Most of us have seen those demonstrations of metal parts that mate together so finely that, once together, they have no visible seam at all. But how, exactly, is this done? [Steve Mould] has a video that shows and explains all, and we’ve never seen the process explained quite like he does.
The secret ingredient is wire EDM, or Electrical Discharge Machining, but that’s only one part of the whole. Wire EDM works a bit like a hot-wire cutter slicing through foam, but all by itself that’s not enough to produce those impossibly close-fitting parts we love to see.
EDM is capable of astounding precision in part because — unlike a cutting tool — nothing physically contacts the material. Also, there isn’t a lot of friction and heat causing small distortions of the material during the machining process. EDM is as a result capable of fantastically-precise cuts, but not invisible ones.
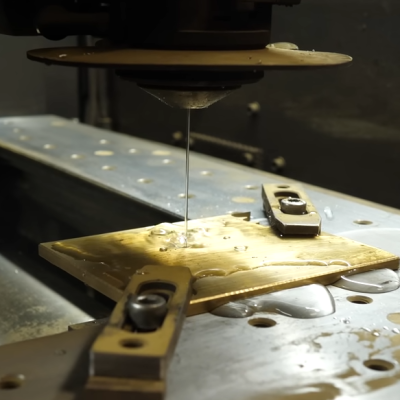
In all good manufacturing, the capabilities (and limitations) of the tool are taken into account, and this is also true for making those close-fitting pieces. The hole and plug are actually made in two separate stages.
The hole is cut separately from the plug, and because EDM is capable of such finesse, the cuts can be made in such a way that they complement one another with near-perfection. After that, grinding and polishing takes care of the surface finish. The result is the fantastically-smooth and apparently seamless fitment we like so much.
The video is embedded below, and there are some great details about EDM and how it actually works in there. For example, we see how a wire EDM machine can use a jet of water to help thread the wire through a hole in the part to start a job, and we learn that the wire is constantly moving during the process.
As cool as wire EDM is, it is not magic and we’ve seen some pretty remarkable efforts at bringing the technology into the home workshop.
I did wonder how they got the wire into the middle of a chunk of metal in the first place. Figured they must have drilled a hole and threaded it through, then cut out from there. The water jet is clever.
Yes, drilling a pilot hole is required. FWIW, many industrial grade CNC mills can hold a tolerance tight enough for that invisible seam effect.
You would use a sinker? I used a brass cylinder, (tube) sparking around the circumference eroded a pilot hole for the wire. If you’re EDM ‘ing the material is probably hard to machine with tooling.
I mill and drill hardened steel quite frequently. Cutter technology has improved greatly over the past 20 years. It’s even posible to mill tungsten carbide.
The water jet is not cutting metal but just guiding the wire through an existing hole. The holes are either drilled by standard means or with a EDM drill “hole popper” on a separate machine and then the thread locations are transferred as part of the cut file.
We sometimes use a simple EDM machine we call a “hole popper” to create that pilot home.
Some dude using a mouse sander on cheese is not what I thought I’d see on Hackaday when I woke up this morning.
All the more impressive, using tools so humble.
“there isn’t a lot of friction and heat causing small distortions of the material during the machining process.”
this part is just wrong on so many levels it isn’t even funny. Commercial discharge machines have a ton of friction, not from normal means of a cutter to the material but the burnt material itself. it doesn’t just disappear and magic no friction. NO it is still there and needs to be flushed this is why you see the parts often submerged completely or massive flow over the part. Otherwise it gets gummed up, causes contact and wire breakage. Also heat is a big factor in the process of an EDM. it literally burns the material away by arcing it. this causes a massive amount of heat and I know several EDM shops that do not need to run any type of heat during the winter because of this byproduct (northern midwest so it can get cold)
also some edm’s do have drills to get started they don’t use just waterjet’s.
sinker edm’s are fun as well, but if you really want to see something cool look into high precision sinker edm lathes, the tech there is insane.
You are incorrect.
There really is no friction in the cutting action of an EDM. There’s more friction in the drive mechanism of the machine depending on how it’s powered but the actual cutting creates zero friction, because the electrode whether it is a diesinker EDM, or wire, never touches the workpiece.
The flushing action is necessary to remove the abilated material that electricity blasts out but there is no friction from this, The flushing is critical to continue actually moving forward. If flushing is not correct, the machine shorts out and stops.
The actual machines themselves do generate heat and the workpiece would be very hot if flushing was not there, from the amount of current going into the workpiece blasting the material way using electricity. Anybody who works in a machine shop knows the machinery including EDM of course generates heat from the drive of the machine, and oftentimes in winter heating aside from the machines is not necessary though it depends on the work environment.
There is a heat affected zone with EDM parts, but it is very small if done correctly. Sometimes that does have to be accounted for depending on what the material end use is, but the heat affected zone is usually very very tiny into the part. We are talking in the thousandths of an inch range of depth into the part past the cut surface. So the parts are affected by heat but very little.
I used to run diesinker EDM.
I’ve poked around the wire EDM machine in our precision shop at work, and the amazing part to me is that they can hold the wire as accurately and consistently as they do.
It’s important to remember that the wire is not fixed, it’s eroding along with the part, so the machine has a big spool of brass wire that’s constantly being pulled through the cutting zone in order to keep fresh, full diameter stock ‘cutting’.
That implies that the 10mil wire slides through some sort of guides above and below the part that keep the wire in place to a few tenths of a thou – while it’s moving at a noticeable clip. Judging by all the gripping and guiding wheels, maybe a few inches a second.
Also, the wire is regularly cut to thread it through a hole in the part to do enclosed features, so whatever guides it has to accommodate that process, dealing with the rough ends.
I don’t know what that technology is, it’s buried deep enough inside the heads you can’t really see it, but it’s pretty incredible that you can drag – literally – miles of wire through it every day and still keep the tolerances they do.
On the Agie wire erroder I worked on these were called saphire guides, miniature Vee blocks made from a synthetic diamond of some sort, although they lasted a while they did need changing.
Also the top guide had XY motors that enabled tapered cuts.
These are synthetic industrial sapphire guides, I would not be surprised if there are synthetic PCD diamond guides on some very high-end machines as well.
The really cool tech is on Sodick wire EDMs- on their newer machines they actually have a proprietary technology that not only feeds the wire like everyone else, but actually twists the wire continuously as it feeds, so that the full diameter of the wire regardless of the direction is being used at all times for the cut, which not only leaves a straighter cut but a better finish and burns much more consistently.
I saw it in person at IMTS and it was explained to me how it worked was a special wheel guide that induces a twist in the wire above the workpiece and forces it to turn as it feeds it. It’s not something you can see the wire doing but it’s spinning the wire perfectly on axis as well as feeding it through. How someone came up with that in the first place is pretty wild to me. They are the only company using that technology for EDM right now.
Hmmm… new 3d printing design challenge… “Razor Blade Adapters”
I guess if someone has the specs one could design the fuel rod adapters too. I don’t think anyone would be using them though.
I enjoyed his advertisement at the end where he shaved one side of his face using the advertised product and the other side using a cartridge razor with the protective plastic cover still in place…