[Jay]’s Chevy S-10 electric conversion needed new batteries. The conversion was originally done with a bank of lead acids underneath the truck bed. With lithium battery factories so large they can boost an entire state’s economy being built, [Jay] safely assumed that it just wasn’t worth it to spend the money to replace it with a new set of the same.
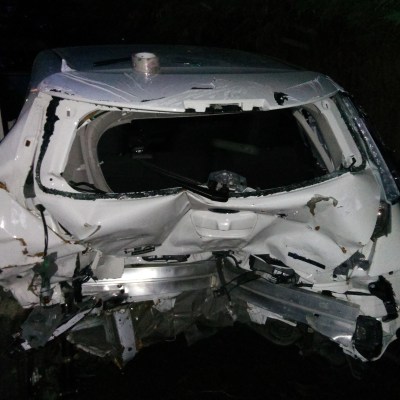
You should remember the beginnings of this story from our coverage nearly a year ago. Being the kind of clever you’d expect from someone who did their own EV conversion, he purchased a totaled (yet nearly new) Nissan Leaf with its batteries intact. It took a little extra work, but after parting out the car and salvaging the battery packs for himself he came out ahead of both a new set of replacement lead acids and an equivalent set of lithium cells.
He has just completed the first test drives with the conversion, having built 48 Leaf cells into blocks resembling the volumes the old batteries occupied. He had to add some additional battery management, but right-off-the-bat, the conversion netted him more amps and 650lbs (295kg) less weight for the same power. Nice!
We linked to all the posts tagged leaf on [Jay]’s blog. There’s a lot going on, and the articles aren’t all linked to each other. It’s a really cool build and there are definitely tricks to learn throughout the whole process. If you have an hour to kill, [Jay] recorded the entire 26-hour process in a 66-minute video that is embedded below. It’s fun to watch him build up and mount the different modules and gives you a deep appreciation for his devotion to the project.
I am doing the exact same thing:
http://www.wolftronix.com/E10_LithiumUpgrade/index.html
Except I am reverse engineering the Nissan Leaf Battery Management System (BMS), so I can reuse it.
Great info Wolf , thanks for linking
ack, could do without the Yellow and black “angsty teen from 1995” color scheme, makes it hell to try to read.
How well are these shielded from the elements?
Reasonably well, they have a rubber mat over the top of them and that is covered by the bed of the truck when it is lowered.
I see sparks in the video thumbnail, and that’s terrifying. I have two Chevy Volt batteries going in to my BMW in series (minus a few modules) for a 620V nominal pack. Like [Wolf] above, I’ve reverse engineered the BMS to be able to reuse it.
How about sharing the deatils somewhere about the protocols and requirements. Lots of volt conversions out there but crap for bms data
What are the battery boxes made from? I personally would had made them out of anodized aluminium plate and lined them with plastic honeycomb structural panels (the technology is cheap enough anymore).
They appear to be plywood – likely to feed the lithium battery fire
Because battery fires are fun!
http://imgur.com/OpFcp
Some foams are also a friend to fire.
The battery boxes are steel (1/4″ bars with sheet steel inside that) covered by plywood and foam (electrical and heat insulation, also physically keeping the “battery” modules from moving around. If the pack catches fire, I’m much more worried about the LiIon batteries than the small amount of wood/foam around them.
Wow, spark, and wood cutting just inches from the battery, that sounds pretty scary.
As mentionned before, it seems that there is not much fire protection.
Are those cars allowed on the road?
There’s going to be an interesting parts opportunity as the Leaf fleet (mostly leases as I understand it) ages out of service.
As far as fire hazard – if I were an emergency services worker I’d be terrified of something like this not because it might combust, but if it was in an accident and they had to start cutting things thinking it was a standard vehicle (yes, it has a big sign on the side, but still) it could get pretty nasty in a hurry.
The high voltage wires from under the bed are routed inside the frame rails under the cab to the front engine compartment, and are not passing through the passenger cabin. Jaws of life would be used on the pillars/doors/roof, not the lower frame rails. Also, the truck has an inertial switch that turns off the main contractors if it is involved in an impact/accident.
I am under the impression that these “pouch” batteries need to be “hugged” to keep them from puffing up and loosing some of their capacity? Or is this alignment just to firm up their mounting.
nah, it’s LiFePO4 you’re thinking about
The LEAF cells are in a metal can that provides some “hugging”. When installed in the LEAF, there’s a sheet metal plate that provides a little extra support, but I suspect his rigid foam and plywood enclosure is almost as good.
The plywood “side panels” of each battery unit provide the compression for the Nissan Leaf Modules. You can follow this URL to find out more about the individual “battery” units.
https://www.summet.com/blog/2015/10/31/how-to-build-a-16-volt-battery-module-from-six-nissan-leaf-cells/
pleeeeeaaase do not use wood anywhere on an EV conversion. ugh.
I see all these conversions for using a Leaf pack with another EV.. What I’m curious is what one would have to do in order to take an additional Leaf pack, reconfigure it to fit in the cargo area, and connect it in series with the existing Leaf pack to increase the range. I’ve seen aftermarket solutions, but they’re $6500 or so, when you can usually get a wrecked leaf for $1500 or so from the auto auction (And can recoup costs by selling off bits of the car)
–Did you use the whole pack (24kWh,) just reconfigured?
–What kind of range do you get and what charge and discharge levels?
–Were these G1 batteries, or 2nd Generation?