Festo has released a video showing the workings of their BionicCobot, a pneumatic robot arm developed for lending a helping hand to humans at a workstation. Since it works intimately with humans, it has to be safe, producing no harmful movements, and reacting when encountering an obstacle such as an arm containing delicate human bone. This it does using pneumatics and rotary vanes.
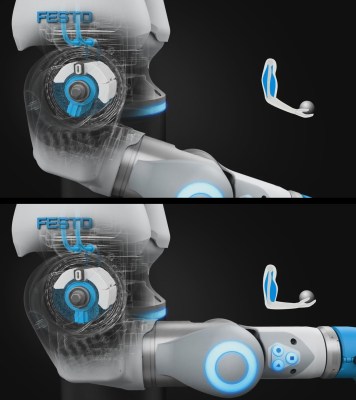
The arm has seven degrees of freedom, three in the shoulder, one in the elbow, another in the lower arm, and two in the wrist. But you won’t find any electric motor or gears. Instead each contains a rotary vane. Compressed air pushes on both sides of the vane. If the air pressure is the same on both sides of the vane then it doesn’t rotate. But with more pressure on one side than the other, the vane rotates. This is much like in a human arm, where two muscles work together to bend the arm, one muscle contracts while the other relaxes. Together they’re referred to as an antagonistic pair. In addition, each joint has a circuit board with two pressure sensors for monitoring the joint.
Using pneumatics, if an obstacle is encountered, the pressure can be released, making it instantly safe. And air being compressible, the joint can behave like a spring, further adding to the safeness. By controlling the pressure, the spring can be made more or less tense.
You can see it in action in the video below the break, along with more details such as how they use ROS, the popular, open system Robot Operating System which we’ve seen here a lot before, along with their Festo valve bank, one of which our own [James Hobson] used for his slick elysium exoskeleton. The video also covers how they handled running the hoses, the kinematics and the UI software.
genius! this would solve .. a lot of issues.
The hardware looks cool but the software GUI is poorly designed. You have to drag the icons repeatedly halfway across the screen which is stupid. I thought we solved this type of problem when we made reconfigurable taskbars in X… like 20 years ago.
I totally agree! IMO – there should be little to no need for a UI at all let alone a complex ‘video like editing tool with icons’.
Robot programming isn’t a high intensity activity, so the amount of dragging is meaningless to the overall productivity of the robot programmer. What is more important is that the programming is deliberate. It looks like the expected skill level for the programmer is similar to that for Lego Mindstorms, somewhere in the 8-12 year old range. The experienced programmers will be making the big bucks on high-speed robotic welders and painters.
Wonder how this compares to other methods of operating a robotic limb?
Nice advert for Festo.
Agreed on the UI. Makes it basically useless except for simple repetitive tasks that are clearly not worth it at this price point.
They need to get together with the people who are making the latest prosthetic limbs. It’s a pretty big leap between this and literally having a third arm but damn the potential of that…
Getting a whack on the face from one of these guys would probablt hurt just as much as if it had motors. I get that it “can” be soft if you reduce the pressure, but for most tasks it would need to be reasonably stiff, and if you happen to be in its path you’ll get a whack.
Anybody that has accidentally been elbowed knows this.
I don’t think it’s the case that it wouldn’t hurt, I think it is more that it’s not going to make you into a fine paste if you get between it and a hard object.
Exactly – it needs to be like being hit by a co-worker, rather than by an automobile.
Maybe it’s more like a co-worker hitting you with a hammer rather than hitting you with the car they are driving :-)
Stiffness relates to being able to shove a worker off their feet or crush them against a fixed obstacle and is not a measure of impact loading.
i dont get the complaints about the GUI, it is the definition of a temporary problem.
that it wont solve some of the safety issue they claim to is a bit harder to fix.
Ancient technology. https://www.youtube.com/results?search_query=vacuum+wiper+motor They also work with low pressure air blown through.
Now there would be a hack, build a robot arm using vacuum wiper motors.
Festo reminds me of Apple.
That’s not a compliment.
Ho odd that this would come from “Microsoft”.
Actually, Festo reminds me of the Microsoft Resarch Labs – lots of awesome inventions that never make it past prototype.
What an awesome design! I’ve been playing around with robot arms, and the real killer is the weight of the motors. The more torque you need, the bigger motor (or gearbox) you need. Or, you move the transmission away from the joint using belts or shafts.
This design has a very small weight at the joint. Although rotary vanes leak (pneumatic and hydraulic), using position feedback would create very usable design (I’m thinking desktop helping hand).
Is there a single shot in there showing the arm actually move on its own? I see some CGI and the end bit ( which might be CGI ) but none of it sitting on a desk and doing something other than being still?
At 7:32 in the video you can see it briefly, but go to the 1st video on their page here https://www.festo.com/group/en/cms/12746.htm for more.