Regular readers of Hackaday are intimately knowledgeable about old electronics, and whether it’s about that old oscilloscope sitting in the pile of other oscilloscopes, or the very rare vintage computer made in a Soviet bloc country, someone somewhere knows how to fix it. One of the biggest problems with these old electronics are capacitors. If it isn’t the battery that’s gone dead and leaked all over, it’s the caps that are either out of spec or have already exploded.
These machines can be brought back from the dead, and in recent months and years we’ve seen an uptick in the number of restomods hitting the Hackaday tip line. If you have a soldering iron and the patience to do so, any machine can be brought back from the grave.
Your Vintage Machine Is Probably Dead
Writing for ByteCellar, [Blake Patterson] asks an interesting question: what experience do vintage computer enthusiasts have with dried up capacitors?
Nearly every week, it seems, Hackaday gets another tip about a repaired or restomodded piece of hardware. There are always two problems. First, the battery leaked everywhere. That’s almost to be expected at this point, and if you’re very careful and very good, the damage caused by either AA cells or exotic lithium backup batteries can be repaired.
The second main issue faced by vintage computer enthusiasts is leaking caps. This is a subtler failure than a leaking battery. First off, not every capacitor will leak, or go bad. It might be out of spec and bring the whole system down with it, but that doesn’t mean it leaked all over the board. Second, not every capacitor will go bad. Ceramic disc capacitors are just fine, SMD caps can be ignored, and tantalum caps can be hit or miss. Larger electrolytics seem to be sturdier than smaller electrolytics, somehow, and everything is completely dependant on the model of computer and how it was stored. If you found a commodore in a barn with wild temperature swings over the seasons, you might be out of luck. If you’re pulling it from the back of a closet, you might be okay. Inexplicably, new old stock electronics — like the Nintendo Power System that’s still mint in box — are usually okay.
Fun With Capacitor Plague
But capacitor problems can crop up in equipment that isn’t as vintage as a classic Amiga or Tandy. In the mid to late-2000s, capacitor plague was the cause of many failures in consumer electronics. Capacitor plague was a result of defective electrolytic capacitors made between 1999 and 2007, with the first problems showing up sometime around 2002. The symptoms are easy to diagnose: if a device from this era doesn’t work, take a look at the power supply. If you have some goo around the caps, or the tops are cracked open, you’ve got capacitor plague. The implication of this is that consumer electronics, everything from LCD monitors to computers, were discarded in huge numbers. In fact, the coolest hackers we know took advantage of capacitor plague and collected LCD monitors, bought some threaded pipe from Home Depot, replaced the caps, and set up an awesome Matrix-style multi-monitor battle station.
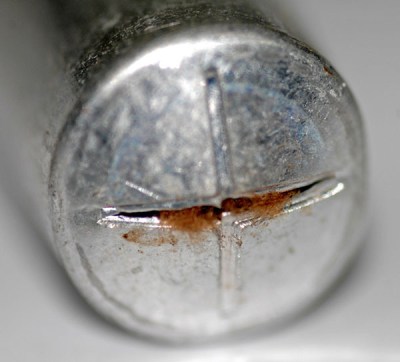
The origins of capacitor plague come from water-based electrolytes developed in the late 90s. Water-based electrolytes are advertised as low-impedance, low-ESR, and high ripple current, all properties that are well suited for power supply design. These water-based caps unfortunately produced aluminum hydroxide when reacting with the cap ‘can’, and reacted to produce hydrogen. This hydrogen built up in the capacitor until the the stamped ‘vent’ on the top of the cap broke.
Although the origins of this type of failure date back to the late 1990s, it was only until the mid-2000s that capacitor plague really set in; these caps will pass initial testing, and it will take hundreds or thousands of hours for these caps to fail. Even in 2012, we were seeing tutorials on replacing bad caps in computer equipment, and for some this became a very fun and somewhat profitable way to equip a computer lab.
How Prevalent Are Bad Capacitors?
There is no community with more expertise in the repair and refurbishment of various bits of our electronic heritage. Here, you have people rebuilding old video game consoles into new portable consoles, turning literal trash into objects that belong in a museum, and repairing vital equipment that has been in use for the last few decades.
What is your experience with broken, dead, and abused capacitors? Did you have fun with a whole lot of monitors around 2006? What have you brought back from the dead, and what, if any, recommendations do you have for hardware designers of today?
Unfortunately, we’ll always have to use caps, and of course manufacturers will always use the cheapest caps available. Dead and dying capacitors will be with us in the future, and it’s up to us to maintain the equipment built decades ago and today.
(Banner image Lincoln Phipps, just one tale of woe among thousands.)
So sad when a colleague got hold of an AppleLisa 1 only to find the capacitors blown on the boards. Still it looked great from the outside.
I am so glad somebody finally addresses this issue and writes an article about this. It seems like so many people(technical or non technical) around us are not aware of this. Well pointed. Indeed the main fixes of the electronic devices nowadays are related to the filtering caps.
https://www.youtube.com/watch?v=HpR1AEZy7b0
I started a new topic on hackaday some time ago addressing the issues that affect the general lifetime of the devices, if anyone is interested in taking a look. I still have a lot of info to add to this page, but anyway:
https://hackaday.io/project/40376-general-longevity-study-on-electronic-designs
Around 2007-2008, I was kept well-employed as a contractor, replacing thousands of motherboards and PSUs for large companies in the area. Companies with the clout to arm-twist Dell into warranty and post-warranty work “as a courtesy,” anyway. We were trained to deny that there was any sort of issue with capacitors in Dell computers. This was a lie. Dell continued to deny there was ever any problem until just in the last few years when they finally fessed up.
“Dell continued to deny there was ever any problem until just in the last few years when they finally fessed up.”
And by ‘fessed up’ you mean “were forced to because of a lawsuit.”
Most techs and young enthusiasts are not aware, but, to satisfy share-holders, many of the larger computer makers declared a loss, such as Dell did, in one quarter of 2008, for $200 Million for repairs under warranty. I have rebuilt computers (1965 – 1985 in the USAF) and, since then, by at least a hundred each year, and install Linux in most of them, FreeBSD, Ghost BSD, in quite a few… New Electrolytic capacitors in the sizes required for most mainboards cost $0.11 to $2.99 each, from Mouser or Digikey. Many of the donated computers go to qualified charities, churches, after hours schools. When attendees at the OrlandoInstallFest.com meetings bring in their computer, the charges are typically cost of parts. Usually, less than $8.00 if it is bad mainboard caps. none of us repair PSUs, and can buy new or used Power Supply Units on ebay for less than $20 each New, often $13.99 to $18 for used…YMMV…
The scuttlebutt is, two-fifths to one-third of all the computer main boards, and peripheral cards, of 1999 through 2008 contained these faulty capacitors. Being able to repair them, gives me an almost unlimited supply of functional computers, and now, I am seeing some 64 bit systems built up to 2012! The supply of capacitors is still a bit contaminated. A whole lot less than in the early days, but, enough to please those of us, who are needful…
I was a tech around this same time I had heard this was a case of corporate espionage where someone stole a capacitor formula but got it wrong leading to a big batch of dell MBs.
https://en.wikipedia.org/wiki/Capacitor_plague#Investigation Dell definitely a high user of the bad boards, along with the single platter Maxtor drives that died in droves, but they weren’t the only ones.
Back around 2008-2009, I worked at a place that had a TON of Samsung 940N (or maybe they were 940B, I can’t remember) monitors that died. A corworker had heard about a batch of bad capacitors, and found instructions on how to repair them. We ordered a bunch of capacitors (I think there was 3 on each power board), and were able to get more than 50% of them back up and running. (We did this during our lunch time, so we didn’t have a ton of time, and the fact that we got any of them up and running again was great).
I am the proud owner now of three Samsung 245B SyncMaster monitors. All three had failed power supplies that were easy to fix by replacing a couple of capacitors. Though the caps were not the only issue. Some components had been ‘glued’ in place with something that over the years hardened and carbonized. Removing the now dark brown glue was the final fix for two of the three monitors.
HAHA, I’m writing this on those exact same monitors. I fixed more than a dozen for work, and asked my boss to get a few for free to keep. The typical fix is documented on Youtube : replacing 3 resistors and a few caps.
Excellent monitors, except, of course, for this point of failure !
I believe that Dell monitors were OEM’d Samsungs at that time. Since they had the same button layout and both said “Genesis Display Technology” when powering on.
I collected a bunch of tossed monitors at work:
http://www.youtube.com/watch?v=X4SdpxxTiJM
After fixing, I took them back and sold them for $20.00 to employees.
I’m just going to have to add capacitor plague to the list of things I learned after it was too late, there were many things that suffered but it was always on the power supply board or circuit and it was always electrolytic caps, but for me this was pre internet and we used a generator a lot, so I lept to the conclusion that it was caused by voltage and frequency fluctuations, yes I know that most of them were or are rated at 500v, but that made the most sense, after much soldering and associated messing around we eventually replaced the incredibly noisy ex military generator with a modern silent chinesium generator, in chinesium “silent” means incredibly noisy, capacitors stopped failing, but according to HaD thats just a coincidence.
We had 4 Dell 1905FPs die but I liked them because they had dual-inputs. So I did some research and found capacitor kits for them. They are now my display. I’ve added Attiny85s inside and turn them on and off and switch sources via I2C.
NIIICE…
There’s a nice side-business there. Premade repair kits.
I thought I remember “capacitor plague” having a bit more interesting of a story. Wasn’t it the result of some company that stole an electrolyte recipee from another. But the company being stolen from was too smart and let them get ahold of an incomplete copy of the recipee resulting in caps that self-destructed much earlier than they should have.
” But the company being stolen from was too smart and let them get ahold of an incomplete copy of the recipee resulting in caps that self-destructed much earlier than they should have.”
That would be seriously awesome, but it’s not quite that interesting. A materials engineer left Rubycon (the initial creator of a commercially successful water-based low-ESR electrolyte) to work for a Chinese competitor, and he duplicated that electrolyte. Some other employees at that competitor stole an incomplete copy of the formula, missing the additives which prevent aluminum hydration (the reason why the problem’s hard in the first place), but they produced it in such quantities and so cheaply that tons of Taiwanese manufacturers snapped them up.
There’s a scientific paper covering the problem with that electrolyte here:
https://www.dfrsolutions.com/hubfs/DfR_Solutions_Website/Resources-Archived/Publications/2002-2004/2004_Electrolyte_Hillman-Helmold.pdf
Interesting,
Thanks for the link!
What made it extra bad was all the component counterfeiters who used the bad electrolyte formula. The knock-off caps got into a lot of stuff, even at Apple. Only buying direct from capacitor manufacturers was a sure guarantee of not getting the iffy ones.
I fixed an old Dell desktop with the fastest Pentium 4 Extreme CPU ever made. Six bad caps right next to the CPU socket. Got $125 out of that free computer from a guy who wanted it to play some old war game that worked best on XP.
Just gave away a socket 939 system that needs 12 caps, I also included the new caps. Threw in an ATI video card that also needs caps, at least they’re through hole.
well. through hole are way more difficult to take off without breaking the motherboard. I found a way to remove smd elcos of pcb’s by turning them while pushing on them, not pulling. that way, the internal conection wires of the cap come out and the pads are unharmed. after that, with a solder iron and flux, ou just remove the remaining connecting wires of the dead cap and you have two pads to solder the new cap on (if you were lucky and the electrolythic goo dod’nt kill the traces on the pcb that is…)
Though I taught Micro-modular Repair, in the US Air Force, in the 1970’s, and am very competent with my Weller 3000, some of my friends still snip the capacitor apart, and solder the replacement to the old leads still on the board. Both of our solutions work fine. I haven’t lost any boards yet, though I desire repeating the original style through board installation.
I suspect the only got part of the formula is urban legend. I really suspect they figured out they could crank out parts that looked the same and worked the same for at least a while which is exactly what the import/clone parts shoot for. I mean these are the brothers of the people putting small signal transistor dies in bigger packages and marketing them at their big brothers. They look good from the outside, and even test OK at low power. IMHO the figured how to make them look the same and cost less to manufacture. They did not care about the longevity of them.
engine control computers on cars are plagued by them. Especially companies that must weather the wrath of cost-cutting venture capitalists. Combine this with many cars remaining operable for 20 or more years and engine controllers often dealing with at least the temperature swings of outdoors… I’ve done at least half a dozen each of Honda, Mitsubisihi, Ford, GM controllers. Fortunately, word has got out that $0.50 of capacitors can save a ECU costing hundreds of dollars to replace so they’re often done as preventive maintenance these days.
A friend’s 92 Accura began to randomly die. Visually inspecting the ECU showed nothing. Resoldering everything didn’t work. I had to go to the parking lot where it broke down, and troubleshoot it when the problem was active. It turned that on of the caps whose mfr was Nichicon had leaked underneath and corroded a trace just enough to make it intermittent. It ran another 15 years until everything wore out
Even good quality capacitors eventually fail. RIP C14
1994 Ford E-250 van started driving up hills like the transmission was slipping episodically: jerk—–jerk-jerk—jerk… After a bunch of failed hypotheses, we discovered a reference to bad capacitors on the engine control module board we pulled it, opened up it up and found just that. Obtained high quality replacements, desoldered the through-hole with braid after removing the conformal/anti-tamper coating, resoldered: success!
Can confirm. I am heavy in the 3000GT Platform and we have leaky caps in our ECU, the Suspension contoller, and the Automatic Climate Control screens.
Replacing leaky caps on those is up on the list of things to check for when you buy one, along with check the oil, and change air filter.
The DSMs of this generation seem to have gotten the worst of the bad 90s caps.
Though I did own a 1994 Honda Accord with a strange starting problem related to an electrolytic capacitor. Granted the car was very old (20 years at the time). Sometimes the car turn over but not fire. The problem was worst in wet weather. But I discovered that if the ignition were left to “ON” (position II) for a few minutes before attempting to start, it would start up. After running the gamut of fuel related electrical checks I finally decided to open up the ECU and poke around. Sure enough I found a leaky cap. I didn’t bother to replace it as I was able to ebay another ECU for $20.
Yep, replaced two caps in my 1994 Suzuki Sidekick ECU.
This is not just a problem with old capacitors. Even brand new surface mount tantalum caps (used for power supply filtering) can fail catastrophically. They can develop low resistance shorts between the power rails, ultimately blowing themselves apart.
Where I worked, we used mil grade Tantalum caps a lot. Sometime back in the mid 90’s, there was a sudden rash of bad ones blowing up. Seems that was due to two causes: [1] cheap replacements (Taiwan?) and [2] parts marked with the wrong polarity. The latter usually blew in-factory. The former, took more time and their performance issues traced to low grade Tantalum electrolyte, which also seems to be the main source of today’s bad Tantalums. Also, even good Tantalum caps are MUCH less resistant to over-voltage conditions than Aluminum electrolytics.
I remember reading an article I think it was on Tom’s hardware, or slashdot about how someone in Taiwan I think, left one manufacturer for another with the chemical “recipe” for the electrolyte solution, but, when they went to another company or something, didn’t get the entire formula correct, but were able to underbid and got a lot of sales that went into computer motherboards and a bunch of other things. I remember my dad’s computer had those and I had to replace about a dozen caps to get his computer back running properly.
U saw a board with a tantalum that glowed red hot. This was a pinned device and the copper traces in the end suspended the glowing capacitor over the hole burned right through the PCB.
I not U
U not me, either…
et tu Brutae?
When I was a kid I had an open frame switcher supply, probably late 80’s. It was sitting on the carpet on when all the sudden I head a sizzling sound a *pop* as a glowing piece of tantalum launches out of the power supply several feet into the air landing on the carpet next to it. Me freaking out as it is slowly burning through the carpet. Good size chunk too, probably 1/4″ in diameter x 1/4″ long.
My personal recent experience with cap failure: If you put 2,800V on a (polypropylene film) cap rated for 600V, it only lasts a few seconds! Then releases a surprising amount of magic smoke an a nasty smell.
Meh. That’s nothing. You should try it with a selenium rectifier! Now that’s fun that’s too good not to share. Take it down town and do it on the sidewalk.
ewwww, seli rects are icky icky icky when they burn up
Is that a failure? It sounds like it performed exactly as it said it would on the tin. :)
I have a small fleet of battery powered portable audio and video gear that’s 90’s and early 00’s. I keep it around so I can rescue audio or video off what is now obsolete media. I’m finding that every couple of years I lose another low voltage electrolytic or tantalum cap. These are really tiny caps with working voltage of 6V or less, and usually are run near the working voltage. I don’t like these low working voltages. Many times it’s difficult to find a replacement part of an equally tiny size. Instead I’ve been using SMT ceramics in stacks to get close to the correct value and fit in the allocated space.
Different capacitor problem: old (<1960s) valve radios often have wax and paper capacitors. The wax goes soft, a bit of the paper insulator is exposed to the environment, paper starts absorbing moisture…
Much more recent equipment can be found with the dreaded “Rifa” AC line filter caps. These are typically metallized paper in a plastic shell. The shell tends to craze over time and lets in moisture much like the ones you describe. They make a horrible mess when they go off.
Back in the early 80’s I was working on video terminals with linear power supplies that had 10,000 uf filter caps the size of a Red Bull can. One of those blew in the field and when I pulled the lid off the case there was paper fluff and aluminum glitter _everywhere_. The cap’s shell was aluminum except for the plastic “base” with the screw terminals, which of course was pointing up rather than down. Essentially it was a confetti cannon.
Shango066, is it you?
Not just radios, ask anyone who is restoring old TV sets or test gear or the like how bad capacitors (including those bumblebee caps that look like resistors with color bands, the wax caps, the paper caps etc) can ruin your day (e.g. blowing an expensive valve/tube) or be a pain to replace.
Had a capacitor fail in the ECU for a 1995 Honda Civic when I went to start the car. This was a large electrolytic that failed, shorted to ground, and sent several square cm of the PCB up in smoke.
C14. known failure point. If you’re lucky it doesn’t take out the PCB…
Back in the day, before the capacitor plaque, cheap TV repair shops used to have a trick of boiling electrolytic capacitors in water to revive them when a suitable replacement couldn’t be sourced easily. That would revive the capacitor for long enough that the customer would get their TV working again, and ensure that they would return after a year or two.
We use to keep a huge can cap with leads to check tv’s usually in the hot days of summer when they would fail and they would do the “twilight zone” wiggles on the screen. I’ll never forget the POP every time you attached one. Just always had to remember to ground it out when you were done… ;)
Why make aluminum can to make capacitors? Does someone make better design instead of aluminum?
Why not high quality ceramic/SS metal can capacitors? Modern technology should last decades without failures. I understand why they make cheap capacitors. Whoever, makes this invention. Just a thought and why people throw away in dumpster make these worst and hurt environmental.
Deafguy
Electrolytic (aluminum can) capacitors put more electric energy storage in a small space than any other non-chemical technology available before the invention of supercapacitors. They are also an economically rational choice.
They aren’t necessarily failure points. I’m still using a 40 year old Lafayette AM/FM receiver; no failures of any sort.
Well then I’ll need to replace bad caps. So which brand name should I trusted before buying it?
Deafguy
Panasonic, Rubycon, Nichicon, Nippon ChemiCon, Sanyo, Wurth, Vishay
Die-stamping aluminum is about the cheapest part-per-dollar metal-working process out there even for deep-drawn parts such as cans. Aluminum is relatively soft and easy to draw. (Every beer can is made this way.)
Deep-drawing stainless steel is significantly more difficult than aluminum though. Stainless steel creates more friction in the drawing process thus needing higher pressures and constant lubrication. Temperatures need to be controlled to prevent work-hardening and resulting fractures. Dies and molds suffer more wear from the harder material.
Thus, equipment capital costs are higher, Job tooling costs are higher, and operating costs are higher too. Then the part needs to be washed of the lubricant, so process costs are higher. Fewer people have expertise in deep-drawing stainless steel, so design engineering and manufacturing operator costs are higher too.
Consider that a 100uF 12V capacitor is about 5c at Digikey. For arguments sake, let’s guess that the can costs about 1c of that. (Leads, heatshrink sleeve, foil/dialectric roll, seal, electrolyte comprising the other components.)
The only reason it can be made for a penny is because of the vast numbers made. Die-stamping has high job startup costs but extremely low relative operational costs. Designing and debugging the die and mold set can be extremely expensive – a set of close-tolerance registered components machined from hardened materials. A $10k die and mold set would need to stamp a million 1c cans just to pay for itself – assuming that other operating costs are zero.
It’s easy to see why it’s a difficult investment choice to make stainless steel cans. That same die set on a run of 100k now costs over 10c a can, and the cost of the capacitor has tripled.
If you have a PSU design with 10 such capacitors, that original 50c supply cost is now $1.50. After retail markup, that extra dollar supply cost is now $3, or 6% of a $50 PSU. Better thermal design is a much more cost effective path to reliability.
I use to work at Apple back in the mid 2000’s. We would get iMac G5’s, Monitors, and G5 towers in for warranty all the time because of blown capacitors. It sometimes wouldn’t even take 6 months for the failure to occur. The procedure was just to swap the bad board with another board with the same bad caps on it just to get the customer another 6 months or a year until the warranty expired and they had to buy a new machine. We obviously knew what the issue was but according to Apple at the time, “there was no known issue.” Apple still hasn’t changed.
Apple didn’t want to admit they bought components at the lowest prices they could find, just like all the PC builders. That would mean admitting they fell for a lot of too good to be true deals on lots of counterfeit capacitors with that bad electrolyte formula.
Look up Louis Rossmann’s repair videos on YouTube. He details the many electrical design flaws of various Apple products, and how he repairs and makes them better – when it’s possible to un-screw Apple’s screwed up designs. One of the worst is a laptop display connection Apple did correctly, then in subsequent models changed to be flat out wrong. The older model had ground pins between the backlight HV and the data pins. The newer model changed that to put the HV pin right next to data.
Get some dust and crud in there along with a moist environment and *kapow*. Shock to the GPU. Repair the display connection (if possible), add some insulating coating, replace the GPU chip. If it’s a model without the discreet GPU you toss the mainboard in the bin because it’s blown the CPU.
Apple should probably learn something from Louis Rossmann. Design their products better, less will fail, less repair work for external companies and so what if people keep their devices longer.
I don’t have the urge to replace my devices every year, a phone does at least 3 years (unless it fails first – I’m looking at you Google!). Let’s just hope my Pixel 3 does longer.
I have a couple of pieces of equipment on my shelves that need fixing, I’m still hoping to find time to do the repairs, a EMS 30-65 which seems to have blown all the power transistors for some reason (my suspicion is bad caps), a HP 6813A which initially seems to work fine, untill you try to ajust the frequency, and some other settings just won’t change anymore, again I suspect bad caps. A Wavetek 2MHz variable phase synthesizer that requires a new Eprom battery, I have not looked inside it yet, as I dread the mess i could find if the battery has been leaking, it keeps complaining that it can’t operate at 0V, leave it on for a couple of hours and it works just fine…
And I hate to see my good working Lecroy 9420 develop capacitor rot, as I don’t fancy replacing all the caps in that one.
Thanks for mentioning the LeCroy, I have a 7400 that isn’t working. I didn’t even think of checking the caps!
(I haven’t opened it yet).
Oops! its a 9400 series too!
I especially love Tantalum capacitors. They don’t leak but they do short often causing Cascade failures of an explosive nature .
When I’m working on anything 15 years or older I use the continuity setting of my meter to check them.
Which meter tester you used mostly?
Meade telescopes had the problem of using tantalums with their rated voltage way too close to their operating voltage and they could pop. What made things worse was that they had one of these in the hand control and the flex cable from the keypad lays against it. If that cap pops it burns a hole through the flex and the controller is junk. No one has been able to make a lasting fix for these keypads.
The defective capacitors were branded as Nichicon, but were most likely counterfeit. The scores on the top of the defective capacitors were in an “X” pattern (as in the above photo). The real Nichicon capacitors had a “K” pattern on top. I saw a lot of bulging capacitors of the first type in Apple equipment from the day, but never had one with the “K” pattern fail.
In 1978, I was in my first year of a trade college electronics class. We were doing a breakdown on a huge am radio receiver, (tubes…yeah, THAT long ago) that you could adjust the plate, grid voltages and all sorts of things. Someone bumped one of the voltages…suppose to be around 12 volts…it was up to 75 volts. We had ONE female in our class. She read one of the test points and said “wow, this is only suppose to be 12 volts, but it reads 75 volts”…about 10 seconds later….POW! One of the cans let go and sprayed her and her lab partner with the confetti inside the cap. She never admitted to soiling her pants, but the rest of us had a good laugh!
As to the bad caps in the 90’s early 2000’s…I replaced a lot of those on computer boards & early model LCD monitors that went belly up.
In the mid 1980’s I was still in the habit of prowling the neighborhood for tossed electronics. Came upon a real find — a 25 inch (for that day huge) console TV in a beautiful wood cabinet. Probably cost over $1,000 in the 1970’s. I dragged it home, and quickly realized the PS caps were not capping and all the voltages were 60 Hz modulated.
In those days you couldn’t just go to DigiKey or Radio Shack for a 450 volt cap. Fortunately I’d been prowling, right, and had a box of similar caps. I wired one up; it didn’t fit physically but I mounted it in an odd corner and ran wires down to where the original had been. Fired the TV up and it had a bee-yoo-tee-ful picture.
For about 30 seconds. Then it started to roll again, and then BAM the replacement cap exploded, putting a hole in the beautiful wood cabinet. Oops.
When Electrolytics fail this fast after mounting it is almost always because the’re mounted with reverse polarity.
I wonder if the case of the replacement needed to be grounded to the chassis…
Fortunately my NextStation didn’t seem to have any leaky caps when I last checked it. Haven’t checked my NeXT Cube but it booted a year or so ago.
I’ve just replaced a cap in the power supply of a small water pump. It’s a hot water circulator, 12VDC, with a magnetically-driven impeller, which sits on a small ceramic bead acting as the bearing. There’s no shaft or seal to wear out and leak.
But the cap on the power supply failed (after ~5 years of pumping 80-90 degree water). It didn’t leak or explode, but the pump wouldn’t start. It would run if I spun the impeller manually. I suppose the constant heat caused the cap to dry out.
1000 uF, 63V, rated to 105C. The failed unit is branded “SAMWHA”, the replacement is “Suntan”.
Toilet macerator (one of those gross things that chews up toilet paper and unmentionables and shoves it down a small bore pipe) went south after 8 years. Fixed by replacing its motor capacitor – both brands were Ducati energia.
That’s a very common failure in single phase AC motors. I have fixed several air conditioners by replacing the capacitor on the fan motor of the outdoor (condenser) unit.
Keep a spare cap around since it’s a known failure point.
Because of the high number of devices I’ve repaired because of failed capacitors, it’s now the first thing I look for on a board.
It’s also the reason I bought a Peak atlas ESR meter and it’s truly the most useful tool in my box (after the multi-meter of course). (That’s entirely my opinion for the type of things I repair).
I remember in the early 00s, I worked for a small computer company and we mainly used ABit motherboards. They had been ultra reliable for the years prior but then we started seeing huge numbers of board dying from exploded caps. Unfortunately I wasn’t as knowledgeable about electronics back then so we just replaced the boards.
more than 13 years ago back in school we built power supplies – my classmate and I took really big ass electrolytic caps from old TVs from the junk yard.. mine worked well..
his. lets just say a different story.. the bridge in his supply got reversed..
the big ass 1.25 inch diameter cap started hissing………. and very similar to how a rocket starts white smoke started leaking from the sides.. then it twisted and launched the metal cap up to the ceiling..
I can still remember the slow event… after that there were a lot of paper like fibre all around
Join the Church of Electrolytic Reformation where old NOS capacitors get a second chance.
(also has a capacitor’s schematic symbol as a cross)
Yeah, 30-50 year old NOS caps are hit’n’miss as well. Some work fine, some don’t, others have to be reformed (they’ll blow up if you try to use them right away).
If Tantalums don’t short, they can fail with weird intermittent internal resistance. I usually use a Testofon for everything. It’s basically a beeper whose frequency is determined by the current flowing. A resistor results in a lower beep than a short. A capacitor has a typical charging curve on which you can read its capacity and its leakage current (if it’s audible, bin it). Tantalums with this failure mode produce a wild whining that sounds like tone-deaf people singing their favorite song.
I think I’ve heard somebody reference this type of continuity testing circuit. It seems like it may be quite useful. I wonder if there’s some glaring reason other than cost that manufacturers don’t put it in their multimeters?
I had never heard of a Testofon, so I DAGS,
https://www.heise.de/select/make/2017/1/1488454739087212
https://www.hahn-kolb.de/Main-Catalogue/Test-buzzer-TESTOFON/1521CL04_09070501.cyid/1521.cgid/en/US/EUR/
88 Euros
Most often it is just electrolytic capacitors failing. An interesting observation did I make when we had two different batches of Asus Mainboards of exactly the same model at our company. You could predict their failure 100% by the color of the capacitors’ shrink sleeve.
I did see a ton of various power supplies, professional and consumer devices likewise, die of electrolytic capacitor disease. I saved many many of these before the dumpster.
However, i did not see a lot of equipment fail of any other kind of capacitors, be it tantalium or film or ceramic.
My takeaway for electronics design is: If you can replace an electrolytic cap in your circuit that is meant to be somewhat durable and reliable, replace it with a different kind of capacitor. If you can’t, choose the best available part. Another option for electrolytic rail capacitors is choosing a higher voltage, temperature, capacity in order to prevent premature capacitors disease.
I have been gathering monitors and lcd tvs for years my friends or family will phone me with it wont go out of standby…. ahhh ok a few new caps later and i stash them in my box wardrobe (its full of the bloody things)
I remember working at a decomm and repair centre for Fujitsu-Siemens out at magna park in Lutterworth in about 2006, I was 18/19 and it was very pre me learning about the cap plague.
They had tonnes (literally) of PCs from major banks that we had to open and check for “K-caps” which were popped or likely to pop caps in old dell optiplex series desktops iirc GX240’s, 60’s and 80’s they were sent off for warranty repair.
X-cap boards were o.k. and were sent straight for reimaging from os2 to xp at the time.
Later the K-capped computers would return with X caps and then be reimaged.
Now I know why and we did at least 3 or 4 of the major banks computers in the UK as well as decommissioning work for other clients too who had upgraded and wanted rid of the old stuff. so many hard drives killed with by a hydraulic press with a steel spike on it.
its either that or X-caps were the problem and K-caps were o.k one or the other
Seeing the Images above and the other posts here, i think K-Caps were okay.
According to other comments above, the K caps were good, and the X ones were counterfeit or knockoffs.
I used to run a small computer service for a couple of years. About 40 % of the defects were related to capacitor failure . Most of them were fixed by just replacing the caps. At some point along the years people started bringing other electronics (tv, amplifiers, kitchen appliances….) and pretty much anything that had a switch mode psu or pwm voltage regulator had a blown cap and caps related damage. After all of this the most damage i saw was in a 7.1 channel amplifier : The case of the capacitor blew all off in the case and shorted pins from one of the final stages transistors, sent power straight to the speaker (around 70+ volts) , welded the protection relay closed and blew all the fuses in the amplifier (some idiot replaced the fuses with a lot higher amperage) .
Recycled a 12 tonne electrolytic capacitor bank from an old fusion experiment. It had been sitting for years and the capacitors were very leaky (charge wise not goo). So I had to spend 3 very long weekends wearing ear defenders slowly winding the voltage up. Every day a bit mor ground was made and the leakage current would go down. Fortunately the capacitors were all individually fused and only 60 or so went pop.
The power supply used was the rectified output of a MOT, controlled with a Variac. It was a case of needing a power supply urgently and not having budget or time to get a proper one – so hacking apart a brand new microwave worked. Much fun.
The dielectric layer in the electrolytic capacitors can degrade with time. Especially if warm and or left off. Leaving a voltage on them usually keeps them happy. Fortunately, by slowly increasing the the applied voltage, they can be healed – as long as the current density through any reforming regions stays low. At home I do this by removing capacitors from PCBs or turrets, then after giving a check on a bridge, clip a test lead with built in (or bodged on) 10M ohm resistor and slowly (over an hour or so) increase the voltage to maximum rating – and if feeling brave, about 10% higher.
This almost always works but can’t fix a popped capacitor. Totall faff, but worth it on occasion. And by measuring the leakage current and watching it slowly decrease, I can convince myself that it’s doing something useful.
During the plague I sometimes replaced 105 degree low esr caps with cheap 85 degree caps. Because the formula was different, the cheaper ones performed better. In face the screen I am now using still runs on a 85 degree caps a decade later.
Motorola Spectra commercial radios. Spectacular units except for the VFD displays and the full array of leaking caps. That’s where i learned surface mount component replacement…
It is useful to note that the life expectancy of electrolytic caps is very temperature dependent. Caps can be rated for as little as 1000 hours at 85c. For something always on, that is only a few months. The good news is that life expectancy rises dramatically as the temperature goes down, doubling for every 10c drop. That 1000 hours could become 64000 hours at 25c or around 8 years if always on. One problem is that the electrolytic in PSUs and on motherboards are often close to heat generating components and can become very hot, thus substantially reducing their life span. I had a powered subwoofer which was always on and the PSU caps just wore out after a few years. Apart from replacing the caps with ones rated at 10,000 hours at 105c, the main solution was to turn off power to the subwoofer when not in use, rather than relying on standby. I try not to leave power adapters plugged in when not in use for that reason. I also always try to use caps rated at 5000 hours or more at 105c assuming there is space. 105c caps are usually a little larger than the equivalent 85c caps. So, keep your caps cool and unpowered whenever possible!
Many people obviously never read what Horowitz & Hill had to say about capacitors in the Art of Electronics, specifically in the table comparing various types on pg. 19. (*) For every other type; Accuracy, Temperature Stability, and Leakage are evaluated within the range of poor, good or excellent.
They rated those respective characteristics for electrolytic capacitors as “Terrible, Ghastly, Awful”.
The challenge is (and has always been) that large capacitance is almost impossible to find in affordable technologies with better characteristics. Supercaps are even worse in several ways and more costly – but they compete against batteries not against capacitors.
This is a problem that hits power supply circuits more than others. Savvy engineers avoid using them where-ever possible, but that is nigh impossible in power supply circuitry where you need the capacitance to reduce voltage fluctuations. Even there, the impact of poor quality capacitors has been reduced by the increased use of switched-mode technologies, but not eliminated. The reduced power consumption of electronic circuitry and the increased efficiency of power supplies have led to better PSU temperatures, and that has increased reliability too. The well-initiated are also aware that the lifetime of a capacitor can be reduced by charging it close to its specified voltage limits, and that even before total failure, the capacitance can drop 20% over a couple of decades – and that’s on top of the terrible accuracy. (IIRC I’ve seen the figure -20% to +10% quoted.) Essentially, a low efficiency poorly cooled 24V PSU using a 25V capacitor with a capacitance specified to just attain the desired ripple voltage is much more likely to fail than a high efficiency cool design using a 35V capacitor with a higher capacitance.
If any young physics scientist or electronic engineer wants to be rich, crack this problem. Make a better high capacity capacitor. The person that patents a design that competes with electrolytic capacitors for capacitance and cost, but polycarbonate capacitors for accuracy, stability, and leakage (“Good, Good, Good”), will make a killing.
(*) pg. 22 in the 2nd Edition, notably missing from the 3rd.
Ah, capacitor stories.
Yes I got to blow a big electrolytic up in a custom power supply after I installed it backwards. Suddenly it’s a 4th of July parade … I restored a lab bench supply by replacing the blowed-up cap that was across the output terminals.
Most recently, when I fired up my late uncle’s Revox A77, an ancient plastic or paper cap exploded (they were used as voltage dividers in the AC reel motor circuit). Replaced all 3 of that type with polyester caps… reel motors running perfectly.
Cap failure or drift is a common problem in old audio gear. Also, since all components in audio have magickal properties, it’s common for older audio gear to be re-capped just because. ;-)
I once had an audio amplifier module that blew a capacitor (something small, like 1 or 1,5cm long and 7mm diameter) in the first 15 min after first power up. It turned out, the manufacturer had installed the cap backwards.
Wear any eye protection?
SOYO PC motherboards, also other low-end brands, 2002-2004. Not sure what the deal was, perhaps also a regime/design issues. I might be biased, but I have the feeling that back then it was may more prevalent. I replaced caps on at least a dozen of these. Recapping a motherboard was normally not an option for a typical PC repair shop until they realized this was happening way too often.
Ivan Stepaniuk said, “SOYO PC motherboards, also other low-end brands, 2002-2004. Not sure what the deal was, perhaps also a regime/design issues.”
I currently own 8+ Soyo Boards and can tell you why SOYO Boardscontinue to have problems andwhy this Taiwan company went out of business… Soyo mistakenly used low-quality Sarcom and Wendell capacitors that were manufactured by the OEM with deceptive specs. The problem was that Sarcom Electrolytic Caps:
1.) used water during manufacturing,
2.) Helium would build up inside the cap during normal use,
3.) overuse outside of specs caused excessive heat & Helium gas buildup inside the cap with possible premature failure, and
4.) the cap’s aluminum top would eventually expand, leak, and/or fail . Sarcom Cap tops could explode on brand new motherboards or over an extended time of normal use.
As far as I am aware, most SOYO motherboards used defective Sarcom Capacitors. The results were devasting for Soyo because they were flooded with customer warranty repair claims, SOYO failed to replace *all* defective Sarcom caps (they only replaced individual caps that tested bad within the warranty period), and finally they simply delayed or ignored customer complaints about their defective parts.
International Lawsuits were filed and judicial court judgements decided against Sarcom Capacitors, Soyo, and many other small Motherboard manufacturers. These small Asian companies were held liable for product repair/replacement of the defective Sarcom Caps. SOYO, like many other small OEM Motherboard manufacturers in Asia and elsewhere, could not financially support a massive recall of SOYO motherboards, so SOYO management staff filed for bankruptcy and dissolved the company. I seem to recall there were no bankruptcy bidders interested in buying and restarting the Soyo company, which is why the SOYO seemed to disappear when its company assets were broken up and sold off…
Over time, I replaced all of my SOYO motherboards Sarcom capacitors with correct cap replacements from Nichion and other reputable capacitor OEMs.
I have 2 BBC Model B’s and a BBC Master. All three turned on after long storage. In all three, capacitors blee violently (noise, lots of smoke) after 30-60 seconds. All three continued to work with blown caps. Of course, I did put in new ones to stabilize the power supplies.
Our hackerspace recently got a Roland PNC-1000 plotter, very old piece of tech, but still capable of cutting stickers out etc. First day we got it, I was making it work and at some point, one of the two stepper motors just started glitching wildly. We spent 2-3 hours debugging that problem, decided it could be a stepper motor’s fault (swapping two motors’ connectors would make the problem disappear). Got it disassembled fully enough to reach the stepper control board – were about to assemble it back, but then I decided to replace capacitors near the stepper driver ICs (4pcs 50V 100uF). After assembling the plotter, the problem magically solved itself. Can’t be 100% sure it was the capacitors’ fault, but it sure seems like it – apart from disassemble-assemble, that’s the only real change we did.
Back around 2007 to 2010, we had a bunch of Planar PL1910m monitors ordered at work (roughly 1000 or so) and pretty much every single one died during the warranty period due to bad capacitors. The replacements weren’t any better so they would also get replaced during the three year warranty window. Eventually, they finally made it past the 3 year warranty window and I started repairing them by replacing the capacitors in the power supplies. I think I repaired about 80 of them before the cheap screens started failing on the monitors by getting vertical lines in the screens. At that point it was no longer economical to replace capacitors on the power supply boards if the screens themselves were bad, which you often didn’t know until after you went through the work to fix the power supply board. Those monitors were cheap garbage. We switched to HP monitors and had hardly any problems since.
Back when I used to repair welding equipment for a living I had a Hypertherm plasma cutter come in dead. These were an inverter (SMPS) design so the first thing that happens is the line voltage is rectified and filtered through two big electrolytics. There is also some some autoranging circuitry that reconfigured the imput based on the input voltage. It is set up to do voltage doubling on 240 and straight through on 480v. With RMS at over 500v they used the two 400v caps in series with balancing resistors so you would normally see less than 300v across each capacitor. Well, one of these balance resistors opened up, one cap went to 0v the other 600v.
When I opened the machine I found the can of one of the cap had blown its seal and slid down halfway the jellyroll inside. These were probably 3″ in diameter and 5″ long, pretty impressive as was the smell. I still keep that cap as a souvenir.
I had a Gigabyte Mainboard in my PC circa 2003. I went on vacation for a month. After returning, the PC was dead. I opened the case and saw 7 or so big caps with their vents split wide open. All were of the same type and rating. The computer was behaving completely normally before. I tried to solder in replacement caps, but I apparently did a bad job (or there was further damage). The thing never booted again. Of course the warranty period had expired 2 months earlier. I never bought Gigabyte again.
Almost got hit in the face by an exploding tantalum capacitor. Pulled an old Hyundai 286 desktop out of a pile, plugged it in, turned it on, and one of the caps let go with a fair amount of force. There was a secondary “smack” sound from the projectile striking the ceiling. There was almost nothing left of the capacitor itself, just the leads and some residual material stuck to them; I never found the bulk of the remains (in part due to the messy environment). IIRC at least one other capacitor had incinerated at the same time, though was a charred lumpy mess and still attached to the board. Previously, i had a general desire to witness where any magic smoke might come from; since then, however, I’ve done all initial power-ups of ancient machines with their covers installed, or at least standing back a bit.
Back in about 2004 or so we had an old Ipex CRT computer monitor that was second hand from a school, it worked well for a couple of years until it started getting intermittent orange ghosting on the screen that would make a different sound from the circuitry. Is this a sign of bad caps? This was often went away if you hit the side of the monitor with you hand. This screen was used for a year or so with this intermittent problem but didn’t worry my family enough to replace it until one day when we heard a few pops come from the study where the computer was idling while the screen had gone into standby. When we went into the room we were struck with the sight of 1 foot flames coming up from back base of the screen as the casing had caught fire. This was put out quickly by my father pouring the kettle onto it and grabbing it and taking it outside. I think the pop sounds were caps failing and when I pulled it apart one of the boards was all burnt and had burnt through the plastic but I didn’t know enough about electronics back then to know if it was part of the PSU.
It was just lucky that we were home and nearby to hear the pop sounds or else the house might have gone up. Later on I had a cheap atx psu die when switched on with a pop, exploded cap and smoke.
I also used to own a Toyota Soarer/ Lexus sc400 that had the digital dash which was notorious for going bad from leaking caps and that car was top of the range S class competitor from Toyota made in 1990.
Around 2003 the site I worked at started having weird problems with the about 200 IBM NetVista desktops we had installed a year or so prior. They would start misbehaving – intermittent random blue screens, memory errors, lockups, boot failures and the like. Fortunately we had a maintenance agreement, and at first it was just the odd few here and there, but pretty soon we were sending batches of 10 off at a time for repair. After about 6 months, it was a regular occurrence, and we had a crisis meeting with our IBM rep.
I then had the joy of orchestrating the team of 6 IBM technicians (sent down from the factory in Scotland to our site in North Wales) to do a site-wide replacement of motherboards. Our site was a relatively large industrial installation about half a mile by three quarters of a mile in size, with umpteen buildings and outposts spread round. They were only on site for a week, and we had taken the option of taking the techies to the machines rather than the other way round, and I can tell you, it was a struggle to schedule hitting the 40-a-day target, mainly because nobody ever reads emails from IT, so didn’t have a clue we were coming to do their workstation that day… grumpy faces all round.
It was a bit of a blur, but at the end of it, I could power down, unbox, swap the motherboard, re-assemble and boot up again in about 10 minutes. Glad they were all the same design box. Oh and they left us a stack of replacement mobo’s “just in case”. You can guess the rest… let’s just say the IT department wasn’t wanting for project motherboards for quite some time ;-)
” I can tell you, it was a struggle to schedule hitting the 40-a-day target, mainly because nobody ever reads emails from IT,”
How could they? Their PC’s were down!
B^)
I’m guessing the site (like one I had worked at in 1999-2000) replaced most of their PC’s during the Y2K scare.
No, that’s the whole point – they weren’t down, but it was a state of impending doom. Surprisingly, we had been buying Dells and Compaqs (remember them?) before that, and had changed to IBM in about 2001/2002 when we rolled out XP.
Capacitor failures are not only limited to poor selection e.g. too low voltage, etc. Electrolytic capacitors are short life capacitors simply because of the technology. LED and CFL lamps have a long life that is well beyond the life of the capacitors that are used for the power supply. Because of the LED Lamp market size capacitor engineering efforts are being made to improve them so the full LED life may be realized. Just like a chain the weakest link will fail first and for LED lamps it is the electrolytic capacitor by far.
All the TV’s I have were dumped on the side of the road with nothing more than a couple of popped caps in the power supply where I know the ripple currents through those caps was substantial. So I pulled the dead caps, put in some highly spec’d Rubycon or United Chemicon parts and voila!
I put it down to planned obsolescence because the TV’s were all of a certain age. But among those sets were better brands rather than “value” brands or the cheap and cheerful type. Having read through this article I now have a new theory, thanks!
Problem is I was designing a lot of power electronics in those years so I wonder how much of my own work has had a bad wrap because of this. Hmmmmm.
I might have a batch of 50 failed meanwell power supplies to add to the discussion ^^ worst ebay score ever, but maybe someone is interested in a systematic analysis…
As others have mentioned all SMT electrolytic caps in Macs and PowerBooks from the 68k era (early 1990s and on) are leaking. All low-voltage side caps in Mac LC, Osbourbe PSUs I’ve had be dry or otherwise leaked. The X caps in clear yellow epoxy also go up in smoke on Macs and Osbornes I’ve repaired. Some Macs have dipped disc type which are fine
All “compact” thru-hole electrolytics are leaking, basically SMT type with leads, smaller than the typical t-h electrolytic of the same ratings would be. I don’t see this type available anymore so I creatively stuff standard ones in place. From my personal encounters this includes the Epson HX20/PX4,8 computers and their accessories, TRS80-100 series, Apple Newton 100, Amstrad NC-100 among others
Only encountered a few tantalum shorts, from the 80s (orange tear drops)
I fixed a Samsung 204B and a strobing Vizio 37″ LED TV by replacing two caps in the power supply and daughterboard respectively. I believe they used the same value, too. That was a nice $5 fix for both.
Ivan Stepaniuk said, “SOYO PC motherboards, also other low-end brands, 2002-2004. Not sure what the deal was, perhaps also a regime/design issues.”
I currently own 8+ Soyo Boards and can tell you why SOYO Boardscontinue to have problems andwhy this Taiwan company went out of business… Soyo mistakenly used low-quality Sarcom and Wendell capacitors that were manufactured by the OEM with deceptive specs. The problem was that Sarcom Electrolytic Caps:
1.) used water during manufacturing,
2.) Helium would build up inside the cap during normal use,
3.) overuse outside of specs caused excessive heat & Helium gas buildup inside the cap with possible premature failure, and
4.) the cap’s aluminum top would eventually expand, leak, and/or fail . Sarcom Cap tops could explode on brand new motherboards or over an extended time of normal use.
As far as I am aware, most SOYO motherboards used defective Sarcom Capacitors. The results were devasting for Soyo because they were flooded with customer warranty repair claims, SOYO failed to replace *all* defective Sarcom caps (they only replaced individual caps that tested bad within the warranty period), and finally they simply delayed or ignored customer complaints about their defective parts.
International Lawsuits were filed and judicial court judgements decided against Sarcom Capacitors, Soyo, and many other small Motherboard manufacturers. These small Asian companies were held liable for product repair/replacement of the defective Sarcom Caps. SOYO, like many other small OEM Motherboard manufacturers in Asia and elsewhere, could not financially support a massive recall of SOYO motherboards, so SOYO management staff filed for bankruptcy and dissolved the company. I seem to recall there were no bankruptcy bidders interested in buying and restarting the Soyo company, which is why the SOYO seemed to disappear when its company assets were broken up and sold off…
Over time, I replaced all of my SOYO motherboards Sarcom capacitors with correct replacements from Nichion and other reputable capacitor OEMs. No eBay purchases here, you never know if eBay Capacitors are really what the Seller claims they are!
Oops, Steve, don’t you mean Hydrogen, instead of Helium? to this day, i repair all my own LCD TV boards, computer boards, and control boards in appliances, built between 1998 and 2008, in products made with Electrolytic Capacitors, which failed. Yes, I order from Mouser, Digikey, quality parts.
How can I use scrap CPU capacitor to make 1hp or 0.5hp motor starting capacitor?