There are a number of ways to give a robotic actuator a sense of touch, but the AnySkin project aims to make it an overall more reliable and practical process. The idea is twofold: create modular grippy “skins” that can be slipped onto actuators, and separate the sensing electronics from the skins themselves. The whole system ends up being quite small, as shown here.
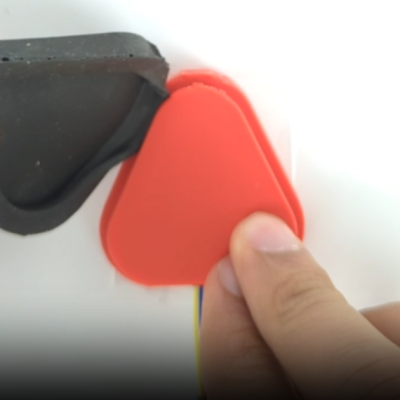
The skins are cast in whatever shape is called for by using silicone (using an off-the-shelf formulation from Smooth-on) mixed with iron particles. This skin is then slipped onto a base that contains the electronics, but first it is magnetized with a pulse magnetizer. It’s the magnetic field that is at the heart of how the system works.
The base contains five MLX90393 triple-axis magnetometers, each capable of sensing tiny changes in magnetic fields. When the magnetized skin over the base is deformed — no matter how slightly — its magnetic field changes in distinct ways that paint an impressively detailed picture of exactly what is happening at the sensor. As a bonus, slippage of the skin against the sensor (a kind of shearing) can also be distinctly detected with a high degree of accuracy.
The result is a durable and swappable robotic skin that can be cast in whatever shape is needed, itself contains no electronics, and can even be changed without needing to re-calibrate everything. Cameras can also sense touch with a high degree of accuracy, but camera-based sensors put constraints on the size and shape of the end result.
AnySkin builds on another project called ReSkin and in fact uses the same sensor PCB (design files and bill of materials available here) but provides a streamlined process to create swappable skins, and has pre-made models for a variety of different robot arms.
My wife, a nurse, works a lot with preventing bed sores in patients. Shear is definitely a problem. I’m wondering how this sensor might be used in her work.
We use this technology for years to provide shear measurements for medical applications: https://innssi.com/s3f/
hmm. picking up magnetic materials or just plain iron is out. :( but for stones, glass, wood or plastic this might work fine.
I wonder two wires on robot finger that somehow get dipped in water deeper the more pressure inside a glove skin could do similar. Kinda like a moisture sensor but with a way to keep it within a certain range on finger. Random thought of the day
Magnetising the bulk material is a great idea! I was working on something similar for a musical instrument that cast magnets into silicone. Motion in the magnetic field was similarly mapped out using magnetometers. The hard part that I never properly worked out was evenly calibrating pressure levels across the whole surface, but I guess that’s not as much of an issue for the small touch area of the AnySkin.