[Madox] is a trackball user, which is fine; we at Hackaday respect and appreciate those who live alternative lifestyles. As you would expect, there aren’t many makes and models of trackballs being sold, and [Madox] wanted something ergonomic. A DIY solution was necessary, but how to you model something ‘ergonomic’ before printing it out? Floam, apparently.
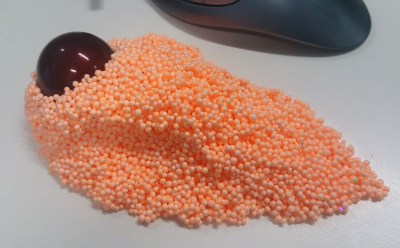
Floam is a sticky, moldable goo originally sold as the follow-up to Nickelodeon’s Gak in the early 1990s. It consists of styrofoam pellets held together with a colored binder that doesn’t leave a mess and doesn’t dry out. While the Nickelodeon version is lost to the sands of time, a Floam-like substance is available at any toy store. [Madox] picked up a few blister packs and began modeling his ideal trackball.
With the proper shape in hand, [Madox] needed a way to get this design into a computer. Photogrammetry is the solution, and while earlier experiments with Autodesk Catch were successful, Autodesk has morphed and rebranded their photogrammetry software into Autodesk ReMake. Turing a pile of styrofoam balls into a 3D model is as simple as taking a bunch of pictures and uploaded to Autodesk’s ‘cloud’ service.
In just a few minutes, a proper 3D mesh arrived from the Autodesk mothership, and [Madox] took to importing this model into Fusion 360, fiddling with chamfers, and eventually got to the point where a 3D printer was necessary. It took a few revisions, but now [Madox] has a custom designed trackball that was perfectly ergonomic.