When designing a printed circuit board, there are certain rules. You should place decoupling capacitors near the power pins to each chip. Your ground planes should be one gigantic fill of copper; two ground planes connected by a single trace is better known as an antenna. Analog sections should be kept separate from digital sections, and if you’re dealing with high voltage, that section needs to be isolated.
One that I hear a lot is that you must never put a 90-degree angle on a trace. Some fear the mere sight of a 90-degree angle on a PCB tells everyone you don’t know what you’re doing. But is there is really no greater sin than a 90-degree trace on a circuit board?
This conventional wisdom of eschewing 90-degree traces is baked into everything we know about circuit board design. It is the first thing you’re taught, and it’s the first thing you’ll criticize when you find a board with 90-degree traces. Do square traces actually matter? The short answer is no, but there’s still a reason we don’t do it.
RF and Capacitance Implications
When you ask someone why 90-degree traces on a printed circuit board is bad, the first reason given is RF interference.
The most-cited reason as to why you shouldn’t use square corners on traces is that electrons bunch up on the corners. This is impossible with our current understanding of physics and would break the universe. Fortunately for everyone, you can just rent test equipment that will test a circuit at 20 Gigahertz. If you’re really good, you can find that test equipment in the trash. Earlier this year, [Bil Herd] put square corners to the test by measuring the impedance of a trace that looked like a square wave. At 20 Gigahertz, the effect of square corners was minimal. At lower frequencies, the effect would be less. Don’t worry about square corners on your traces.
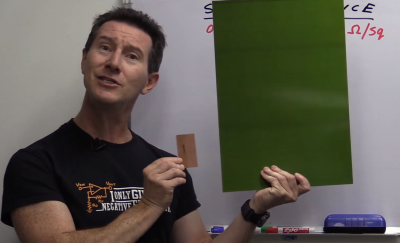
There are few, if any, implications for using 90-degree traces in respect to RF interference, but due to the nature of square corners on traces, we do bump up against the resistance of a trace. This resistance is a function of the shape of a trace, and this is known as sheet resistance. [Dave Jones] did a wonderful video on sheet resistance, and the big takeaway is that resistance of a trace is measured in Ohms per square. That’s Ohms per square, without any other dimension; a square of copper two millimeters on a side has the same resistance as a square of copper ten millimeters on a side. It’s counter-intuitive.
With that said, a 90-degree corner makes little difference in the resistance of a trace provided it is replaced with a 45-degree corner. That’s simply how triangles work. It does make a difference in the capacitance of a trace, although that effect is very minor. This has been covered by [Bil Herd] in his test of high-speed PCB design techniques and it’s been written up in EDN as a rule of thumb for high speed design. The takeaway is that square corners do effect capacitance, but it is not really an issue unless the rise time of the circuit is extremely low. The official rule of thumb is that a square corner will affect the circuit when the line width in mils is greater than five times the rise time in picoseconds. Unless you’re dealing with relatively high-speed signals — the black magic of RF or SPI busses on the order of 100 MHz, it doesn’t matter.
Acid Traps During Board Etching
Acid trap isn’t just the latest frontier of my Soundcloud, it’s also something you must take into account when manufacturing a circuit board.
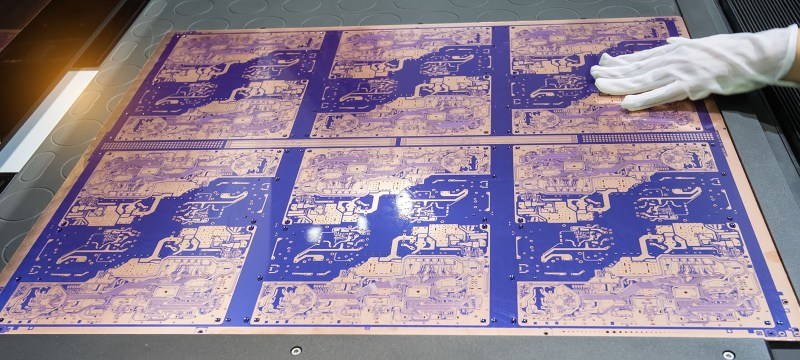
Most circuit boards begin their life as a sheet of fiberglass or other substrate covered with a layer of copper. This is the raw material for every board house, and although there are differences in the substrate, the amount of copper applied to a board, and whatever intermediary processes go into manufacturing a PCB, everything begins with copper bonded to some sort of non-conductive material. To turn this raw material into a board, a portion of the copper is masked off and the copper is removed. This can be done with laser printer toner or Ultraviolet-cured photomask, and the copper is then etched with a chemical, either Ferric chloride, Sodium persulfate, or Cupric chloride. There are many different ways to make a PCB, but they’re all strikingly similar.
When etching a board, it is possible a ‘puddle’ of the acid solution could collect at the corner of a trace. If this happens, it is possible the acid could eat away at copper underneath the photoresist. This, in turn, decreases the effective width of a trace, potentially breaking the trace entirely.
For all the tips and tricks presented to first-time board designers, the ‘acid trap’ explanation is the implicit reason for why you should not use 90-degree traces. The Eagle blog gives a top-ten routing tips for new PCB designers, and acid traps are the reason why you shouldn’t use 90-degree angles. ‘Ease of manufacturing’ is the reason for not using 90-degree traces on many articles for the tips and tricks of PCB design.
However, this tip for avoiding acid traps is decades old and the technology behind PCB manufacturing has improved greatly over the years. If your PCB fab is having problems with acid etching copper in a corner, you should probably find another board house.
So Why Does It Matter?
The know-how that goes into designing a PCB is a lot like driving a car. Anyone with a drivers license can get in a car, drive a few miles, and pick up some groceries. You can put some drinks in a cooler and go on a two hundred mile road trip no problem. The basics of driving a car are more than sufficient for 99% of your time on the road.
In driving and PCB design, there are exceptions to the majority. Popping down to Dollar General in a Chrysler Sebring is a lot different than taking your favorite supercar around the Nürburgring. Likewise, building a multi-Gigahertz circuit is much harder than connecting a Bluetooth module and an OLED display together to make a smartwatch.
The reason we don’t see square traces in most PCB designs is simply due to aesthetic convention. If it looks wrong, it is wrong. There is no specific reason why every circuit board design should shy away from 90-degree angles on traces, it’s just something that you shouldn’t do because it looks wrong.
I just think it looks nicer, but I suppose you could argue that’s the case because everyone does it.
Actually I wish KiCAD had bezier or arbitrarily curved traces…. you could make some really nice looking circuits with that. Really the only place you see stuff like that is hand drawn PCBs… and the extremely rare modern PCB done with a EDA suite that supports curves.
Does the Gerber format support curves? Sections of ellipses maybe, but Beziers?
That does not really matter, all you need is to export the trace as sequence of very short lines when saving in formats that does not support it.
Your comment remembers me those old printed circuits from the 70’s with curved lines.
The Russians would disagree: https://en.wikipedia.org/wiki/TopoR
I use TopoR for routing. It creates nice curved traces, like hand drawn. An example:
https://cdn.hackaday.io/images/9643181561638360096.png
From one of my projects:
https://hackaday.io/page/6119-programming-an-ice40hx4k-with-an-arduino-and-python
To the author’s point, that is likely a fine circuit you’ve designed there, but it looks like a hot mess because of the curved traces. I’m firmly in the “keep ’em straight and angled” camp.
For very high frequency, curved traces are better. But the best is that it minimizes the number of vias, which are even for lower frequencies an additional inductance and could be a problem. Any given layout with straight traces can be routed with less vias, if you use curved traces. The TopoR webpage shows some impressive examples of more complex layouts, where they even could reduce the number of layers, and the length of the traces. Function and price is more important than aesthetic.
But for my simple circuits it doesn’t matter, I bought it for the nice curved traces :-)
How about this? I *love* curved traces far too much, and I use them almost exclusively. I am obviously biased a bit, but I think they look really swell. They look much less hand-drawn since they generally use 45/90 degree paths when not changing direction.
Zoomed out: https://i.imgur.com/Ze0Jdcs.png
Zoomed in for some of the detail up top: https://i.imgur.com/XiONTDp.png
For some reason, clicking my hotlinks fail to load the images until they are refreshed. Maybe copy the link into a new tab.
I removed the i.imgur and replace with imgur and that worked for me.
Pretty :D
The Kapersky effect is why many of us will pass on Russian software. For better or worse.
You can just run it in a non-Internet-connected VM if you’re concerned, you know that, right?
No, you can’t. At least the full version I bought detects a VM and doesn’t allow to run in it, you need to run it on a real PC. I guess they did this to make it harder to make illegal copies.
OK, don’t pay your bill, no interwebtubes.
Oh no. Well, there’s another way… Just get a throwaway laptop from, like, 2012 =D that way, you can run *all* your suspicious software on it!
The free version of eagle supports curved traces. I just got a few boards in that use them exclusively and I must agree with you: they look really nice.
Those images you posted are slick. Now those are some curved traces I can get behind. Looks organic! :)
Thank you! I was worried that it would look silly in real life, but I like the finished PCB even better. It’s definitely some work to get them to come out that way and look consistent but I think it was worth it since I’ve got the room to spare on this board. I especially like the organic comment, since I was having trouble articulating how they felt to me when I first started playing with them. Definitely feels less electronic.
thanks for the info / dig the curves. seen on some boards of the past: a bonus silkscreen (of the traces) on the component side of a single-layer board. for visualization and for kit pcbs, the components can be seen with their connections. (the silkscreen is a duplicate of the traces, in this case.) applies to through-hole simple circuits and not smaller/complex/surface mount pieces.
or maybe even a software that convert your traces to look like a well known painting…
Check out https://boldport.com and pcbmodE (https://pcbmode.com/)!
I’ve designed plenty of PCBs without a single straight line in them! We would often pull up AutoCAD to draw flex PCBs where the mechanics were too complex for Altium. LinkCAD can convert DXF to Gerber, but you have to clean it up afterwards using a proper CAM editor like UCAM because it can make a bit of a mess out of some shapes, though later versions of LinkCAD were significantly better in that aspect. It all depends a bit on what the goal is, you’re usually aiming for “manufacturable enough”. The only time you really start looking into such things is if you’re pushing the manufacturing process to its limits or have to achieve some ridiculous reliability standard in dynamic applications.
One concern is the likelihood of a square trace peeling…….coming unglued. Also I did not observe the word “reflections” being discussed in the post. Impedance discontinuity? Best to measure with a single square corner in a long trace, and proper impedance matching otherwise.
Adhesive integrity was the reason given to me by the mentor I respected. Impedance was only considered when impedance was critical.
I forgot to mention, that same mentor also told me modern manufacturing techniques make the adhesive concern moot, except for extreme situations. “But folks stuck on old fashioned tradition will get bent out of shape.”
Still matters for polyimide boards in some instances, and 90° corners can act as a failure initiation point in thermal cycling, so it’s still best practice to avoid them.
You can actually trim the outside of the corner to avoid the increase in capacitance and the produced reflection. Incidentally, the amount of additional capacitance produced by series resistor pads is huge compared to the amount of extra capacitance produced by a corner. To avoid the extra capacitance produced by pads, designers of high speed circuits often make windows in the ground plane underneath them.
Am I the only one who remembers when circuit boards were routed without sharp corners at all, of any angle? I remember when circuit boards used to have nice, smooth, flowing design without a single angle to be seen. Ahhh…. the past…. I miss you so ;)
And we have found that old grizzled artist who still hand draws his PCB’s with sharpie with nice flowing signal traces. :)
lol… I really do!
I work with a woman who routes our production test boards straight from one pad to the next one. There are no parallel traces, or perpendicular, on the whole board: it’s just a mass of shortest-route lines. The boards work, but they sure look weird. It isn’t flowing at all, either. It’s like how a comic book artist draws an explosion.
Check out the flexible circuits on 1970’s and early 80’s car instrument panels. No computer routing there. All the traces flowing smoothly with no sharp corners.
I used to do them, not least for the LED clock in the Ford XD Falcon. The crepe tapes could be curved a good bit. The most convenient way to make a 45 degree corner was to cut the tape most of the way across from the inside of the corner, swing the tape on that hinge, press down. Quite quick. A curved corner could be made by compressing the tape on the inside of the curve. I liked the look of that, but in hot weather the compression could lead to tape lift if you’d gone too tight. A great ugly loose curve might stick better, but ugly is ugly.
it’s good to hear the appreciation/preference/details, yet it’s difficult to know the scale of those taped designs. from photographs seen of 1950s/60s/70s, the taped work was about 10 times the size of the produced board. it’s unclear if that was a common sizing or if the original art was created at bigger sizes in the past, smaller in later years. hopefully this question of scale will be answered someday because imagining the tape and cutting work.. can not be accurate given no scale or units [by anyone, online, ever].
I always did my taped layouts 4X. 10X would be too big to work with.
Check out TopoR — it makes traces exactly in this style.
Awesome! Unfortunately (in this case anyway), I run linux. I may see if that’ll work with wine.. Thank you!
Ahh… the days when the preferred CAD system was Chartpak tape, Rev 1.0
Thank you for reminding me how old I am.
I have some big 4X taped acetates mounted as art in my offices. 34×22 inches :-)
Those were done with tape and decals. The tape was really thin black masking tape, like that used for pinstripe masking on cars. The decals were DIPs, TO-92 and such, and holes were little black donuts. You stuck them to mylar sheet, repositioned them with an X-acto knife and then photographed the result on a light table with litho film. Exposed the resist covered PCB through the litho negative with UV light.
Black for the pads, and red or blue for the traces made double-sided boards.
Modern software, like DipTrace for example, can do that too. I did a headphone amp design that used such traces and free-form copper pours to achieve the “hand-drawn” effect of old designs. I based it on a PCB from old Unitra tape recorder I had in 1990’s…
https://www.youtube.com/watch?v=7weZ0TNRcuw
I often find myself needing to create a branch in a trace, and instead of just drawing a trace perpendicular to a straight trace (for a T junction), I make two 45 degree bends with the third trace on the intersection, which still makes a 90 degree corner, just rotated by 45 degrees on the screen…
The sum of the 3 angles obviously equals 360 degrees, and assuming you restrict angles to multiples of 45 degrees, it’s impossible to have all 3 be more than 90 degrees.
360°/3 = 120°
45+45+90=180
“If your PCB fab is having problems with acid etching copper in a corner, you should probably find another board house.” this is true, though, making really tiny details on modern processes can give lower yields if one doesn’t take acid traps into consideration every now and then.
So keeping the practice alive on larger boards is a bit like saving oneself from a problem one might never run into to start with. Unless one suddenly sits there designing a board with tiny dimensions and ending up with slews of problem with etched through corners on traces and such…
But other then this, it really doesn’t matter much.
Back in the ’80s, my mentor didn’t mind square corners, the processes of the day could handle this with no problem. He did disallow angles tighter than 90 degrees though, potential acid trap was his reasoning.
I’m not sure I understand the discussion about sheet resistance and square vs angled traces.
Going at a 45 degree angle across a square is a shorter trace than going around the square edge.
Shorter trace, lower resistance.
But then I do low(er) frequency, higher current circuits. I^2R is not to be ignored.
Sheet resistance, AIUI, is the resistance of the unetched PCB. Measuring resistance across an unetched sheet from opposite corners, is an infinite number of parallel resistive paths. Does that help?
It’s very simple:
If you have a PCB track, and make it twice as long, then the resistance doubles.
If you have a PCB track, and make it twice as wide, then the resistance halves.
If you have a PCB track, and double both it’s length and widht, it’s reistance stays the same.
A short ans stubby PCB track can be square.
If you change the width and length of such a track, but keep the length to widht ratio, it will still be square and the resistance of that part does not change.
There are a few caveats of course, it implies uniform resisttance distribution. If you make the copper thicker, then the resistance drops. It also implies uniform current distribution through the area, and neglects edge effects, or sudden widht changes.
I find it difficult to resist a widht
reistance is feudal.
I understand sheet resistance. But square corners seem to imply longer paths.
Longer paths -> higher resistance, all other things being the same.
you’re right: an angled trace-corner is cutting a hypotenuse, QED shorter linear length of trace for a given routing, although you get into diminishing returns on the usual ‘chamfer corner’ that’s < 2mm compared to power traces that have to handle the entire load of a large widget getting a 5 cm corner knocked off (sqrt( 2×5^2)= 7.mumble, so you're saving 3 cm of distance
Two things missed by the article:
1) The total impedance change follows approximately the “loop area” of the traces leading up to and following from the turn whether it has a sharp corner or not. You’re making an inductance loop every time you change the direction of the trace – but that’s only going to make a small difference. Whether you go into the turn gradually or sharply affects how abruptly the impedance changes around the turn, and with sharp changes in impedance, you get signal reflections and resonances.
2) High current carrying traces exhibit proximity and skin effects, which make the current distribution across the trace uneven. This creates hot spots around the sharp inside corners of square traces. That causes Joule heating, uneven thermal expansion, and may cause the traces to either burn or peel off the substrate.
Oh, and
3) Traces carrying high voltages should not have sharp corners because you get charge concentrations that arc over more easily.
4) with lots of traces, sharp corners waste board area because making a 90 degree corner always makes the trace longer
Someone modeled a square trace as a very fine grid of resistors in spice, and came up with this (current is going clockwise from the bottom left to bottom right around the white area):
https://i.stack.imgur.com/PIADF.png
Eddy currents too….
Don’t forget these 3 guys!
https://en.wikipedia.org/wiki/Ed,_Edd_n_Eddy
B^)
The 90° corner has more area, and therefore greater capacitance which changes the impedance at that point. And no, the inductance loop doesn’t care a bit about direction. It only cares about the area of the loop, not the shape of the loop.
The 45 degreee angles are often a pure neceesity to get a board routed.
The actual angle does not matter, but 45 is a simple default of most PCB programs.
Just have a look at the picture at this post above.
The bottom part between the connector would not be possible to route with square angles.
Also, try to convert al the slanted lines on that picture to horizontal and vertical tracks.
They simply would not fit in the same space on the board.
It’s for the same reason that SMT IC’s are somtimes put under 45 degrees on the board.
It leaves more room for routing the tracks around it.
But apart from these practical reasons:
Thanks Hackaday for exposing this urban fallacy.
“With that said, a 90-degree corner makes little difference in the resistance of a trace provided it is replaced with a 45-degree corner. ” So the key to using right angles is to not use right angles? Similarly I was hard-pressed to find a right angle in the accompanying graphic. I think you’re onto something.
I am not convinced. The one thing that was left out of his test was what gets induced to a trace next to a 90 angle. If he had ran two tests on his PCB to show that then I would be convinced.
I.E. Two parallel traces close together. One with a bunch of 90’s like he did for one trace and then a straight trace next to it. View the secondary trace with scope to see what (if any) would have gotten induced on it. Then another test much like the first, but with rounded corners for the squiggle.
Do grace us with all that Brian got wrong in this article.
He assumed anyone cares about what he says.
As far as I remember. Square corners add noise.
Well, rounded or 45 deg corners make for shorter traces, which makes for faster circuits.
Is there a reason that the “equal length” features in CAD packages use serpentine instead of square corners or even Greek Key?
Greek Key, that was a new term for me to explore.
https://en.wikipedia.org/wiki/Meander_(art)
Square corners should be avoided on signals with fast edge rates, such as DRAM, PCI Express and other high speed interfaces. The impedance discontinuity of a square corner causes reflections which damage a fast signal’s waveform.
Slow edge rate signals like CMOS GPIOs, SPI, I2C, etc. are less vulnerable and square corners are probably OK for them. So for most Hackaday sort of projects I wouldn’t worry about it. That’s one of the benefits of professionally developed boards like Raspberry Pi, the fast sensitive signals are already well routed.
That’s what I was told also as the main reason not to use 90° angles. Reflections. And even though it was several decades ago, I can remember doing a practical experiment in class on this topic, and observing reflections or “replicas” of a signal edge due to that kind of trace.
Another nice article that goes beyond “here’s the rule, trust me” and explain it with science then test it in the real world : https://www.edn.com/electronics-blogs/all-aboard-/4438573/When-to-worry-about-trace-corners–Rule-of-Thumb–24
I always figured no 90s was for mechanical reasons. Sharp corners are stress risers and could cause cracks (broken traces) over time. I know they require round corners for flex PCBs for this reason.
my kid made a small tear in the outer nylon shell of his stuffed winter coat. i didn’t know what to do but i figured it would peel off right away if i repaired it with duct tape. some forum somewhere had someone saying to cut the duct tape into a circle so it doesn’t have corners to start peeling at! kind of obvious in hindsight. took a whole calendar year to peel off. anyways, a demo for the mechanical problem at corners. of course, a 45 is still a corner (if you don’t round it off).
Yeah, when I am using iron-on patches for my clothing, the round corners (is that an oxymoron?) take longer to de-laminate than the square ones.
Early mass produced cost down PCBs had only one copper side and no solder mask or screen. Components were placed and the board wave soldered. The solder covered the traces and protected from oxidation.
Square corners would hold a large drooping bubble of solder.
Some 1980’s micro computers (like the TI-99/4 and 4A) had the whole board wave soldered, then solder mask was sprayed over the whole bottom side. Made all the traces heavier being fully solder covered.
Grid bug behavior is inefficient.
I’ve seen square traces in older computers before, it’s interesting to see Example https://i.imgur.com/2ekLdkh.jpg
(rest of album https://imgur.com/gallery/Xzllw)
And a typewriter from the 70s https://i.imgur.com/IFXb9cm.jpg
(album https://imgur.com/gallery/ygjmH)
A lot of folks like me started off doing the standard hand taping of a mask and etching it with skin-melting chemicals in little plastic containers. I too was told the 90 degree thing, but the problem was twofold, mechanical and aesthetic. Mechanical because the sharper the corner the easier the tear. So when laying down tiny strips of plasticized tape, any mechanical tension on a trace (such as as simply touching it with your big mitts as you lay another really close) meant if was going to peel off or tear, at a 90 bend was where it would start, guaranteed. The other reason was just because right angle bends looked bad to my professor, and he would deduct points for style! Lol
I do a lot of RF PCB simulation using the Sonnet application suite. I don’t know about whatever guy’s square corner PCB trace measurements at 20 GHz but in my work from VHF to low microwave I definitely see a difference in the sims. These are the kind of small impedance discontinuities I *intentionally* design with in order to make planar PCB filters out of nothing but PCB (no components, even passive ones).
I totally agree with you and some others that ‘normal square corners’ don’t perform good at anything from VHF to microwave frequencies.
This is due to the fact that the corner itself adds capacitance and the impedance of the corner is no longer 50Ω.
That is why mitered corners are used, I found that a miter of about 80% is usually good enough.
More information about RF performance of this can be found at:
https://www.microwaves101.com/encyclopedias/mitered-bends
For normal design rules I am not allowed to make traces with <90° (this is what we call acid trap) bends so 90° are allowed and should not be a problem.
This article leaves me feeling the need to create my next circuit board with as many square corners as possible.
Yes.
Anything under 1 GHz is DC!
B^)
Kudos to you; I have worked on RADARS for years and everything you said was totally true. Delamination was àlso a problem with 90 degree corns but modern manufacturing has cured that problem. Most people don’t work with GHz stuff and then that becomes another monster requiring a different skill set with better planning.
One problem I’ve seen with square traces was power supply for CCFL tubes for monitor back light. There was a high voltage square trace (around 800V) supplying power to the back light tubes next to gnd plate and apparently after some time sparks started to appear between the edge and ground plate. I guess that at high voltage you have to avoid sharp pointy shapes to avoid unexpected discharges.
coronal concentration points, it’s why high static voltage demonstrator connecting bars have knob ends instead of just square-cut rods
Acid-Trap sounds intriguing – can we have a link to your Sound Cloud? :)
That’s the name of my new Heavy Metal band..
Even just saying “acid trap” I can hear the beat and bassline already. You will make millions!
Could it have anything to do with the higher possibility of arching between lines, when shorting an overloaded circuit ?
(Ancient history.) My father was an electrical engineer at Westinghouse. He designed (huge) power supplies used in steel rolling mills and aluminum refining. The currents used were perhaps 100 amperes and up. (This occured 60 years ago and I’ve forotten the details.) The current flowed through busses with a few square inches of cross section. One device was behaving unexpectedly and they localized the problem to a right angle turn in a buss bar, something generally avoided. The quarter of a turn created an unexpected inductance that affected the performance of their device. I normally thought of inductance as based upon the number of turns of a wire and the idea of a quarter of a turn was baffling to me. My father did the calculation and explained it to me. With bemusement.
One thing about non curved traces is, they are a disaster when doing test boards for new chips and impedance is very important. It is almost impossible to gain 100Ohm differential with 2 traces running with 90 degree corners.
The real world are sometimes funny. We have done test boards for backbone switches and what measurement tools told us did not matter actually did when You looked at it from the die of the chips. There were rather large differencies between 90degree, 45 degree and fully curved (spline lines) lines, even thugh scopes and other tools said it did not matter.
Saying Acid traps are from the past is not good. You just killed the hole community of Youngster who would try doing PCBs at home. Acid traps shoulld always be considered. even proff do “home” pcbs at job every now and then. If these are not washed correctly or treated with chemicals, acid traps could easily mean problems. So just to say, it is time consuming to take care is extremly bad, there might be projects where laisyness could cost a lot of debugging hours.
And talking about good or bad fabrics, I still beleive fabrics has these problems every now and then, but the good fabric throw out boards not having You paid for that.
Ok I might be more scared than others as many of my jobs demanded 0,07 or 0,06 mm traces, and they do not need a lot of acid to be cut. This is very difficult to see under a bga chip or equal unless you are the owner of an xray tool.
What are you talking about?
If 45’s were good enough for the paper corners on Battlestar Galactica they’re good enough for my layout.
Apologies in advance but I can’t help it….
“But is there is really no greater sin than a 90-degree…”
According to my calculator sin(90) = 1 so there is in fact no greater sin.
Back when I worked for Tektronix and their circuit boards were designed by ladies, there were no sharp corners on traces because they caused interference problems. Their boards were considered the best in the business because of this (and other features).
Guess I am going to start putting some intentional 90-degree traces on my PCB design from now on then. Haha.
Here is an image of a 741 op amp die, 90 degree corners thru out.
http://www.righto.com/2015/10/inside-ubiquitous-741-op-amp-circuits.html
More examples of high speed circuits with 90 degree traces.
https://commons.wikimedia.org/wiki/7400_Series_Overview
He may have tested it to 20 ghz, but these days with high speed transceivers it’s very easy to require analog bandwidth even above that. Thunderbolt 3 for example, requires the traces to be routed with no corners. 40gbps lines often require analog bandwidth greater than 28ghz.
Acid traps are still a concern if you bake your own PCB at home, with laserprinted etch masks, home-depot materials, and all such technology that was left behind by the big companies ages ago.
Anyways, it appears that I was taught well. Because ‘acid trap’ is exactly the reason I was told to not use 90-degree corners, in University. :)
Well it seems it falls to me to be the graybeard on deck that puts the origins of the “no right-angle bends” meme onto the Hackaday historical record.
Back in 1971 Motorola published a book titled the MECL System Design Handbook by William J. Blood Jr. Back in those pre-web pre-microwave simulator days it quickly became the go-to compendium of information on the new field of high-speed circuit design. There were a sprinkling of IEEE Trans articles on the subject and I remember Ivor Catt published a couple of somewhat confused articles in the area, but the MECL handbook gave you a quick insight into the general design requirements and all in one slim volume.
So I guess it took a while for there to be a large enough pool of end-users working at those logic speeds for the Cad vendors to get interested. By around I’d say the early to mid ’80s the vendors like Cadence had realized there was a useful competitive advantage in being able to create chamfered bends and they started coming in and giving us presentations on their resulting new tool offerings.
The source of this change was an illustration that Blood had included: figure 7-17 ‘Reflection Caused by Signal-Line Shape Variations’ on page 138. He showed a comparison of the TDR results for an S shaped trace with 90 degree right-angle bends compared to the same trace layout with smooth radius bends. The sharp right-angle bends coincided with rho = -0.075 and -0.05 reflection discontinuities in the reflection coefficient trace. These discontinuities were absent when he tested the trace with smooth radius bends. That diagram was pretty much the entire reason for the seachange in layout technologies.
However fewer people seemed to have paid attention to the PCB technology that Blood was using for the test fixtures used in his illustrations. He cites his Er =5.3, board dielectric thickness = 0.062″ (1.7mm) and copper thickness = 0.0014″ (0.035mm). Using these numbers he set his 50 ohm line width at 0.1″ (2.54mm or 100mils).
Because of the width of the microstrip lines he was using a large discontinuity occurred in the per unit length line capacitance at the corners – roughly 0.09pF. You can get a very crude feel for the way the reflection changes with line width if you imagine clipping the outside of the corner off at 45 degrees and then calculating the capacitance of the right triangular piece of etch you just removed. For a 3mm wide 1oz trace on 1.57mm thick FR4 (Er~=4.3 ) you get a Z0 of 49.3 ohms and a corner capacitance of 0.11pF, very similar to the MECL handbook case. If you reduce the line width to 5 mils using the same board stackup you get a Z0 around 155 ohms but that additional little triangle of etch now only contributes a capacitance of 0.2fF. So the line impedance changes by a factor of 3 while the corner capacitance decreases by a factor over 500. As a result the frequency at which you start to see reflection artifacts from the corner impedance discontinuities on a 5 mil wide line goes up by a couple of orders of magnitude. However you also pay a really heavy toll in increased skin effect losses and line-line crosstalk as you decrease the line width so you’re not going to ship high speed data as far.
Given the data rates we were using back then and the fact that PCB real estate was and still is a critical factor which drives the use of minimal line widths it always amused me that the entire PCB layout industry enacted a technology churn that only benefited nets that were mostly edge cases back then.
Younger Dave? Dude that video is from 2015 and your post from 2019, barely any time passed…