[Huaishu Peng] and a group of other researchers have come up with a system that allows them to use virtual reality (VR) to model an object in a space in front of them while a robot simultaneously 3D prints that object in that same space, a truly collaborative effort they call the RoMA: Robotic Modelling Assistant. This is a step toward fixing the problem of designing something and then having to wait for the prototype to be made before knowing how well it fits the design goals.
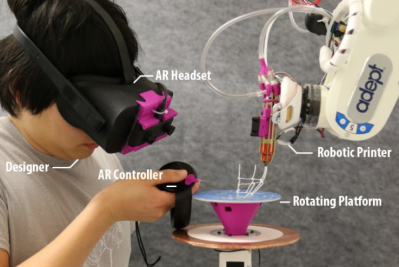
How does the designer/robot collaboration work? The designer wears an Oculus Rift VR headset with a camera mounted to the front, turning it into an AR (Augmented Reality) headset. In front of the designer is a rotating platform on which the object will be 3D printed. And on the other side of the platform is the 3D printing robot. In the AR headset, the designer views the platform, the object, and the robot as seen by the camera but with the model he’s working on overlayed onto the object. An AR hand controller allows him to work on the model. Meanwhile, the robot 3D prints the model. See it in action in the video below.
Some of the advantages of this collaboration are demonstrated in the video below by designing and printing a teapot. When it’s time to model the teapot’s handle, the designer reaches out and positions a finger where it should go through the handle while drawing a virtual handle around his finger. This way there’s less chance of printing a full teapot with a handle only to find the handle’s not quite big enough.
They also show how you can put physical objects on the platform and draw and then 3D print onto the objects. In the video below they add a stand to a toy jet fighter. Or you can draw and 3D print a little, then add physical objects for scale, and then even draw and 3D print around them. They demonstrate this in their paper about this project by creating a structure around some LEGO pieces.
As with any collaboration, they have to lay out some ground rules, what they call domains, controlling who can access the object at different times. For example, the robot can print on its side of the platform while the designer is close the platform on his side but if the designer touches the platform then the robot automatically backs away. If the designer is far from the platform then the robot can do whatever it wants, including rotating the platform.
Sharing a workspace with an industrial grade robot arm can be dangerous. In addition to the domains, the robot arm is programmed to remain in its work area and if the designer strays into the robot’s work area then the hand controller vibrates. The robot’s speed is also limited.
As you’d expect, they also wrote some software, an AR renderer and an AR editor, but we’ll leave that to their paper to describe.
If this looks familiar then that’s probably because they previously wowed us with their On-the-Fly Printing, the first iteration in this ongoing project.
So it’s a 3D pen wielded by a robot, plus AR.
Minus safety.
Super expensive inferior 3d printing plus buzzwords and an inevitable death by crushing. I like how all the attempted safety measures are things programmed into the robot. No redundant or separate system. What about when the robot controller fails? You’re supposed to stay away from those unless they are completely and physically locked out.
this
cool… but (how) does CTRL+Z work?
They use an AR controller with clippers attached (looks like a pair of wire cutters). They simply use it to cut away the parts they don’t want and the software automatically removes the parts from the model. See page 6 of their paper under the heading Physical Modification (http://www.huaishu.me/projects/roma.pdf).
This is some wild stuff, on the surface it looks silly but I think it’s a pretty neat project. I mean yeah, this is a bunch of AR stuff and giant robot arm that function about 5% as well as a ball of modeling clay, but you have to envision the potential.
It might have been easier to skip the AR stuff at first and first try to just refine the robot that quickly prints wireframes. That by itself would be a useful niche 3d printer product.
It’s all about allowing non-computer people to do modelling. Not everyone is adept at using CAD software, they are trying to make designing easier. Is it a good idea? Time will show.
Time will show that the robot arm will eventually have a software crash and kill someone. It’s only a matter of time if all the safety precautions are simply programmed into the arm itself.
Mhhhh don’t look ergonomics at all.
Hi-tech means nothing without ergonomics.
Amazing how they fail to implement the simplest 3D Printing techniques. They should read about retracting. Otherwise, amazing potential.
Nice one! Check out my article on Virtual Models https://unpluggedcreations.com/virtual-supermodels/ ????