[Tom Stanton] is well-regarded in the maker community, and has put much effort in over the years on a variety of electric vehicle builds. In the process of upgrading his e-bike last year, he ran into some issues with the main drive pulley. Rather than rely on guesswork, he threw engineering at the problem.
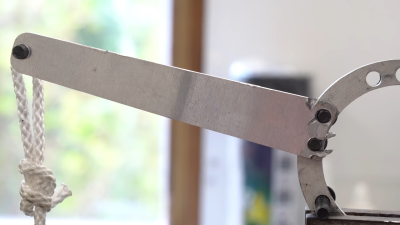
The problem concerned the mounting bolts on the pulley’s hub, which would pull out under high torque. [Tom’s] initial finite element simulations had suggested the design was sound, but reality was proving otherwise. After further analysis and testing, [Tom] determined that his analysis hadn’t properly simulated the bolt pull-out condition. With this corrected in the software, it was readily apparent that there simply wasn’t enough material around the bolt holes to hold the torque load.
With the simulation now more closely agreeing with reality, [Tom] was able to correct the design. New parts were created with a strengthened mounting section, and the pulley was successfully able to deal with the loads in service.
It’s a great example of using engineering simulation tools to solve a problem quickly, rather than simply guessing and hoping things will hold up. We’ve seen [Tom]’s work before, too — like this fun backyard trebuchet build. Video after the break.
Look hard enough, and you’ll find a flip-flop hub with one side reverse threaded. You can get a matching reverse threaded, and reverse acting ratchet flange. Need then only to find/ manufacture/ adapt an appropriate sprocket. The set-up on my 4-stroke bike was all off-the-shelf, but took some finding of all the parts.
Nice idea, that however would drop the possibilty of using your gears. They sre usually just two singlespeeds oneside freewheel, otherside locked.
Mine has room for a 7-speed, screw-on cluster on the derailleur side, and tons of room for the 415 chain sprocket, with screw-on reversed ratchet, on the other. Maybe I should be saying ‘two-sided hub’, rather than a flip-flop hub with one reversed thread? In either case, it works great for my situation, but took a lot of help with Chinese translation to track down the parts.
You don’t even have to find a reverse ratchet as your can simply screw it the other way :) I already tried it…
E-bikes were fun until they were cucked by EU regulations recently. Now ESCs have mandatory cut-off at 25kph. Hope that once we leave the EU this year we’ll be able to ditch those absurd rules.
Not really though. In Denmark, the legal ebike limit is 45 kph. It is up to local regulators
The 45 kph limit is for bikes that basically mopeds in a bicycle-frame, and needs regulation-brakes, frame, steering, etc.
If you just want to smack an electric motor on your bike, it has to only work when you rotate the pedals yourself (Kind of a dead mans switch), and only push when you’re going under 25 kph. And the motor cannot put out more than 200 watts PEAK. Not even RMS.
And to be honest, 45 kph electric bikes are kind of scary. If it’s on a double-width bikelane in the country with no other traffic, sure, but in the city, where you’re going next to children and other traffickers and has to stop suddenly for a dog, child, red light, pothole, etc, most bike(r)s are simply not up to the task.
Try going 30 kph on your bike and perform an emergency stop. Now go do the same in your car and measure the distance both went. I wouldn’t be surprised if the bike went between 2 and 3 times as long. Most mopeds have the same issue because they aren’t taught countersteering(Necessary to suddenly make a turn on heavier 2-wheel vehicles, not on pushbikes) and to use the front brakes properly
I can’t help but feel that the solution here is to not ride like an idiot. Yes if you’re going nearly 28mph on a narrow cycle lane down a busy road with plenty of pedestrians the chance of an accident happening when someone steps out is high. It’s high regardless of whether you’re in a car or on a bike, though the bike will do less damage to a person. When you’re on a bike you’re far more aware of your surroundings and aware that you are fragile and crashing into anything at 28mph will break bones, so if there’s the chance for an accident your self-preservation instinct should kick in and slow you down.
On the flip side I feel limiting ebikes to 15mph and making 28mph ebikes as hard to own as a moped (which are cheaper up front but mean you don’t exercise) is unhelpful overall. 28mph is a darned sight safer when mingling with 30mph traffic as you must do in plenty of places where cycle lanes are non-existent or poorly laid out. They’re also more likely to be used for long distance travel since e.g. 20 miles is 40 minute journey not a 1 hour 20 minute journey.
I own a 28mph ebike and my average speed you’d imagine would be 20mph+ in all situations but no. On the usual canal towpath, it’s 11mph. On the road where there is no cycle lane for half my journey so I’m taking the lane a lot, that’s when my average speed reaches the dizzying heights of 19mph.
>”When you’re on a bike you’re far more aware of your surroundings and aware that you are fragile and crashing into anything at 28mph will break bones”
When I was a teen, we had mopeds that were tuned to go 100 kph. They had drum brakes and tiny wheels, and frames that would start to rattle above 60 kph. Nobody thought about what would happen if you actually had an accident, even after barely avoiding collisions with cars. I remember one cold morning it took me 200-300 meters to stop because there was black ice, yet we still kept riding.
You give people too much credit.
On a second note: consider that people will drive these bikes while drunk.
If they’re “mopeds”, the police can take their driver’s license away. If they’re “bicycles”, the police can’t do anything except fine you.
Is UK leaving EU using an e-bike ? That would explain why it’s absurdly long ;)
Seriously: sad to let you go … I wish you good luck for the future !
They didn’t. They just moved it up to a different vehicle class, which is subject to registration and insurance. (L1e-B, 45 kph, up to 4000 Watts)
Also, don’t think that UK will allow “bicycles” that are really electric motorcycles, but without the structural integrity or proper wheels.
Besides, thank’s to UK lobbying, the EC has removed the requirement for the actual pedelec sensor and now e-bikes can have throttle-only operation so you don’t have to pedal if you don’t want to. The power limit was also lifted from 250 W to 1000 W, and as long as you actually have pedals on the bike and it stays under 25 kph, it’s L1e-A which only has to be type approved and nothing else.
The main argument against it is that the type approval is an extra hurdle that you have to cross to get your bike on the market, and that hobbyists building their own bikes are most likely unable to clear it, but that’s just the point of it. An L1e-A bike is still allowed to drive among other bicycles on biking lanes and paths, and if it’s much more powerful and quicker than conventional bikes, and still only has the brakes and the frame of a conventional bicycle, then it’s going to be a disaster as you crash into people.
If you want an e-moped instead, then you should register as such, and clear the requirements for a moped – such as disc brakes instead of rim brakes etc.. and an insurance for when you do crash into people.
or you get a motorbike license for your (electric)motorbike, and pay insurance and road tax like the rest of the road users on powered vehicles.
should add im not trolling here, in edinburgh where my business is , and where I commute through there are LOTS of cyclists, for the most part they obey the highway code, but lately im seeing more and more of these “phat” e-bikes being driven by people with little regard for the highway code, now normally this wouldnt be an issue as you average person out riding a bike is slow enough to avoid when they do something silly, avid cyclists pay more attention to there surroundings and they are capable of hitting 40kph+ on pedal power. .. basicallly they seem as capable as a moped / skooter so really should be regulated as such. Yes if you were not an idiot on your e-bike then it sucks for you but we all have to play by the rules, and the rules have to be adjusted for emerging technology, just enjoy it while it lasted.
>”and they are capable of hitting 40kph+ on pedal power. ”
Capable, but they do need a much longer head start than a 1000 Watt e-bike, and the vast majority of people don’t have those sort of leg muscles anyhow.
The spandex dildos zooming through town thinking they’re running Tour de France shouldn’t be there anyhow. They’re a right menace.
ohnestly i disagree on that, from my own observations, mr Tour de France is usually more aware of his/her surroundings and adjust speeds accordingly, is aware when cars my turn left or merge without warning etc. Wee Dave on the 1kw e-bike he bought off banggood couldn’t give a seconds thoughts to what the cars are doing and just wants to pass mr Tour de France, cause thats worth bragging about down the local.
In my experience, the Mr. Tour de France is borderline out of his wits with tunnel vision from the sheer effort of going as fast as possible, adrenaline pumping and raging at everyone going slower than them.
Here’s an interesting graph:
https://62e528761d0685343e1c-f3d1b99a743ffa4142d9d7f1978d9686.ssl.cf2.rackcdn.com/files/19873/area14mp/pf4tcn9y-1359953952.jpg
Turns out, people in athletic shape are able to put out “moped” power around 1000 Watts, for five seconds. That’s enough to accelerate an 80 kg person and a 20 kg bike to a speed of 7.1 m/s or 25.5 kph, neglecting the rolling and air resistance, and drive train friction, and the angular momentum of the wheels…
Which goes to say that no, cyclists can’t just zoom out like a moped, while e-bikes can.
Sorry, forgot to multiply by 1/2 – which would put the final speed at 36 kph – again assuming that there’s no air resistance, no friction, and your wheels have zero rotating mass (no flywheel energy).
Ignoring the horrors that politics brews up, nice bike, and great work on the Finite Element Modelling. I’d love to see FEm methos that could operate on (triangle based) stl files though rather than most of them only working within a few specific CAD programs and only for shapes produced in those programs.
Triangles are considered degenerate elements in FEA, with lots of problems due to the fundamental mathematics behind FEA. Most FEA programs do not care about your CAD package, they are more then happy to take in a step file. For the longest time FEA was completely separate from CAD and only recently has it been added to CAD as a feature.
There are also open source FEA projects, look at salome meca and code aster.
1. A safety factor of 2 isn’t high enough for cyclic loading. The spokes will still fail after a while due to cracking.
2. The bolt is carrying the load, which is a no-no. It should be tightened with enough torque that the friction between the parts keeps the joint.
3. The bolts and their mating threads are too short – not enough material to make a stiff spring to hold the two pieces together.
4. Advice n. 2 doesn’t hold under cyclic loading when the safety factor is low, because the material deforms slightly and the friction joint starts to creep, putting the loading back on the bolt.
The whole structure is iffy and difficult to make it work in the long term; should re-design with a full solid ring.
also, if you look at spokes of a bicycle wheel, you see that they almost never are perpendicular to the hub but always exit under an angle. as the drive sprocket only gets tension in one direction, it would be beneficial to connect them to the hub under an angle so both fixing screws help each other. in the current situation only one screw does the right job, the other is acting as a lever pivoting point for the arm.
simulation could help, but some down to earth mechanical knowledge never hurts.
He does have that, but the angle is rather shallow.
The point of the spokes is that they’re under constant tension – they’re tightened by a screw at the rim. This means they don’t “rattle” at the point where they hook onto the hub, but rather they’re acting as springs and damping the stresses. In his design, the varying torques on the belt are jerking the bolts back and forth, which makes the friction joint and the thread loosen up, and causes cracking.
Plus, the threaded hole acts as a starting point for crack propagation, which means that the actual strength under cyclic loading may be something ridiculously low, like 1/10th of the simulated strength because it’s like tearing paper that’s already been cut with a wedge. Should just have a straight hole with a nut on the other side.
there, bolts and nuts: another point well mentioned.
but the lever principle is the thing at work here as the forces are not relieved well in this design.
about the spokes: they are not under constant tension. actually the wheel is hanging from the spokes above the hub. the lower spokes could be complete tension less if not tightened enough. that situation changes while the wheel is turning during biking constantly.
ps. I’m not a mechanical engineer, but a real one once told me to regard every construction as if everything is made from rubber and imagine what would happen when fasteners would be loose in a stiff one. That makes forces and distortion in any construction a lot more clear.
No. Bicycle wheel spokes are under constant tension.
If the hub was only hanging down from the spokes above it, it could still swing sideways like the seat of a swingset. If the spokes below the hub aren’t pulled tight enough that they stay under tension while the wheel is loaded, the wheel has no lateral stability.
But simply pulling the spokes tight is not enough. The other trick that makes a bicycle wheel work is the fact that the hub is slightly wider than the rim, and the spokes alternate between the two flanges of the hub. If the spokes went along the same line both on the rim and on the hub, it would again have no lateral stability.
It’s like the classic trick question: how hard do you have to pull to make a clothes line exactly straight? Answer: hard enough to snap it so it hangs straight down… reason being that the force of gravity that is bowing the string acts exactly 90 degrees from the force that is pulling it taut, so no matter how hard you pull on the string, it still takes no force whatsoever to put it out of straight. The same thing happens with the bicycle wheel – if the spokes are all aligned laterally, it simply cannot run straight.
That’s why the spokes basically form two shallow cones facing each other. The deeper you make the cones (the wider the hub), the more lateral forces your wheel can handle before it turns into a taco. This is also why you can’t (shouldn’t) go 45 kph on bicycle wheels – if you get any sudden lateral forces on the wheels, they will buckle under you.
I’m no mechanical engineer, but that whole assembly looked much too flimsy to survive accelerating the mass of an adult human being. People rely too much on simulators and not enough on common sense.
I used to run circuit simulations on RFIC designs and quickly learned that any dope can get a simulator to spit out some numbers, but it takes training and experience to get them to spit out meaningful numbers, and to know the range of conditions under which those numbers are valid.
When in doubt, overbuild! It may not look as pretty, but you won’t be stuck on the side of the road with a busted pulley. What’s the reference? Look at a the chain rings on the same bicycle- those rarely fail while performing the task of accelerating an adult human body mass.
I’ve got a engineering and motorcycle industry back ground. The featured pulley “design” is so deficient, on so many levels, it should be thrown over the fence. Lucky it didn’t kill someone.
Looks like an application for a variable diameter sprocket unfortunately no design has ever worked well enough to be usable … but wait … have you seen activesprockets on youtube?
If you don’t know how to do an initial hand calc, don’t use FE methods.
Garbage in, garbage out with pretty colourful contour plots.