BIQU has released a new line of low-temperature build plates that look to be the next step in 3D printing’s iteration—or so YouTuber Printing Perspective thinks after reviewing one. The Cryogrip Pro is designed for the Bambu X1, P1, and A1 series of printers but could easily be adapted for other magnetic-bed machines.
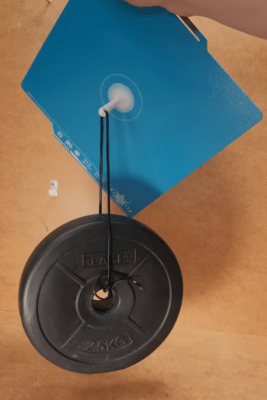
The idea of the new material is to reduce the need for high bed temperatures, keeping enclosure temperatures low. As some enclosed printer owners may know, trying to print PLA and even PETG with the door closed can be troublesome due to how slowly these materials cool. Too high an ambient temperature can wreak havoc with this cooling process, even leading to nozzle-clogging.
The new build plate purports to enable low, even ambient bed temperatures, still with maximum adhesion. Two versions are available, with the ‘frostbite’ version intended for only PLA and PETG but having the best adhesion properties. A more general-purpose version, the ‘glacier’ sacrifices a little bed adhesion but gains the ability to handle a much wider range of materials.
An initial test with a decent-sized print showed that the bed adhesion was excellent, but after removing the print, it still looked warped. The theory was that it was due to how consistently the magnetic build plate was attached to the printer bed plate, which was now the limiting factor. Switching to a different printer seemed to ‘fix’ that issue, but that was really only needed to continue the build plate review.
They demonstrated a common issue with high-grip build plates: what happens when you try to remove the print. Obviously, magnetic build plates are designed to be removed and flexed to pop off the print, and this one is no different. The extreme adhesion, even at ambient temperature, does mean it’s even more essential to flex that plate, and thin prints will be troublesome. We guess that if these plates allow the door to be kept closed, then there are quite a few advantages, namely lower operating noise and improved filtration to keep those nasty nanoparticles in check. And low bed temperatures mean lower energy consumption, which is got to be a good thing. Don’t underestimate how much power that beefy bed heater needs!
Ever wondered what mini QR-code-like tags are on the high-end build plates? We’ve got the answer. And now that you’ve got a pile of different build plates, how do you store them and keep them clean? With this neat gadget!
I guess today’s sponsor is Bambu Labs?
Doubt it! Bambu Lab doesn’t even make or sell the CryoGrip, it’s a Biqu product.
Ironically to this comment chain, BambuLab is releasing their own version next month.
Finally some innovation in printing!
There’s been a ton of innovation over the last few years. An easy way to track it is to watch for Stratasys patents since they seem to collect community efforts. They’re probably stumbling over themselves to patent this coating as well.
Love the plate, nearly impossible to remove prints, and the print residue. after 3 prints, I have little pieces of filament I cant get off the plate. Brims, etc, can be easily removed with heating the plate to 80c then you can peel them up.
These are third party by BIQU, not from Bambu Lab.
Yep. Bambu Lab have announced they intend to release their own polyurethane plate, but it’s not even available to preorder yet.
Aw, I wrote Bambu Labs instead of BIQU. I knew I’d get that mixed up. This video was hard to follow. Corrected, thanks.
I’ve more issues removing the parts from the bed than part not adhering to the bed. For the former, you have to be super cautious not to damage the (costly) bed, while the latter is easily fixed with glue or a brim or higher bed temperature or…, in fact there are lot of solutions.
All down to what you are printing, so many variables from print settings to filament to part design that can make a big difference. So having an option like this that adheres better at low temp than most build plates is a good thing. At least a good thing for some, no good for me though – I’m still a dinosaur on printing methods using ABS slurry doped tape on the build plate as it works well enough for me so no reason to get fancy build plates).
I only print PLA on glass, and I’ve pretty much eliminated adhesion problems. Given how long it takes to get reliable printing techniques dialed in, I am reluctant to start experimenting with build surfaces again, but if this meant I could print at room temp with zero warping, I’d be tempted.
My aging Ultimaker is proving frustratingly reliable, but whenever I eventually replace it, it’s nice that a bunch of incremental improvements will be mature by then. I should be able to get something noticeably faster, bigger, quieter and free of build plate issues, without having to make a whole year-long research project out of it.
“…frustratingly reliable”
Nothing worse than something that just works. I feel the same way about my printer, I know so many ways in which the next would be better (mainly with its bed, though I’d also beef up it’s structure and give it rails for more speed)! I just can’t justify the expenditure of precious hobby time on it (especially since it only sees use a couple of times a month nowadays).
You’ll be able to get all of those goals (faster, less trouble, bigger, quieter) pretty much right away, but waiting a tad bit longer maybe a good idea since IDEX/multi-tool is maturing to the point where the cost may start to drop, it’s superior to swapping filaments mid-print that has been the go-to (via an AMS type system). There’s a few cheaper options but they require tinkering, which is what I was trying to get away from myself (making 3d-printing less of a hobby of the machine, and more a tool of for my other hobbies) .. give it about a year and I think there will be some good options available.
I think bambu should put these on there machines from now on they work great and the print lets go when it cools down.