A while back I looked at lubricants for the home shop, with an eye to the physics and chemistry behind lubrication. Talking about how to keep parts moving got me thinking about the other side of the equation – what’s the science behind sticking stuff together? Home shops have a lot of applications for adhesives, so it probably pays to know how they work so you can choose the right glue for the job. We’ll also take a look at a couple of broad classes of adhesives that are handy to have around the home shop.
The Science of Sticky
So how do adhesives work anyway? It turns out to be one of those “we’ve got some ideas, but nobody’s sure” things. Our biggest clues come from looking at the chemical structure of adhesives, and as usual it’s helpful to look to nature for first principles. From the mucilage or latex secreted by some plants to trap insects to the boiled connective tissues of horses sent to the proverbial glue factory, natural adhesives are all macromolecules of some sort. The long protein chains of hide glue, the polysaccharides secreted by plants and animals in need of a little stickiness, or even the hydrocarbon chains and terpene resins that early humans learned to gather from tarpits and pine trees to glue ax heads to hafts – all sticky stuff is composed of long molecules.
Whether natural or synthetic, polymer adhesives have a lot of sites to interact with each other and with the substrates they’re sticking to. The degree to which these molecules stick to each other is called their adhesiveness cohesiveness, while how they stick to something else is called their cohesiveness adhesiveness. Adhesiveness has a lot to do with molecules being attracted to each other thanks to van der Waals interactions, which is the total force between molecules based on their electrostatic charges and polarization moments. The forces are weak individually, but macromolecules offer lots of places for the force to act, contributing to both adhesive and cohesive properties. Additionally, macromolecules are good at penetrating into the pores of the substrate, contributing greatly to the adhesive properties by mechanically locking the adhesive to substrate.
Adhesives can be roughly organized into two broad categories based on how they cure. Non-reactive adhesives cure by non-chemical transformations, such as evaporation of a solvent or by cooling. Reactive adhesives undergo some sort of chemical change, generally polymerization, during the curing process. To be useful, both reactive and non-reactive adhesives need to be prevented from curing until they’re applied. Non-reactive adhesives are pretty simple to manage – a sealed container to keep solvents from evaporating, or keeping a stick of hot glue at its melting point. Reactive adhesives can be a little harder to control, though, and might take measures as extreme as making the adhesive a two-part formulation that won’t react until mixed, or keeping light-cured resins in the dark.
Now that we know a little about how adhesives work, let’s look at a few glues that you might want to keep around the shop.
Cyanoacrylate Glues
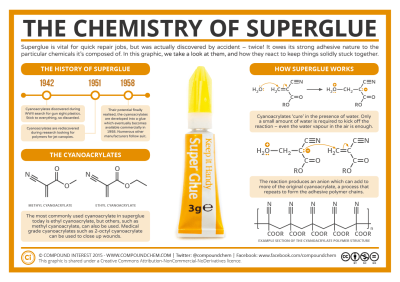
Those of a certain vintage will remember when “Krazy Glue” burst onto the mass-market scene in the early 70s with cheesy commercials about how a single drop was “strong enough to keep this man suspended in midair.” Cyanoacrylate glues have come a long way since those days, and while results are not always equal to the hype, CA glues are a great tool to have around the shop. A reactive adhesive based on the rapid polymerization of methyl-2-cyanoacrylate, the polymerization reaction is catalyzed by water; even water vapor in the air will do it, which is why CA glues go off so fast once the tube is opened. Even a factory sealed tube is only good for about a year, so it’s best to write the date of the package and rotate your stock. You can extend the life of a tube by keeping it in the freezer, though, since the polymerization reaction slows way down with decreased temperature.
CA glues are good for a lot of things, but not every material makes a good substrate. Very smooth surfaces such as glass are poor candidates for regular CA glues. Among the best substrates for CA glues are human tissues, with the skin on fingers and eyelids being particularly vulnerable. Acetone is your friend here, at least for the fingers; you’ll want to get to a doctor for the eyelids. You’ll also want to keep CA glues off of cotton and wool; the MSDS for some glues warn of a strongly exothermic reaction that can cause spontaneous combustion, but as it turns out, this usually doesn’t happen. Still, better safe than combusted.
One neat trick is using CA glues as a filler by combining them with a powdered substrate. Baking soda is the classic example – the mixture forms a hard but workable material that fills gaps and cracks. Woodworkers also mix CA with fine sawdust to fill defects in veneers and fine furniture.
Threadlockers
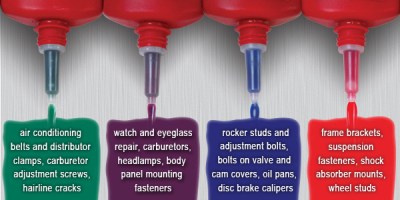
Not generally thought of as adhesives, threadlockers are nonetheless just that – adhesives engineered to glue metals together. Threadlockers are one-part reactive adhesives similar to CA, but generally based on monomers of methacrylate. The adhesive cures when exposed to the electrochemically active and oxygen-free environment deep inside the threads of fasteners. As it polymerizes, the threadlocker works into the gaps in and between the metals and increases the friction needed to loosen the connection.
Threadlockers come in various strengths and with different formulations for filling wide gaps in worn threads or for wicking into preassembled fasteners. For less reactive metals like stainless steel, or for fasteners coated with cadmium or oxide compounds, a primer may be necessary to get the polymerization reaction started.
Epoxy Resins

Everyone knows epoxy – it’s the stuff that’ll stick metal to metal or pot components for a waterproof application. Epoxides are three-atom rings with oxygen at the vertex. The bonds are highly strained, so epoxides are very reactive. Resins containing epoxides readily polymerize with themselves to form cross-linked structures with properties very similar to plastics. Most epoxies are two-part adhesives consisting of a resin and a hardener, most commonly available as a double-barrel syringe that mixes the two components in the correct proportion immediately prior to application.
Epoxy adhesives can be engineered to perform almost any job, and some are classified as structural adhesives that hold together things like buildings, boats, and airplanes. In electronics we see epoxies all the time, with epoxy resin and glass fibers being the main components of FR-4 circuit boards.
Adhesives for 3D printing
3D printers often require a little adhesive assistance to get prints to stick to the bed. Advice abounds in online forums and around the local hackerspace as grizzled 3D-printing vets swear their method is the best and all others are inferior. A common suggestion is to use hairspray, which after all is just an air-cured single-component aerosol-dispensed adhesive for hair. This works, but the method has its drawbacks and is not without risk. A safer alternative is plain old white glue or wood glue, which is poly-vinyl acetate (PVA) adhesive. PVA is a non-reactive adhesive that cures as the water in the solution evaporates. For 3D printing, a dilute solution of PVA brushed onto the heated bed of the printer will keep ABS and PLA prints stuck down until the bed cools, at which point they can be pried off.
Hot Melt Adhesives
Finally, no discussion of shop adhesives would be complete without the go-to glue of hackers and crafters alike – the hot glue gun. Great for temporary bonds, wire management, reinforcing connections, and general potting needs, hot glues are non-reactive thermoplastic adhesives that cure by cooling. Most glue sticks are composed of the copolymer ethylene-vinyl acetate (EVA) which cures quickly after being dispensed. Hot glue has some advantages over other non-reactive glues – for example, it doesn’t change volume as it cures since it doesn’t lose solvent to evaporation. It’s not great for heat-sensitive substrates, of course, or for applications that are going to be subjected to high temperatures, but for a lot of simple jobs it works fine.
Conclusion
That’s it for our quick summary of our favorite adhesives, but we’re sure that we’ve missed out on some special-purpose gems. Are there any adhesives that you just can’t live without? Tell us tales of how you’ve gotten out of sticky situations.
I believe you left out an important one – polyurethanes like Gorilla Glue.
Plus rubber cement, heavy duty spray mount, silicones … … …
There are also specialty adhesives, such as UV curing epoxies or acrylics. There are also regular acrylic based adhesives as well as cyanate ester adhesives. Then there are specialty single and plural component adhesives that are designed for low surface energy materials such as polyethylenes or polypropylenes.
You got Cohesive and Adhesive reversed…
What’s annoying me about epoxies lately, is seeming inability to get locally any 30 minute working time ones, they’re all 5 mins cure…. well 5 mins until “waxy” then freaking ages to gain any strength, seem to remember 30 mins stuff getting harder inside an hour, though still taking a day to reach maximum.
If you haven’t tried the local hobby shops, it might be worth a trip. At least I bought my 30 minute epoxy at a hobby shop. I hadn’t seen it anywhere else, but I haven’t needed to look either.
Heat accelerates the cure, bake at 150 C, or place inside a black plastic bag out in the sun to get something hard and strong within a few hours.
“The degree to which these molecules stick to each other is called their adhesiveness, while how they stick to something else is called their cohesiveness. ”
Are you sure? Unless there is some weird twist in logic somewhere, I am highly certain it should be other way around: particles of same substance sticking to each other is cohesion, particles of one substance sticking to particles of other substance is adhesion. After all, glues are “adhesives”, not “cohesives” (the latter even isn’t a word, according to my spell-checker).
Yep, I too think those two got switched around.
If you’re using wood, plain old wood glue is hard to beat.
Indeed.
Apart from newer water-/weather-proof varieties, standard yellow PVA is already stronger than the wood you’re gluing. Under ideal conditions it sets up enough to be handled in 15 minutes.
Solvent cement! I often use the ABS and PVC cements, (available in the plumbing sections of hardware and big-box reno stores), for plastic repair. You need to test the solvent in an inconspicuous spot on what you are repairing to be sure that it DOES cause damage to the surface. I put on a drop, leave it for a minute, then scrape it off and look for a little pit in the surface. That means that the glue will dissolve the plastic you’re gluing, allowing separate pieces to meld. The solvent evaporates after gluing, leaving a strong bond that is partly original plastic and partly fillers in the glue, all melted together. Because it melts the plastic you have to be careful applying it, and masking is often a good idea. Also, wipe off any squeeze-out immediately, (unless you don’t care how it looks), clamp it if you can, and allow at least several hours for full bond strength to develop. Acetone is your best bet for clean-up, but be careful. It’s volatile and flammable, it’s harsh on breathing passages, and it can damage lots of materials and finishes.
I’ve also started to use contact cement with good effect on some small plastic repairs. On small surfaces, the time for it to get tacky enough to allow joining pieces tends to be much shorter than that specified by the manufacturer.
As for epoxy, my favourite brand, (outside of hard-to-obtain industrial stuff), is J-B weld. I really like their steel-filled epoxies. I try to avoid Lepage – they used to be really good, but over the last several years I’ve found that their epoxies seem not to work as well as they used to.
While it’s common to call solvent cements glue, but are they really an adhesive?
That’s a good question, and one that never crossed my mind. Wikipedia calls an adhesive “any substance applied to one surface, or both surfaces, of two separate items that binds them together and resists their separation”. And they define solvent-based adhesive as “a mixture of ingredients (typically polymers) dissolved in a solvent”. So I think solvent cement qualifies as adhesive.
– Styrene or Silicone based construction adhesives (Liquid Nails, IronGrip, & Others ) are worth having a tube or two around. A glob of that can save you from having to drill into masonry. For small projects glues like E6000 give the same idea but in a squeeze tube.
– Medical grade superglue (generally heptyl- , Octyl-, nonyl- isomers to avoid exposure allergies in standard methyl- / Ethyl- varieties) in your first aid kit works great in place of butterfly closures or for covering a torn blister.
But AFAIK this medical variants are extremely expensive. I had it used on my one time in hospital and googled it afterwards. The stuff (octyl-CA) costed about 100,- (€/$) per small tube. Is there a cheaper (“generic”) source of this glue?
Vetinary… But don’t use it on humans ;-)
Dang!
I bought some in the first aid aisle at my local Grocery / all in one store a few years ago. It was expensive but not prohibitively so, IIRC about 3USD / tube.
Amazon (US ver) has ‘mastisol medical liquid adhesive’ 4 for 12 USD
‘Surgical glue’ (2-Octyl CA) seems to run about 20USD / mL as ‘Ethnicon Dermabond’
Dang!
I bought some in the first aid aisle at my local Grocery / all in one store a few years ago. It was expensive but not prohibitively so, IIRC about 3USD / tube.
Amazon (US ver) has ‘mastisol medical liquid adhesive’ 4 for 12 USD
‘Surgical glue’ (2-Octyl CA) seems to run about 20USD / mL as ‘Ethnicon Dermabond’
Here we go again blaming the Hair Spray 3D Printed Bed Adhesive for a death that was caused by an improperly stored explosive (Nitrocellulose). That’s just a Clickbait and sensationalized Fake News story that does nothing but damage 3D printing in the public eye. That story would be akin to saying the Twin Towers were destroyed by a fire started with dangerous box cutters.
Improperly used box cutters :-)
You have your basic terms reversed. Adhesion is different materials sticking together. Cohesion is elements of the same material sticking together.
From the Free Dictionary:
The adjective cohesive comes from the Latin word cohaerere, or “to cleave together.” Cohesive things stick together, so they are unified.
Adhesive comes from the Latin adhaerere, meaning “stick to,” which is precisely what something adhesive does — it sticks to things. An adhesive bonds surfaces together.
I have found in my experience that certain plastics can be a real bear to glue without the right adhesive: It seems that the more chemically resistant the plastic, the harder it is to glue it. Sometimes you just need the ‘right’ glue. Polypropylene for example is a tough one to bond: CA just peals off most of the time, and solvents don’t really touch it. However, if you get the right glue, made for the plastic, it bonds well and very strong. Most adhesive manufacturers have a lot of good literature on their sites about selecting adhesives, and while they plug their products, the documents can still provide you with some very valuable information when working with hard to bond materials.
So far in my experience, it is sometimes just best to break down and buy the right glue for the particular job or material. It may cost you some money, but can help you avoid failures and other ‘sticky’ situations.
The plastics you are referring to which are hard to bond are called “Low Surface Energy” plastics. The PETG plastic which makes soft drink bottles is in this category, and we’ve done extensive research into glues for these plastics. It turns out that there are special glues dedicated to many of these plastics, but they are massively expensive. They also have limitations, such as ability to make great structural bonds of solid parts, but something that needs to be flexible they are terrible for. We use the bottles for our huge Water Rockets, and find a lot of these specialized glues fail in areas where a lesser glue using a simple mechanical bond will be superior.
I actually used your guides to glue some PETG bottles together with urethane construction adhesive… It appears to work great! I also could never figure out a good way to couple them together at the threads besides something like a tornado tube, but after looking at your guides, I decided to try the Loctite Glue and activator you recommended to bond the lids. It also worked great!
In my eyes, this is one case where the right glue does the trick…I have tried for a long time to get the lids to bond using CA, and never had any success; they would just peel apart at the seam.
So I do agree with you in most cases, but there are just some applications where nothing but the right adhesive works properly.
In any case, my point was that it never hurts to do a bit of research. In some cases you may need to shell out the cash, in others, somebody may have found an alternative that works great, as in the case with your rockets!
P.S. Nice work by the way guys with the water rockets!
I one time used a glue for such plastic (PE, PP). It was two part in consisting of a primer and a urethane based resin.
Seems like almost nothing will join HDPE.
TAP Poly-Weld (TM) claims to, I’m sure there are others out there but this is a somewhat recent development, at least for the DIY market. Not sure if this works on UHMWPE they only list HD and lower density PE on the label.
For thin stuff you may be better off using rivets, direct threading or nut and bolt connections for thicker slabs.
With fasteners in HDPE, you have to be aware of the fact that it creeps (sometimes quite a bit) and plan for that…
Is there a rule of thumb for that sort of stuff? Like a best practices manual or anything?
West System Epoxy claims a workable bond on HDPE after the surface is cleaned with acetone and then heated with a propane torch to oxidize the surface-obvious warning to let the acetobe evaporate first…
A pass with a torch is SOP in repairing many large plastic surfaces (kayaks, molded floats etc.).
You really need to weld this stuff together using heat and plastic sticks for a good bond.
I second that. I welded HDPE (shower gel bottle cutouts) parts together using soldering iron. Can’t say it was a strong bond, but they stick together. If I had an ultrasonic knife, it would probably had done much better work.
Not true. Look for specialty adhesives designed specifically for low surface energy materials. They tend to be $100+ per cartridge but they do exist.
WOW, thanks for all the ideas everyone! :D
3M™ Scotch-Weld™ Structural Plastic Adhesive DP-8005 works for HDPE
Amazing GOOP® …
no love for Pliobond 25 ?
contact cement with a mil spec rating.
smells horrible, works on lots of surfaces, but not that PE….
I have to second the ‘smelly’ part of this comment. Pliobond has got to be some of the most horrible smelling stuff on the planet! it smells like extra smelly rubber bands, burning, on steroids… It does work pretty well though for odd combinations of materials and stuff though. Ever wonder what the brownish gorilla snot you find in cheap chinese electronics holding the wires is? Pretty sure its a variant of pliobond. It definitely has its place… But dat smell, OMG…
I almost never totally disagree, but CA is the worst glue ever. It sticks to nothing except your fingers and any small impact to the joint will knock it loose. The only CA I’m willing to even consider is Black Max.
But in the spirit of one of those rant+rave articles – my go-to glue, despite the smell, is E6000 (get it from TAP plastics).. It has good (not epic) holding power, stays flexible and the coolest thing of all is that if you want to take the joint apart (assuming it’s a small joint) you can pull it apart and the glue can then be removed cleanly from both surfaces.
There’s this stuff called RTV157 I’m wanting to try out too.
CA can be great for a lot of purposes. Especially if you have the Kicker (Loctite7649) then it is great as an initial bond to hold awkward parts together while an epoxy goes off if you need something rock solid. As for small impacts, again everything is relative, a small bond with a large cantilever will break quickly but large planar surfaces will still create a crazy strong bond. Some even use it in machining operations, myself included.
https://youtu.be/ZSXDIraHz3k?t=79
Great vid – I would not have guessed that CA would hold that wheel in place. Also, thanks for the great tip on setting gear tooth depth!
Real hot glue on wood. I restore old stuff, especially if it had to be broken apart to restore so it can be again. Cooked up at 140F.
So called hot glue (stick stuff) has far less sticking power than bublegum. Really, I just flick blobs of it off where they use it around caps and wire inserts on boards.
Real hot glue is the dogs bollocks…. and the cows hooves…. and almost everything from a horse…
The real benefit of hot glue sticks is when you discover it can be released with a few drops of isopropyl alcohol. Making it a fantastic fast setting *temporary* adhesive. If you want it to be more permanent, you really can’t rely on it’s adhesive properties – but the material itself is fairly strong, so depending on how it’s applied it can hold on mechanically.
Ah, Sticking down smallish heat-sinks with Cyanoacrylic glue to overheating southbriges, they were the day.
Currently sticking a custom heatsink to my RPi PXE server crammed into a router. Fell off once shortly after use, tried another brand and the heat-sink is permanent now.
Can we go back to using “Continued after the break”, please?
No mention of chlorinated rubber based glues?
Yes the smell is terrible and it looks like snot, but leaves a flexible and fairly strong bond…
3M Super 77 (or other spray glues like it), great for glueing down large areas and multiples, also if you spray the back of a paper pattern and let it dry before applying it the pattern will remain in place until you pick up a corner and peel it off. Basically spray on contact cement.
Epoxy putty which activates when the 2 pieces are kneaded together is one of the few glues really capable of filling gaps. Also in the epoxy family, JB Weld is good up to almost 400 degrees, and I will second the observation that it is getting harder to find slow cure epoxies, and that can be a shame when assembling complicated things.
As a builder I would not be without the construction adhesives that come in caulk gun tubes and are stronger and more weatherproof (although thicker and messier) than normal wood glue.
For durable, flexible bonds it is hard to beat E3000 and other silicone glues.
Lots of specialized glues for plastics, PVC, styrofoam, ABS, etc, etc.
Special CA glues with matching refractive indexes for invisible glass repair.
I love glue.
If it’s of any use to anyone, here’s my personal three favourite Loctite products (there are so many that it’s hard to settle on one).
#290: Extremely low viscosity (20-55cP) threadlocker, strength about 5N/mm^2. Good for applying to finished assemblies because it “wicks” in so easily.
#603: Low viscosity (90-190cP) adhesive, strength 22N/mm^2. I mainly use this – runny enough to wick into crevices, but very strong.
#638: High viscosity (2000-3000cP) adhesive, strength 25N/mm^2. Got this before discovering #603. It’s good for filling larger cracks, but doesn’t wick very well.
A useful tool/third hand is a 5 micron double sided tape dispenser (5mm wide), and uv curing epoxy.
Look up for a local 3M dealer, got mine here: http://sury.ch/einwegabroller-doppelseitig-starkstark-84-mm-breit-p-15532.html?sort=2a&cPath=6_24_689
Sorry, 50 microns not 5, and 8.4 mm wide.
StixAll Cement (Elmers) and its silane sisters. Releases acetic acid as it cures so it’s smelly, but it’s strong and heat/water tolerant I’ve glued toaster ovens and boat parts together with them and they’re still running. It can often be peeled off or cut apart which is good in some applications, but sticks well enough for most applications.
I 2nd this. StixAll is the best general purpose glue I have ever used.
Very interesting article. Thanks!
About the only adhesive I don’t use is hot glue. I wished many others wouldn’t either as it’s misused/overused and is a low quality way to get a job done. With my projects I don’t think I have come across an application where hot glue was the ideal solution.
There is regular hot glue, and then there is the industrial stuff that lasts decades.
You get what you pay for.
Yah, get away from the kiddie craft hot glue and in the higher temperature stuff you can get one for wood that’s stronger than the wood.
It often does the job. And it hardens very fast.
What would i use to stick reflective Mylar to a large (4′ x 8′) parabolic sheet? Something liquidy that could be squeegeed out with a soft roller, that wouldn’t need air to cure, that would allow one a couple of minutes to get the sheet in the correct position and that wouldn’t leave large bubbled areas… On our first run, we tried axel grease – lol. Or maybe just staples…
How about liquid nails?
Thanks, John! We’ll have to look into it. Have a great day and thanks again for replying! :)
I’m pretty sure you measure adhesives by tencile, shear, and compression strengths.. I once seen a black epoxy that when cured held thousands of pounds and it was only enough to fill a thimbul..
I’d like to measure some elmers and gorilla glues but not time to setup tests..
I was right.. http://www.epoxysystems.com/strength.aspx
Denatured Alcohol can be used to break down hot glue. I’ve hesitated in using hot glue sometimes due to damaging circuit boards when trying to remove it, but now that I know that just a little dab of denatured alcohol and some time can break its bond, I use it everywhere!! It is great for attaching things on quadcopters because it holds pretty good, has a slight amount of vibration dampening, and now with the denatured alcohol trick, it is easy to undo.
It doesn’t break down the glue, but it does pretty much instantly remove any bond it has to other materials, which is my favourite adhesive trick. If the glue blob is mechanically secured then you still have to cut it away somehow.
My daughter once asked me, “Who invented glue?” First response was, “Probably the same guy who invented the wheel.” Later while doing dishes, and working on some stubborn stuck on food came to a realization — “It must have been a cook!”
Another realization that came to me once building a kit violin and learning to use hide glue. It is essentially gelatin, in fact in a pinch you can use unsweetened gelatin from the grocery. And I realized that violins are made of wood and Jello!
Hide glue has one real benefit — it’s reversible. With a little heat, wooden instruments can be easily disassembled for repair. A little old fashioned, but it has it’s uses.
Another advantage of hide glue is that it is glass-hard when it cools. Many guitar builders use hide glue to attach the bridge of the guitar to its soundboard, because the hard adhesive layer transfers more of the vibrational energy from the strings to the soundboard. Other glues like PVA are often a little rubbery after they’ve cured, and that rubbery layer would absorb some of the strings’ vibrations, especially higher frequencies. The result would be a muddier, deader sound.
Application of the glue is important. You need pressure, lots of even pressure, and time to get a really good bond. Watch some demos for adhesives and they’ll usually use a paint roller and put their weight into it. Use clamps whenever possible, edge clamps for edge banding.
What’s wrong with egg whites? Even tried to clean off a dried up egg spill ….?