Trash is relative. When my coworker accidentally lit an ABS-barbecue inside the company laser cutter, he made trash. The wreckage was headed for the dump, but I managed to save it and pass it on to my friend [Amy]. Four months later, she phoenixed it back to life from the trash-it-was to a glorious new system more powerful than the original. This is her story, carefully told in detail in a three-part series (part one, part two, part three) that takes us on a journey from trash to triumph. She even recorded video of the entire process (also embedded below)
Get your notes out because while [Amy] spares every expense to keep this project cheap, she spares no expense at laying out the details for anyone’s path to success when working with these beasts.
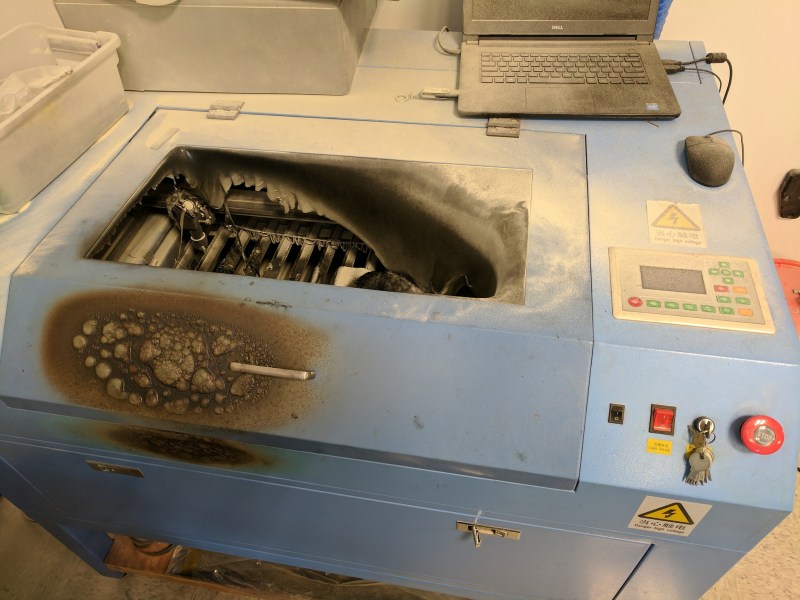
As far as origin stories go, our story starts at my last employer’s office. I was in the machine shop asking one of our MechEs a question when the intern points a finger towards the corner of the room and asks: “hey is that supposed to be on fire?” I turn around to see billowing flames coming from our budget Chinese laser cutter. “Nope!” I say. “We need a fire extinguisher!” But our MechE was already on it. In half a moment he returned with an extinguisher. With one squirt the fire was out, but the machine was caked with a nasty powdery debris. It turns out another coworker had committed the almighty sin of laser cutting: he turned it on and walked away. Better yet, it was cutting ABS with a disconnected air nozzle.
This cutter was headed to the dump, but a few shenanigans later, I managed to divert this heap to [Amy]. The paint job was an absolute disaster on the outside, and the gooey ABS-and-powder mixture had caked over the inside. [Amy] dug in, stripping off the paint flakes and re-coating it. Apart from the belts, she salvaged every other part inside the machine. Her secret: “IPA and steel wool.” From there, she built her own fume extractor and lofted the whole system onto a frame she welded herself so that she could push both extractor and cutter around her wood shop as a unit. These days, it’s seeing some mileage for cutting out jigs for her woodworking projects.
Perhaps what’s truly special about this project is that she restored it with the camera rolling. As if building projects isn’t hard enough, getting the right lighting and camera angles while you’re doing the work is even more work! There’s no drop-down lofted camera setup in her garage, so each documented step is carefully set up so it captures what’s happening onscreen. While the IPA-and-steel wool might’ve been one nifty trick, by the end of these videos you’ll find that there really aren’t any secrets: just one engineer who sees the dignity in a project done well and has the patience to carry it out.
Get to know [Amy] on her blog, and you’ll discover the true finesse of her scavenging and engineering wielded hand-in-hand. From Ukuleles borne of fallen tree branches to a garage woodshop bootstrapped from a series of Craigslist adventures, it’s no surprise that a broken laser cutter would find a new life when it landed in her hands.
“Trash is relative. When my coworker accidentally lit an ABS-barbecue inside the company laser cutter, he made trash.”
Why didn’t the company fix it?
“I turn around to see billowing flames coming from our budget Chinese laser cutter. ”
Oh, never mind.
“Her secret: “IPA and steel wool.” ”
In case you are confused, IPA in this case is isopropyl alcohol, not India Pale Ale. ;-)
India Pale Ale would also be acceptable. Think of the long days and nights of this rebuild.
Perhaps a single malt…
That was my first reaction, IPA to lubricate the arm wielding the steel wool!
might be worth installing at least a smoke or over temp alarm for the future
maybe an automatic fire extinguisher, if i remember right from a work project a few years ago a solenoid embedded rechargeable fire extinguisher is around $75 – $100
We’ve had small fires in our laser cutter at our hackerspace – and it’s almost exactly the same make and model of the one in the article.
Our response was to have extinguishers available, hang a fire blanket within easy reach, and teach people never to leave the cutter while cutting, and to grab the fire blanket.
Seriously – we have student authorization classes where we tell them to imagine having a fire, and imagine themselves reaching for the blanket. This, so that they have an action to fall back on when an emergency happens.
We have two CO2 extinguishers near the machine, one nearby for training (so it’s no big deal if it’s half empty), and one on the machine itself for real fires. Nice thing about clean-agent is you can practice blasting things with it, and there’s no mess to clean up. So every student actually grabs a real extinguisher, pulls the real pin, and blasts real extinguishing agent into the machine. Or at the instructor. Or at other random objects around the space…
It considerably reduces hesitation in the event of a real fire. I don’t know why this sort of practice isn’t more common, the refills are cheap.
Also there should be a spring-loaded extinguisher port in the housing so that you don’t have to open the lid (and risk increasing the fire) to flood the interior with CO2. Kill the power – you DO have a Big Red Button, don’t you – poke the nozzle into the port, squeeze the handle and done.
Because training people to randomly blast a fire extinguisher at people or things isn’t a good idea? It’s not a huge deal with CO2 extinguishers, but the powder or foam ones are rather messy (powder more than foam). On top of that, foam and powder require different technique from CO2. And added to that CO2 is AFAIK one of the least prevalent forms of extinguisher, so training people to use one isn’t all that useful.
A simpler solution is used in rally cars. Extinguisher is used to pressurise a low-melting-point plastic tube. Fire melts tube, releases fire-eating powder.
Remember kids, keep a CO2 fire extinguisher around for your expensive, delicate, and potential flammable machines.
Yep. Dry powder is evil. Better than a total-loss fire, but not by much…
Also remember to never extinguish people using CO2 fire extinguishers.
That rather depends on the alternatives available and how much they’re on fire.
That seems difficult and hard to clean up. Better to just hit them with it until they leave on their own.
*never extinguish “a fire on” people using CO2 fire extinguishers.
A CO2 extinguisher would actually do a decent job at extinguishing people.
Yup, I was hit by one as a joke and still have the scar on my chin from the fall to prove it!
Hell, if your goal is to extinguish people then just leaving them on fire is pretty effective ;-p
And when the landlord insists on getting a guy in to check the fire extinguishers, make sure they don’t try to silently walk off with the only extinguisher in the laser cutter room, and then when we notice and complain, try to replace it with a powder one.
We had words.
hey people, I have had this idea of rigging some kind of smoke alarm and CO2 gas dispenser for my 3D printer, I couldn’t find anyone doing it before me. I can’t be the first one to think about it, has anyone looked into it?
Cutting makes smoke, so, no. Perhaps some kind of IR limit In. Fires tend to make their own CO2, so perhaps just turning the cutter and it’s associated fans off may be enough to put the fire out. Or at least put it to smolder while a siren calls for help.
Put a deadman’s switch to lazer cutters…?
An alarm can sound if you break contact, allowing 2 seconds to be away from the machine… 5 is too much. Bring your IPA. Plan ahead. Once you start cutting, you are there for the duration. 2 seconds lets a coworker fill in for you.
In order to hear her video, I had to turn my volume up to the max. This wasn’t really a problem until I played another video, and got quite a blast of audio.
Cant have an “Accidental” ABS fire as you shouldnt be using ABS in a Laser cutter as it just melts in to goo and sets on fire whilst poisoning you. It’s either on purpose or ignorance I assume the latter…not too great
That said in the last 8 years I’ve had one piece spark up
I can never stress enough that laser cutters are not toys, but are easily capable of burning down buildings if left for their own devices….
Though, at the same time, if one is laser engraving metals, then fire is the least of one’s worries, and keeping eyes at it can be a danger in and off itself. But rather to oneself. Reflections can easily burn through laser “safety” glasses are typically rated to less then a watt or two, so 40+ watts of CO2 laser doesn’t consider them an obstacle per say. Next in the line of sight is in worst case your eye. (Recommended to not have line of sight to metals that one is laser etching. Though most laser cutters have an acrylic window that “stops” most of that laser from reaching your eye.)
But still, don’t leave the laser cutter/engraver unwatched, especially if one is working with wood, plastics or other potentially flammable stuff. A few seconds is all it takes at times. If your project takes hours to laser, then better watch it cut then have that once in a while fire burn down the house.
Yes, fires are actually semi common in laser cutters. Especially when one is just winging it with new materials and other stuff, or just fiddling with settings. If one catches it quickly enough, they are typically easy to put out without any damage to the machine, oneself or the building.
Agreed most of the fires seem to be when trying new materials. We tend to keep records for best cutting settings. Generally faster is better not last as you are generally in a hurry also though it keeps the beam moving and pumps less heat into the piece thus less likelihood of heating it up enough in a given area to cause a fire.
Maybe when having a new user drive one of these it would be best to make them aware of the acquired (hopefully documented )knowledge. Also there are a whole range of materials like ABS and Polycarbonate that never should be used in a laser cutter they always just burn !
“Also important to note: this new tube is almost a foot longer than the original one. So I cut a hole in the side of the enclosure and welded up a box to protrude out and enclose the extra length.” How was this metal (alum, steel) box cut??
Yeah the number of times a Larger Tube replacement as actually been cheaper than the original.. I’ve been tempted to incorporate a “Power Bulge” in to my Cutter on several occasions. Basically you need a box about a foot long and 5-6 inches on side, you may even just re-purpose a standard enclosure and then just rivet it to the side of the cutter, bodgey but functional
Yeah. Sure. Accidently.
This is why we are not allowed to take home things we mark as broken and for disposal, but our co-workers are.
#conflictofinterest
“…when the intern points a finger towards the corner of the room and asks: ‘hey is that supposed to be on fire?'”
When has the answer to that question ever been, “Yes”? (c:
When it’s a bunsen burner.