PVC pipe is a valuable material to the backyard hacker. It’s cheap, readily available, and comes in a range of different sizes. However, what do you do if you need to bend it? The typical approach would be to grab a heat gun or blowtorch, warm it up, and go from there. These methods can get messy however, with kinks and melted surfaces spoiling the final result. Now [Linn] has released a video with a method that delivers impressively neat results.
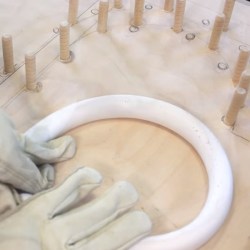
The method is simple, using that classic hacker staple — duct tape. The end of the pipe is taped off, and the pipe filled with sand. With the correct amount measured out, the sand is heated on a cooktop, then poured back into the pipe. After giving the heat some time to soften the plastic, the pipe can then be manipulated into the desired shape.
[Linn] does a great job of explaining the process in a clear and concise manner, and shares tips on how to use a bending jig to guide the final shape. Results are best with smaller pipes that are easier to heat through, but larger sections can be manipulated with patience.
We can’t wait to see what [Linn] builds with this new technique. The possibilities could be further expanded by combining with these PVC fittings designed just for building stuff.
[Thanks to George for the tip!]
The lady’s name is Linn, Darbin is her dog as I recall.
Thanks, James! Fixed.
Just a heads-up, her name is Linn, not Darbin. The channel name was derived from her dog (Darwin) although the derivation was somewhat unclear in her video explaining it lol. https://www.youtube.com/watch?v=SjnBqcfxQqU
That’s a nifty bending trick though!
Similar technique is used for bending metal pipes, filling it with sand prevents it from caving in on itself. Neat idea to heat the sand and apply it to poly pipe!
It’s important that the dried sand carries no moisture as the metal pipe can explode lethally when fired.
Yeah, even the tiniest bit of moisture turns it into a literal pipe bomb. It’s a great trick for forming custom exhaust pipes on the cheap. Pipe bending mandrels and dies can really add up.
That said, I’ve also seen plywood moulds used for bending metal pipe, too. The jig instantly bursts into flame, but if you’re clever and careful it’ll work for one or two uses.
Saw my dad do just that at my uncle’s house more than 20 years ago, when I still was a teen. Nice to see this again!
For PVC and acrylic tube you can get silicon sausage for this exact purpose for most common sizes. Its quicker and cleaner than sand, doesn’t requires correct metering or leave impressions on the inside. Common for running conduit, PC watercooling and perfectly applicable to quick DIY hacking!
Just don’t google “silicon sausage” from your work computer! Not “safe”!
I guess you don’t realise that Google only shows you what it has learned you prefer to see?
As an electrician, we use a long metal spring made to the inside diameter of the pvc conduit to make nice bends.
thank you! i owned one of these springs and used it to bend copper tube and i was super disappointed, and you just told me why: i got the spring that fit around the outside of the pipe, not the inside. duh.
Silicone, with the ‘e’ :)
Also: wow I did not know about that! Safe search term might be “silicone pipe bending insert” which yields stuff like this:
https://www.amazon.com/dp/B00ZXYBVFG/ref=psdc_3015422011_t3_B01786PQ7A
The sand method is awesome all the same since you don’t have to match diameter or length. A+ tip!
Electricians sometimes uses a long and strong spring which has a outer diameter matching the inner diameter of the pipes.
Serves the same purpose as the sand, but faster to use.
My exact same thought… at first… BUT: the spring isn’t heated, the sand it. That’s where the “magic” happens. If the sand is hot enough the pipe should bend easier then with the spring, therefore allowing you to make nicer shapes but also allowing you to correct. I’ll keep this idea in my mind as some day it might come in handy, not for bending pipes for home installation (I’ll still have my trusty spring for that) but for tinkering.
Doing this with sand and PVC piping could have shocking results :)
Concur. It’s also interesting to read the other comments, most of which bear absolutely no relation to the article. What happened to the order of “Read, Comprehend, Comment”?
I like to “unbend” pvc pipe — that is, take large diameter pipes like 4 inch sewer pipe and saw lengthwise along one side. Bake in oven at 250 for 20 minutes, and then unroll it and clamp it flat. It makes nice tough flat sheets about 1/4″ thick.
How flat is flat? I tried this once, by boiling the piece, but the end result was wavy…
Nice tip. But I’m guessing you mean 250°F (120°C) rather than 250°C (480°F)? It’s going to make quite a difference to the inside of your oven, and the patience of your spouse! Please try and use units, for clarity, on this international site!
Do countries outside the US have electricity and ovens?
Or… maybe the us hackers in the US could blaze the trail towards an internationally accepted standard (and uniformly accepted by professional scientists, engineers, and doctors). You know… Just to make it so these screw ups quit happening.
Just a thought.
I blame the pirates
Are you sure you didn’t mean a 4-meter pipe? Because I can’t figure anything out by myself.
I once did a commercial install of a CCTV security system where we had to run all the cables through Schedule 40 PVC. We had a heater box that we used. Essentially a couple of resistive heating elements inside of a box approx. 3ft long with an opening on each end, and a lid to close over the pipe. Lay the pipe inside, close the lid, turn the pipe while it’s heating, once you feel it getting soft, take it out, make your bend, and hold it for a few seconds. The PVC cooled fast enough to set your bend pretty quickly. I imagine something similar could be DIY’ed from an electric space heater.
I wonder if this technique would work for acrylic tubing. I put together a water cooled PC a few years ago with hard acrylic tubing, and I definitely had to discard some of that tubing due to it getting kinked during bending.
I do a 180 degree bend in 3/4 inch sked21 for harmonic flutes I make with a jig of a wood tombstone shaped “sandwich” of 3/4 inch “meat” and “bread” that sticks out 3/4 inch from the “meat”. Heating is done with an open window and the kitchen stove. Back and forth and roll to heat (don’t linger in the middle and leave parts too cool), to softness is good. Then holding the ends which are straight, drop into the top of the jig. and pull the the ends down and press into the straight sides. The “bread” sides keeps kinks from happening. Cool.
For 1 1/4 inch sked21 I use a fat screen door spring my dad had kicking around in the junk drawer I still have. The sked21 in much thinner and more prone to kinks and thinwall deformations. Still the spring can get caught and be sure to unscrew it in the diameter reducing way, don’t just pull it out.
I’ve used this technique before and it works great. Just be careful with the hot sand. It can burn you.
That material is awesome – really reminds me of the strandbeests from Theo Jansen.
I also saw some local guys doing a huge dragon for a Musical play with it. They also took some pictures of the build process [Warning German]:
http://stonehenge-das-musical.de/requisitenbau-drache-teil-1-grundkonstruktion/
Final:
http://stonehenge-das-musical.de/requisitenbau-drache-teil-3-bemalung/
Sand is messy, I have always used this:
https://nl.wikipedia.org/wiki/Buigveer#/media/File:Buigveer2.jpg
Fill it with a mixture of sand and small magnetic ball bearings, and heat it using an ordinary kitchen induction hob Gets you better temperature control and relaxed timing.
We privileged few, who won the lottery of birth against all odds, how dare we whine at our inevitable return to that prior state from which the vast majority have never stirred?
https://hocasino.newone2017.com