Since the construction of the first commercial light water nuclear power plants (LWR) the design of their fuel rods hasn’t changed significantly. Mechanically robust and corrosion-resistant zirconium alloy (zircalloy) tubes are filled with ceramic fuel pellets, which get assembled into fuel assemblies for loading into the reactor.
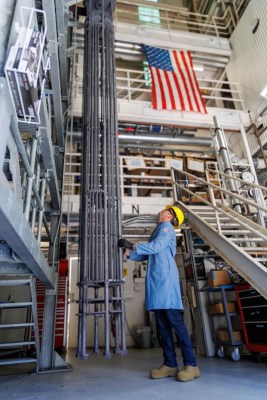
Now it seems that silicon carbide (SiC) may soon replace the traditional zirconium alloy with General Atomics’ SiGa fuel cladding, which has been tested over the past 120 days in the Advanced Test Reactor at Idaho National Laboratory (INL). This completes the first of a series of tests before SiGa is approved for commercial use.
One of the main advantages of SiC over zircalloy is better resistance to high temperatures — during testing with temperatures well above those experienced with normal operating conditions, the zircalloy rods would burst while the SiC ones remained intact (as in the embedded video). Although normally SiC is quite brittle and unsuitable for such structures, SiGa uses a SiC fiber composite, which allows it to be used in this structural fashion.
Although this development is primarily part of the Department of Energy’s Accident Tolerant Fuel Program and its focus on melt-down proof fuel, the switch to SiC could also solve a major issue with zirconium, being its use as a catalyst with hydrogen formation when exposed to steam. Although with e.g. Fukushima Daiichi’s triple meltdown the zircalloy fuel rods were partially destroyed, it was the formation of hydrogen gas inside the reactor vessels and the hydrogen explosions during venting which worsened what should have been a simple meltdown into something significantly worse.
In other news: I may replace Tylor Swift as the highest grossing musical tour.
Le Lepetomane reborn!
May is a weasel word, like could etc.
Anything that comes after is speculation.
May the force be with you.
May you live long and prosper.
Mayday!
Mayday!
Why that’s the Russian new year! We’ll have a big parade and serve hot hors d’oeuvres…
Horse ovaries?
Is that something like rocky mountain oysters?
I’d like to know what binder is used in the composite. In epoxy-binder composites, the epoxy is generally the limiting factor when it comes to heat resistance. Obviously the binder in the SiC composite handles the high temperatures.
It’s most likely a SiC matrix composite with a woven SiC fiber filler.
“a SiC/SiC composite is made by having a SiC (silicon carbide) matrix phase and a fiber phase incorporated together by different processing methods”
See: https://en.m.wikipedia.org/wiki/SiC%E2%80%93SiC_matrix_composite#Processing
under the wikipedia link, Chemical Vapor Infiltration (CVI), Polymer Impregnation and Pyrolysis (PIP) and Melt Infiltration (MI) are mentioned.
Through all processes, a mostly-SiC matrix is produced, but its porosity, crystallinity / microstructure and stoichiometry will differ depending on the synthesis method.
“Binder” in this context usually refers to an additive that is subsequently converted or removed from the part before sintering / matrix formation reactions take place.
Addendum: they say it explicitly:
“GA’s engineered ATF rod cladding is a multi-layered composite design composed of SiC fiber in a SiC matrix”
Explanation and better fabrication pictures including cross section of the finished product:
https://www.ga.com/nuclear-fission/accident-tolerant-fuel
“simple meltdown” – I think this wording significantly downplays the consequences of a melted core. It is anything but simple.
Yes, if there were no hydrogen gas explosions in Fukushima Daiichi, the accident would have been much less severe.
But a melted core still means that the whole plant has to be cooled down, decontaminated, torn apart and disposed of over a timeframe of decades.
I got the impression that Hackaday recently began to regularly report about nuclear fission tech like it is something cool and has a bright future. I think when you look at the costs of building new, running and disposing reactors and compare them to a mix of solar, wind and grid storage (with batteries or else), fission isn’t able to compete. And on top come the risks of accidents and long-term disposal of spent fuel.
Solar, wind and grid storage is so cheap, fast and easy that even with the might of the whole worlds research and development, involving more money and people several times the Manhattan and Apollo programs, not a single country or even caribbean island with the best possibilities, has been able to eliminate coal and gas with renewables.
Nuclear did it 45 years ago for several countries, big industrial nations and small ones, with an still unbeaten record in built times, with statistically proven the most safe electrical production and waste management, while being the most cost effective with least natural resources needed due to its high energy density and long life time.
+1
Wind/solar are niche technologies best suited for places you can’t/don’t want to be connected to the grid.
Nuclear power is not and never has been remotely economic. We have it is because countries cross subsidise nuclear power from nuclear weapon programs. Now we have developed a nuclear industry is still expensive even with the sunk cost of development already done. We need a new approach, not just a spin-off from weapons programs, but that is going to be difficult to fund if it doesnt make bombs.
“not a single country or even caribbean island with the best possibilities, has been able to eliminate coal and gas with renewables.”
First page of google results to find multiple places that claim to be running off 100% renewables. Kodiak Island in the US is one example and they claim the cost of their energy has fallen thanks to it.
Even if that were not the case I’d be willing to bet that in the 10 years it would take for a new NPP to be built you won’t be able to make such statements without a torrent of ‘um actually’s coming your way.
Thing is – those numbers have already been run.
And it’s wind/solar that can’t compete.
Maybe if you use overoptimistic price calculations done by fission plant manufacturers.
But better take a look at for example Hinkley Point C, Flamanville 3 or Olkiluoto 3 how the actual costs and time to build look like and can run off the rails.
grid storage is still basically a wish list item, compared to the scale that will be needed if solar becomes a major fraction. my understanding is that the only reason it’s working as well as it is today is that there’s a lot of throttle-able fossil fuel capacity (‘gas turbine’) that comes on at night. and all of these things are enormously expensive, edging eachother out on occasion but all requiring big investments of finite resources…land, materials, maintenance, war. and they all pollute and destroy in their own unique ways too.
i wouldn’t put all my eggs in the nuclear basket any more than i’d put all my eggs in the solar basket.
one of the problems with nuclear is that its risks are often overstated in media and in the popular imagination. especially when compared to other technologies. so a lot of coverage of nuclear power is intentionally trying to confront that problem, to spin it in a more positive way than coal and gas.
another problem is that a lot of severe real known problems, such as “zircalloy+steam=hydrogen explosion”, have simply been accepted because testing new technologies is difficult and expensive and runs into regulatory headwinds. so i’m glad to see this research, and i’m cautiously optimistic that eventually a better fuel module will win the day
This may work for new reactor designs but it will change the way the core of existing reactors work. Carbon is a neutron moderator do each reactor eill have to be recertified to run this fuel.
General Atomics: “these new fuel rods have the potential to greatly improve the safety and economics of current and advanced nuclear reactors.” (https://www.ga.com/nuclear-fission/accident-tolerant-fuel)
‘Current’ sounds to me like they aim for it to be a drop-in replacement, unless they mean “current designs”, excluding the fleet of older generation reactors currently in operation.
As far as SiC is concerned – it’s a reasonably thin walled tube (vs. graphite moderator blocks which add several cm of plain graphite), SiC has 50 at% carbon and it displaces water that itself functions as a moderator.
We can both agree though that even if it’s a 1:1 replacement for Zr claddings, a substantial amount of paperwork will have to be produced before ATF is fielded.
It might be slotted into CANDU reactors fairly easily.
Nuclear issues. :(
The History of Uranium Mining and the Navajo People.
On April 29, 2005, Navajo Nation President Joe Shirley Jr. signed the Diné Natural Resources Protection Act of 2005 that outlaws uranium mining and processing on Navajo Nation lands.
NEW MEXICO (KRQE) – A federal agency said seven more abandoned uranium mines will be cleaned up on Navajo land in New Mexico. The EPA said it will target the sites near Smith Lake and Mariano Lake which are both east of Gallup. Once this project is complete around 260 acres of land will be restored.Oct 9, 2024. ”
Ten years after use, the surface of a spent fuel assembly releases 10,000 rem/hr of radiation, far greater than the fatal whole-body dose for humans of 500 rem received all at once.”
“how many gallons of water used to produce 1 kwh in a data center?.
2 gallons”
Ok, they irradiated this fuel for 120 days. Now they have to put several full size rods into an operating reactor and operate them at the design-rated power levels, to the design rated burnup level, which will take only about 6 years, if everything goes right.
Then they can take them out of the reactor and let them cool down (physically and radiologically), in the spent fuel pool, for a few years. Then they get to be transferred to a facility that has a hot cell that can unload a cask containing 12 ft fuel rods. There are very few of those facilities in the world. And to transfer them they have to get permission from a lot of different government entities, which exposes this project to outside intervenors who do not want it to succeed, because they hate everything nuclear, with a passion.
The examination process in the hot cell will take several years, after which the results get presented to the NRC for approval. The NRC approval process can easily take over 2 more years.
All in all, only about 10 years till it might be able to be used as real fuel.
And this schedule does not include the development and approval of new analytical methods and models to predict the performance of the fuel during normal operation, transients, and accidents, which is extremely non-trivial.
Given the relevance for both fission and fusion reactor designs and a substantial body of research on the subject, it shouldn’t take that long. One would also think that samples are processed in high neutron flux research reactors to accumulate neutron damage faster, not in reactors under regular operation – but I’d need to find the time to read the papers linked below.
https://en.wikipedia.org/wiki/High_Flux_Isotope_Reactor
“Neutronic Analysis of SiC/SiC Sandwich Cladding Design in APR-1400 under Normal Operation Conditions”
https://www.mdpi.com/1996-1073/15/14/5204
“Mechanical and thermal properties of SiCf/SiC composites irradiated with neutrons at high temperatures”
https://doi.org/10.1016/j.fusengdes.2005.06.307
You cannot just put a sample of the material into a research reactor and irradiate it, and decide that the material is suitable. Irradiation is only one part of a qualification program that looks at all sorts of metallurgical, chemical, mechanic, hydrodynamic, and thermal phenomena. And all of the models that are used need to be justified with actual testing, at full scale, in an operating reactor.
As the fuel is burned up, it expands, because fission creates 2 atoms where there once was only one, and those 2 atoms take up more space than did the one atom inside the cladding. The cladding design has to take this expansion into consideration as it exerts pressure on the cladding, and it takes about 6 years of actual operation in a real reactor to burn up enough of the uranium to see the real effects of this phenomenon.
Similarly, heat-up and cooldown cycles stress both the cladding and the fuel pellets, and you need to validate the models for the interaction of the pellets and the cladding over the entire life of the fuel. You cannot do that in 120 days.
And then there are the chemical interactions of the cladding with other structural materials in the fuel bundle, with the coolant, and with the fission products themselves, which change their chemical composition as the fuel is burned and FPs are released from the fuel pellets into the cladding plenum and throughout the rod. The FPs decay into different elements over the life of the fuel, with different compositions along the length of the rod.
This is all very complicated. The goal is to prevent the cladding from being damaged thoughout its entire lifetime, not just during accidents. Small leaks during operation are a major headache for operators and maintenance, and utilities like to stop them quickly.
I will give you some other interesting numbers about fuel failures and new fuel designs. The design standards for pebble bed fuel about 25 years ago was a “failure” rate of less that 1×10-5 per year, for each of the balls inserted into a core. Failure is defined as the release of fission products from one ball. Many balls are loaded into a pebble bed reactor, and they are recirculated. Balls are removed at the bottom of the core, inspected to see if they have failed, and then returned to the top of the core.
If you look at the existing light water reactors, for which one fuel pin is about equivalent to one of the pebble balls, the failure rates 25 years ago were somewhere between 1×10-5 and 1×10-6 per year. The goal for the fuel vendors was ZERO failures, because if they detected a failure during normal operation, they could identify the location of the failed pin from the radiochemistry, and adjust control rod positions to suppress the power in the region where the failed pin was thought to be. If the suppression worked, and reduced the leak, then they could continue to operate till the next planned shutdown. If not, they would voluntarily shutdown and remove the failed bundle/pin, in order to avoid contamination the reactor system. Most LWR reactors currently operating do not experience any leakers at all, during normal operation. This is one of the reasons why the NRC requires thorough testing of fuel at design rated power, at design rated temperatures, for design rated burnup, in a real reactor, before a new design can be approved.
If the owners of the pebble bed reactor detect a leaking pebble, they MIGHT be able to figure out where inside the reactor it is currently located. I don’t know how well they would be able to adjust the control rods to suppressed a leaker, but since the pebbles are constantly moving as they are withdrawn at the bottom, it would be a challenge to keep up with a leaker.
And, the Germans instrumented a lot of the pebbles they made for their prototype reactor, to see what kinds of burnups and temperatures they experienced. With melt wires for temperature. Their inspection of the pebbles that came out indicated that some of the pebbles experienced temperatures much higher than predicted. I don’t remember the failure rates for these pebbles, but time and temperature are usually the factors that influence failure most. Before they shut down the reactor permanently, there was some balls that were instrumented that had NEVER BEEN RECIRCULATED, even though this was not predicted. They stayed inside the reactor the entire time it was operated.
So, it they decide to remove a leaker pebble, they have to offload the entire core to ensure that they find it. This is a non-trivial evolution.
The manufacturer claims “Provides hermetic sealing with strength retention
at high temperature and neutron fluence” (https://www.ga.com/images/products/energy/pdf/SiGA-SiC-Data-2301_0518.pdf) and I think one should bite into that first – preferably without resorting to nagging Mr. Faibish or dragging in pebble fuel that gets mechanically abused during normal operation. So what about failure cases?
One thing I find puzzling is that these seem to be bare SiC tubes, while elsewhere Nb / Ta liners within the SiC composite tubes are investigated, which would not be strictly necessary if the SiC tubes guaranteed hermeticity. (“Blast and tensile properties of tantalum/niobium lined SiC/SiC composite tubes for nuclear cladding”, https://doi.org/10.1016/s1003-6326%2822%2965922-3)
In “Failure behavior of SiC/SiC composite tubes under strain rates similar to the pellet-cladding mechanical interaction phase of reactivity-initiated accidents” (from 2018, https://doi.org/10.1016/j.jnucmat.2018.11.023), a few more details on initial gap, tolerances and tensile strain in the failure case are elaborated:
“We recognize the fact that SiC/SiC cladding will not creep-down to the fuel like zirconium-based cladding does. Therefore, the likelihood of initial pellet-cladding contact before an RIA event will be small. However, the objective of this work is to determine what the failure behavior of the cladding might be if such contact does exist”.
See “4.2. Nuclear reactor safety perspective”: “While the SiC/SiC composite is deforming, matrix cracking (microcracking) begins to occur at the concentrated stress regions in the vicinity of matrix pores. This microcracking may lead to loss-of-hermeticity and the release of fission products.. Coatings on the SiC/SiC cladding will also potentially affect hermeticity.”
The authors conclude, “The appearance of failure after the simulated
PCMI tests in this study indicates that coolable geometry might be maintained. However, this behavior should also be investigated by in-pile transient tests of fuel rodlets with SiC/SiC composite cladding.”
Progress has certainly be made since, and I think it’s unlikely that the final product will rely exclusively on the hermeticity of a composite tube.