Powerful lasers get powerfully hot and if you don’t keep them cool you’ll pay the price. After two such experiences [NixieGuy] got smart and milled this flow sensor as a failsafe.
Laser cutters are awesome. But acquiring one can be expensive, and keeping them in working order is no small feat. From the gunk that builds up as a byproduct of vaporizing the cutting stock, to keeping the optics focused correctly, it’s a game that forces you to become a laser cutter operator and not merely a user. One of the worst things to deal with is having to replace a burnt out laser tube. They do have a life to them but in this case the filter on the water cooling system clogged and the tube cooked itself. Twice.
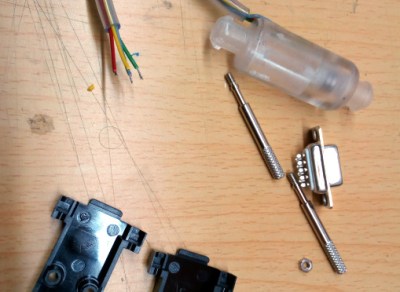
This flow sensor now acts as an interconnect with the laser enable line. Starting with an acrylic rod, [NixieGuy] machined out a center hole for a magnetic stopper, then milled three channels for water to pass around it. Each end of the rod was turned on a lathe to interface with plastic tubing of the water cooling system, and a slot was milled on the outside for a reed switch.
The demo video is below. You can see that when water flows it pushes the magnetic stop up (against gravity) where it engages the reed switch, allowing the laser to operate. If something impedes the flow of water (even if the pump still runs) the laser will be disabled and (hopefully) prevent future tube loss.
Want to see some of the oops moments faced by many a laser cutter operator? Check our guide on how to fail at laser cutting.
[Thanks for the tip George]
A good safeguard, but it seems to me the solution is to just clean the filter after every [x] hours of machine time. An ounce of prevention and all that…
Pumps fail, hoses split, tanks run dry… A clogged filter is only the highest probability failure item, but lots of others can and do occur.
On the failures I’ve seen, no 1 was “cable got disconnected to power pump”
Engineering safeguards are orders of magnitude better at preventing a scenario than procedural action. This is why we have safety systems in the first place.
very nice, thanks for sharing :)
Is temperature monitoring of the coolant around the tube impractical in this situation?
I’m surprised even cheap modules don’t have a thermistor on them.
This method does provide a more immediate stop though.
You could do it, however, the actual cooling path is inside a glass tube, so you can either monitor the exit temperature (wich, with a stopped pump might not raise the alarms until it’s too late) or put a probe inside, but that could restrict flow or worse, create a hot spot.
Just making sure the water flows is easier.
HOWEVER, I do monitor the temperature of the water tank (45L) and have a cheap temperature monitor for all year round, using the beer cooling circuit for summer and 2x1000W water heaters for winter.
Nice hack, but I just used a $4 Hall effect flow sensor – has been in use for the last two years with the lasercutter at my local ‘space.
I had the acrylic around, magnets and reeds, so, it was even cheaper than that. XD
XD? Are you old enough to be operating a laser cutter?
Nope!
/runs away making airplane noises/
Yeah, this. The Chinese flow-sensors are practically free on eBay and I use one to make sure that the coolant is flowing through my CNC router. Trivial code for it here: https://github.com/phenidone/flowmonitor
I’ve been thinking about a solution to this as well. I’m thinking a large leafswitch which is hit by the water returning to the basin. Once hit, it triggers a 110V solid state relay to power the laser. Simple. Waterproofing the leafswitch innards is the only challenge.
Flow switches are just too cheap to mess with anything else: https://www.amazon.com/uxcell-Thread-Sensor-Flowmeter-0-75-3L/dp/B00HR7KQEE/ref=sr_1_28?ie=UTF8&qid=1506820190&sr=8-28&keywords=water+flow+switch
Nice! I used to have a similar setup, but found this approach difficult to keep running reliably with low flow rates, as the small plug could sometimes get stuck in place. To improve it, I made what is essentially a cork with a magnet floating in a cup with a hole at the bottom. It’s largely the same thing, but can move the magnet with much more force because it takes advantage of the accumulation of water over a few seconds instead of just its instantaneous flow rate.