time Civil Engineer who retrained as an archaeologist. It lasts an hour but it (and the other documentaries in the series) go far deeper into the practicalities of Roman Engineering than any other programme I have seen.
https://www.youtube.com/watch?v=2pLjzlSz4R4
Go to 32 mins in if you just want to see the bit about drainage, but you’re missing a lot.
…And here is a dramatic case of mine re-watering: https://en.wikipedia.org/wiki/Lake_Peigneur
Shorcrete isn’t really used as a hydrostatic barrier, the stuff is pretty porous and let water pass through, it’s meant to be surface support for tunnels. When you’re making new tunnels you’ll occasionally drill probe holes to see if you’re interesting large geological features that will make a lot of water, when you do you’ll setup a grout plant and pressure grout the hole to fill the broken feature up with cement before proceeding with any more tunneling.
And here is one case of a mine re-watering that is an attraction. I have dove Billion Gallon lake as it is known and the mining tools and carts at around 60-70 feet are awesome. Bonne Terre Lead Mine south of St. Louis is a year round scuba destination.
https://bonneterremine.com/
In Canada, the Giant mine has 50,000 tonnes of arsenic trioxide sitting around, held at bay from the water table (it’s literally in the middle of town) by nifty carbon dioxide heat siphons keeping the permafrost frosty. Better hope that global warming stops before the heat siphons do!
Thanks this has been my favorite read this week