The Wheatstone bridge is a way of measuring resistance with great accuracy and despite having been invented over 150 years ago, it still finds plenty of use today. Even searching for it on Hackaday brings up its use in a number of hacks. It’s a fundamental experimental device, and you should know about it.
How It Works
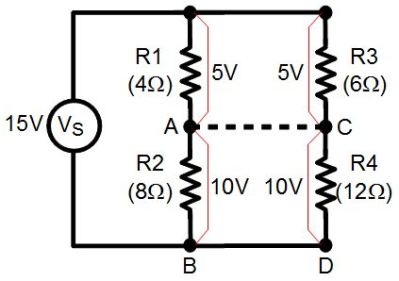
Here’s an easy way to understand how the Wheatstone bridge works. In the schematic are two voltage dividers (pairs of resistors in series): R1 with R2 and R3 with R4. If you do the math, you’ll notice that the voltages across R1 and R3 are the same, as are the voltage for R2 and R4. That’s because the ratio of the resistances R2/R1 is the same as the ratio R4/R3. Both form divider networks and both divide the voltage the same way.
But the key is that if we were to measure the voltage between point A and point C, you would read 0 volts between them, no current would be flowing. At this point we say that the Wheatstone bridge is balanced.
Now let’s say we don’t know the resistance of R4 (let’s instead call it Rx). And let’s connect A and C through a galvanometer as shown above. If the current is 0 amps then we can find the value of Rx. That’s because, as we said above, when no current is flowing between A and C, the ratio R2/R1 must be equal to the ratio Rx/R3. Rearranging, we get Rx = (R2*R3)/R1, and solving, we get (8*6)/4=12 ohms.
But what if there is current flowing between A and C, or we could ask what if there is a voltage across A and C? In that case we’d change R2 from a fixed value resistor to a potentiometer, as in the second diagram above. Note that points B and D were really electrically the same so we can make them the same point and redraw the schematic in the more common diamond shape for a Wheatstone bridge. When we turn on the circuit, the galvanometer would likely show current between A and C. We’d then adjust the value R2 until the galvanometer shows no current. We could then measure the resistance of R2, getting 8 ohms, and then do the above math again and see that Rx is 12 ohms.
In fact, that’s just what I’ve done as shown in the photos to try it out. Of course there was no doubt that it would work, but I couldn’t resist (get it?) seeing it for myself.
But the question arises, if we can measure R2 then why couldn’t we have just measured Rx instead? Well, Rx could be a strain gauge integrated into a building and so we couldn’t get at it to measure it. We’ll see strain gauges more below. Alternatively, the change in resistance could be so small that our meter couldn’t be relied upon, in which case we’d actually be amplifying and measuring voltage instead, but we’ll talk about that below too.
Wheatstone Bridges In Strain Gauges
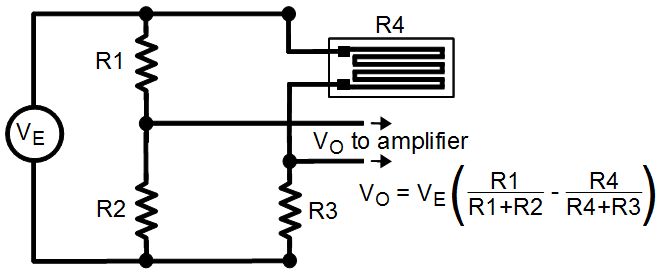
Due to the Wheatstone bridge’s ability to measure very small changes in resistance, it is often used for measuring the strain on strain gauges. These detect changes in buildings, bridges and other structures.
Pictured is a Wheatstone bridge with a strain gauge as R4. Stretching a strain gauge causes a change in its resistance, hence a strain gauge is a variable resistor. Either one, two or all four resistors can be strain gauges and the bridges are respectively called quarter-bridge, half-bridge or full-bridge Wheatstone bridge circuits.
Note that the voltage output, VO, is so small that it needs to be amplified to be useful by further circuitry. The formula shows how VO is related to the excitation voltage, VE, and the resistances.
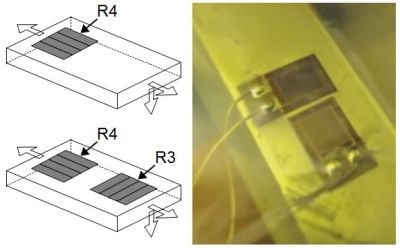
Pictured here are tension bars with strain gauges built into them for measuring strain. The one with only one strain gauge is a quarter-bridge.
The other tension bar has two strain gauges and so is a half-bridge. However, R3 isn’t bonded to the strained material and so won’t be affected by strain. Instead, R3 is there to compensate for the effect of changes in temperature. Changes in temperature cause both to expand or contract but because it’ll affect both the same, the ratio of their two resistances due to temperature will remain the same and will not affect the output voltage. In this way only the change in resistance due to strain in R4 will affect the output voltage. In the photo you can see strain gauges in the same configuration glued to a bicycle crank.
Strain is denoted by ε (the greek letter epsilon) and the relationship between strain and the change in resistance is defined by this formula.
There the change in the resistance is related to the strain and a gauge factor k which is a characteristic of the strain gauge and has been derived from experiment. More than that is beyond the scope of this article but can be found in this publication on applying the Wheatstone bridge (PDF).
Measuring Small Temperature Changes
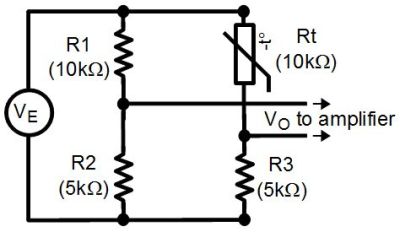
Measuring small temperature changes can be done with a Wheatstone bridge and a thermistor. A thermistor is an electrical component whose resistance changes with temperature. As shown, we put the thermistor in the bridge as the resistor whose value we want to measure, though we don’t measure it directly.
In this case we don’t balance the bridge. Instead we directly use the differential voltage between the two sides of the bridge, VO. VO is then proportional to the change in the thermistor’s resistance, Rt, and is mapped to a temperature.
One thing to look out for is that too high a current will cause extra heating in the thermistor. In that case we keep the excitation voltage low. But that causes the output voltage, VO, to be low too. We solve that by putting an amplifier after the output.
There is also non-linearity in the way the thermistor’s resistance relates to temperature. If the temperature range being used is a small one then that’s less of an issue. However, some thermistor manufacturers give formulas for when their thermistors are used in Wheatstone bridges, as with this one.
Finding Faults Underground – Murray Loop Test
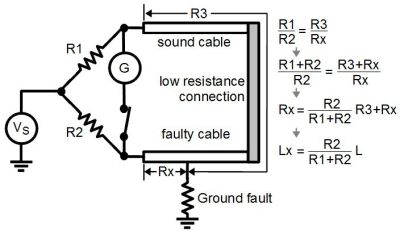
The Murray loop test is a method of using a Wheatstone bridge to find the location of a fault in underground wiring without having to dig first. One way to make the test is to use the setup shown. The faulty cable is the one that’s underground with a ground fault at some unknown location along its length. A sound cable is connected to the faulty cable using a wire whose resistance is low enough so as to not affect the test.
Lx is the unknown length of a portion of the faulty cable shown whose resistance is Rx (also unknown). L is the known length of the sound cable and the faulty cable combined. If the cross-sectional areas of the sound cable and the faulty cable are the same then the resistance of the two conductors is proportional to their lengths. That allows us to do the substitution in the second last equation to get the final equation solving for Lx, shown in the diagram.
With this used for a Wheatstone bridge, we first have to balance the bridge, meaning that the current through the galvanometer has to be made zero. That’s when the ratio in the first equation is true and therefore the remainder of the equations are also true. But once it’s balanced, we know R1, R2 and L and we can solve for Lx. Knowing the length Lx, we know where to dig to repair the fault.
Conclusion
We said you can find Wheatstone bridges in hacks here. One such is this digital scale made from scratch using a strain gauge. Another is this bike power meter with strain gauges glued to the pedal crank, including gauges for temperature compensation as described above.
And we could go on and on talking about uses for the Wheatstone bridge. For example, we haven’t even covered its use in AC applications and measuring capacitance and inductance. Perhaps we’ll leave that for another time. For now we’d love to hear about your uses for Wheatstone bridges in measuring resistance and any other things you’d like to add to the above from your experience.
Ah the joys of doing a Wheatstone bridge lab with 20% tolerance resistors and an instructor out to make us figure out a work around using math and patience.
Go on….
What , and rob some student of the satisfaction of working it out themselves?
These nulling methods are really cool. I can recall that in my yoot, I was quite puzzled over how the precise measurements of the second half of the 1800’s were made without amplifiers. The answer was the clever null balance devices like the potentiometer, and beyond clever physics in things like the ballistic galvanometer. The theory of these instruments is worth serious study. The broader your physical measurement tool kit the better.
On of my prized possessions is a ballistic galvanometer complete with a leather case that I found decades ago scrounging the trash of the local telco CO when they were converting it from Strowger switches. Don’t use it for anything but I do love it.
Okay, that does it. I don’t know what a ballistic galvanometer is but it sounds too cool to not look up… Awesome. Doesn’t involve the same magnitude of ballitics offered by, say, a trebuchet, but I love instruments where the principle is derived by very simple math (https://en.wikipedia.org/wiki/Ballistic_galvanometer).
I have one of the large ones that hang on a wall or in a special mount for the table top. The quartz fiber was broken when someone gave the T handle tensioner a couple extra cranks. I found an old book with a how-to for replacing it and calibration, but have not tried.
I dropped a 5-pack of strain gages in the traveling hacker box this weekend, and they disappeared pretty quick. I hope whoever grabbed them reads this article!
Any buddy know where the box is now. The box that gets mailed around the world with parts.
I for get what it was called. I do know that hackaday has a few of them going around.
Maybe it time to do another story on them.
Great article.
Don’t forget the use in mass airflow sensors (MAF) based on thermal loss on a Wheatstone bridge – every car engine has one (or several). You can argue among yourselves whether you’re measuring laminar or turbulent airflow at the sense-point though…
Thanks for that bit. My vehicles are pretty long in the tooth these days, and I’ve had to get to the component level on a few things, like the fan speed controller and the EATC, so MAF info intrigues me. You don’t happen to know how an EATC interprets the potentiometer sensor of an electronic controlled blend door, do you? Leads are to all three points on a pot, so rather than dig out the dash, thinking of cutting in with a pot to simulate position. I have the read values, but am wondering if I need to current limit with a 250 ohm resistor or something since read values are listed at 250+. Door moves, just never settles down.
Sir Charles Wheatstone is a distant great uncle of mine
I work for a company that makes platinum resistance thermometers, and we’ve got a white paper that includes some of this, if anybody’s interested (http://www.minco.com/~/media/Files/Minco/Whitepapers/Sensors/Resistance-Thermometry.ashx, page 10 shows Wheatstone and Murray bridges), it shows variations on how we use this for measuring 3 and 4 lead resistance sensors as well, which compensate for the resistance added by long lead wires connected to a sensor.
This image – VS is 15V not 5V as the image states.
https://hackaday.com/2016/11/08/crossing-wheatstone-bridges/wheatstone_bridge_how_it_works_3/
Thanks! Fixed. It looks like that drawing started life as one intended, but never used, for illustrating my breadboard test, which was 5V.
Throwing my 2 cents in here as I’ve been working professionally with strain gages from engineer, to manager, to director of technology. Wheatstone bridges are great when you have very small signals and a good gain and analog setup. In a practical sense though someone called out one of the main weaknesses. The dummy resistors. The tolerance of the resistors isn’t too important, it’s their thermal coefficient. Most of them are hundreds to thousands of ppm. That means a breeze by someone walking by it can have more effect than total deformation you expect to have happen in a load cell. To get around this half bridges help assuming you have a great reference, and full bridges get you most of the way there — for hobbyists pretty much all the way there.
What you want is < 5ppm/degree and ideally less than 0.2ppm/degree in a matched network for the dummy half bridge. If you can't afford the laser trimmed thin film resistors then the next best is wire wound, but still not great. Soldering or screw terminals is a must. Contact resistance changes are a pain
“if we were to connect point A to point C, there would be 0 volts between them” Isn’t that the definition of two points connected together? Even an unbalanced bridge would have 0 volts between them. I think you meant measure between A and C.
Good point. I don’t know why I wrote it that way. Maybe it was during one of many rereads and I had in mind what I do below where I join up B and D to get the diamond shaped bridge. Dunno. Thanks.