In the beginning, there was hot glue. Plus some tape, and a not inconsiderable amount of Bondo. In general, building custom portable game consoles a decade or so in the past was just a bit…messier than it is today. But with all the incredible tools and techniques the individual hardware hacker now has at their disposal, modern examples are pushing the boundaries of DIY.
This Zelda: Ocarina of Time themed portable N64 by [Chris Downing] is a perfect example. While the device is using a legitimate N64 motherboard, nearly every other component has been designed and manufactured specifically for this application. The case has been FDM 3D printed on a Prusa i3, the highly-detailed buttons were printed in resin on a Form 3, and several support PCBs and interface components made the leap from digital designs to physical objects thanks to the services of OSH Park.
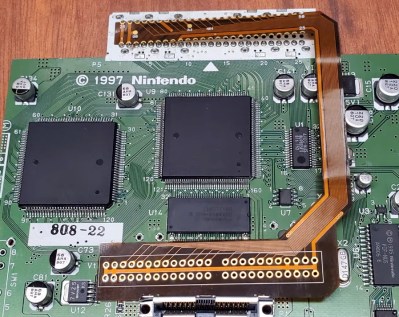
Today, those details are becoming increasingly commonplace in the projects we see. But that’s sort of the point. In the video after the break, [Chris] breaks down the evolution of his portable consoles from hacked and glued together monstrosities (we mean that in the nicest way possible) to the sleek and professional examples like his latest N64 commission. But this isn’t a story of one maker’s personal journey through the ranks, it’s about the sort of techniques that have become available to the individual over the last decade.
Case in point, custom flexible flat cables (FFC). As [Chris] explains, when you wanted to relocate the cartridge slot on a portable console in the past, it usually involved tedious point-to-point wiring. Now, with the low-volume production capabilities offered by companies like OSH Park, you can have your own flexible cables made that are neater, faster to install, and far more reliable.
Projects like this one, along with other incredible creations from leaders in the community such as [GMan] are changing our perceptions of what a dedicated individual is capable of. There’s no way to be sure what the state-of-the-art will look like in another 5 or 10 years, but we’re certainly excited to find out.
The fit and finish on this is highly impressive. I’m always happy to see stuff like this, it’s hard to keep track of how awesome the market is sometimes.
One of my inner hackers is about to hit up amazon for enough googly eyes for every connector in the house, and another one is menacing the N64 which is quivering in a corner, with the dremel. A third is pointing out the gamecube and the spare wii, and the team leader is trying to restore some sort of order and frantically waving the green laser pointer across the three whiteboards of in progress, backburnered and potential projects.
I feel…. targeted
That just about sums up the thought/action process of a console modder! Nicely put :)
What impresses me the most is that flex-PCB (or FFC as it was referred to in the article). Many years ago (mid-1990’s) I worked for a company that produced those kapton flex-PCB’s for customers all over the world. For one example, we made part of the wiring harness for the Sidewinder missile.
Seeing that reminds me of the three years I worked there and all the things I learned while doing so (some good, some bad).
I’m impressed that the process has been computerized and/or automated to the point that custom parts can be made on demand. There’s no way that could have been done economically with the technology we had back then.
Yeah I had a glimpse into that kind of business at the start of the 90s and it all looked like lithography and screen printing in bunnysuit clean room.
That sounds awesome! Being on the front of new tech back in the day like that sounds like so much fun! Kinda reminds me of how the first controller PCBs were done on the original NES which had essentially “hand drawn” traces. Archaic by today’s standards, but what a manufacturing achievement is was back then.
Indeed, those flex flat PCB cable things are really neat. Wish I’d had access to them for some projects – even relatively recently they were (if available to hobbist at all) expensive enough to force me into hand soldered cables..
Really love the use he put them too in this project too, sleek and slim for the gameslot relocation. Massively practical for joining the two case halves together in a detachable way! Best i’d ever done on that score was salvage IDE/FLoppy connectors and cables which are soo damn bulky and inevitably have either one too few or far too many conductors…
Amazing job.
I’d love to see this project done in the shape of a blue pan flute.
My first (and only) attempt at console modding (more like gamepad modding) was turning an original PlayStation controller wireless.
I did everything, wrote firmware to read the controller status, read battery level, transmit using NRF radio chip, wrote firmware for receiver to enumerate as USB HID, etc. It was a truly great learning experience. It taught me that things can go wrong BADLY, no matter how prepared you think, you are.
I need that ffc strip!!!