It’s been a few years since we first started hearing about “tools of the future changing the way we work” but this astounding whole-room floor inlay might be the best argument for them yet.
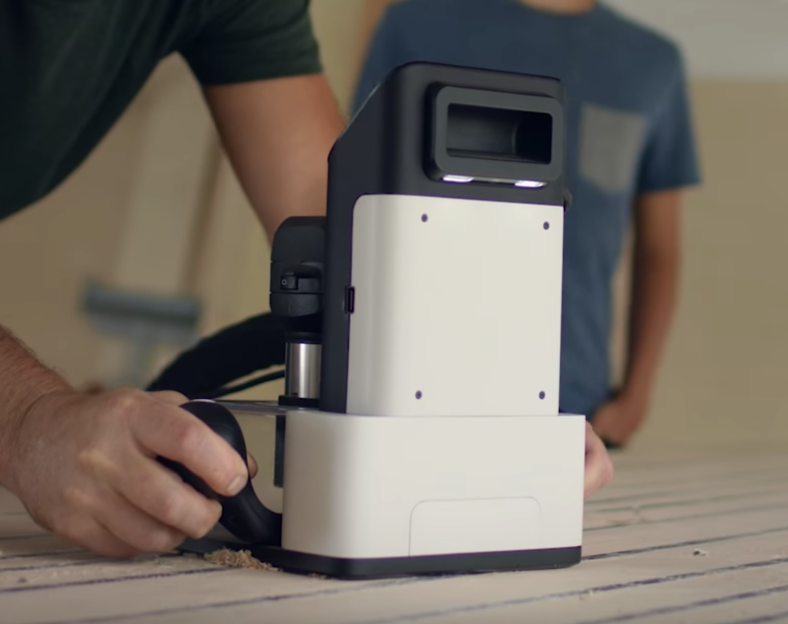
A couple of years ago we wrote a hands-on preview of a unique tool called the Shaper Origin. If a milling machine is classically defined as having a stationary tool head with moving stock, the Origin is the reverse. To use an Origin the user adheres specially marked tape to the stock material, then holds the origin down and moves it much like a hand router.
The Origin has a camera which tracks the fiducial patterns on the tape, allowing it to know its precise position, even across an entire room. The operator sees a picture on the screen of the tool that guides them with superimposed lines, while the tool head makes its own precision adjustments to perfectly cut the design in the X, Y, and Z.
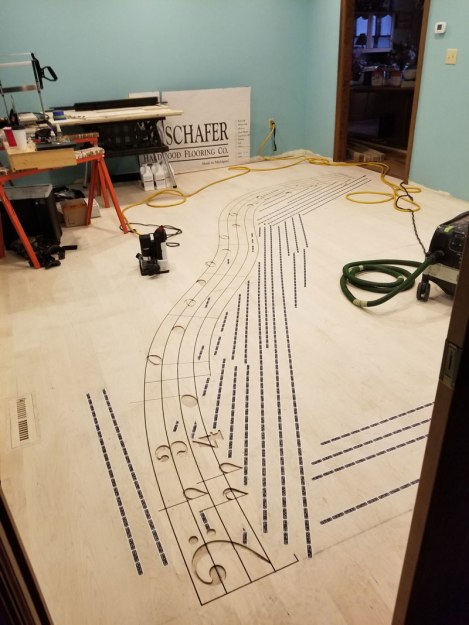
But what do you use a tool like this for? Cutting boards, small tables, and toy blocks are fine examples but don’t highlight any unique features of the tool. Many could just as easily be made using a ShopBot, X-Carve, Carvey, or any of their ilk. What you can’t do with any of those tools (or really anything besides manual labor, endless patience, and master skill) is inlay an entire floor in situ.
[Mark Scheller] (eight time winner of Wood Floor of the Year awards) used an Origin to cut a curvaceous 22 foot long rendition of the first 9 bars of Handel’s Passacaglia into the floor of a lucky homeowner’s music room. Without decades of practice, it’s difficult to imagine doing this any way besides with a Shaper Origin. You can’t put an entire room into a CNC router. The individual floorboards could be cut, but that would be tedious and increasingly difficult as the room gets larger. With the Origin it seems almost trivial. Do the design, place the marking tape, and cut. The same model is used to cut the inlays for a perfect fit. This is an incredible example of a unique use for this unusual tool!
Truly beautiful, and a perfect application for this unique tool.
I hadn’t known that the spelling of “vaporware” had changed to “unique”.
Shouldn’t this thing be selling at home Depot for ~$800 by now?
Brilliant! Something tells this wouldn’t look as great on my lino floors though…
There’s only one way to find out!
Never mind the computerized router, I’m blown away by the fact that there is a ‘Wood floor of the year’ competition!
NWFA hosts a large convention in some exotic location every year, where middle and upper class business men come together to drink, play golf, and visit strip clubs. I know because before I was an engineer, I was a wood flooring construction worker, the best detailed installer and finisher for the company I worked for.
“This is one of those moments. The world of tools is seeing a new change, and I think this is the first of many tools that will change the way we build.”
So did it change the world as much as the original article thought it would? And how about that “many”?
it didnt change the world and it wont unfortunately. the problem is that this brings a whole other set of skills into the tool chain. This requires someone to actually be willing to take a crack at 3d modeling and while this design is simple, that extra step alone can prevent people learning to use this tool. I think that its a flaw that is becoming prevalent in product designers, they understand that there is a subset of people who are interested in 3d modeling as well as a separate subset into wood working but they overestimate the overlap between the two groups.
This technology has been around for at least a few years in commercial form. I am glad that someone found an appropriate use for it but there is really no mass market for this product.
If I’m not mistaken, only a simple 2D program would be used. Also, most common functions, like mortise/tenon, dovetail joints, simple shapes, text, etc can be done on the tool so a PC isn’t even required unless you want to do some custom stuff like this musical bar project.
I’ve never seen anything like this in commercial form, maybe you could link to one? This is significantly different to CNC routing tables like the Xcarve.
This definitely isn’t a mass market product, but I don’t think anyone said it was. It hasn’t even been fully released yet to tell how much of a change it will make either. They’ve just been doing slow limited release “presales” to fully test the product. A great sign.
At that massive price point, adoption will be slow, but still notable. Consider the popularity of overpriced Festools. If the price ever drops, or they get competition, I have no doubt you’ll see them everywhere.
Beautiful work. I am floored!
There are other ways to do it.
You could use a cnc to cut a series of templates that you followed with a normal router and guide bushings.
This isn’t that hard to do using more conventional tools though. Cut a wood stencil (in pieces with alignment notches) on a CNC router table or by hand using a jigsaw if you’re patient, then place it down on the floor (with some sandbags to keep it down.) Use a Pattern cutting bit of the appropriate length in a conventional router to trace the design. Yes, this is more convenient and I see the benefit of having this new tech but to say it would be impossible using traditional means is a bit of a stretch.
Ok, that’s a great point!. There are definitely ways to do this that we didn’t think of. Still seems like a great application of the Origin though.
Could do with hand tools as well, though it might take a little longer, since the workpiece is significantly large.
Would LOVE to see you try.
Truth is, it’s hard with conventional tools even if you have the skills. Alignment from one end to the other and just creating positive and negative jigs resulting in a ‘suction fit’ is very difficult. It requires not just skill, but time.
Doing the same job with conventional tools wouldn’t be impossible, but doing it within even close to the same time-frame and skill set would be impossible. For example, a high school kid could probably layout and cut that floor, along with all the inlays in a day with the Shaper. A 30 year pro with all the ‘conventional’ tools, might take a day just to create the jigs.
I don’t care anymore if the origin is that good. They still aren’t able to sell them anywhere outside the US. It seems to me, that most of their effort goes into marketing for a product thei do not sell. They even were in Germany showing it at a woodworking faire, allthough they don’t sell it to Germans. They should stop this BS and start delivering.
They haven’t really started selling INSIDE the US either. They’ve gone through about a dozen major revision changes and filed at least as many patents. They appear to be trying to build a company and sell a quality product instead of the typical start-up model (juicero, nest, etc) which attempts to build a product to sell the company. Other than Hackaday, I don’t see them marketing it much, just gathering feedback from testers.
what did he fill the floor with once it has been carved out?
The floor has ebony inlays set into the maple flooring. That’s what makes it so dependent on precision. It’s not just ‘carve a shape and fill it with back goop.’
It’s not just ‘carve a shape and fill it with back goop…
Thats not an invalid pathway to an ebony inlay though.
Release coat, Black goop, cure, remove pattern, pantograph ebony inlays and install.
So does the origin also cut the inlay from stock material to precisely match the new floor?
Good question… It seems like it could if you had the inlay in sheets large enough to fixture and cut?
Yes. The artist even talks about how he adjusted the gap for a suction fit.