I had a friend who was an engineer for a small TV station. I visited him at work once, and despite the fact that he wouldn’t let me climb the 1,200′ antenna tower, I had a great time. I was working for a video production studio at the time, so there was a fair amount in common about our jobs. One of the regular chores we faced was cleaning the heads on tape machines. He had a 5-gallon pail of cleaning solution under his bench that he told me was Freon, which he swore by for head cleaning and general contact cleaning. He gave me some for my shop in a little jar.
I never knew for sure if that stuff was Freon, but it was the mid-80s, shortly before CFCs were banned, so it might have been. All I know is that I’ve never found its equal for cleaning electronics gear. With that in mind, I thought I’d look at contact cleaners that are in use today, what’s really going on when you clean contacts, and why contacts even need cleaning in the first place.
Oxidation is the Enemy
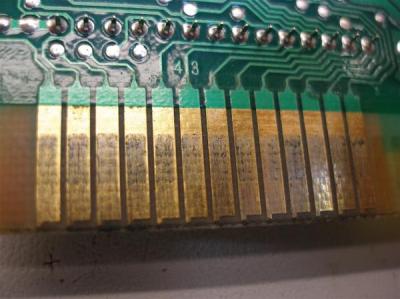
It may not seem like it, but we live at the bottom of an ocean of corrosive gas. Oxygen in the atmosphere is the culprit, and metals are the victims. Pure metals rapidly combine with oxygen to form metal oxides, which usually have different properties than the base metal. Sometimes this is handy, as when an aluminum screen door forms a layer of aluminum oxide that makes it essentially impervious to further corrosion. Other times, metal oxides cause problems. The copper and zinc oxides are nowhere near as conductive as either base metal, so electrical contacts made of brass can have problems if there’s too much oxidation on them.
Exposure to the atmosphere isn’t the only source of trouble for contacts. Arcing across contacts can cause corrosion and oxidation too. In general, direct current is harder on contacts than alternating current, because AC arcs tend to self-extinguish during zero-crossing. But either way, the heat produced by the arc oxidizes the contacts and can produce debris that interferes with conductivity.
A certain amount of contact oxidation is unavoidable, and a properly engineered circuit will take it into account. Wetting current is one way of dealing with oxidation. Wetting current is the minimum current needed to “punch through” the resistance of the oxide layer on contacts. If the wetting current is too low, contacts that appear to be physically connected might actually still be open electrically. Snubber capacitors can be used to remedy this.
Cleaning Solutions
There comes a time when contacts need cleaning, though, and that job mainly consists of removing oxidation. This would seem to call for a solvent a little stronger than the lab standard, isopropyl alcohol (IPA). Metal oxides are not especially soluble in alcohols, so it would seem that IPA is a poor choice for dealing with them. But not all contact contamination is in the form of oxides — greases, oils, and organics can foul contacts too — and not all oxides are in the form of tough films. Some oxidation flakes off the base metal naturally but still sticks to it via the other gummy debris. So IPA and similar volatile solvents, like my long-ago Freon, are a good first choice for flushing away some of the gunk. The volatility of these solvents is key, since it quickly evaporates and leaves little residue behind.
Not all contact cleaning jobs are that simple, though. Sometimes the metal oxide films need a little more persuasion to leave the scene, and in these cases contact cleaners with more complex formulations might be needed. The gold standard for tough jobs for quite a long time has been DeoxIt by CAIG Laboratories. DeoxIt claims to be a “contact rejuvenator” that contains all sorts of goodies. Exactly what’s in DeoxIt is a trade secret — the Safety Data Sheet lists only “Proprietary Trade Secret” ingredients other than the propellant and mineral spirits. There seems to be an urban legend that the secret sauce is oleic acid, but CAIG denies that in their FAQ page. Something slightly acidic like oleic acid would make sense, as it would react with the metal oxide films and expose bare metal. Whatever is in there, it seems to work well enough to inspire fierce brand loyalty.
As good as it is, DeoxIt is expensive stuff – $18 or more for a 5-oz spray can. If you don’t want to shell out that kind of money, you might start looking for alternatives. There are plenty of commercial alternatives on the market, and some folks even claim that a 5% solution of oleic acid in naptha is a suitable DIY substitute for DeoxIt. There are a number of head-to-head comparison videos out there that pit DeoxIt against cheaper rivals, like WD-40. It’s not really clear from these highly unscientific tests how these cleaners stack up, though. But for something best used sparingly, my tendency would be to just buy the original and call it a day.
Now it’s your turn – how do you clean contacts and controls? There seems to be a fair amount of voodoo when it comes to contact cleaners, and we’d like to hear about your experiences. Leave a comment below and let everyone know what your go-to method for fighting contact corrosion is.
[Featured images from WD-40]
For cleaning off card edge contacts, a couple of swipes with a red rubber pencil eraser does just fine.
For something more stubborn, Scotch-Brite pads work great.
DeoxitD5 for sure. Chemtronics also has some great product but not as good as DexIT. +1 for the Freon on contacts and tape heads. When I was working in the commercial video business back that’s what we used. Great for tape heads and rotary switch contacts and pots.
CRC makes a couple good ones at consumer-grade prices and widely available. But in a pinch, your local auto supply store is sure to have disc brake cleaner.
Remember that tiny little cut at the joint of your finger? Brakleen remembers.
LOL, so true!
Contact cleaners often have a lubricant in addition to the cleaner. Brake cleaner will clean things up but may be bad for the contact in the long term.
^^^ This. Brake cleaner will clean the thing and leave it bone dry, much like isopropyl alcohol. Both are great but neither would be my first choice for switch contacts.
Decades of experience in electronic repair agree with the both of you. Sliding contacts with no lubrication will wear and even spall.
I over-oiled a sewing machine while trying to free up the moving parts. The oil seeped into the motor housing. I haven’t tried to run it since then. Is the motor ruined or would it be possible to open the housing and clean off the oil with electronics contact cleaner like CRC or WD40 electronics cleaner? Would it be better to use isotropic alcohol? If so, what strength? I would simply spray off the windings, not soak them, correct?
Any oil in the windings should just spin out. I would not soak the motor, you’ll deoil the bearings. Are you having a problem with it not running? Perhaps the oil got on the motor brushes. You could take the brushes out and clean them with a degreaser or 99% isopropyl alcohol, and wipe off the commutator as well.
Carbon Tetrichloride
Brake parts cleaner melted a slide switch in an old boom box i was cleaning. I wouldn’t use it.
CRC make a couple good ones, consumer-grade pricing and widely available. In a pinch, your local auto supply store wiil have brake disk cleaner that works pretty well.
Ageed
I always used newspapers to polish copper contacts, as it is abrasive enough to take the oxide away but not enough to scratch the copper itself.
For those hard to reach places nothing beats freon spray, but I want to know what comes closest.
considering that the oxides are harder than the metal, how would that actually work?
Paper has a lot of silica in it from the wood and is quite abrasive. There are also clays in some paper to make it whiter.
Before ceramic rods, I stropped my knives on newspaper.
Arklone rocks. Sadly mine is running out :(
For mechanical removal, a fiberglass scratch brush has worked well for me.
Just be careful. If it is a copper PCB that is plated with gold or tin, it will remove it right down to the copper. And do so rather quickly.
Wish this article was longer.
Whatever he gave you, it was not freon. (It may have had CFCs in it but not freon.) Freon is a gas at room temperature and although it may have been stored in a 5 gallon pressure vessel it cannot be reliably stored in a bucket.
Freon is a family of compounds, some of which are slow enough to evaporate at room temperature that they were used for cleaning. Freon cleaning compounds were amazing. I once fixed a VCR by cleaning the head with an industrial freon/alcohol mix that worked wonders after a commercial head cleaner failed.
It was probably trichlorethylene.
Friend of mine worked at ICI (the chemical company) and swore by this stuff. He also had a nasty story of a coworker who’d been tap dancing on the top of an old 55 gallon drum of it and went though the top.
Actually, it probably was Freon- since Freon is actually a brand name and not a formal chemical designation- a specific Freon (branded) cleaner was Freon TF, 1,1,2-Trichloro-1,2,2-trifluoroethane- which is (was) an awesome solvent. I worked at a Ford Electronics plant in Lansdale PA in the late 80’s where they were phasing out their Freon based PCB wash stations. We had 55 gallon drums of the stuff to use to clean boards- I remember it was particularly good at (along with a brush) cleaning the conformal coat off of EEC-IV EFI modules.
Freon is a brand name, for refrigerants made by Dupont. They use it for all sorts of different refrigerants with different boiling points.
Wiki:
R-11: Trichlorofluoromethane also called freon-11, CFC-11, or R-11, is a chlorofluorocarbon. It is a colorless, faint ethereal, and sweetish-odor liquid that boils around room temperature. (23.77 °C)
It was the first widely used refrigerant. Because of its high boiling point (compared to most refrigerants), it can be used in systems with a low operating pressure, making the mechanical design of such systems less demanding than that of higher-pressure refrigerants R-12 or R-22.
R-11 is assigned an ozone depletion potential of 1.0. U.S. production was ended in January 1, 1996.
Trichlorofluoromethane is used as a reference compound for fluorine-19 NMR studies.
Prior to the knowledge of the ozone depletion potential of chlorine in refrigerants and other possible harmful effects on the environment, trichlorofluoromethane was sometimes used as a cleaning/rinsing agent for low-pressure systems.
We kept 5 gal containers of freon as a cleaning solution when I was in the navy 69-72. It evaporates quickly in open air, but remains liquid in the container. Requires no pressure, just replace the cap.
There are many different kinds of Freon. Freon is a trademarked name covering many different formulations.
We also had a type of freon that was used to clean VCR and tape deck heads. Just kept in unpressurized bottles. Not the same as the CFCs used in refrigeration.
https://en.wikipedia.org/wiki/Freon
I was in a 757 once long ago where testing the cockpit lights produced a strange pattern of failure among some, but not all, of the lights. It was looking to me like a long delay or a cancel, but after a moment or two of thinking, the mechanic took one card out if it’s slot, cleaned the contacts with the eraser of a pencil, and we were good to go.
First time I had ever seen that trick, and I was impressed – both with the trick, and how he new where to apply it.
The part of me that thinks like a theorist would have wanted a schematic and would never have solved the problem. Guys like that mechanic taught me to approach problems in a different way.
Having worked in aviation maintenance for most of my life, I can almost guarantee that was a recurring issue that the tech had seen before, probably several times or heard about on the grapevine. The real troubleshooting that you didn’t see happend months or years ago after hours of searching. However many of these types of issues are functions of design and come up again and again, and when you run into one, you can make a great show of it if the onlookers aren’t in the know.
Without listening to and retaining all the tips, tricks, and common problems learned in my A and two C schools I would have on more than one occasional wasted hours troubleshooting while fixing my gear. Just knowing that you can look at the thrytron in a radar and tell by how far down the glowing ring was on the outside of the ceramic casing, one could tell how close it was to failing saved me lots of time; not only in troubleshooting when it did fail, but also in ease of training others in my shop on common things to look for so we were all cross-trained and able to help each other out.
Here’s my beef with all the “experience trumps book learning” types: when you really understand the part and know how it works in theory, the failure modes are also going to be apparent. I’ve seen guys who genuinely believe that theory “doesn’t work”, i.e. you need some magical personal touch that cannot be transmitted by simply describing the case.
But there’s book learning and book learning. Someone with only cursory understanding of say vacuum tubes can still design and build the circuits, but they don’t really understand what they’re doing, and so the “self-taught mechanic” comes in and spots an obvious problem he’s seen a thousand times and gets cocky about how the book nerds don’t understand anything – but he simply hasn’t met someone who really knows their stuff.
Anyone who’s been to school knows that often times you only learn what you have to learn to get ahead. That’s what the “tips and tricks” are – they’re shortcuts to patch the biggest gaps you’re left with after you’ve learned the minimum to get ahead.
Bravo! The fact is I’ve never met a competent tech, or engineer that was good at his job that disparaged the other. You really only find that attitude coming from those that either have a chip on their shoulder or have serious self confidence issues.
Hear, hear. I’ve worked with techs that have only a cursory knowledge of theory. Often they are pretty good at run-of-the-mill problems, but fall down hard with anything out of the ordinary.
Go to Oregon Tech. They will teach you book and hands on. An added bonus, graduates from this school earn higher starting wage on average than any other Oregon college.
DV82XL: College educated, pure engineers with no hands on experience are a prime example of chip on sholder.
Will bet same connection needed cleaning again some while later. The pencil eraser works as stated above but some believe leaves a residue which is corrosive to the connector, in any event the problem often comes back after a while. More often you do it, the quicker it comes back. So yes, it’s a trick… a trick on you.
Better method. Use only a clean pencil eraser you reserved for this purpose and clean the connector with an alcohol swab before using the eraser, and a fresh alcohol swab after the eraser, then reassemble. Much better reliability. It’s the ticket.
Another method with less reliable results yet some think a better technique, is an ink eraser instead of pencil… don’t do it. It’s abrasive enough to remove some of the gold tin…. you’re tricked twice.
The real trick is keeping more than one box of alcohol preps around the shop, one in the trunk, and a few preps in the toolbag, plus a protected and clean eraser you treat like it’s gold. Use liberally.
Good advice. I’ve seen more than one edge connector destroyed by someone with an ink eraser or sandpaper.
Oh so true. Never do I use an eraser and reassemble. That is a short term fix … for whatever reason. In fact I avoid erasers all together unless the surface conductive coating is thick, and there’s a lot to do … and I don’t have anything else. If it’s a gunk buildup … I use chemical followed by paper. If no gunk … just paper. In any event, leaving behind eraser gunk, or anything that is not designed to protect or lubricate contacts, then a dry polished by paper finish is good. I keep 3×5 cards at the ready.
I had a computer whose graphics card was exceeding sensitive to position in its slot connector …. barely worked at all. Polished the cards contacts with no improvement. Cut and stacked 3×5 cards to be the same thickness as the board, sprayed them with brake parts cleaner, and slid them once or twice into the connector slot. That connection became perfect and utterly insensitive card position. You could move that card side to side as as far as it would go while in operation and never have the slightest hiccup. Gotta remember, connections have 2 sides. By the way, there was absolutely nothing visible to the naked eye on those 3×5 cards used to do the cleaning.
I wanted to rehabilitate a 9V breadboard calculator that I’d built in 1973 that had languished on a back shelf for 25 years and that didn’t respond to a new battery. I gave every contact surface a shot of Deoxit D5, worked the 15 push-buttons a few times but didn’t touch the 4 chips or 2 display sockets. The calculator came back to life and has functioned nicely as a vintage display piece ever since.
Faber typewriter correction erasers are my tool of choice — it looks like a wood pencil, but has ink eraser in the core instead of graphite. Convenient brush on the eraser end, too.
Yep! I use it too!
Could not live without it!
On, what, though? You need to specify. I’ve seen edge connectors destroyed because someone used an ink eraser and removed all the gold or tin plating.
There is no one-size-fits-all cleaner. Anyone who tells you there is, is selling you patent medicine.
Ink erasers are a bit aggressive for electronics. I use a pink eraser on tin plated edge connectors. Gold contacts should NEVER require anything aggressive, not even paper. I’ve seen gold switch and relay contacts destroyed when paper was used as a contact cleaner. The gold is thin and soft. I’ve used paper to polish the edge of knives.
You mention using WD40 for contact cleaning. It is not a good solution(pun intended) Although it does clean fairly well, it leaves an oil residue that can attract dirt making the problem worse further down the line. Many cheap contact cleaners do this. Ive always used Servisol Super 10 Switch Cleaning Lubricant. Although this also leaves a slight residue, I doesn’t seam to have the same degradation on contacts as WD40. WD40 does have one use, it is superb as a cleaner in wet or damp environments, probably because it does leave an oily residue.
This, I have imbibed too much cheap jim beam copy to commment coherently in depth, but wd40 as per the image is not a cleaner, it leaves a reside. If this is a problem is left to the more sober reader.
WD40 Contact Cleaner != bog standard WD40
per here – https://www.wd40specialist.com/products/contact-cleaner
WD40… I got to really hate the smell. Some amateur sound guy would hose down all the controls on an amp or console, leaving a residue that mostly evaporates and may eventually result in potentiometer failure. It is really horrid on slider pots.
+1 agree
Gotta ask….why did blowing on the damn cartridge seem to be the goto solution? that was the de facto standard back in the day. I remember taking my game to someones house to play and the first thing they did was blow on it before putting it in their console.
I had never seen that and took my game back, asking “what the hell, man!”.
They explained to me that was the way to clean them since dust caused bad connections. No idea at the time, again, I never, ever had problems with my consoles to do such and argued that there wasn’t enough dust floating around to cause that kind of poor connection and that something was wrong with his connector inside of his console. No idea during that time about oxide corrosion.
Anyway, as time went on, I saw this “solution” being performed more and more until it seemed to spread across country, if not world wide.
I must have lived in a oxygen poor and dust free home because non of my consoles or games never needed “blowing”.
The first time I saw someone use an eraser was my first electronics job out of school. I worked for a place that mass produced specialize computers and computer boards for trains and subways.
I had some daughter boards come out of thermal cycle and I was having problems with them passing test. My thought was, cheap, bad connectors warped during all those hot/cold cycles. the company had this woman, I know for a fact she was over 70, that had worked with the company forever, like, employee #1 or something, before I was born I know, and her job, no sh!t, was to do detail solder repairs on stuff others messed up and could not do, I’m talking repairing 8mm traces, replacing vias, components, on 4 layer PCBs. Stuff that should go into the trash but was waaaaay to expensive to scrap.
I was told to take it to her for “advance repair”.
I’m thinking, how does this older woman, whom looks like a typical southern grandmother sitting on a front porch reading a bible, get a job doing this and have this much experience and knowledge.
I took it to her, thinking this was going to be interesting, fruitless and time consuming.
I told her what was wrong, she pulled out a pencil and started erasing the gold plated connectors. I’m thinking, OK…….
She told me to try that one, and if it worked, do the same to the others.
I tried it, it worked, I did the same to all the others, they worked, flawlessly.
from that moment on, I spent as much time with her as I could learning.
When i left that company, she was still doing that work, a little slower, a new set of glasses, and was MAYBE thinking about retiring…..
I hope that when I’m 70 I can still solder traces thinner than 8mm…
I had a lady a bit like her at work. She also used to be a snowmobile racing champion… I still have some of her special tools at work that I got from her when she retired.
2 different Daniel’s here…
Most Daniels are interchangeable though, when did you last meet a super unique one?
Three
Hi. My name’s Darryl. This is my brother Darryl. This is my other brother Darryl…
What I find fascinating is that back in those days, before the interwebz (Ok so we had BBSes but not every kid used those), every kid knew to blow on the Super Genintari cartridge when it glitched.
The original NES frontloader console suffered badly from dust buildup because the cartridge slot was mounted horizontally. Later consoles all used a top loading design but the cartridges themselves remained vulnerable of course.
No it did not. is was a mechanical problem with the springiness of the contacs in the machine if the cartridge was left pressed down all the time. As the NES has a dust cover and is otherwise a closed system, dust was never a problem. Just remeber to not only turn the machine of, but also disengage the cartridge by putting it in the lifted position.
Probably had seen others do it (where it was actually necessary), asked why, then started copying the ritual. Cargo cult in other words.
This is an example of how misogyny and societally-reinforced ideas of gender norms hurt creativity and stifles everyone (the person being stereotyped & the stereotypers). Assume everyone is capable of anything, wait to be proven wrong, and break the cycle of judgement/profiling. It’s freeing.
your failure to mention the microaggressions has left me triggered without a safe space in sight!
Not only do you fail to address my valid point, but you somehow manage to construct a narrative around topics I made no mention of. Consider thinking critically about whether profiling “old ladies” as technically inept is benefits anyone, and then perhaps attempt to reconcile my comment with your attempted insults. It’s extra laughable to profile old ladies as technically incompetent when you consider the history of computer science (and science in general). Attitudes that mock attempts at self-reflection are a reason for hostile environments toward women in STEM fields.
Blowing on “the connectors”, and i assume you are refereing to NES cartridges, worked because the humidity that stuck to the contacts worked to increase conductivity. Easy fix thus thats why. It had the horrible side effect of speeding up the corrosion and buildup on the contacts though.
Eraser may have been best back in the day, but now i wouldnt recommend it. I got my hands on some old cartridges and went at the first one with an eraser after 30 years and the eraser took off some of the contact. Electric contact cleaner i had on the shelf originally from radio shack did nothing for the bulk of the buildup on the other cartridges either. On a guess i tried soaking the contacts in windex and they shined like new after a firm drying/wiping off with papertowel. Windex(ammonia) is my goto now for any contacts that can be soaked and rubbed with a cloth after.
can confirm, I used to give every single one of the bare copper pads on my circuit boards a go with an eraser before OSHpark started putting ENIG on everything. now I only need to break it out if a board has been sitting for a while. physical ( as opposed to chemical ) removal of foreign debris ftw!
Ink erasers work best because they’re a bit harder and grittier. After the eraser, I use a Qtip soaked in alcohol to remove any remaining dirt.
And when all else fails, I use a model railway cleaner stick/block. They’re abrasive so use with caution.
Felt like there was a revelation or “The Answer” coming up. Instead found was being walked down the chemical aisle at a hardware store… and then asked what I would do.
Was given a “dead” Canon Powershot s100 with the dreaded “lens error” … swapped the lens and … well, not much – lens error gone but the camera still wouldn’t fire. A quick research on Canon’s user board revealed that this was a common problem with this camera (list price 449.00 at the time). As it turns out, you had two options: A) a USD 160.00 repair by Canon or B) a single drop of Caig DeOxit on a micro switch.
Because I treated myself a while back and got a whole whole assortment of Caig Labs products, I chose the DeOxit solution. Worked like a charm and the investment paid for itself instantaneously. This stuff is impressive and I prefer it over the more aggressive “Teslanol Oszillin T6” (yes, that’s a real product) which is the standard over here.
Dust and carpet fibers were the reason for blowing, not corrosion. First duty is to blow out the connector or switch. I use full pressure shop air form a slender non OHSA blow jet, fits into all kinda slots and tiny spaces in “sealed” pots and switches. At this point a lot of problems disappear. Spray chems first and you will make soup inside and then have to get all of that with my next weapon. A modified air gun with a coaxial brass tube going into a little bottle of naphtha or alcohol or whatever I need, beats the pants off any spray can and cheaper.
Airgun?? Doesn’t it “diesel” with the flammable solvents?
vinegar, slightly heated if the oxides are persistent, clean off with alcohol.
white vinegar is preferred but most vinegar will work in a pinch, cleaning is more important if you don’t use white vinegar.
in theory any acid should work but white vinegar is cheap and readily available.
i never heard of the eraser trick, i will have to remember that, sounds nifty.
Yup!
Depending on the situation, I’ve had to use fine sand paper on contacts and apply a really thin layer of conductive grease. That pretty much eliminates any future oxidation.
For automotive applications under the hood and especially in areas subject to spray, salt, water, weather, cleaning the contacts of the connector best you can, tiny wire brush, even a point file at times, then overfill with silicone dielectric grease, reconnect, wipe away excess grease so it won’t hold dirt. Doubt you’ll ever see a gold plated connector, just plain copper with green and black buildup to remove. Try to leave shiny copper surfaces rather than all roughed up but there will be compromises. Same procedure is used to clean up and waterproof motorcycle, jeep, and atv harness connectors for those making river crossings. Easy to be successful here… fill connector with grease!
Never understood why EVERYBODY who makes “water proof” connectors downright refuses to use gold plating… best you can find is usually nickel plating…
you can find a lot of the connectors used in RC in gold plated versions, we use some for our primary power distribution in our largest multi-copter, it pulls around a hundred amperes continuously.
After using DeoxIT cleaners and enhancers for several jobs, and reflecting back to the days before I broke down and bought some, I absolutely recommend them to anyone who needs them. Other fixes and sprays may do similar things, but DeoxIT has always delivered results, and fast. That’s worth its weight in gold. Spend the few extra bucks. Buy one of the small size(s) if you can’t afford the big size. A little bit goes a very, very, very long way, so unless you’re using it daily, the small sizes will last a very long time. The DeoxIT website is very informative, which is a plus as they have a number of different products and variants depending on application.
Speaking of solvents and sprays, I’ll give another plug for Kroil for getting seized and stuck connections (bolts, nuts, axles, etc…) loosened up. Again, there are a number of other products that do similar things, but the time saved by going with the best more than makes up for the price difference (if any) over any of the competing products.
IMHO, DeoxIT and Kroil are must-haves on a professional workbench!
Hmmm with some inspiration from here and gut instinct (Refined by years of experience and knowledge accumulation.) ima try 10% olive oil, 50% mineral spirits or varsol and 40% IPA ….
Vinegar + hydrogen peroxide = peracetic acid.
Wipe on or dip copper with oxide or verdigris (they are chemically different) coatings and you will end up with the brightest copper surface I have ever seen. Wash clean with deionised water. Try on some scrap first until you have a feel for how it behaves.
Don’t use concentrated solutions of acetic acid and hydrogen peroxide, and never let the solution get hot. Don’t ask, just never do it!
Why thank you! New tip! Try it out on the bike harness soon as it gets warm out! Just what I was looking for. She’s getting old.
As you’d know, use gloves and dispose of wastes appropriately.
The safety sheet for the end product that is rinsed off is here, http://apps.wku.edu/sds/uploads/docs/2839.pdf
For non-electronic use (braze welded joints) copper-based alloys can be chemically cleaned with a mix of ammonia solution & table salt (DON’T DO THAT INDOORS! … or use a fume hood!). Had good success with carbide-tipped tools where the brazing had corroded during transport…
I don’t generally need to clean connectors but for the water-damage sort of oxides on electronics , I use a toothbrush and CLR followed by generous rinsing with maybe IPA and lots of water followed by a long dry time or less in an oven. Yes it’s an acid cocktail, I try not to take very long :P And since moving to the country where they have a cistern, my coffee maker is getting sluggish– time for that other legit usage.
Well here in Canada a few summers ago the Federal Government said that it has been proven that Freon does NOT affect the Ozone layer. It was all bunk all along.
But it is still illegal to fiddle with it……
Link please
I knew it! (Thanks, Al Gore!)
Actually, I did. It never made sense that these stable and heavy chlorine compounds would be banned, whereas other chlorine compounds that were volatile, such as bleach, were not.
According to a colleague at the time, the real agenda was to get rid of such compounds whose patents had expired (hence ubiquitous and cheap), and force the switch to newer alternatives with newer patents (hence much more profitable).
[Citation Needed]
i found CorrosionX works great on contacts. Found it during my time in the navy working on connectors in salt spray. And PBblaster is a great penetrating oil.
Dichlorofluoroethane if you can find it also1.1.1. trichorotrifloro s y c l i n e [sp] ???
I still have a full bottle of the first stuff, the second stuff long gone…
R11 is liquid freon sold by gallon or drum non pressurized, though not available for purchases to the public, however I think you can drain it out of old compressors sumps in fridges A/C units etc I believe it was used in conjunction with R22 and or
R12 to lubricate the compressor…
A reply to Carl above, true but only because it is about 150 degrees Celsius too cold up there…
Anyhow today I just use the deoxit stuff…
later
PS if you browse the ham radio shows an whatnot you mite find some hard to get chemicals from above an other posts…
Ordinary pencil eraser also has the advantage that it can be cut in any shape, then used in places hard to reach, e.g. the interior of a BNC: https://hackaday.io/project/7574-the-devil-is-in-the-details/log/26489-a-pencil-eraser-trick
Paper and IPA. If stubborn a bit of white, simple toothpaste and a wash with IPA.
Nice read.
“This one is quite good, seriously”
True but pencil erasers often are too soft to be effective in polishing contacts. I got much better results with pen only (harder) erasers and excellent results with even harder round/polygonal typewriter erasers. They’re also perfect for cleaning pcb tracks, but make sure you remove any rubber traces left with some alcohol.
I use pink erasers. A bit more aggressive than the white erasers, but a lot less aggressive than the sand-filled ink erasers.
I worked at a place that among other things manufactured flexible flat copper conductors. The raw material was about an inch and a half wide and insulated with a clear flexible plastic. The ends were flame stripped by a machine and than humans would use those motorized drafting erasures to remove all of the smakn after the flame stripping, leaving a bre bright copper surface. After that the ends were machine punched into a circular shape with a hole in the center, and than tinned. It was interesting that the clean up process was totally human driven. Machines (at that time, mid 1980’s) could not ensure that the ends were clean and bright..
Using solder wick works great. It’s about as hard as copper (either bare, gold, nickel or bronze plated), but a way harder than the oxide, so it’s able to remove the oxide without causing too much damage on the traces or connectors.
Another thing is to prevent the oxidation. I sometimes “waterproof” automotive connectors with silicone sealant. Silicone oil is also nice for avoiding oxidation on edge connectors.
You have to be careful which silicone caulk you use. The stuff that smells like vinegar before curing will oxidize metals like mad. Get the automotive variety, then you are sure to get the kind that won’t eat metal.
Good to know, I’ll pay more attention next time. Hopefully I put two layers of heat shrink tubing over the crimps, but I did really use the vinegar-smell caulk that I previously used in my bathroom… I guess there should be no oxidation problem once it’s cured and airtight.
I searched for a replacement for Freon TF, (which is without equal for precision cleaning or de-fluxing) and found 3M Novec “Flux Remover” is a pretty close match. It’s really expensive (probably less per ounce than Caig products), but when you need your boards to be really really clean, there’s no substitute.
1,1,1 Trichloroethane was the best thing ever made. They quit selling it in the early 2000’s but an acceptable substitute Trichloromethane. Also known as chloroform, can be easily made at home with the haloform reaction. https://www.youtube.com/watch?v=7ilKvNmPDy8
And it should be mentioned that trichloromethane, especially the bootleg DIY variety is not something you want in your house… prolonged contact causes all kinds of bad things and if exposed to oxygen long enough, it slowly produces phosgene, which is also “fun” to be around…
Hey, does this rag smell like chloroform?
i have worked with all sorts of diffirent types of cleaners and other methods. the best thing i have used is this industrial electrical cleaner called 279. it is awesome for any type of corrosion or liquid damage, have recovered at least 40 phones with this stuff. http://chestertonlubricants.chesterton.com/en-us/Products/Pages/279.aspx
Strange how no one has mentioned Super Contact Cleaner by MG Chemicals. The old radio restorer guys seem to swear by it. Cheaper than DeoxIt and more effective they say, especially for pots and switches with no easy access to the contacts.
DeoxIT D5 Spray is only $9.99 at parts-express.com & $14.99 at markertek.com with free shipping. DeoxIT is the product used and spec’d in by big companies like Boeing, HP, Xerox, Honda, Ford, Yamaha, Bombardier, UPS, Motorola, Logitech, etc. so it’s the best contact cleaner in the market.
KF F2 anyone?
FWIW, windex(ammonia) is my go-to for cleaning nintendo cartridges with 30+ years of build up on the contacts. Has worked flawlessly every time where a commercial electric contact cleaning solution has failed and an eraser has been too abrasive. Soak for 10+ minutes and rub dry firmly with a papertowel and those 30 years of grime come right off leaving shiny contacts that work.
Great for cleaning off years of spit from cargo culters blowing on the cartridge.
I have used DeoxIt, but as you told, it is expensive. Worth the money though.
Not to mention I have been using Deoxit and Radio Stack. Both of them have worked for me, but on the money side I would go for radio stack for cleaning purposes.
I have a can of radioshack “cleaner and lubicant” that is at least 10 years old, probably 20.
It has always worked well. I just looked on the radio shack web site and it’s still for sale, the can looks identical.
I downloaded the “saftey data sheet” and low and behold it’s made by caig.
It lists the ingredients and they are the same as caig except instead of the magic DeoxIT it contains dimethicone.
I wonder if that is what DeoxIT is???
BTW, the radio shack stuff is cheaper.
I have been using tarnx to clean audio connections. I first wipe with tarnx (using a pipe cleaner) and then rinse with plain water (wet with water pipe cleaner) and then wipe dry,
The “freon” was S-711. A “halogenated fluorocarbon”, whatever that was. Sounds smelly! Regards.
I tried and compared an oleic solution and deoxit. I applied to several types of connectors. At first it seemed to work OK. After about six months the oleic solution treated parts, the plastics seem to get soft. On one RCA connector, it broke apart when I tested. The Deoxit treated connectors were all fine. For me, don’t want to take the chance, especially when I use on expensive or sensitive equipment.
Just an FYI
Oops, forgot to add – if oleic is in it, must have something else to neutralize its effects.
To eliminate sparking of contacts that cause most contacts to get dirty use NO OX ID special A, a conducting grease that has been used for over 50 year in naval applications on ships and on model railroad track to keep them from sparking and clean forever.
An alternative to just cleaning -Chemially tin coating.
Copper-to-brass contact between circuit board fingers (copper) and socket contacts (brass) will scratch away at the copper promoting more and faster corrosion as fresh surface is continually exposed with each mating/extraction. If lots of pugin/pugout cycles are expected for a circuit board then a better plan is to apply a sacrificial coating that can be replaced periodically; tin is a good choice, and its cheap!
Tin is softer than copper so the eraser cleaning method will remove much of the damage done to tinned circuit board finger surfaces and a quick re-treatment will repair any deeper scratches.
See this utube video for a cheap recipe and demonstation –
https://www.youtube.com/watch?v=Hsw3lOnHaas
bye.