Launching things with electromagnetism is pretty fun, with linear induction motors being a popular design that finds use from everywhere in hobby designs like [Tom Stanton]’s to the electromagnetic launchers on new US and Chinese aircraft carriers. Although the exact design details differ, they use magnetic attraction and repulsion to create a linear motion on the propulsive element, like the sled in [Tom]’s design. Much like the electromagnetic catapults on a Gerald R. Ford-class carrier, electrical power is applied to rapidly move the sled through the channel, akin to a steam piston with a steam catapult.
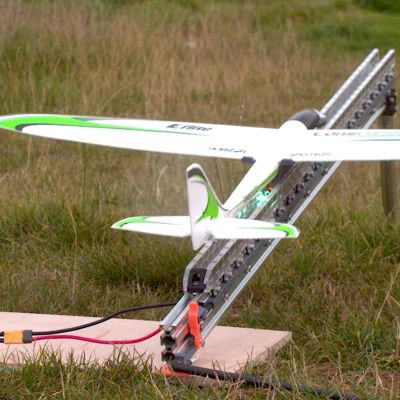
For [Tom]’s design, permanent magnets are used along both sides of the channel in an alternating north/south pole fashion, with the sled using a single wound coil that uses brushes to contact metal rails along both sides of the channel. Alternating current is then applied to this system, causing the coil to become an electromagnet and propel itself along the channel.
An important consideration here is the number of turns of wire on the sled’s coil, as this controls the current being passed, which is around 90 A for 100 turns. Even so, the fastest sled design only reached a speed of 44 mph (~71 km/h), which is 4 mph faster than [Tom]’s previous design that used coils alongside the channels and a sled featuring a permanent magnet.
One way to increase the speed is to use more coils on the sled, with a two-coil model launching a light-weight model airplane to 10.2 m/s, which is not only a pretty cool way to launch an airplane, but also gives you a sense of appreciation for the engineering challenges involved in making an electromagnetic catapult system work for life-sized airplanes as they’re yeeted off an aircraft carrier and preferably not straight into the drink.
How is it an induction motor?
‘Tisn’t. It’s a linear, brush-commutated, DC motor.
It induces linear. A distinct linear is induced in whatever you strap on top of it
Hi, this is nice and relatively simple. The biggest problem is mechanical contacts. Would you like to consider to use electronically one using Hall sensors and MOS-FET tranzistors replacing fizical contacts. Another ideea is to use a magnets for moving part and fixed coils, switched electronically using the same system with Hall sensors.
I agree with this, it would allow a computer to ramp and time the pulses for maximum effect.
However it would mean either electronics and capacitors on the sled with continuous brushed power, or a ribbon capable of acceleration to follow the sled. Possibly ‘noodle wire’ and higher voltages?
Either way, fun!
He already did it in a previous vid with a teensy and hall sensors before each coil, the sled used magnets only.
I’ve always wondered looking at linear rails designs is, doesn’t the sled speed up along the channel which means, that the timing when to trigger the poles need to change? Like, using AC on the coil will switch poles at 50/60Hz. this would not necessarily have the correct pole alignment at the correct time for best efficiency.
Who needs AC? It has brushes that switch the coil at whatever speed it happens to be going
“linear induction motor”
Is that another way of saying “large rubber band”?
B^)
I thought it was a fancy way of saying “miniature rail gun” 😂
Yeah, but this one is miniature coil gun.
Linear motors are very cool but, 4mph/44mph = 1.1 times as good as the earlier design. I think I’d sooner take the reliability and longevity improvements of the earlier brushless version and tolerate not getting quite as much speed at the output end.
138 g airplane at 10.2 m/s is 7.2 J imparted to the load.
His current numbers don’t add up (claims 90 amps at 48 volts, but measures 2 ohms in the maybe different coil).
But assuming a pair of 2 ohm coils in parallel in the final rig, and 3x12V supply, that’s 36 amps x 36 volts. With a 0.1 second duration that’s 130 J from the source, for an efficiency of 5.6%. Right on par with an aircraft carrier steam catapult.
If you count the energy gone into the sled, that actually 11.4J imparted into the accelerated mass, or 8.8% efficiency.
Pretty good for a design with so much obvious room for improvement.
Interestingly, scaling this up to something like a F-14, you find that it would take the simultaneous full capacity output of all eight nuclear reactors at on the USS Enterprise to launch the plane.
Does anyone know what the video tracking software he uses to characterise the speed of the sleds is? Looks very useful.
Ages ago, he used to use Physlets Tracker.
https://hackaday.com/2018/09/10/trebucheting-tennis-balls-at-124-mph/
Is that still a thing?
Too bad you can’t use a model rocket engine as JATO.
Maybe a CO2 cartridge?
A very cool, just to do it (I assume) project. Bungee cords, of course, are cheaper and more practical.
Freewheeling diodes one each coil will reduce the arcing. The disadvantage is with the stored energy being released back into the coil, the magnetic fields slightly extended.
It’s not an induction motor. It’s a linear brushed DC motor.
I’m attempting to make a similar rc plane launcher is there any things I need to know?