The vast majority of motors that we care about all stick to a theme. They rely on the electromagnetic dance between electrons and magnets to create motion. They come in all shapes and sizes and types, but fundamentally, they all rely on electromagnetic principles at heart.
And yet! This is not the only way to create a motor. Electrostatic motors exist, for example, only they’re not very good because electrostatic forces are so weak by comparison. Only, a game-changing motor technology might have found a way to leverage them for more performance. It achieves this by working with fluid physics on a very small scale.
Electrostatic Foibles
Electrostatic motors date back to the 18th century, having first been developed by such luminaries as Andrew Gordon and Benjamin Franklin. These motors relied upon electrostatic principles; Franklin’s version used brass thimbles on a wheel which were attracted towards charged electrodes hooked up to Leyden jars. This was enough to create some rotational motion.
Our understanding of electricity and physics have progressed a lot since then. However, as with many electrostatic curios, these motors proved very limited in their usefulness. They have struggled to find widespread application due to their reliance on high voltages to work, and the fact they produce precious little torque. The technique of creating motion via electrostatic attraction and repulsion has found some applicability at the very small scale with microelectromechanical devices (MEMS). For these chip-sized devices, the tiny scale involved reduces the voltages involved significantly, and at small scales, torque or force requirements are much lower. Still, the electrostatic motor has remained relatively obscure to this day.
New Approach
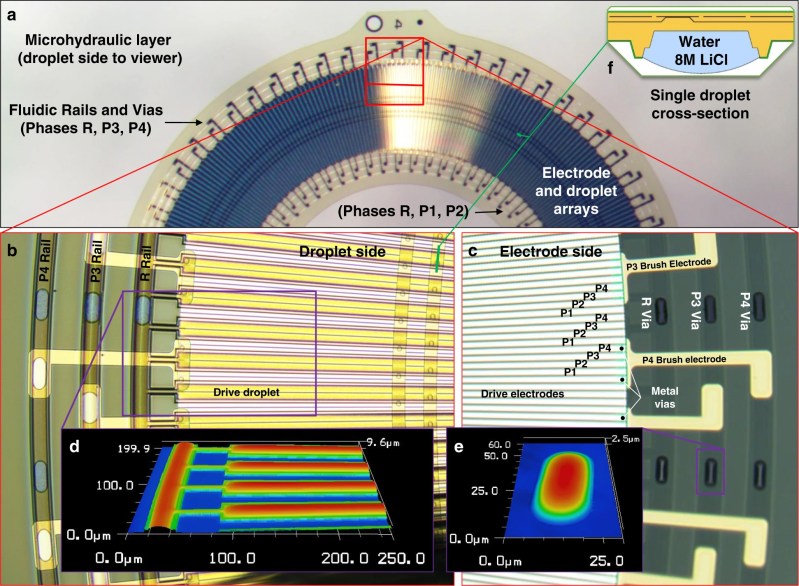
There’s a way to get around these limitations, and it’s outlined in a published in Nature. As the research outlines, there are already known ways to improve the performance of electrostatic motors. The paper cites low voltage operation, high torque, high efficiency, and the ability to scale up in thickness as desirable attributes; the latter in particular in reference to very thin MEMS motor designs. Low voltage operation can be achieved through the use of thin dielectric material in the electrostatic motor, while higher torque can be achieved by creating a motor with a very small stepping distance. Scaling in thickness is possible too, by using a layered motor design, and efficiency improvements are achievable by choosing a dielectric material with very low losses. The interesting thing this paper points out is that while these attributes have all been noted and explored individually, they haven’t been combined and leveraged in a single motor design.
The motors are a more advanced version of “electrowetting” actuators. These work by manipulating the surface tension of liquid droplets using an electric field—referred to as the electrowetting effect. That’s why they fall into the class of electrostatic motors. Basically, by creating electric fields with various electrodes, the droplets “wettability” on a surface can be affected, which can be exploited with multiple electrodes to move droplets around. The actuators themselves have droplets placed between surfaces with hydrophilic and hydrophobic regions, which attract and repel the droplets themselves. Thus, by moving the droplets in controlled fashion, the droplets can drag the surfaces around as they move, creating motion.
The magic is when you get more advanced and stack these things—hence, multilayer microhydraulic actuators. By stacking multiple layers, these actuators can offer high torque for their size without requiring high operating voltages, and they can move incredibly precisely. These actuators also achieve impressive power density, and their relative performance improves as they scale down to smaller sizes, too.
The structure is the key. Each polyimide layer of the actuator consists of an electrode array on one side and a droplet array on the other, and measures just 10 um thick. Individual layers are separated by fluid—droplets of water. Radially oriented droplets are distorted by the electrodes, which are covered in dielectric, and this drives the motion of the actuator. When an electric field is applied on one layer, they attract the droplets on a layer above, and as the droplets move, the drag the layer along. It’s not dissimilar to Franklin’s design from centuries ago, it’s just being done with different components on a different scale—and with many layers of droplets and electrode arrays stacked up for improved performance.
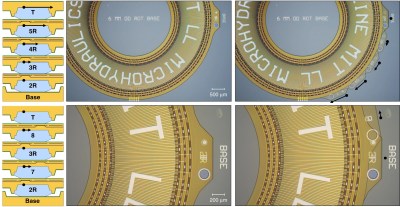
The layers can be configured to optimize for either speed or force, making the technology highly adaptable depending on the application. For instance, a five-layer actuator in “speed mode” could move each higher layer at a relative velocity to the one below it, with the effect stacking so the top layer is moving much faster than the bottom. Alternatively, when configured for force, each layer moves in the opposite direction relative to the one below it, significantly increasing the available force while maintaining a compact form factor. Alternatively, the same principles can be applied to create a linear actuator, too.
Multilayer microhydraulic actuators could be a game-changer for robotics, especially at small scales where conventional inductive motors fall short. The actuators’ ability to deliver high torque with precise control makes them ideal for use in micro-robotic systems, including robotic surgery, where dexterity, fine movement, and force are all vital.
Additionally, because these actuators don’t require external gearing to change their speed or force characteristics, they can be more compact and flexible for some applications than their inductive counterparts. This could open up new possibilities for responsive robotic joints, providing new levels of performance and finesse in fields like prosthetics.
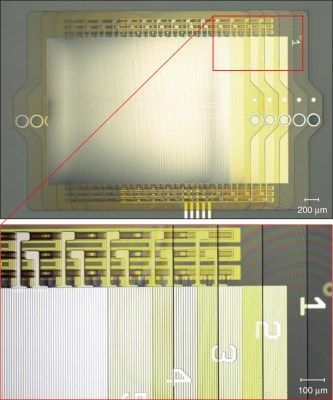
One of the most exciting aspects of this technology is how it scales. These multilayer microhydraulic actuators improve as they get smaller. Reducing the droplet pitch from 40 µm to 15 µm increases torque and power density by an order of magnitude, making these actuators a promising solution for future micro-scale applications. Basically, the smaller they go, the better they get.
While the potential is vast, the technology does face some challenges. The fluidic nature of the actuators introduces the need for precision fabrication to prevent issues like evaporation and contamination. Moreover, particles as small as 10 µm can affect performance, requiring careful handling and assembly in clean environments. These aren’t rough and tumble rugged motors—they’re precise and delicate machines. Neither are these particularly useful at large scales—don’t expect to see this technology running your drones or EV. That’s not really what it’s about. It’s more of a small scale thing.
Oh by the way they have insane acceleration. Full speed after the first step.
This is realtime! Cmonnnnn pic.twitter.com/s607zPOwEN
— Nick Parker (@NickParkerPrint) October 6, 2024
These actuators are being used in chip assembly work.
Multilayer microhydraulic actuators represent a significant leap forward in actuation technology, offering high torque, precision, and efficiency at low voltages. Their unique ability to scale down without losing performance makes them an attractive option for applications ranging from robotics to medical devices. As researchers continue to refine this technology, we may soon see these actuators powering the robots and machines of tomorrow.
I, for one, welcome our new microrobotic overlords!
Now you have me thinking about future nanobot wars (I just recently finished the Hugh Howey Silo books).
I wonder how this compares to “USM” piezoelectric motors?
Nitinol motor.
https://www.youtube.com/shorts/jvRpNFBM0Tg
I’m disappointed that he felt he needed to justify the need for this technology in chip stacking based on AI demand as opposed to any other chip-building requirements.
It’s not surprising. Whenever you are selling an idea, you will statistically be successful by associating it something else that is receiving large investments.
I promise a purpose for this bit of pedantry: published not in Nature but in Microsystems&Nanoengineering, a “Nature research journal”.
The purpose:
Hey y’all! This is the crowd to cheer for the people behind Microsystems&Nanoengineering making their journal all open access all the time. That was a bit of swimming upstream for the benefit of non-affiliated plebs like (most of) us. Yay M&N!
I promise a purpose for this bit of pedantry: published not in Nature but in Microsystems&Nanoengineering, a “Nature research journal”.
The purpose:
Hey y’all! This is the crowd to cheer for the people behind Microsystems&Nanoengineering making their journal all open access all the time. That was a bit of swimming upstream for the benefit of non-affiliated plebs like (most of) us. Yay M&N!