Concrete is an incredibly useful and versatile building material on which not only today’s societies, but also the ancient Roman Empire was built. To this day Roman concrete structures can be found in mundane locations such as harbors, but also the Pantheon in Rome, which to this day forms the largest unreinforced concrete dome in existence at 43.3 meters diameter, and is in excellent condition despite being being nearly 1,900 years old.
Even as the Roman Empire fell and receded into what became the Byzantine – also known as the Eastern Roman – Empire and the world around these last remnants of Roman architecture changed and changed again, all of these concrete structures remained despite knowledge of how to construct structures like them being lost to the ages. Perhaps the most astounding thing is that even today our concrete isn’t nearly as durable, despite modern inventions such as reinforcing with rebar.
Reverse-engineering ancient Roman concrete has for decades now been the source of intense study and debate, with a recent paper by Linda M. Seymour and colleagues adding an important clue to the puzzle. Could so-called ‘hot mixing’, with pockets of reactive lime clasts inside the cured concrete provide self-healing properties?
Concrete Recipes
At the core of modern concrete as well as mortar lies cement: this is the binder that is mixed with additional ingredients such as sand and gravel to turn it into concrete. Although each type of cement starts with calcium carbonate (CaCO3), the way this base material is processed and mixed determines how it cures, and what other material properties will be exhibited. The most basic type is called non-hydraulic cement, which starts off by firing the calcium carbonate (also called limestone), which produces calcium oxide and carbon dioxide:
CaCO3 → CaO + CO2
CaO is commonly called quicklime, as well as burnt lime. In the next step, this quicklime is mixed with water to ‘slake’ it:
CaO + H2O → Ca(OH)2
When the resulting calcium hydroxide is then exposed to carbon dioxide, the cement will begin to set:
Ca(OH)2 + CO2 → CaCO3 + H2O
At atmospheric concentrations of carbon dioxide, this is a very slow process and, thus, generally not very practical for construction. Common cement types such as Portland cement are, therefore, hydraulic cement, which sets by reacting with the clinker minerals that are part of the mixture. Portland cement is a fine powder which consists of at least two-thirds of calcium silicates, primarily alite (Ca3SiO5) and belite (Ca2SiO4), along with additional silicates and aluminates.
The initial step of producing hydraulic cement is the same as for non-hydraulic cement, with the firing of calcium carbonate:
CaCO3 → CaO + CO2
The next step is where things get interesting, as the resulting calcium oxide reacts with the silicates and aluminates:
2 CaO + SiO2 → 2 CaO · SiO2
3 CaO + SiO2 → 3 CaO · SiO2
3 CaO + Al2O3 → CaO · Al2O3
Finally, the oxides (calcium oxide, aluminium oxide and ferric oxide from e.g., brownmillerite) react to form the final hydraulic cement mixture:
4CaO + Al2O3 + Fe2O3 → 4 CaO · Al2O3 · Fe2O3
At its core, this is the recipe which any hydraulic cement uses, whether it’s so-called ‘Roman cement‘, Portland cement, or Ancient Roman cement. When used to create concrete, this cement is mixed with aggregate, usually small rocks, stones, and sand. Upon adding water to this mixture, the hydration process will cause the cement to set without the addition of carbon dioxide.
Sands Of Time
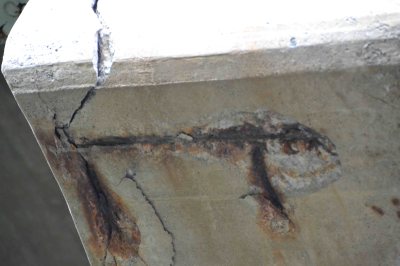
As with all building materials, concrete is also subject to many influences that degrade it over time. Some types of damage include mechanical and chemical sources, including oxide jacking and bulk fractures that chip away the material or causes cracks. Other types of damage are due to the metal rebar inserted to reinforce the concrete, with the corrosion of this rebar and subsequent volumetric expansion resulting in the concrete being destroyed from inside. Having cracks form in the concrete that allow moisture to seep in to reach not only the rebar, but also freeze during winters further work to limit the lifespan of modern concrete.
Preventing and repairing this type of damage has been the subject of much research the past decades, with a range of approaches attempted, including manual repair of visible cracks using cement, epoxy or resins. Even so, modern-day concrete is subject to rapid degradation due to the merciless effects of exposure to the effects of water. Considering the almost pristine condition of so much Ancient Roman concrete that survived over a thousand years of exposure to weather and the elements, this has obviously raised many questions.
Ancient Concrete
The ancient Romans were not the only ones who knew about and used concrete, with the ancient Greek also using the building material, even if not in quite the same amounts. One aspect about Roman concrete that we were already aware of was their use of pozzolan, specifically pozzolana such as volcanic ash. These are naturally rich silicates and aluminates, and a big reason behind the discovery of hydraulic cement by Roman engineers.
Since modern-day cements like Portland cement also include either natural or artificial pozzolans, their presence as ingredients can not be the sole reason. What other secrets have made it so that cracks and fractures haven’t shattered this ancient concrete into fine dust? For answers to this, the researchers of this recent study turned to a small former Roman settlement called Privernum in Italy.
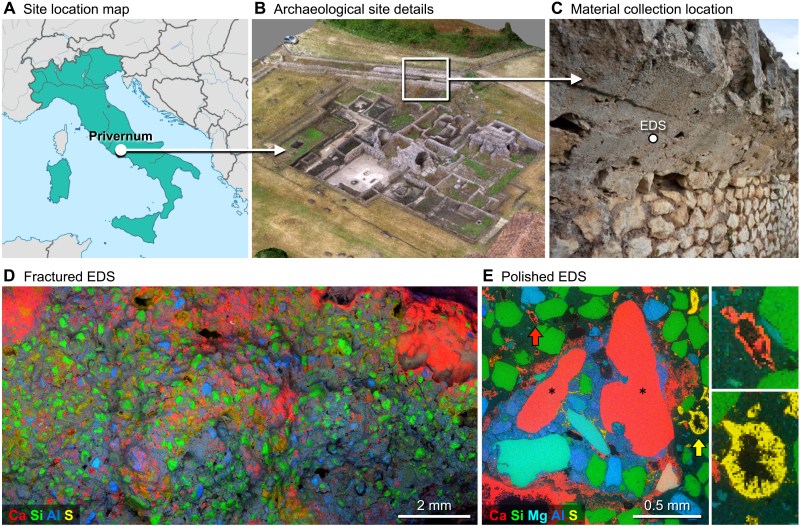
The Roman concrete test samples came from the archaeological site of Privernum, near Rome, Italy (A), and shown as a photogrammetry-based three-dimensional reconstruction (B). The architectural mortar samples were collected from the bordering concrete city wall (C). Large-area EDS mapping of a fracture surface (D) reveals the calcium-rich (red), aluminum-rich (blue), silicon-rich (green), and sulfur-rich (yellow) regions of the mortar. Further imaging of polished cross-sections (E) shows aggregate-scale relict lime clasts within the mortar (the large red features denoted by asterisks). The colored arrows in (E) denote the pore-bordering rings visible in the EDS data that are rich in calcium (red) or sulfur (yellow), which are enlarged at right to show additional detail. Photo credits (B and C): Roberto Scalesse and Gianfranco Quaranta, Associazione AREA3, Italy.
By taking samples of the concrete city wall of Privernum and studying its composition, they found that they saw pockets of calcium oxide, which was a feature that had been previously mostly dismissed as probably not relevant or just an artifact of the primitive methods used two-thousand years ago to make concrete. The theory that Linda M. Seymour and colleagues wanted to test here, however, was that these pockets of calcium oxide were not only there on purpose but that the engineers who created these mixtures likely knew what they were doing.
The Experiment
In order to test this theory, the researchers created batches of concrete inspired by their analysis of the Privernum samples, featuring Portland cement, pulverized fly ash, sand, and water. Across these batches, a varying amount of quicklime was added, and each batch cast into cylindrical molds. After curing for 28 days, the cured samples were compared with the Privernum samples, with the bright white of the lime clasts clearly visible in both. To test that it are these pockets of quicklime which enable the self-healing properties, the cured samples were split longitudinally and inserted into a flow circuit with 0.5 mm distance between the fractured sides of each sample.
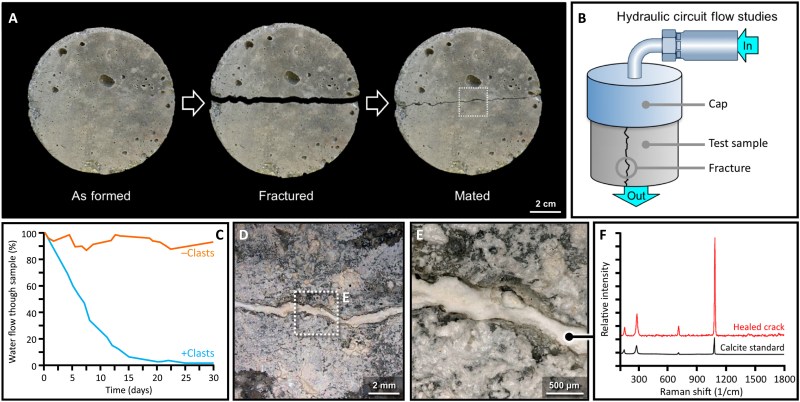
In this flow circuit, water was constantly forced through the fracture in each sample, with the flow rate measured. After an initial flow rate of 10 to 30 liters/hour, depending on the sample, after thirty days, the flow rate in the samples with the lime clasts was reduced to practically zero, whereas the flowrate in the regular concrete mix samples without the clasts had remained essentially unchanged.
The results of this experiment showed that the calcium from the lime clasts had likely interacted with the remaining free pozzolanic material to form fresh crystallization that is capable of healing fractures. These experimental results are indicated to match the analysis performed on the Roman mortars of the tomb of Caecilia Metella where a similar microcrack filling had been reported.
Vivat Romanorum Architectus
Despite so much of the engineering knowledge of Ancient Roman times having been lost over the past few thousand years, the gathered body of evidence on Ancient Roman concrete would seem to show unequivocally that self-healing concrete through the mixing in of coarse quicklime was the standard way in which such concrete was made. How this came to be, or which engineers first invented it will probably never be known, but it does appear to be a technique that can be applied to our modern-day concrete without question.
Linda Seymour and her colleagues considered this option and created a second mixture using coarse aggregates and a superplasticizer. Here the main concern was the shrinkage rate, which is mainly a factor of the setting process. The outcome here was that there was less than 1% difference between the drying shrinkage of regular and experimental concrete after a year, making it a potentially commercially viable concrete mix.
Whether we will see commercial concrete being poured using newly formulated cement mixtures based on this research remains an open question, but considering the benefits of having concrete structures that can outlast entire civilizations – both in terms of reducing the carbon dioxide output of the cement industry and a sharp reduction in the maintenance and replacement of concrete structures – it would be curious indeed if we did not.
(Heading image: “Inside the Pantheon” by Macrons on Wikimedia Commons)
Never heard of carbon carbonate…
I too have never heard of that until your comment. I searched the article text and found no such reference. I have heard of typos and misreading, which happen all the time. Maybe it was already corrected by the time I read the comment? (Leave no stone unturned?)
The Roman use of Volcanic ash and the Rock Tuffa which is soft to carve and then hardens. Self healing concrete with graphene re-enforcement will allow for advanced light weight designs. Well if it gets past 20 years of testing.
Likely calcium carbonate, CaCO3.
Should have been building our dams with it.
https://www.timesfreepress.com/news/2021/jan/09/crews-cut-slice-chickamauga-dam/
Thanks for the link. It’s wild to see the effect in action.
“The material expands slowly over the years because of a phenomenon called alkali-aggregate reaction. As the concrete expands, the moving parts of the dam lose the clearance they need to function for flood control and hydroelectric generation.”
From the article: “crews use a diamond wire saw, which is a steel cable with 15-millimeter diamond beads in it.” 15 millimeters is huge for diamonds. This seems unlikely. Perhaps 15 micrometers is intended?
Follow the link, there are pictures of shiny grit covered 15mm dia. hardened steel beads strung on a cable. The pulleys drive engine etc. pretty techy for a newspaper. Worth the visit.
Looks more like 15mm steel beads, coated in diamonds. But still an awesome thing.
Construction Physics had a great article on this Roman Concrete Study and what was known already and the biggest issues regarding modern concrete used in construction. Basically it’s that we want concrete that sets fast and uses steel internal reinforcement. Both those things give us safer and better concrete structures than the Romans but both cause issues long term.
https://constructionphysics.substack.com/p/roman-vs-modern-concrete
If our concrete has long-term issues, how is it safer and better? Maybe we should learn some patience and go back to building arches.
Not necessarily, but our average villages here in good old Europe are older than the states; many times, actually. And the village’s houses made of stone and wood are hundreds of years old, too. It’s not always necessary to use beton, err, concrete. Sometimes a self-holding building with a strong outer structure made of natural material has its advantages, too. Just look at ancient churches, they’re still standing. Or how about integrating nature? Some native tribes use wines and roots to build living bridges that last for generations.
” Or how about integrating nature? Some native tribes use wines and roots to build living bridges that last for generations.”
There’s growing furniture as well.
https://en.wikipedia.org/wiki/Full_Grown
We need to reduce energy in building by reducing heating and cooling.
Reinforced concrete allows us to build structures that are impractical or impossible with non-reinforced concrete. Highrise buildings, long bridges in places where you can’t use arches, etc.
The biggest use of concrete is in building foundations. In Massachusetts the crumbling of concrete is a major issue for many homeowners, for many years home foundations were made from concrete with impurities and now these houses all need massive repair work. Also it is used extensively everywhere for sidewalks I wonder do you know of a way to replace a concrete foundation or a sidewalk with arches? Just curious.
One example is that modern reinforced concrete is designed “under reinforced” which means that it’s failure mode will be slow and obvious to bystanders (cracking and bending). It isnt legal in any building code I know of to install “over-reinforced” concrete that would fail in a sudden and brittle way. That could be an example of one reason why we would continue to install our less durable modern concrete.
Did they check the water for calcium, before letting it flow through the sample?
Concrete is conductive, better than soil. Who’d have thought? Check out “Ufer ground”.
An even more incredible piece of ancient engineering which is sadly far less known about is the Pergamon siphon, also known as the Madradag aqueduct, designed to carry water to the Greek city of Pergamon in around 200BC.
When we talk of ancient aqueducts, most people assume we mean the overground stone constructions seen particularly around Rome, but then as now most plumbing was underground, and all were generally known as aqueducts. To carry water to the city of Pergamon from the nearest suitable spring meant crossing a valley 190m deep. It would be quite impracticable, if not impossible, to build a stone structure that high. So instead they built a siphon. The principle of a siphon is pretty simple: fill a tube with water, and it will reach the same level at either end, no matter how much the middle hangs down. The problems are 1) keeping it leakproof, and 2) making the lowest points strong enough to cope with the pressure. Remember that for each 10 metres of water height you add roughly an extra atmosphere of pressure. The Greek engineers who built the Pergamon siphon made it work successfully, apparently only using terracotta piping.
The best exploration of this and other areas of Roman Engineering I have found are in the Spanish series Ingeneria Romana, which is available on You Tube with auto-generated subtitles which are for the most part pretty good.
https://www.youtube.com/watch?v=lLVjv6J-7A0&list=PLX9K6BsUtIfJaMieISPGbsNLsIXB-RR-o&index=2
> So instead they built a siphon. The principle of a siphon is pretty simple: fill a tube with water, and it will reach the same level at either end,
I don’t see that in the documentary. What I see is an graded tunnel. They used a siphon tube to check the level of the digging along the way, not for the aqueduct itself. For obvious reasons as stated in the documentary: if it wasn’t downhill all the way and steep enough, it would get clogged up with silt. If it was too steep, the water would speed up too much and erode the tunnel, so they had to keep it descending at 1 part per 10,000 all the way, or about 10 cm per kilometer.
They went through many mountains and hills, but not once did they make a U bend in the aqueduct. That wouldn’t have worked at all.
There is a u bend in the aqueduct with lead pipes under concrete. there were 50 sand traps to clean the water to avoid it silting up. I believe you are watching the wrong video as the siphon is covered in los aqueductos part 2
I’m watching the video that was posted for reference.
That particular point may have come up in part 2 – I’ts been a while since I watched the programme – but I thought it was worth linking because that show is by far the best mainstream coverage I have ever seen on Roman engineering. I believe the presenter has a background as a civil engineer. I would have also like to see more detail of the Pergamon aqueduct, but this was a Spanish programme made for a Spanish audience and understandably concentrated on Spanish structures. I do remember it being discussed, though. I had never previously heard of it.
If you want something even more impressive, watch the episode on mining (Minas) on the same playlist, where he explores in great detail how the Romans washed away mountains of soil to extract gold from the area now known as Las Médulas. Google pictures of teh present site. The tips of those orange columns are the remnants of the ancient surface level. It is comparable to some of those giant Australian mines but done without modern machinery.
Are there any video in that series that go over old formulations of concrete?
Dude it’s well known that siphon were used in such a way and also when a river was blocking the route of an aquaduct. I haven’t watched the video but I do know from reading they used siphons.
Stone moves;modern life just doesn’t give it the time.
This is a wonderful article, a lot of effort, research and heart had been put into it. It’s very informative and interestingly written, even to the clayman! Let’s congratulate the author! Kudos! 😃
Thomas Edison knew the secret to durable concrete. The sidewalks around the Edison museum are over 100 years old and yet they look like new, with the Edison Concrete logo.
I still don’t see how the experiment proves whether the excess CaO in the Roman concrete was there by design or chance. It shows that there is a benefit to having it there, but not whether the Romans knew it.
Obviously the Romans weren’t able to do empirical chemistry. Ancient chemistry was a lot more qualitative than quantitative. Mix a shovel of this with a shovel of that and half a bucket of water… Frankly, much small scale concrete work even today is much the same. I’ve mixed my fair share of concrete that way laying the odd slab or two for garden projects.
I suspect the excess CaO is as much a beneficial result of the limitations of Roman metrology as anything else. It should be noted that Roman concrete tended to be thick compared to modern concrete because they didn’t reinforce it with metal. I wonder how much it even cracked during a typical mason’s career span.