RCExplorer, or [David], or just ‘The Swede’, has come up with a bicopter kit. Yes, there are a lot of people making frames and kits for quadcopter, multicopters, drones, and so forth, but [David] is really the leader in weird multicopters. Now, we have the weirdest multicopter imaginable as a kit, complete with firmware that works.
[David] is one of the great unsung heroes of the drone and multicopter world. He’s famous for rocket knives, even though that really doesn’t have anything to do with drones, he bought an airplane for his front yard (again, little to do with drones), he was one of the first to take a glider up to 100,000 feet with a balloon, and he’s been one of the main forces behind tricopters as a superior — or at least cooler — platform for aerial acrobatics and camera work. There’s a lot of work being done to the various firmwares to support tricopters, and we have [David] to thank for that.
Like [David]’s earlier tricopter kits, this frame is made entirely out of carbon fiber plate, square tube, and threaded standoffs. It also looks like batman’s drone. The firmware — the real trick for a bicopter — is stock betaflight, and there are a few problems with the stock firmware. The bicopter doesn’t like flying backwards, tuning is fiddly, and it’s harder to fly than a quad on rails. That’s to be expected with a platform as weird as a bicopter, but this kit does open the door to firmware developers hacking and making the bicopter features better.
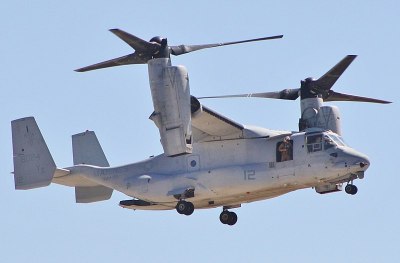
While pure bicopters are great, the release of what will surely be a popular bicopter with a good community of firmware developers means the door is open to a simple VTOL fixed wing, not unlike a V-22 Osprey.
Remember, San Francisco tech bros, if you need a delivery drone, you need three things: long range, VTOL capability, and payload capacity. A quad or hexacopter will not get you there, and fixed wings will give you lift for free. There is no Moore’s Law for batteries, and right now if you want to ship a bottle of shampoo 20 miles in 30 minutes, the way to do that is with a drone that looks like a V-22 Osprey. Please, delivery drone bros, learn physics, use a tilt-rotor, and learn to put the battery in the wing. This is how you found a company that will get an easy $100M valuation.
Wing lift is hardly free. It adds induced drag as well as increased skin fiction drag.
That said as cool as this is the reason we haven’t seen it much before is because typically engines sized for VTOL are very inefficient for cruise once the aircraft has transitioned to level flight.
As batteries increase in specific capacity and electric motors become more efficient this type of electric hybrid aircraft may become more attractive. It will be interesting to see.
The main reason we haven’t seen it much before is mainly because the V-22 program has already claimed 30 lives just during the testing phase and an additional 12 in operational use. Not sure if they finally rated it safe (enough…) for use on high state officials :D
Until someone builds a convertoplane that is at least as safe as a normal helicopter, they will remain unseen and unheard of.
To be fair, most V-22 crashes have to do with the wing folding (technically rotating) mechanism, especially the controls that run through it. If the V-22 didn’t have to fold up to pack tightly into an aircraft carrier, it would have a much better safety record.
“If the V-22 didn’t [have legitimate operational requirements] it would have a much better safety record” is probably the hottest take.
That’s a little harsh, a tilt-rotor which didn’t fit into a carrier would still be a useful plane. The carrier bit was probably what meant they allocated budget for it, but it’s not essential to a useful tilt-rotor.
Has there been any v-22 crashes that have anything to do with the wing stowing capability? No, there hasnt. What controls run through the rotatey wing from the cabin? Are you talking about cables and pulleys? Its just a bunch of wires, fuel lines, and air that pass through the rotatey part, and there is a shit ton of redundancy.
And Id challenge you to back up your claim with sources snce what your saying is simply not true.
There was a fatal crash involving an oil leak in the engine gondola. When the engine tilted to transition to horizontal flight, that oil got dumped unto the motor, which caught fire and then failed. Sorry no sources but I am sure it is online somewhere.
There are hydraulic lines running through the rotating part of the wing to/from the engines. The rotating mechanism massively cramped the internal layout of the wing. There has been one crash and two fires caused by hydraulic leaks in the wing or engines. You’re right that this isn’t “most crashes” overall (which would be pilot error), but that is a large share of the unprovoked mechanical failures. Here’s a good article on how badly the requirement to be stowed on a carrier compromised the design of the V-22:
https://www.wired.com/2011/10/osprey-down/
@Tadpole, yes there was a hydrualic fitting in the engine compartment that leaked and pooled up in there, and after they transitioned it did cause a fire which resulted in the crash. Since then, they rerouted where those hyd lines go and removed that style of fitting. The only hyd line that goes in the engine compartment at all is the engine starter and there is a valve outside the compartment that controls flow. The book The Dream Machine details this.
@GameboyRMH, no, thats not how it works. All the hyd pumps and lines save the utillity system for the landing gear and such are located in the wings or nacelle. The lines only rotate from the pumps to the engine starter (the only external hydraulics going to the engine compartment) via the swivel going from the wing to the nacelle.
And yes of course, design constraints constrained the design to what they needed to be, but to say it compromised the design is not fair. It needed to fit where it needed to fit so they so had to do some engineering magic. Its not a perfect design by any means, but it sure does work mighty fine. One crash and two fires due to hydraulic fluid leaking over the number of years its been in test and operational use is hardly significant. I would have you look up the deaths involved with the ch46 and ch47, and see how the osprey compares.
The v-22 has had its problems, just like many other new aircraft, and most likely will have some more before it gets retired, but its a damn fine aircraft and its a shame to see all the slander on the internet for this success story.
Of course, the reliability requirements for an uncrewed delivery drone are less than for carrying high state officials.
You will only say that until you get hit by one…
Still not remotely as risky as developing an actual manned aircraft.
For me the value of most my packets is higher than that of many state officials.
Despite what people like you say all the time, the V-22 is an amazing machine that brings a capability like no other currently in our inventory. Much like other aircraft, the v-22 had a rough start and mistakes were made by engineers and aircrew alike, but the current state of the aircraft is pretty safe.
In 2013 a few cv-22s caught a few hundred rounds between them and were still able to fly 500 miles and land safely. https://breakingdefense.com/2014/11/mackay-trophy-for-afsoc-osprey-crews-a-tale-of-bullet-riddled-planes/
There has been a few crashes in the past few years, and most of then can be attributed to poor choices or poor training. Its a proven machine that isnt going away anytime soon.
This has the potential to be more efficient than a quads or tricopters: Fewer propellers are bigger propellers for the same weight which are more efficient.
Actually it has more to do with the total amount of rotor area available and (hence) the disc loading. In forward flight there is a tradeoff to be had because you are also dealing with inflow damping. I could go deeper into this if you like.
If HAD is interested, I’ve had a long career developing some of the fundamental technology of drones (rotors, motor control, flight control) and still hold some records in efficiency and endurance.
Cool! You should ask to do an article on it!
There seems to be some interest, so I’ll see what I can do. At the very least, talking about my research will provide an excuse as to why my next pocket watch version is taking so damn long… (It’s only been 10 years!)
I’m stupid interested!!!!! This is awesome
Absolutely!
And when you do write it up… https://hackaday.com/submit-a-tip/
Hi Pauline,
I’m a student currently undergoing a project in Bicopter / Tilitrotor aircraft.
Researching, designing, manufacturing and testing a drone model is the plan of the project.
And I was wondering if you could share your research and help me along with this project.
Thanks Anthony (chiuanthony2001@gmail.com
Was it hard to fly around and if you are a 1st timer do you need practice for this drone
Interesting view Jonititan! My senses tell me that having 2 engines and wings must be more efficient than having 4 engines running… However, with regards to motor dimensions : high power for VTOL and less powerful for wing flight – Isn’t it so that those brushless motors with an efficient inverter have a constant efficiency regardless of output power? If so; the inefficiency (difference in motor requirement VTOL/wing flight) would be mostly the size of the engine?
It really depends on so many things its difficult to say. Kerosene has more enery per unit volume or mass than batteries have currently. It is not converted at a 100% into Thrust. I think that is more like 30% but it is still better. It also has the effect that as fuel is used up the aircraft is continuosly getting lighter. Lighter means less lift required which means you can trim the aircraft to generate less lift for the same speed which means less drag which means less thrust required which means less fuel. The Brequet range equation implies fuels that are consumed as they are used will always have an advantage over batteries.
That said I can definetly see a niche for short range electric hybrid aircraft. Hybrid in the sense that they are not pure planes or rotorcraft. Ttiltrotors, tail sitters, gyrocopters, etc
Ill preface this with “I literally have zero experience with Flying RC” and “Using experience working on cars” so I’m probably completely wrong. If you are using a gas engine though you always have the weight of the gas tank, fuel pump, pipes, hoses, carbs and associated bits and bobs that are required to get the gas conditioned and transported into the engine. As long as your batteries weight is less than all of those parts you should always have an advantage over gas ya?
Well, that MIGHT be, if it weren’t for the fact that the energy density of gasoline or kerosene are orders of magnitude higher than for the best batteries.
For RC, the simplicity and cleanliness of electric is a main reason also, the power density of lipo batteries and brushless motors is good until you try for long flight times. Noise of electric is also a bit more tolerable.
Having flown RC glow engines years ago and now flying some electric, it is a welcomed change. As you mentioned fuel requires a heavy engine, fuel tank, dedicated electrics battery, the motors run “rougher” so the airframe needs to be sturdy, coatings on the airplane need to tolerate the glow fuel oil for small planes, the power output of gasoline small engines (10-20 cc) per weight is not much fun/performance.
Nitro glow engines start showing good characteristics of power/weight/flight time at about .40 cu inch. but the plane ends up being 50″ wingspan
I can have a less than 30″ wingspan on electric and still have an enjoyable plane.
Not to mention the cost of fuel engine is 3x of similar electric (battery, esc and motor/prop) can be purchased for significantly less than the motor. And for nitro engine, the fuel is $25/gal.
“There is no Moore’s Law for batteries.” Well, maybe there should be. Energy density, current capability, and number of charge cycles have been steadily increasing since cell phones arrived on the scene. Now that electric vehicles are becoming more than a novelty, batteries can only get better. The Moore’s Law equivalent for batteries may not run for as many decades as the original, but there’s just no way to know.
Hate to say it but I’ve seen at first-hand ‘working’ patents for battery tech bought up and sat on by some of the big companies. I wonder why they’d do that!
Probably because they were only ‘working’? There are many theoretical advances with demonstrations that can’t be made into a mass market product. Some of those goes to some specific market where the disadvantages aren’t relevant or where the buyer don’t care about the costs (military mostly).
Most of the “new battery breakthrough” patents are related to improving a single aspect of the battery, which doesn’t lead to any real world applications because some other parameter suffers. Things like renewable energy or batteries are today’s diploma/paper mills where career researchers can spend their years doing essentially nothing, because the interest in these technologies is so great that even a tiny insignificant “advantage” like making a solar panel 0.1% more efficient (and 100% more expensive) gets people throwing wads of cash at you.
There are many battery patents that go nowhere, but GM had a good thing with the NiMh battery before they sold the patent to Texaco, who then refused to license it for any battery large enough to be useful in an electric car.
They’re heavier than lithium, but when Panasonic licensed the technology to make batteries for Toyota (prior to the sale to Texaco), the result was a 100 mile range RAV4, many of which are still running 20 years later in spite of the lack of replacement batteries.
The GM/Texaco patents were only valid in the US, and weren’t of the actual chemistry but the battery format. The rest of the world still had free use of NiMH batteries in EVs, and they did try to use them, but in the end they only managed to prove that GM was right and NiMH wasn’t the solution that would bring EVs to the market.
>>” many of which are still running 20 years later in spite of the lack of replacement batteries.”[/q]
NiMH batteries are nearly indestructible when treated right, which is why Toyota used them in the first Prius, and which is why they’re not using them anymore (planned obsolescence), but that’s their only good point. NiMH has high self-discharge, doesn’t work in the cold (sub 32 F / 0C), the discharge curve is eccentric so it’s difficult to measure the state of charge (poor range estimates), and it develops hydrogen gas when stressed.
Some of the older Citroën Berlingo electric vans sold in the EU have caught fire because of their nickel batteries leaking hydrogen into the cabin.
Disc Brakes that never wear
Water powered engines
Various other stuff
100 mile per gallon secret carburetors! Use the generator to get hydrogen from water to “energize” the fuel.
I have never seen an actual case of the squirreled away tech or planned obsolescence. There is too much competition in the world to hold back advantages. There is cheaper stuff that doesn’t last as long, because there is a market for cheaper stuff. The paper drinking straw is made for one use (if that). You can buy a stainless steel gold plated straw, but where do you keep it?
Long life [light bulbs,tires]
Conspiracy theories all. The sad truth is that the laws of physics simply don’t like us very much, and seek to frustrate our dreams.
But that’s only natural. Anything physics makes easy, we take for granted. It’s the things that are on the edge of impossibility that we really desire.
Yeah, none of those things actually exist.
What do you mean? I have several disc brakes that never wear water-powered engines.
Any “Moore’s law” is just wishful thinking, because it’s suggesting exponential growth without regards to real world limits.
So yeah, maybe there should be, but will there be is up to practical reality.
““There is no Moore’s Law for batteries.” Well, maybe there should be. Energy density, current capability, and number of charge cycles have been steadily increasing since cell phones arrived on the scene. Now that electric vehicles are becoming more than a novelty, batteries can only get better. The Moore’s Law equivalent for batteries may not run for as many decades as the original, but there’s just no way to know.”
So there are a couple of problems here.
First, any manufacturing law is going to run into fundamental limits. Obviously. The version of Moore’s Law that was “transistor density doubles every X months” obviously runs into atomic limits, and so how long that Moore’s Law could run just depended on how far away from that we started, and how fast we were increasing the density. Obviously you’re not going to hit that fundamental limit, but knowing it, you could guess where you’d run out of steam.
Same goes for battery capacity. There’s no way to beat the fundamental limits of energy storage: lithium-ion batteries have a certain maximum energy density, and there’s no way you’re going to beat that. So how long any “Moore’s Law for lithium-ion batteries” runs is again, just a question of where you started, what the limits are, and how fast you go.
So go look at lithium ion specific energy density over time: in fact, there *was* a portion of time that showed roughly exponential growth: from about 1992 to 2002, with a doubling time of about 10 years (from ~100 Wh/kg to 200 Wh/kg). Since then, as you’d expect, the rate of growth has slowed significantly, unsurprising considering the theoretical upper limit for lithium-ion batteries is probably something around 400-700 Wh/kg, depending on the chemistry. So at this point, you’re almost at 75% of the theoretical limit.
Now, it’s easy to say “yeah, but that’s only one battery chemistry,” and that’s true. But Moore’s Law for transistors only really ran up until the point where geometric scaling kept working, and it totally died (to the point where fab companies stopped trying to hit the Moore goals) at optical lithography’s limit.
So there was a Moore’s Law for lithium ion batteries. Problem was that the batteries started out pretty good at the beginning, so there was only about 1 doubling-time in it. And you really can never expect exponential growth across complete technology shifts.
>”how long any “Moore’s Law for lithium-ion batteries” runs is again, just a question of where you started, what the limits are, and how fast you go.”
It’s actually a matter of how often you’re willing to re-define your “law” with a different constant and still pretend it’s the same trend.
The transition from a potential to the actual is an S-curve. Early development is slow because nobody’s interested, and late development is slow because getting the last percent of performance out is infinitely hard. The middle part where everybody’s interested and the discoveries come easily is roughly “exponential”, at least in contrast to the early phase, but by the time you recognize that you’re on an “exponential” trajectory you’re already entering the late development phase and the rate of new innovation is slowing down. That means your “Moore’s law” needs to be continuously adjusted, by which point it isn’t a trend at all but just wishful thinking.
That is what happened to the actual Moore’s Law as well. They’ve changed the time period at least three times so far, and people can’t even agree what the “law” is actually measuring (transistors per chip, transistors per dollar, transistor speed, speed x number, number per area…) with the definition changing between the person you ask, so it’s basically a hype buzzword by now. It exists because people keep saying it exists.
“but by the time you recognize that you’re on an “exponential” trajectory you’re already entering the late development phase”
Yeah, I don’t agree. The technology node scaling (which is really, seriously what Moore was thinking of) was observed back in the 1970s really early on, and that was *way* in the early phase of development. In fact, it could’ve accelerated *faster* without NTRS (and then ITRS), which set out a path that the industry considered sustainable in the near-term. Especially through the 1990s, Moore’s Law was basically a *choice* that the semiconductor industry made.
If this isn’t clear, look at Wikipedia’s entry on ITRS, which shows a roadmap from back in 1993, forecasting forward 14 years, with a Moore doubling every 3 years. The industry actually beat that projection pretty significantly, but you see the idea.
“so it’s basically a hype buzzword by now. It exists because people keep saying it exists.”
I think pretty much everyone would agree Moore’s Law is done at this point, and the “time of death” would definitely be sometime around 2014-2016 or so. Why then? Again, it’s an industry choice – with optical lithography at its limits and EUV not ready, it didn’t make sense to project nodes forward.
The reason “Moore’s law” stuff exists is to allow industries to plan long-term, so I don’t really agree they generally get formulated in the *late* development phase. Most other examples were similarly formulated very early on as well.
Nice. Looks like an ideal starting point for a model Vertibird.
replace the beam with a slightly longer but wide wing,
RC multicopters look cooler and can change direction faster, but why no love for RC helicopters anymore? They’re faster, more efficient and can lift more payload for the same power output.
In regards to deliveries, why not just a plane? Couldn’t an RC plane with enough lift to takeoff traditionally with a heavy package just do a vertical stall and slowly drop the package in reverse? It would rocket up when that weight was released, no?
Helicopters can be maneuverable:
https://www.youtube.com/watch?v=HvOzQLzB-Us
Well if you ever flew a helicopter you would find that automating such a thing would be a daunting task. Sure an RC plane would not be a huge automation feat, but the idea of performing a vertical stall and then “rocketing” up is even worse than automating a helicopter. The control surfaces are very unstable during this and there is just way too many things that can go wrong when performing such a maneuver.
So helicopters are not as commonly automated because it’s harder? Sounds like a challenge I’m surprised no one has taken on considering the advantages.
“Rocketing” up is a side effect of releasing the package. Transitioning from level flight to a stall sounds like the easy part. Just fly up and cut just enough power to remain pointed up. Accuracy of placement would be the biggest issue I see. The idea doesn’t depend on accurately hitting a mark. Just dropping the package…. less fast.
This is not the case. DJI had a autonomous controllers for heli’s 8 years ago with the Naza-H. With how good gyro/flight controller technology is for all forms of RC flight, flying and automating is fairly easy. Landing usually needs the most tuning (but not impossible), which is why most people will take off, switch to GPS control, then take back over when it is close to home.
If we are going to learn physics can we learn that flight is not really a terribly efficient way to deliver anything, particularly not anything “long range”, unless there is no ground transport to that place?
Wheels are very efficient, and not fighting gravity the whole way to your destination is very efficient.
The reason for drones in long distance delivery is for fast long distance deliveries… most deliveries are not going to be fast.
Automation around deliveries is going to happen when automation around wheeled transport happens… and while the final step in the delivery might be a quadcopter carrying the package to a door step, the bulk of any deliveries range should be done via wheels… low resistance highly efficient wheels.
That’s exactly why efficient flight is so important though– if you need a fast delivery you need to fly. If your flight is more efficient, you can travel farther to make deliveries, so your circle of possible customers is proportional to the square of your efficiency.
watched a video of this thing flying yesterday. it has stability issues backing up (really, it has stability issues in general)
it can do most of the motions associated with other multirotors, but everything besides “keep going forward” is going to be super-hairy “oh wow, you managed not to immediately crash when you went into acro-mode!”
https://www.youtube.com/watch?v=9DwcerOzLJw
Rotor Riot just had this on the other day, here flown by pro pilot “Le Drib” :
https://www.youtube.com/watch?v=9DwcerOzLJw
Shoot, didn’t realize the post above was the same.
Last time I saw a video about the Amazon drones, they were already some plane/copter combination: VTOL with the efficiency of lift for forward flight.
I don’t see how this particular design is any more efficient than a quadcopter. It’s not as if it has wings or anything to provide lift while moving forward. At least not enough to have an impact.
Self driving light trucks with a quadcopter to deliver to the door seems like the most efficient way to deliver packages to me.
Gonzotron: I have to agree with you on the light truck half, but once you’ve gone that far, why not just do the final 50 feet with a robot?
The design locks like someone like Serenity and combined it with a Reavers ship. I like it!
Get a pair of those mini jet engine turbines and go to work! That would be super amazing and super dangerous too.
No power in the Verse can stop it.
Google’s Wing company utilizes an interesting combination of VTOL and fixed wing flight to extend its range.
Delivery Drone may look more like this… large wings will get you long distance, vtol is needed for small area landing.
Think https://en.wikipedia.org/wiki/Lockheed_U-2, small power input long flight time, also predator/reaper but with vtol.
https://youtu.be/mm9Rh6wPDVM