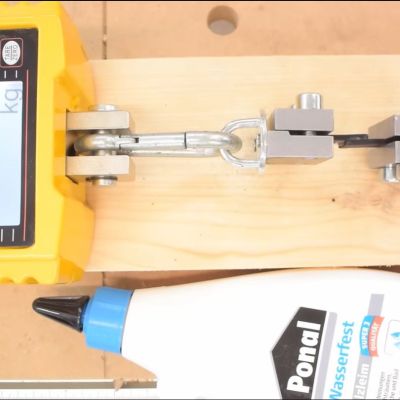
PETG is a pretty great material to print 3D models with, but one issue with it is that gluing it can be a bit of a pain. In a recent video by [Cosel] (German language, with English auto-dub) he notes that he found that with many adhesives the adhesion between PETG parts would tend to fail over time, so he set out to do a large test with just about any adhesive he could get his hands on. This included everything from epoxy to wood glue and various adhesives for plastics
TL;DR: Some superglues seem to weaken PETG, and a construction polyurethane glue is the absolute winner.
For the test, two flat surfaces were printed in PETG for each test, glued together and allowed to fully dry over multiple days. After about a week each sample was put into a rig that tried to pull the two surfaces apart while measuring the force required to do so.
With e.g. two-part epoxy and super glue the parts would break rather than the glue layer, while with others the glue layer would give way first. All of these results are noted in the above graphic that has the force listed in Newton. The special notes and symbols stand for strong smell (‘Geruch’), the PETG itself breaking (‘Substrat gebrochen’) and high variability (‘hohe Streuung’) between the multiple samples tested per adhesive.
Interesting is that multiple superglues (‘Sekundenkleber’) show different results, while MMA (Methyl Methacrylate) and similar score the highest. The Bostik P580 is a polyurethane construction adhesive, usually used for gluing just about anything to anything in interior and exterior applications, so perhaps its high score isn’t so surprising. Trailing at the end are the wood glue in last place, with the UHU general adhesive also scoring rather poorly.
Clearly there are many options for gluing PETG parts, but some are definitely more sturdy than others.
Thanks to [Risu no Kairu] for the tip.
I do a lot of 3D printing using PETG, so this is very helpful. Many thanks for quality citizen science!
I’ve heard some people use flame or plasma to activate surface energy of PETG to bond more readily with glue and paint. Haven’t tried yet.
I have used a product called TAP Polyweld, which is for gluing HDPE together. The secret is in the surface prep, you need to flame both surfaces. It actually works great, I need some right now and I think I have enough left, but I was looking for it online and it has been discontinued, with no explanation. I can’t find any adhesive anywhere that mentions polyethylene on the label, nor anything that mentions the flame treatment.
Does anyone know what happened? It just says discontinued and there’s no warning to discard any you may have. Or is there hopefully some new formula that makes it easy?
I’ve found instruction manual for TAP Polyweld, it actualy has quite useful description of the process.
https://www.tapplastics.com/image/pdf/Prod_Data-_Poly-Weld.pdf
Clean and roughen all bonding surfaces.
Polyethylene must be flame treated to ensure a strong bond.
• Fit a propane torch with a flame spreader.
• Following the operating cautions of the propane torch, ignite the flame.
• Observe the flame in a darkened room, noting the primary (bright blue) and secondary (faint yellow) portions of the
flame. (See drawing below)
• Adjust the flame so that the primary flame is contained within the spreader, and the secondary flame is 1-1/2” beyond
the spreader. (see drawing)
• Treat the polyethylene to be bonded with the tip of the secondary flame by passing it over the polyethylene in 5 gentle
strokes. Total exposure to the flame should be 2-3 seconds (.5 seconds per stroke). This light exposure should not
deform or melt the polyethylene in any way.
• Test the polyethylene for bond readiness by wetting it with water. If the water beads up and runs off immediately, the
treatment was not effective. If the water sheets on the surface, the surface is ready for bonding. If unsure, compare
water’s action on the treated area with an untreated area.
• Bond joints within 1 hour after treating. Always prepare test bonds to be certain that flame treating is effective with
your material.
Search for “low surface energy adhesive” or “polyethylene adhesive” to find more products. 3M DP8005, SCIGRIP SG400, and Permabond TA4605 came up for me. None of them can be considered inexpensive.
I dont like to use glue at all. I prefer to bond parts with plastic welding instead. Depending on the part I either use a modified soldering iron, an ultrasonic cutter, or a 3d printing pen. I get that glue is easier, but if you dont mind surface finishing work, welding really gives a superior result. YMMV
this is probably the better idea, pvc pipe welding solvent is the one I think?
Thats chemical welding. While that works, if you choose the right solvent for the plastic youre working with, I dont love handling solvents.
Thermal bonding just makes the most sense to me when dealing with fdm parts.
Haha, before even opening the article I thought to myself “I bet UHU is at the bottom of the list”
What a suprise….
I genuinely don’t understand how they are still in business
Stores stock it because people buy it, and people buy it because stores stock it.
Bit unfair, use the right glue for the job and you’ll get good results, UHU make a large range of different adhesives, glues etc for all sorts of different materials.
Revell Contacta Liquid (don’t know about Professional) smells like it contains a lot of acetone, so it will probably chemically weld ABS.
PVA glue is missing from that list.
I believe Ponal Wasserfest is a PVA glue.
yes, also the Uhu Alleskleber is a PVA in Acetone
For plastic bonding my first stop is usually the Loctite Design Guide for Bonding Plastic. Loctite products only obviously, but very useful for deciding what to use on plastics/rubbers. Looks like loctite 401 wins in most cases for PET at least (no PETG on the list).
ChatGPT seems to agree with you. It tells me that Loctite 401 is superior to BOSTIK P580 for bonding to PETG.
The study above by Cosel is flawed anyway. Some of the tests bend the samples enough that he’s not purely testing shear strength anymore like he is in the other samples.
In my opinion, testing shear strength is a poor substitute for testing adhesion anyway since much of the time that we would want to glue 3D portions together they would be in tension instead of shear … unless of course the equivalent of holes and dowels was included in the print.
The description of BOSTIK P580 on the website also says that it gains a bit of volume during curing because it produces CO2. I think that’s a no-go for many applications with 3D prints.
It would have been nice to see how JB Weld compares to the others. It’s fairly cheap at two large electronics suppliers here in Germany.
Methylene chloride is unbeatable, direct solvent weld. Never had a break in service, only smash/vise breaks which never break at the joint.
Make 2 coplanar surfaces, mate them (a dot of super glue can pin) and then let the methylene chloride capillary into the gap.
Always ventilate outdoors or directly under bathroom fan for 24 hrs, always.
I also use dichloromethane and find it excellent. It is incredibly useful for bonding pla as well.
I have used weld-on #1, #4, or #16, as they all contain Dichloromethane. Works very well to solvent weld PETG to itself, ABS, acrylic, PC… I assume HIPS would also be soluble.
Um.. isn’t the plastic supposed to break at roughly the same load, regardless of the glue used?
I mean – if the glue held longer than the plastic, then we are no longer measuring the bonding force of the glue. Having a large variation in outcomes marked * (“Substrat gebrochen”) would indicate that either there is something wrong with the testing methodology, or the glue is influencing the strength of the plastic itself (less likely IMHO).
Solvent glues can affect the strength of plastics and you have to be careful how you prep the surfaces too, some common solvents will leave polycarbonate extremely brittle for example
the test is fundamentaly flawed, because the crossection of the test sample and glue surface is greater than the substrate – that is why in material testing “dogbone”-samples are used, where the test area has the least crossection ;)
You can solvent weld PETG prints using ethyl acetate. Home Depot sells it as “MEK substitute”.
I believe it also works on ABS and maybe even PLA (for those of you who still use it).
It’s about as viscous as water, so it tends not to stay where you put it.
haven’t tried it with PETG, but i used to use PVC pipe cleaner for solvent welding PLA. that stuff is i guess a real bucket of random noxious solvents, and there’s always a jar around somewhere.
when i was experimenting at my workbench i was very impressed with the results…but when i actually used the parts, over time every one ultimately broke. not sure why. probably a problem with my process. not sure if i’ll try again with PETG
i just googled this exact question. i have a PETG part and i want to trap an axle in a hole in it (axle is a bit of 12 gauge copper wire). and i came up with the same recommendations for epoxy and CA. epoxy is too much mess and waiting imo, and it needed to fill a little gap so i ruled out CA (though i suspect the CA+baking soda hack would have done me alright, with only a little risk of accidentally gluing the moving part).
so, like mentioned above by other commenters, i went with a kind of plastic welding. i did “G0 Z100\nG0 E10 F100\n” on my printer, and rubbed my part on the bottom of the hot end as it dribbled out. works great. looks bad. PETG sands alright though.
You can use a soldering iron rather than the hotend, if you’d like. In fact, if you grab some filament you can add it in very much like oxyacetylene or tig welding, lay down a nice fat melted-in bead that sticks up above the surface, then sand it flat and get a good solid weld without all the ugly. Even a sharp chisel will pare PLA or PETG welded joints pretty flat.
Hot air gun? Should be easy to get it up to melt temperature.
Whether you melt the rest of the print or not is left as an exercise for the reader…
My best solution for glueing PETG with PETG is Dichloromethane (DCM, methylene bichloride, CH_2Cl_2).
It is a bit hard to source and requires personal health and safety equipment, but it works for PETG like Acetone works for ABS. Apply, let soak in, repeat, press parts together, wait, one piece.
Most five-minute epoxies are not all that great. A thirty-minute epoxy would have been a better choice, it’s greatly superior as there is enough to work into the nooks and crannies. Although I don’t do 3DP, I use epoxy by the gallon when building high-power rockets, and I avoid any that has a pot life of less than about 20 minutes. (Most of the rocketry guys do the same.)