Delrin, Acetal, and its many trade names is a material properly known as Polyoxymethylene or POM. It is one of the strongest plastics and is a good go-to material when you want the best properties of plastic, and don’t need the full strength of a metal part. It was originally formulated to compete with Zinc and Aluminum castings after all.
I won’t go too deep into the numbers behind POM. If you need the Young’s Modulus, you probably don’t need this guide. This is intended to be more of a guide to its general properties. When you’re looking for something to fit an application it is usually easier to shift through the surface properties to select a few candidates, and then break the calculator out later to make sure it will work if you’re uncertain about the factor of safety.
The most popular property of POM is its ease of machining. While doing this research every single site I came across referred to it as the most machinable plastic. That’s about as objective as subjective praise can get. It doesn’t tend to grab tools like, for example, HDPE. It also chips nicely unlike UHMW and Nylon. Some plastics, like UHMW, have the unfortunate tendency to render the dials on a mill or lathe meaningless as the plastic deflects away from the tool. POM does not do this as much. Of course these other plastics have their strengths as well, but if any plastic will do, and you’re machining, POM is a very good choice.
POM in many ways behaves like brass than compared to other plastics. It’s naturally stronger and stiffer than other plastics. It has low thermal expansion. It doesn’t absorb a lot of water, and therefore stays dimensionally stable better than Nylon. POM is also very hard and abrasion resistant. It doesn’t suffer from as much creep; which is the tendency for a material to stay bent if left under a stress for too long. You could make a plastic spring or compliant mechanism and expect a useful service life, as long as the mechanism rests in the sprung state.
Surprisingly, Delrin != Acetal
I once got in an argument with someone about whether or not Delrin and Acetal were the same material. I thought they were the same, I ended up being quite wrong. Acetal refers to the pattern and shape of the molecule that makes up its building blocks. Delrin, is an acetal homopolymer unless otherwise specified by Dupont. When you buy acetal without a trade name attached, you are usually purchasing acetal copolymer. These are the two most common names for POM, but there are other formulations out there under different branding and it will take some research to figure out what you are buying.
There is a mechanical difference between homopolymer (Delrin) and copolymer (Acetal). Delrin has a higher melting point, is a little stronger, and has a few other slightly more initially desirable properties. The homopolymer is less uniform throughout its cross section. In thicker sheets, blocks, or rods of homopolymer, there will be little bubbles causing a less dense area which formed as part of the manufacturing process in the center. If you are machining a small hole through the center of an extruded rod of POM, the copolymer may be a better choice in this case. The name brand is usually more expensive. The copolymer is a little more elastic as well, but if you’re pushing the plastic hard enough to see this difference it may not be a good fit. It is possible that the copolymer will have better stability over a longer service life. Unless you are doing fancy stuff, just buy the cheapest, over engineer it, and it probably won’t matter which one you choose.
Impervious to Common Solvents
POM is resistant to chemicals. It is generally unaffected by solvents, fuels, etc. I couldn’t find a common lubricant that would damage it. Here’s a really big and immensely useful list of things that will damage it (and some other plastics). For example, chlorine is pretty bad for it. It has stabilizers to help, but it isn’t impervious. So if you’re testing your underwater ROV in a heavily chlorinated pool; your POM propeller may suffer a failure after enough exposure. It has an excellent resistance to beer, for what that’s worth.
One huge advantage to POM is its high lubricity. POM is often mistakenly said to have self-lubricating properties. However, it simply has a high abrasion resistance and a very low coefficient of friction, making it appear to be self lubricating. POM can benefit from correctly chosen lubricant. Properly lubricating a load bearing POM part will lengthen its service life. A dry lubricant like Moly or Graphite will work. Also a Teflon based grease such as Super Lube is a good choice. You can also purchase it with exotic fillers like Teflon or Moly, in which case it will be self-lubricating for a much higher price.
My preferred place for purchasing POM is auction sites like eBay. The prices are usually better if you’re willing to give up on guaranteed accurate tolerances and formulations. However, if I want to be sure about getting brand name plastic or a specific formulation I’ll buy from a distributor to be sure of getting the material I’m asking for.
Keep Away from Flame
One big downside to POM is flammability. POM is not-self extinguishing. So once it starts burning it will continue to do so until oxygen is taken away from it. The flame can be colorless and with little smoke. A simple Class A extinguisher will put it out. If your application could get uncomfortably on fire, choose a self extinguishing plastic like PVC or ABS with a UL rated flame retardant for your application range mixed in (making it self-extinguishing). Even though POM is a good dielectric, it is probably not a good choice for a lot of sparky electrical applications.
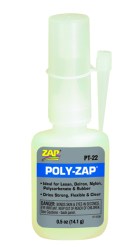
Another downside is a result of its upside. Due to its solvent resistance and high lubricity you can pretty much give up on adhering anything to it. Glue, Paint, Stickers, etc. All of them will have a hard time sticking to POM. There are some glues that claim to adhere to POM, such as Zap Poly-Zap. Even with these special glues it is recommended to sand both surfaces before gluing and to expect a weak bond. A silicone based adhesive has also been mentioned to have similar success to specially formulated CA. If you break your POM part or want to do a two part assembly it’s just not possible
If you need POM in a color other than black and natural, it has been reported to dye well. Just like with nylon, any regular technique for dying should work and give a good, if subdued, color. However, if you are building something that is rated for an engineering application it’s good to call the material supplier to see if they have a color solution. Some dyes may have adverse effects over time on the performance of the plastic.
I’ve used POM in projects and always found it to be a dream to work with. It’s one of my favorite materials. When I’m in doubt and need to try out an idea I like to reach for it, and it’s cheap enough to keep a small stock. If you have useful information, an error to point out, or anecdotes to add please do so. I’m excited to learn more.
Featured Photo By Pierre, CC
Good write-up of an interesting material
As an injection molding technician for the past 15 years, I have used Delrin, POM, Acetal Copolymer, Acetal Homopolymer, Celcon, etc. quite extensively. I’m sure everyone here has different applications for these materials than I do, so I’m not going to debate semantics of name-brands and molecular differences. However, there are a few things that should be known when using POM. First of all, it shrinks a lot. We take great care in the molding industry to cure POM properly to avoid the parts shrinking out of specification and very slight changes in ambient temperatures can change the shrink rate and alter the final product, so keep that in mind for size tolerance dependent parts.
Another thing to keep in mind is heat sensitivity and fire reaction. The article mentions a warning for flammability, and it is true. POM burns low and blue and its open flame can be nearly invisible. Aside from that, burning POM emits formaldehyde gas and it will burn your nose, throat and eyes as it degrades. You’ll definitely want to assure proper ventilation and do not overheat or expose to its melt temperature (around 200 C/ ~400 F) for long periods of time. A final warning, and this is VERY important. Never mix POM with TPEs or TPVs such as Santoprene or PVC. I’m not familiar with how much these materials are used in the hacking and hobby world, but it is very, very dangerous to mix POM with any of these plastics. I have personally seen POM and PVC with heat and pressure blow a 400 pound hopper off of a machine and hit the ceiling nearly 15 feet in the air. The Santoprene and POM mixture is not explosive, but inhaling the gas emitted is one of the worst things that you can do to your lungs, even in small amounts.
POM is a great material with a host of applications when used responsibly.
A good article. Along with Matt Norris’s input it’s one of the best things I’ve read on Hackaday for a while.
I second that, almost like the early days of the site.
Thanks for the info, interesting stuff! If you don’t mind, could you expand on the reactions between POM and PVC or Santoprene? The result of mixing the two sounds really interesting from a chemistry standpoint!
To be honest, I’m not 100% on the chemical reaction specifics, but I pretty sure that the explosion from PVC and POM is caused when the chloride gas produced by PVC makes the POM spontaneously degrade. The POM/PVC warning is day 1 stuff in the molding industry, especially in places that mold both resins under one roof.
As for the POM and Santoprene, I had never heard of that until this year. I found out first hand when one of our new setup guys didn’t purge the Santoprene out of a machine that was set up to run Acetal. Once that Acetal hit the screw and began to melt, it instantly choked me out and evacuated everyone in the area. It was more intense than anything I have ever experienced, so now I am sure to warn everyone I talk to about plastics.
That goes to show, even after 15 years in the plastics industry, I still learn new things every day. Now that plastic part making is accessible to everybody with an interest, I try to share as much knowledge as I can!
Acetal releases formaldehyde, PVC releases chlorine…the 2 cause an exothermic reaction when mixed, add heat and pressure (like in your normal injection press) and you get too much heat and pressure = boom…
Also, several carcinogenic compounds are created, the hazmat team is no joke.
Does Acetal have any chlorine in its make up?
Just to check – is the shrinkage issue specific to hot processing POM? I would expect that most of the hacking/hobby uses to be machining-based (Well, that or printing, but anyone who does much of that will be aware of just how big a deal shrinkage is already – good info for them), and I wouldn’t start out assuming that there’d be much shrinkage if it’s kept cool.
Yes. It is only molten processing. Machining POM should be no problem at all.
I agree, we use lots of delrin for assembly fixtures, particularly when adhesives are involved. It is purchased in rod or bar stock, so shrinkage was already accounted for.
We also do lots of injection molding, but we specifically avoid processing PVC.
I personally avoid PVC. I specifically ask in my interviews if the facility processes PVC. If they do, “Thanks but no thanks.” There are just too many health risks.
Did it rip a hole in the sheetrock?
No, but it did clean snap 4 m12 bolts and bend some steel plates and made an enormous mess of about 175 pounds of material
Wow, thanks for the great information! This is part of why I love writing for Hackaday so much; there are so many knowledgeable people around.
I used to work in an injection moulding factory 25 years ago and we hated running acetal. I don’t think it needs to be mixed with anything to be dangerous – it can explode all on its own given heat and time. When I was running acetal (Kemetal brand) I used to check the machines every 5 minutes to make sure the nozzles were not blocked – I too have seen a hopper blown off because the nozzle was blocked and nobody noticed for 20 minutes. And the smell of the smoke is absolutely choking.
“Never mix POM with TPEs or TPVs such as Santoprene or PVC.”
In an injection molding / melting context, I assume?
Santoprene TPV is a dynamically vulcanized alloy consisting mostly of fully cured EPDM rubber particles encapsulated in a polypropylene (PP) matrix. It’s basically EPDM rubber and PP plastic, which melt processes fairly easily as an elastomeric “plastic”.
When you mean mix, what do you mean? You mean mix under pressure and heat in an extrusion / injection molding situation? Never heard of any issues with Santoprene before at room temperature just in contact with PVC or Delrin and just wanted to learn more about what you are saying exactly. I own injection molding equipment but I am not a technician.
Yes, I’m speaking only in a molten state. Sorry for any confusion. There’s no problem with them coming in contact under normal room temperature situations. However, if you have designs on heating them at any time, you might as well do all that you can to keep them separate, though I don’t know how many average people would even have access to TPV/ TPE as it’s pricey and difficult to work with.
Interesting that the melting point of POM is 200 C. I’m fairly certain acetal is used as the structural component of several 3D printer nozzles. Obviously we print ABS and PLA with a temperature of 190 to 230 C, so does that mean our extruders are pushing the limits on the material? Is it possible also that the material shrinks over time from repeated heating?
In the early days people were thinking it could be a smart way to build a thermal barrier with delrin/acetal between the hot end and the filament drives. Usually there was some way to dissipate heat away with a heatsink, so the plastic would not be in direct contact with the heater, or else, the failure rates would have been even be higher. I think it was just a bad shortcut made back in the days. Most of the newer and better hotends are designed a bit smarter and have a full metal design. But there are still some designs that use a piece of teflon or similar plastic tube inside the metal to prevent the semi-molten plastic from sticking to the metal. I don’t think that the tube would shrink because of the repeated thermal cycles, but if it was used as stuctural part, it was squished together slowly between the heated nozzle and the drive unit, and thats why you could think the bore diameter was shrinking. I don’t think it’s that much of a problem if you just use it as a ‘glide bearing’ inside a metal tube, but of course it will tend to get dragged down slowly too if you pass a few kilometers of filament along the inner hole.
I think you may be referring to the jhead. http://reprap.org/wiki/J_Head_Nozzle It is made of PEEK with a PTFE (Teflon) liner. There may be others I don’t know about, but I’d be interested to learn of them if you have links:)
Very interesting and useful insights, thank you Matt!
Hi Matt, any idea as to to the type of filler(s) used in POM?
Is runflat insert on a defence vehicle uses delrin?
From the Celcon Design Guide: “When heated, PVC forms acidic decomposition products which can rapidly degrade Celcon acetal copolymer at processing temperatures, releasing large quantities of irritating formaldehyde gas. Celcon acetal copolymer and PVC should not be processed in the same equipment. If this is unavoidable, thorough purging with acrylic or polyethylene or disassembling and thoroughly cleaning the machine’s components is essential prior to the introduction of the second material.”
Using Delrin 100 NC for a worm gear system. Worm is steel and gear wheel is Delrin. Under load, the worm is digging into the teeth of the gear wheel and subsequently getting jammed. Per design, we allow 25% regrind. One customer recommended Delrin 111 instead of 100. The motor being used is approximately 12Nm. Any advice?
Note, the fire is a real risk with POM, do not underestimate it. We lost 2 laser cutters at Ultimaker due to POM fire and people walking away from the machine while it was operating.
^^^THIS 1000%
Any tips on laser cutting POM, other than to be careful? Fur instance, does air assist help?
Not exactly a laser tip but it waterjets quite nicely with no heat or burning.
That’s very interesting. I never leave my laser alone while it’s running on anything period anyway but never had Delrin catch fire on me. I use 1/8″ sheet for making embossing dies. I have noticed it absorbs alot of heat so I never try to cut it in one pass. If I’m cutting anything over 1/8″ I always do multiple cut passes at a higher speed to reduce heat build up and meltage deformity. I always have the air assist on and I have always gotten very good clean results on my projects.
Good article, but……
“POM in many ways behaves like brass than compared to other plastics.”
Lets try that again. I’m guessing you either meant “when compared to other plastics” or “behaves more like brass than other plastics”.
Great, great article! Please keep it up, I for one wish that more material suppliers would provide guides similar to this along with the technical data. Sometimes you’ll find decent app notes, but many times materials are presented as a sea of datasheets and idiotic marketing jargon with no clear description of what they are good for, what they aren’t good for, and how to design using the material. Just look at the Sabic website, it’s more or less useless.
I was just looking at Sabic today. Apparently that’s what the Saudis are doing with the oil money before it runs out. They bought Lexan(tm) from GE. Sigh.
Alex, take a look at the articles at the direct plastics site: http://www.directplastics.co.uk/popular-topics/ they’re short, readable introductions to many different plastics. Very similar to this article I think.
Nice, these actually are pretty good, thanks for the link.
Holy crap, need to re-iterate after I have read about 5 of the articles from this plastics distributor. These articles are excellent, thanks again for posting!
actually Delrin/Acetal are not good with even trace amounts of hydrochloric acid. If there is internal stress the acid will trigger the plastic to catastrophically fracture. under little to no loading you might not see any issues. but with high concentration of the chemical it can totally dissolve acetal or delrin. and the byproducts contain formaldehyde.
nylon doesn’t really like water either. you might see some slight swelling if you put them together. hot water? you might totally dissolve your part depending on exposure.
Nylon deals well with water, but only down to a certain pH, then things go south…
Nylon can be annealed in boiling water making it very tough (also you can mix fabric dye with the water and it will be taken up). We used to do this with nylon model airplane propellers and they were tough enough that you could run the engine and grind the tips off against concrete and the prop wouldn’t fracture.
I’ve subsequently done this to toughen up nylon parts that break a lot.
I have never heard of this. Do you just dip it for a while?
As others have stated, one of the better HaD articles in a long time. Plus the invaluable input from Matt Norris is icing on the cake.
Great job guys.
But, it’s not a hack!
B^)
But it facilitates hacking with this material. Good stuff
Very helpful thanks!
This sort of article should get priority because the knowledge is enabling and more content (projects) can flow from that.
This article is awesome, and Matt Norris’s input is also extremely valuable, particularly the potential safety issues with it both in the article and in Matt’s comment. Too much of the time, those issues get ignored in guides for newbies under the assumption that “everybody knows that stuff”.
Keep it up! This is great.
Great Stuff!! …but it ain’t cheap.
Did I mention, it ain’t cheap?!
Awesome.. Especially since most of those plastic cheap arse chopping boards available at supermarkets are made of the stuff; it’s easy to get too. :-) Some maybe delrin substitute, but, pretty good for chasis and the like :-)
hmmm I think they are actually HDPE. :-( meh.. sorry if i got your hopes up.
They are HDPE, Nylon, or most commonly, LDPE. I think they’re really just made of whatever regrind the injection molder has to get rid of that day. Also they are rarely as flat as they look. Still a pretty decent chunk of plastic for the price though:)
Great article Gerrit. Thanks to those posted sensible value added comments
I’m not overly impressed with laser cutting POM. On a 100W laser cutter it works reasonably well for material perhaps up to 3mm, But for material 10mm thick POM, even with multiple passes, the results were awful. With acrylic (which ablates) we could easily get a precision cut at 10mm with a single pass. The cutting action with POM, however, melts the material and retains too much heat, so as it tends to distort. So a sharp entrance cut resulted in a ragged edge and distorted geometry on the exit side.
Hi Nate. I laser alot of Delrin. Some things that help me out to avoid deformities in the Delrin is always have the air assist on. You also want to have a really good fume extraction system. I hooked up a 2 hp blower motor to the back of my laser so it’s almost like a vacuum inside. Another thing to consider is the focal length of your laser lens. If you’re cutting Delrin you definitely want to do multiple passes at a higher speed to avoid the heat build up and deformity but need to have a laser with a focal length of 2 inches or greater. NOT focal point, but focal length. Big difference. That kind of difference is what makes some companies advertise their laser systems as laser cutters or laser engravers. Laser lenses with long focal lengths make for better cutters but poor engravers. Vice versa is true for lenses with short focal lengths.
As someone who’s recently got a lathe & CNC micro-mill but has no real clue what I’m doing with them, this article pleases me greatly – proper quality content from HaD.
Does anyone have any information on the reactions between Delrin and Buna-N type rubber? Is there degradation of the delrin at the rubber contact points over time? my equipment uses a delrin female fitting which has an buna-a type o-ring on a male fitting connected to it. After 1 month, there is a ring of decay on the inside of the delrin fitting where the o-ring makes contact….which causes leakage. I would really like to resolve this issue.
It’s kind of crazy more people don’t use this in 3D printing. I’d drop everything just to get some reel stock and convert my delta printer to only do this. If you can use this ABS and PLA are kind of pointless.. What gives why nothing going on around this??
Maybe toxicity: formaldehyde is released when acetal is heated.
Great article. Does anyone have recommendations for tapping Delrin? I’m trying to tap threads for an M5 (.8 or .9), 10-32, or 10-24 screws to attach steel (1mm) and aluminum (3mm) (ski bindings) onto 1/8 or 3/16 Delrin. I could also use a self-tapping or thread forming screw. I can through tap but the screw must be flush with the back. Because of the flush back and thin sheet requirements I don’t think inserts could work. So what would give me the greatest pull-out strength? I foresee direct pull out pressure, and pressure coming from the sides — figure a pull out load of +/- 100 pounds per screw. I’d like it to be able to hold about as well as a 5mm wood screw in 9mm of wood. Once mounted, I won’t need to remove the screws. I also have 3mm and 5mm ABS, but I figure Delrin will hold a screw better. Appreciate any input here.
Is there any risk in using POM in a 170 degree Fahrenheit dry ice sublimation environment?
HI hope someone can advise on gluing Delrin to an air rifle piston, normal way is to mill so far through the piston and simply gluing them in, its called BUTTONING.,the piston and receiver glid smoothly taking out any free play. I don’t have that type of machinery,so is there any type of glue that would adhere Delrin to steel? Thankyou heres a link of how its done correctly..https://www.youtube.com/watch?reload=9&v=g6wwLgOq2Uk
Hi
I am looking for a material I can mould cold in a silicone mould for gear wheels in 1/10 scale discontiued radio control cars can you suggest any at present Iuse a 2 part fast setting resin ?
Would acetel bend with an approximately 6 lbs suspended load?
I’ve been trying to print POM so hardly without results!
My only luck was with petg as a raft and printing pom on top of the raft. if you have a single extruder you can simply do a fialment swap
my issue is that tho that petg can’t hanlde more than 60 degrees. so it gets gooey and considering justhow hard acetal warps it just pulls it up without releasing.
my enclosure is 30-35 to 40 degrees and it’s passive. I think if I get it to 60 with a heater i might finall ybe able to print acetal! so far i’ve only used acetal in conjuction with PETG purely for wear resistance around parts that suffer from it!
Great article, Im using POM for M5 plasdtic screws, and strugle to choose the correct type of POM, for max strenght/tortion. I would like to be able to gain a torque about 1,5Nm, any advice, also there is an issue with to much hollow/air close to the head of the screw , sp they break to early.
Nube question – my apologies. Forming a frame for an internal frame backpack. Was looking at HDPE, but I see that Delrin has a higher tensile strength. Can Delrin rods be molded into shape, perhaps with heat?