I bet the hand saw really changed some things. One day you’re hacking away at a log with an ax. It’s sweaty, awful work, and the results are never what you’d expect. The next day the clever new apprentice down at the blacksmith’s shop is demoing his beta of his new Saw invention and looking for testers, investors, and a girlfriend. From that day onward the work is never the same again. It’s not an incremental change, it’s a change. Pure and simple.
This is one of those moments. The world of tools is seeing a new change, and I think this is the first of many tools that will change the way we build.
Like most things that are a big change, the components to build them have been around for a while. In fact, most of the time, the actual object in question has existed in some form or another for years. Like a crack in a dam, eventually someone comes up with the variation on the idea that is just right. That actually does what everything else has been promising to do. It’s not new, but it’s the difference between crude and gasoline.
My poetic rasping aside, the Shaper Origin is the future of making things. It’s tempting to boil it down and say that it’s a CNC machine, or a router. It’s just, more than that. It makes us more. Suddenly complex cuts on any flat surface are easy. Really easy. There’s no endless hours with the bandsaw and sander. There’s no need for a 25,000 dollar gantry router to take up half a garage. No need for layout tools. No need to stress about alignment. There’s not even a real need to jump between the tool and a computer. It can be both the design tool and the production tool. It’s like a magic pencil that summons whatever it draws. But even I had to see it to believe it.
Enough Ranting, What Is It?
Shaper Origin is an augmented reality CNC router. The augmented portion is a suite of sensors and an onboard computer. You give it a few reference points on a surface and it uses that to track its position on the surface. It then augments your view of that surface with a rendering of the paths you’d like to create, edit, or cut.
Unlike most AR devices, it doesn’t just augment the data available to you, it actually changes physical things about the world around it. This includes your ability to use the tool. When you use the router to trace the paths it’s projecting on its display, it automatically corrects any errors you make by moving the bit opposite of them. Previously, your best freehand work might have been to stay within a half inch of the path. Now you’re magically able to hit a hundredth of an inch.
How Does it Work?
There are undoubtedly many ingredients in the secret sauce that makes up the Origin. One of them is the fiducial tape used by the system. The tape looks like (and is) a perpetually randomized pattern of dominos. There are only a few hundred possible dominos, but the tool’s computer vision software interprets both the dominoes and their relationship to neighboring dominos. When you consider that the tape is endlessly repeating and randomized, the chance that you’ll have the same segments of tape on the same work piece in the same orientation become virtually zero.
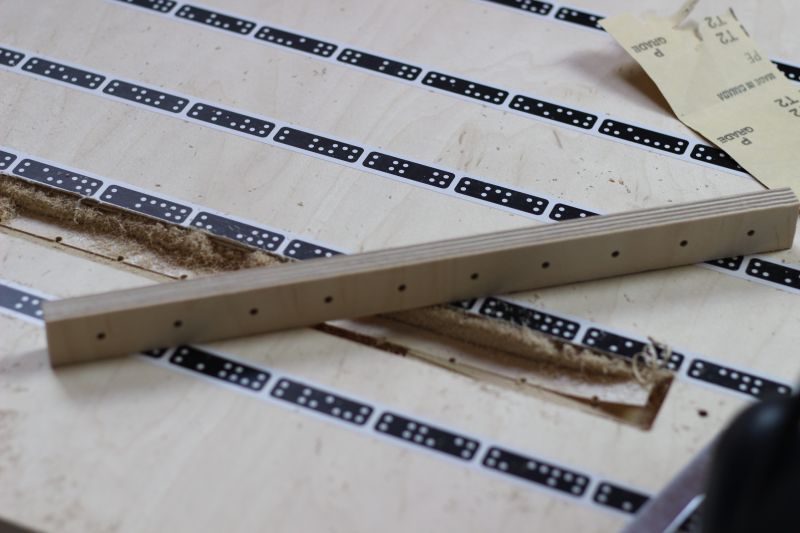
One really cool feature of the tape, which Origin uses to its advantage, is as an identifying marker. Since it is very unlikely that the tape will ever be in the same configuration twice, Origin can use the configuration of the placed tape as a unique identifier for the material. Let’s say you have a bit of baltic birch sitting in the corner of your shop. A few months ago you cut some wooden gears out of it. Well, when you need a new piece cut out of it, Origin will instantly recognize the arrangement of tape on it. It will know where it had previously cut out the gear. It is possible, then, to have an entire library of materials in your shop with very little set-up needed to begin a cut.
As for placing the tape, Origin isn’t picky. It is using only the relative distance to the tape,and so the tape can be placed in any orientation. No efforts need to be made to keep the tape in any particular alignment. Origin can figure out where it is as long as it can see at least six dominos in its field of vision for maximum accuracy.
Lastly. If you cut over the fiducial tape, or find yourself needing more tape. It’s absolutely trivial to add more. Just place it on the surface and rescan. You won’t lose your progress on the workpiece.
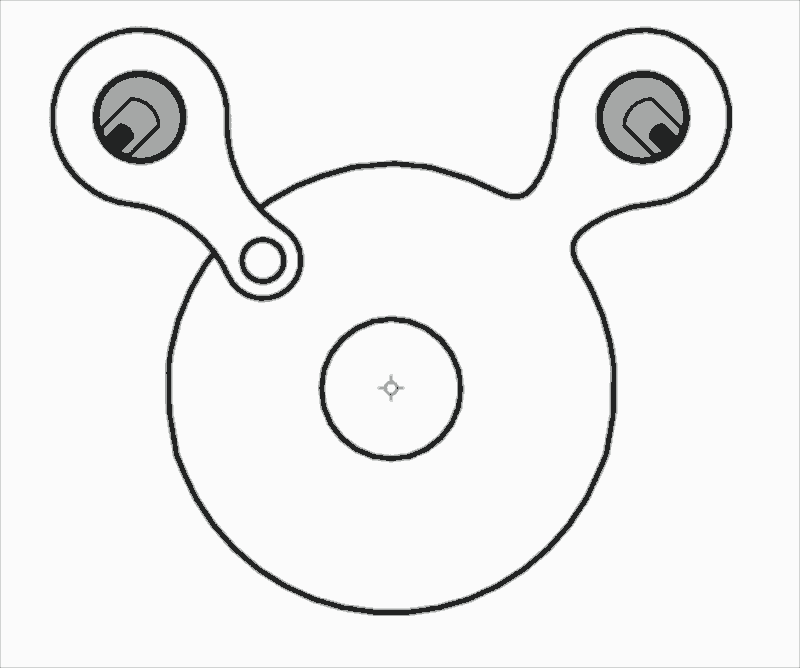
The Mechanism that Fine-Tunes Origin Placement
At the core of Origin is this mechanism. Two eccentric cams are inside of two arms creating a very compact five bar linkage. It’s as non-linear as they get, but fortunately it’s deterministic. Since it’s all computer controlled anyway, this doesn’t matter at all. Any microcontroller could effortlessly perform the required transformation. What it does mean is that there are no bulky linear motion guides, allowing for a compact device.
On top of that the eccentric cams provide a lot of mechanical advantage for fast, compact, and constrained movement. This is especially important when it’s compensating for the unrestrained and uncoordinated movements of a Hackaday writer. Both Mike Szczys and I were able to pick up the tool and cut with it flawlessly, and with minimal training.
There’s certainly a trick to it. Shaper employees were able to hold much tighter tolerances due to practice. Origin actually has quite a bit of feedback to it. Rather than setting the cutting speed in GCODE, the user sets it by moving the device. This is especially handy when cutting a fragile material or getting close to the end of a board. Rather than just accepting that there will be some blowout, you can just slow the cut down and be extra gentle. It offers a lot of control. It’s not a tool that does the work for you, Origin is a tool that makes you better at the work.
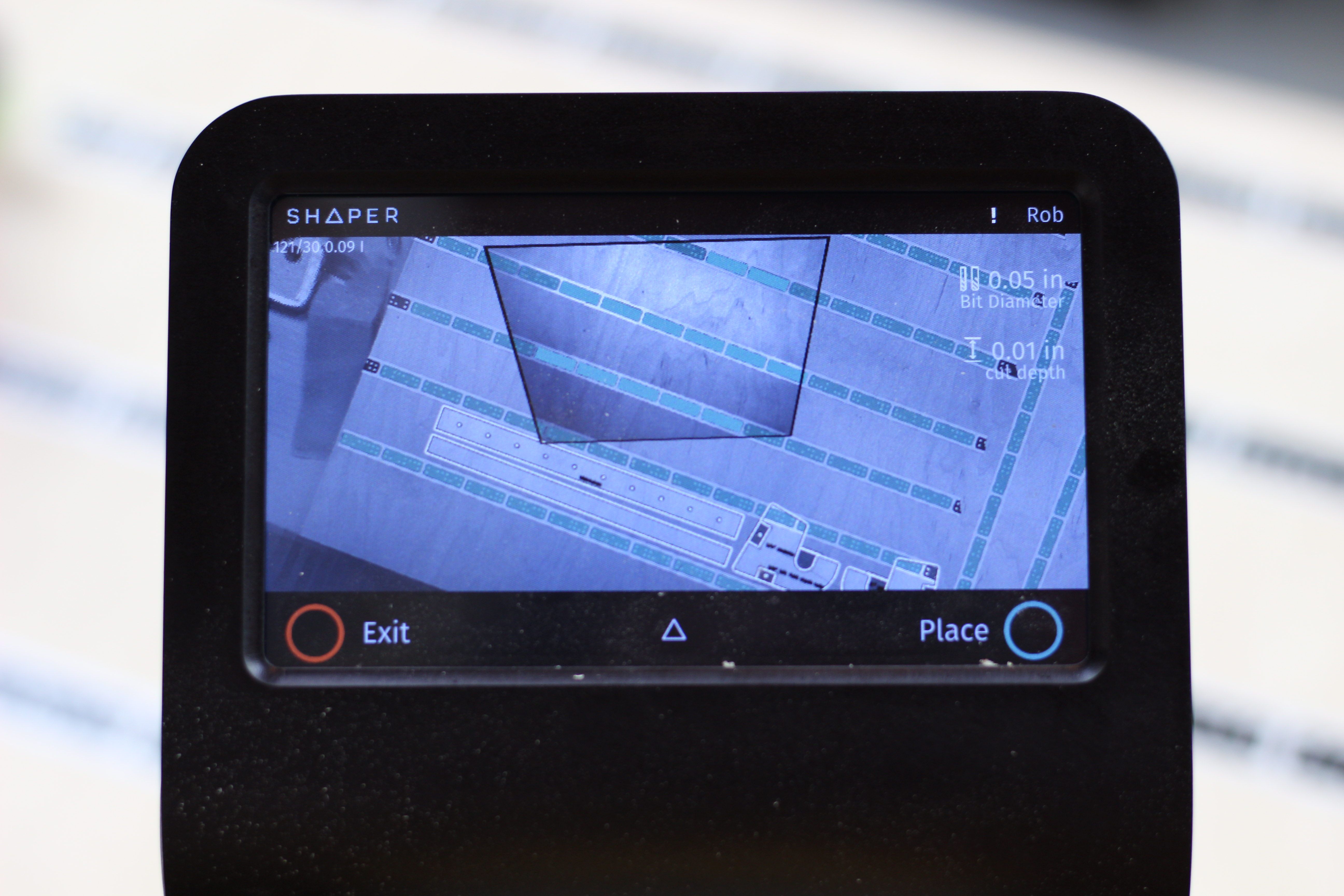
Origin derives most of its tracking power from a carefully mounted camera on the forward facing side of the device. Since the algorithms know the exact location of the camera relative to the cutting tool, it can work its way backwards from the fiducial tape to determine its position. Of course it’s not all so easy. To achieve the accuracy that Origin delivers took years of work, and it will be a while before any of the undoubtedly soon-to-be emerging competition will be able to match them.
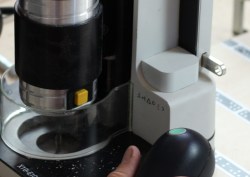
In the photo above we can get a really good look at Origin’s display. The triangle in the middle is a menu button. When cutting, the bit location is shown with a circle centered on the screen. If you look at the bottom of the screen you can see some outlined parts. These have yet to be cut out. To place a part you simply move and rotate Origin until the part is oriented properly underneath it on the board — Origin works just like a mouse.
The trapezoid in the middle is the actual live view of the camera. All the highlighted dominos are the ones that Origin is using to hold its position. Everything around the trapezoid is blind to the device, it is rendering a picture it scanned earlier. This way the user gets a very high level overview of the workpiece. Pretty cool.
Origin can store a wide array of paths on its internal memory. It can also take vector paths from the cloud, generate them directly from the tool’s touchscreen interface, and thankfully, it can read designs from USB Drives. (Looking at you Glowforge).
One of the coolest features, mentioned earlier, is that Origin can actually be used to draw the needed paths. Want to cut a 30mm hole? Mark an X with a pencil where you want the center of the hole. Move Origin until you can see the X on the screen. Place the center of the circle on the X and then drag Origin to change the size. Optionally, just type in the dimension of the circle using the onscreen keyboard. More than outlines are possible. You can easily do things like layout a pocket for a hidden hinge without ever having to open CAD or vector software.
The best part about the Origin is its responsiveness. A lot of work has gone into bringing it below the threshold of human perception. Robert B. Miller first wrote in 1968 that any user interface element must respond within a tenth of second or the user will notice the delay. Considering the amount of heavy processing involved in this kind of machine, it’s nearly miraculous that they manage to stay under this threshold.
What Went Into Its Development?
We only got a glimpse of the thousands upon thousands of hours of development that have undoubtedly gone into Origin. Thankfully they gave us a great set of highlights.
The origin of Shaper and Origin began with a frame. Not a machine frame or anything technically difficult; Alec Rivers, one of the founders of the company, decided that he would very much like to properly frame a photograph. From what we understand, a few hours into the project… perhaps even a few tears of frustration later, the founder became aware that woodworking was absolutely not his thing.
However, no shortcoming can survive unmolested by progress for long. Engineering is always waiting there in the shadows, ready to solve a problem. “Surely one can just build a robot to do this, ” Alec thought. “It would be simple, just move opposite of all the mistakes I’m making,” he followed the logical progression; thoughts unhindered.
We’ve been told that it’s been five years and the picture frame has not been built yet, but instead we have the Shaper Origin as we see it today.
It started with a machine vision camera and a portable x-y platform. This platform used regular lead screws and linear bearings to perform the translations. It was assumed that the user would take care of the Z depth. The next iteration was the first one to feature the mechanism that is used today. The Z depth was still managed by the user. They’d have to manually plunge the router.
It is at the next point that Hackaday first interacts with Origin at a Makerfaire. The device starts to evolve. Gone are the clunky handles and better industrial design begins to have its influence. Still it’s a long way from the machine we see today. You can see how far its come from the following video (Shaper changed its name from Taktia to Shaper in 2015):
Further user testing and development added the Z axis control. This is an important development. Not only is pocketing possible, but Origin can now retract when it senses error or the cut has been finished. Finally, Origin begins to look like the machine we see today. We’re not certain if the commercial version will look similar, but we imagine it will be close.
It was quite a challenge to find a manufacturer who could produce the fiducial tape. Not only does the pattern have to infinitely randomized, it has to be extremely accurately printed or Origin will have errors in its positioning. Ilan Moyer, Shaper’s other co-founder, confided that the their original fear was that they’d have to make it themselves. To that end he constructed a rather cool set-up. An industrial ink jet head would print a continuous pattern on a carefully reeled spool of tape. A python script controlled it all. Thankfully, they did eventually manage to teach the production process to a professional tape manufacturer, who is now supplying Shaper with the magic tape.
Testing and More Testing:
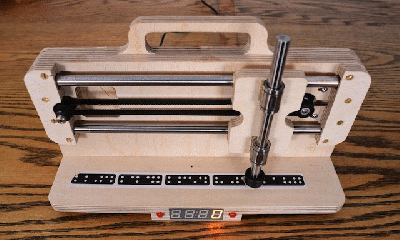
Naturally a device this complicated needs extensive testing. The Shaper team has come up with a lot of interesting in-house solutions for testing their machine.
For example, the tape needs to be optimized for workshop use. It needs to stick to a variety of surfaces. It needs to be cheap. It needs to come off of the surface without leaving residue. It also has to be durable. A machine tool is going to be scraped over its surface multiple times in use after all.
Shaper had ordered their first run of professionally manufactured tapes. They’d also ordered the entire assortment of abrasion coatings offered. It was time to finalize the tape specifications, but they came to the realization that their testing up to that point was too unscientific to have produced a clear winner. So they did the only thing that made sense. They built a testing machine from what they had around.
The machine is simple. An Arduino drives a floating head with some sandpaper glued to it back and forth. It counts the cycles. The tape with the least amount of damage would come out the clear winner.
Another problem was that of the spindle. While the Dewalt router that everyone seems to use is fine and dandy; there are hundreds of router spindles out there, and Shaper wanted to find one that would provide the best power, control, quality, and cost to integrate into Origin. The only way to know for certain is to test the options – all of them. But there’s a problem. How do you test a spindle anyway? Do you have an intern route wood all day long, keeping a subjective log of the spindle’s performance?
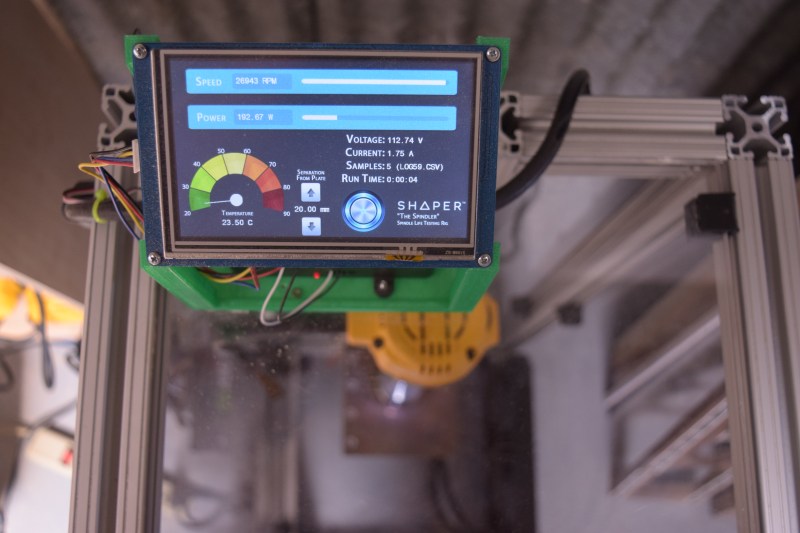
We were kind of blown away by the testing device, but then again these guys are very clever. They came up with a way to place an arbitrary load on the spindle. They do this by attaching a really strong magnet to the end of a shaft attached to the spindle. The magnet hovers over an aluminum plate. By moving the magnet closer and further away from the plate they can dynamically adjust the load by inducing eddy currents in the metal. Naturally, this heats the plate up quite a bit when it’s eating 500 watts of power, but it gave them a way to test any of the spindles out on the market. A bit of off-the-shelf watercooling meant for CPUs and the machine can run indefinitely.
Jeremy Blum threw together a simple touchscreen control panel that logs spindle metrics in real-time, and allows them to push the spindles until they break. We’d love to see their data for all the routers in the market.
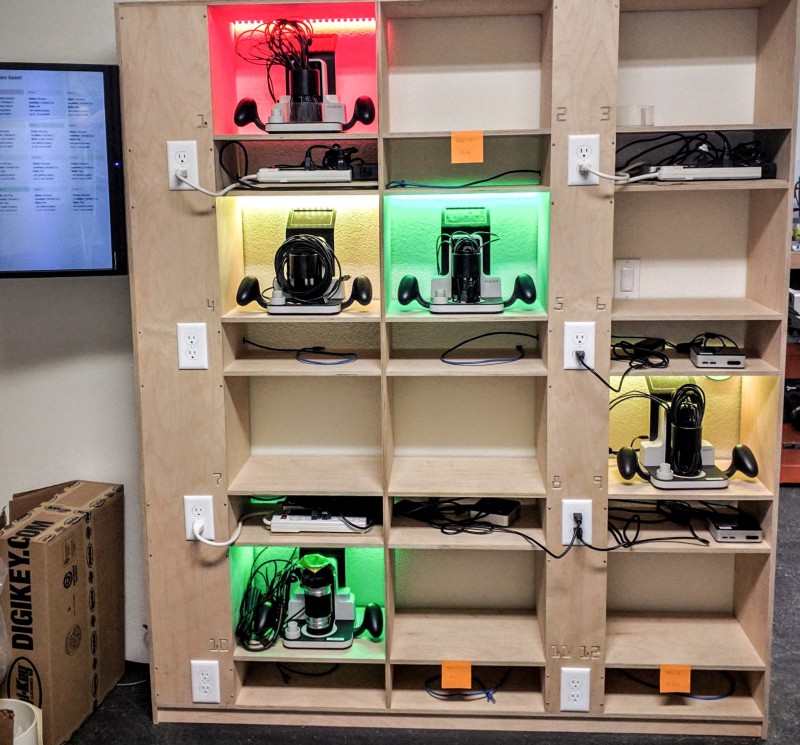
They go into it in some detail on their behind the scenes blog, but another reason for their success is their excellent system for tracking bugs and testing results. The device above is called “The Basket” — they like to joke that all their “eggs” (their hand-built beta prototypes) are in one basket. The basket employs purpose-built software for checking units in/out, and logging detailed bug reports for each unit.. The shelf is, of course, also entirely made with Origin. We feel that its ability to cut properly sized holes for plugs is worth it alone.
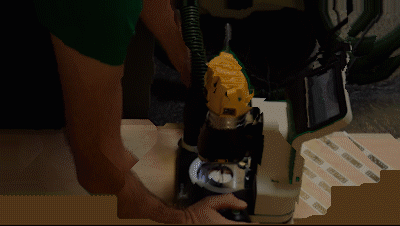
The Basket can track who’s using the tool, who broke the tool, its current status, and much more. They even use it to keep track of beta testers. All the data is seamlessly pushed to their internal beta logging system. One problem any engineer faces when performing tests on a newly designed hardware is whether or not the problems they are seeing are a fault of the design, or just a fault of assembly. Having nicely organized logs is the best way to make such determinations.
What can I make with it?
Fortunately Shaper has recently begun posting more videos of the device in action. The simple answer is, anything you could imagine building with a Shopbot or Shapeoko is fair game. But, you can also do much more since there is no limit to build envelope, and you cut non-sheet materials, like existing desks and already installed panels, etc. Shaper currently recommends that Origin be used for wood-like materials, soft metals, plastics, and composites. However, they’ve been doing a lot of testing on tile and granite. Since all it requires is the fiducial tape, it can make anything from the size of a matchbox to something as big as a thirty foot conference table. Most of the test rigs shown in this article were made using the device. Below is a playlist showing way more example videos.
The Future:
After a long wait, Shaper has opened up pre-orders for the device. They hope to have the first production units in people’s hands next year. Keep in mind this isn’t a Kickstarter where they’re, “pretty sure it will work, we know a guy”, they’ve been at this for five years now. So we’re betting on a good chance it will turn out well for them. There are some early bird discounts rising up to the final estimated retail cost of $2,099 US dollars.
Having used Shaper’s Origin, there’s no tool I want to add to my personal shop more. I’ve fantasized about owning a Shopbot for years, but even if I could afford it, the chances that I’d have a place big enough for it are even less. This just opens up so many possible avenues for making. For most of the things I’ve used a CNC or laser cutter for, this will do. For most of the things I’ve wanted a full wood shop for, this will do. It’s the size of a breadbox, easy to use, and enabling.
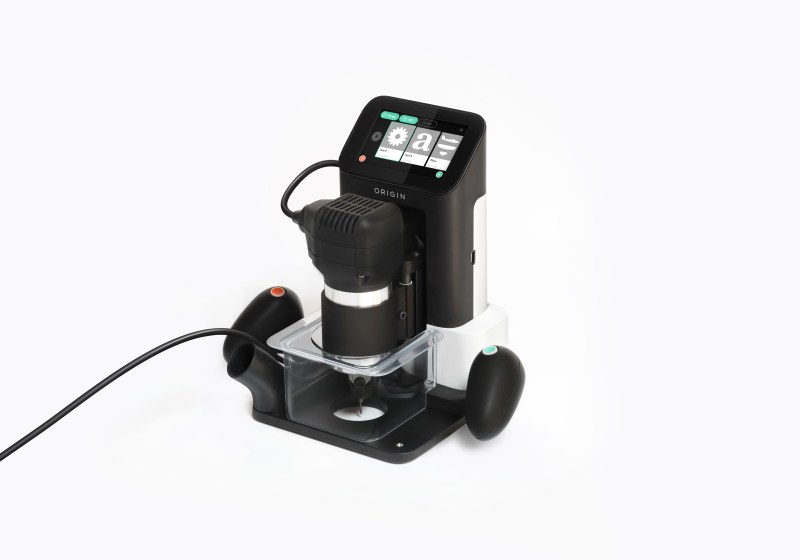
This thing is awesome, I’ve built an MPCNC and it definitely is great but I love the mobility of this tool. If you are looking for yet another referral link please try mine!
https://preorder.shapertools.com/ref/G943WVN3X