The venerable ATX standard was developed in 1995 by Intel, as an attempt to standardize what had until then been a PC ecosystem formed around the IBM AT PC’s legacy. The preceding AT form factor was not so much a standard as it was the copying of the IBM AT’s approximate mainboard and with it all of its flaws.
With the ATX standard also came the ATX power supply (PSU), the standard for which defines the standard voltage rails and the function of each additional feature, such as soft power on (PS_ON). As with all electrical appliances and gadgets during the 1990s and beyond, the ATX PSUs became the subject of power efficiency regulations, which would also lead to the 80+ certification program in 2004.
Starting in 2019, Intel has been promoting the ATX12VO (12 V only) standard for new systems, but what is this new standard about, and will switching everything to 12 V really be worth any power savings?
What ATX12VO Is
As the name implies, the ATX12VO standard is essentially about removing the other voltage rails that currently exist in the ATX PSU standard. The idea is that by providing one single base voltage, any other voltages can be generated as needed using step-down (buck) converters. Since the Pentium 4 era this has already become standard practice for the processor and much of the circuitry on the mainboard anyway.
As the ATX PSU standard moved from the old 1.x revisions into the current 2.x revision range, the -5V rail was removed, and the -12V rail made optional. The ATX power connector with the mainboard was increased from 20 to 24 pins to allow for more 12 V capacity to be added. Along with the Pentium 4’s appetite for power came the new 4-pin mainboard connector, which is commonly called the “P4 connector”, but officially the “+12 V Power 4 Pin Connector” in the v2.53 standard. This adds another two 12 V lines.
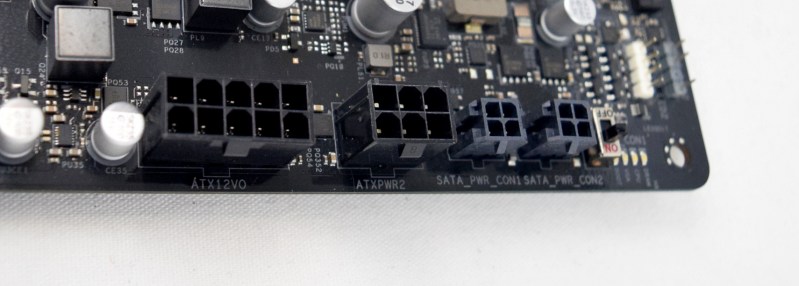
In the ATX12VO standard, the -12 V, 5 V, 5 VSB (standby) and 3.3 V rails are deleted. The 24-pin connector is replaced with a 10-pin one that carries three 12 V lines (one more than ATX v2.x) in addition to the new 12 VSB standby voltage rail. The 4-pin 12 V connectors would still remain, and still require one to squeeze one or two of those through impossibly small gaps in the system’s case to get them to the top of the mainboard, near the CPU’s voltage regulator modules (VRMs).
While the PSU itself would be somewhat streamlined, the mainboard would gain these VRM sections for the 5 V and 3.3 V rails, as well as power outputs for SATA, Molex and similar. Essentially the mainboard would take over some of the PSU’s functions.
Why ATX12VO exists
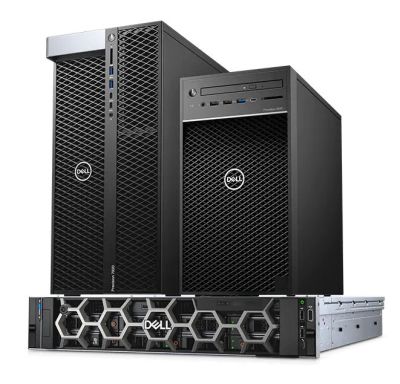
The folk over at GamersNexus have covered their research and the industry’s thoughts on the topic of ATX12VO in an article and video that were published last year. To make a long story short, OEM system builders and systems integrators are subject to pretty strong power efficiency regulations, especially in California. Starting in July of 2021, new Tier 2 regulations will come into force that add more strict requirements for OEM and SI computer equipment: see 1605.3(v)(5) (specifically table V-7) for details.
In order to meet these ever more stringent efficiency requirements, OEMs have been creating their own proprietary 12 V-only solutions, as detailed in GamersNexus’ recent video review on the Dell G5 5000 pre-built desktop system. Intel’s ATX12VO standard therefore would seem to be more targeted at unifying these proprietary standards rather than replacing ATX v2.x PSUs in DIY systems. For the latter group, who build their own systems out of standard ATX, mini-ITX and similar components, these stringent efficiency regulations do not apply.
The primary question thus becomes whether ATX12VO makes sense for DIY system builders. While the ability to (theoretically) increase power efficiency especially at low loads seems beneficial, it’s not impossible to accomplish the same with ATX v2.x PSUs. As stated by an anonymous PSU manufacturer in the GamersNexus article, SIs are likely to end up simply using high-efficiency ATX v2.x PSUs to meet California’s Tier 2 regulations.
Evolution vs Revolution
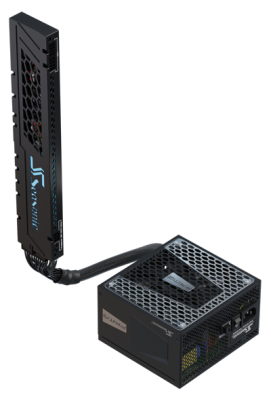
Ever since the original ATX PSU standard, the improvements have been gradual and never disruptive. Although some got caught out by the negative voltage rails being left out when trying to power old mainboards that relied on -5 V and -12 V rails being present, in general these changes were minor enough to incorporate these into the natural upgrade cycle of computer systems. Not so with ATX12VO, as it absolutely requires an ATX12VO PSU and mainboard to accomplish the increased efficiency goals.
While the possibility of using an ATX v2.x to ATX12VO adapter exists that passively adapts the 12 V rails to the new 10-pin connector and boosts the 5 VSB line to 12 VSB levels, this actually lowers efficiency instead of increasing it. Essentially, the only way for ATX12VO to make a lot of sense is for the industry to switch over immediately and everyone to upgrade to it as well without reusing non-ATX12VO compatible mainboards and PSUs.
Another crucial point here is that OEMs and SIs are not required to adopt ATX12VO. Much like Intel’s ill-fated BTX alternative to the ATX standard, ATX12VO is a suggested standard that manufacturers and OEMs are free to adopt or ignore at their leisure.
Important here are probably the obvious negatives that ATX12VO introduces:
- Adding another hot spot to the mainboard and taking up precious board space.
- Turning mainboard manufacturers into PSU manufacturers.
- Increasing the cost and complexity of mainboards.
- Routing peripheral power (including case fans) from the mainboard.
- Complicating troubleshooting of power issues.
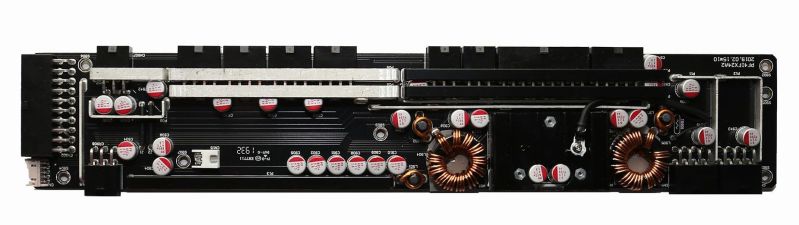
Add to this potential alternatives like Seasonic’s CONNECT module. This does effectively the same as the ATX12VO standard, removing the 5 V and 3.3 V rails from the PSU and moving them to an external module, off of the mainboard. It can be fitted into the area behind the mainboard in many computer cases, making for very clean cable management. It also allows for increased efficiency.
As PSUs tend to survive at least a few system upgrades, it could be argued that from an environmental perspective, having the minor rails generated on the mainboard is undesirable. Perhaps the least desirable aspect of ATX12VO is that it reduces the modular nature of ATX-style computers, making them more like notebook-style systems. Instead, a more reasonable solution here might be that of a CONNECT-like solution which offers both an ATX 24-pin and ATX12VO-style 10-pin connectivity option.
Thinking larger
In the larger scheme of power efficiency it can be beneficial to take a few steps back from details like the innards of a computer system and look at e.g. the mains alternating current (AC) that powers these systems. A well-known property of switching mode power supplies (SMPS) like those used in any modern computer is that they’re more efficient at higher AC input voltages.
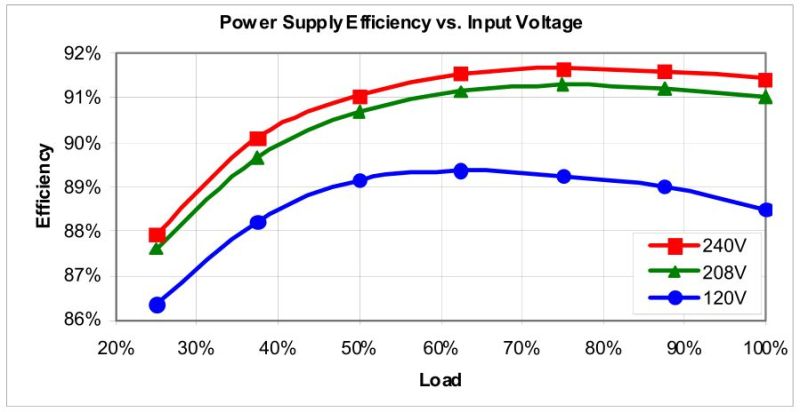
This can be seen clearly when looking for example at the rating levels for 80 Plus certification. Between 120 VAC and 230 VAC line voltage, the latter is significantly more efficient. To this one can also add the resistive losses from carrying double the amps over the house wiring for the same power draw at 120 V compared to 230 VAC. This is the reason why data centers in North America generally run on 208 VAC according to this APC white paper.
For crypto miners and similar, wiring up their computer room for 240 VAC (North American hot-neutral-hot) is also a popular topic, as it directly boosts their profits.
Future Outlook
Whether ATX12VO will become the next big thing or fizzle out like BTX and so many other proposed standards is hard to tell. One thing which the ATX12VO standard has against it is definitely that it requires a lot of big changes to happen in parallel, and the creation of a lot of electronic waste through forced upgrades within a short timespan. If we consider that many ATX and SFX-style PSUs are offered with 7-10 year warranties compared to the much shorter lifespan of mainboards, this poses a significant obstacle.
Based on the sounds from the industry, it seems highly likely that much will remain ‘business as usual’. There are many efficient ATX v2.x PSUs out there, including 80 Plus Platinum and Titanium rated ones, and Seasonic’s CONNECT and similar solutions would appeal heavily to those who are into neat cable management. For those who buy pre-built systems, the use of ATX12VO is also not relevant, so long as the hardware is compliant to all (efficiency) regulations. The ATX v2.x standard and 80 Plus certification are also changing to set strict 2-10% load efficiency targets, which is the main target with ATX12VO.
What would be the point for you to switch to ATX12VO, and would you pick it over a solution like Seasonic CONNECT if both offered the same efficiency levels?
(Heading image: Asrock Z490 Phantom Gaming 4SR with SATA power connected, credit: c’t)
For anyone else wondering, 208v power is different from your 240v power plug you may have in your house. The US power grid tends to run as 3 phase power. House power is a single phase of 240v with a transformer center tap serving as neutral. 208v power is what you get across *two* of those phases.
Ah, thanks, UK resident here wondering where 208v came from, or whether a HAD typo, surely not the latter.
We seem to like standards in the US, as we have so many of them! There’s also 277v, which is two phases of 480v three phase. Sometimes used for lighting circuits in buildings that have the higher voltage three phase equipment.
Yeah. In the US, it’s 208Y/120, 480Y/277, and then there’s a higher voltage for commercial 3-phase
Europe has 400Y/240 – which has the same single-phase voltage as the phase-to-phase voltage of US residential split-phase.
And just to complicate things: In Canada there is commonly 600V/346V, with the 600V 3-phase going to things like large air handler motors, and the 346V used on lighting circuits.
600v is not unheard of in the US in industrial settings, though I never worked on anything higher than 480v myself.
All clearly and unambiguously labelled, I’m sure. :-)
in fact, Yes. The NEC is very picky about such things
Pretty well labelled — to excess sometimes. There is a uniquely-shaped plug for every combination of voltages and current. https://en.wikipedia.org/wiki/NEMA_connector In *theory* if you have a 240V 30A appliance but a 240V 50A outlet, you should be able to plug in — but in practice there are still enough common corner cases (and modern electronics like car chargers can efficiently accept a wide variety of inputs) that EV owners tend to carry around a small collection of “dumb” adapters that just adjust plug shape.
208v it’s the phase-phase voltage of a 120v phase-neutral system, which is appearantly also used in the us, next to the 240v phase-phase with center tap system.
To add to that the 208V is mainly an industrial thing. You’re very unlikely to see it in any kind of residential setting
So two phases are not even used on a high power item like a cooker ? (Using two phases there would reduce the wire thickness required from the fuse board to the cooker).
For most residential uses in North America, the cable coming from the pole transformer has 3 conductors: +120V, neutral, and -120V. the 120V lines are 180º out of phase with each other and aren’t the same as phase-to-phase on two legs of a three phase system. For the big stuff like ovens and clothes dryers, they’re typically hooked up to both the +120V and -120V lines. This gives them 240V effectively.
This YouTube video from Technology Connections does a much better job of explaining it than I can : https://www.youtube.com/watch?v=jMmUoZh3Hq4
You’d use 240 for that in a residential system. It’s still 1 phase, just uses the whole transformer vs only 1/2 of it
And generally our breaker boxes are set up so that roughly half the house runs on -120 and the other half on +120 and so the two phases are loaded roughly the same, with a few “double wide” slots at the bottom which route 240V to any “big stuff” (air conditioners, electric stoves, etc).
You sometimes see 208V in large apartment buildings where they feed two legs of 3phase to each apartment
High-rise apartment buildings often use 3-phase power. They will provide 2 phases to the apartments for driving stoves and the like. Sometimes they will also split the phases up for different circuits in the apartment, so if you take an AC meter and measure between outlets in different rooms, you might find 208 V.
“Essentially, the only way for ATX12VO to make a lot of sense is for the industry to switch over immediately and everyone to upgrade to it as well without reusing non-ATX12VO compatible mainboards and PSUs.”
Not a good thing in the midst of a parts shortage worldwide.
Also strikes me as flat out wrong – I don’t think it ever makes sense as the global standard, you still need to regulate power somewhere, putting more of it on the motherboard isn’t inherently a big gain (if a gain at all) over having the right voltages all from the PSU…
You want more efficiency just put in a higher quality PSU, the transmission losses around something as small and high draw as a computer are basically irrelevant, doesn’t much matter much where the voltages are created, just how efficiently they are. Case in point the 5v phone charger I was powering a Pi through was shockingly bad compared to hooking that same pi up to a spare ATX supply in wall draw (yes the phone charger is crappy, running hot enough to be scary and the ATX is a platinum rated) which as a plus side means I now have a neat bench power supply, LED light strip, and powered USB hub all off the same powersupply neatly built into my desk, and being a modular ATX can plug in the extras to power whatever else I might need.
Actually makes it much harder to verify the efficiencies too, the PSU does just one thing take AC and turn it to regulated low voltage DC – you can easily test each of its outputs. Soon as you build lots of that into the motherboard it becomes harder to really characterise – as the motherboard will be no doubt taking some of those voltages for itself. Also limits how much power you can provide – nice fat traces to the outputs allowing the mobo to run that 12 HDD system off the motherboard are pretty much never going to exist, its too much extra expense, board real estate for a niche use. But build that same system on a generic motherboard and all you need is a big enough PSU and probably a PCIe sata card. Keeping everything properly modular is just so much more flexible, which has to be good on the e-waste front!
What ATX12VO does make sense for is those specialist builds, and as a computer standard to integrate into caravans/boats/cars – most of which seem to be 12v, some 24v but all of them are DC. No need for the extra inverters, PSU etc, probably put a little smoothing capacitor bank in and plug the computer straight in (assuming said standard allows for input voltage running under 12 enough to accommodate the batteries voltage drop). Having just one 12V ATX standard so everything is interoperable for those usecases that actually need it really does make sense.
HP (and dell) seem to think different. They have been putting “12VO” (their versions) power supplies in their machines for years now. At least HP published the reasons for this move. And one of those is a claim that generating the needed voltages on the board where and when they are actually needed, improved efficiency. Maybe there are more regulators, but they run less hot, and they are like all electronics shrinking in size.
You can debate this off course. But I am quite sure an manufacturer like HP would not do this if it was not worth it. They are in business to make money.
And as big OEM system builders of for business PC’s they are a specialist case, large volumes of relatively low spec machines that won’t have strange peripherals, masses of excess harddisks, all the multitude of things normal PC’s do get because individuals, and strange edge cases like labs tend to buy just the one or two PC and throw everything they need into it. Where in business the terminal your worker sits at could almost be pi zero for the performance and local storage they actually need, most everything being on the servers..
Its a very different thing saying 12v only doesn’t make sense as the only game in town, to saying it never makes sense at all.
It’s kind of weird to label the vast majority of PCs made and sold a “specialist case”, no? Isn’t that more or less the definition of something general, with other use cases thus being specialist?
I guess so, but humans are like that, boring common stuff in the background of life isn’t worth as much note.
Though I wasn’t really talking about the PC’s themselves but the OEM builders – its the creators of these potentially very limited mostly garbage PC’s that are specialists – often it seems in charging fortunes for rather low spec computers, that often can’t be upgraded or even kept running if a part fails, but hopefully at least offer support (at an extra profit) and making them efficient in the process.
As to me at least the vast majority of PC’s that count are not OEM built at all – a real PC is built by somebody that needs its versatility, upgradableity or repairablity – the folks buying OEM, espically such upgrade restrictive OEM stuff are basically only needing a smartphone/laptop/Pi just something that can render their webpage and text document.. Its not the same market, or really the same device at all, they just look similar and have some overlap in functionality…
…yet when speaking of improving PSU efficiency, the most impactful approach would be precisely to address the “boring common stuff in the backgruound […] that isn’t worth as much note”? Given that there are hundreds of millions of OEM desktops in service across the globe, and a fraction of that of DIY and custom built PCs, which would you target for improving efficiency in order to make a meaningful difference?
This is also potentially a move to make OEM PCs more standardized, get them away from their current proprietary solutions and make them more serviceable, reusable, etc. I have a (rather heavily) modified Optiplex 990 SFF that I use as a travel desktop, but that was the last generation where Dell still used the ATX PSU connectors, so later generations could never have been modded like I have done. ATX12VO opens the door for replacing OEM PSUs with more powerful versions (enabling repurposing old office PCs as gaming PCs, for example), replacing them if they break, etc., etc.
Thankfully, due to the simplicity of DC-DC conversion and the current delivery capabilities of 12V, ATX12VO is still perfectly capable of powering pretty much any PC hardware. A few devices will need additional power conversion circuitry that they don’t currently have, but the vast majority will not (anything slot powered, anything PCIe or EPS powered), and will work just as it does today. 12VO even has far superior allowances for PCIe slot power delivery through a standardized additional 6-pin cable on the motherboard. For those devices requiring SATA, Molex or Berg power connectors, most of them can be powered off the SATA headers on 12VO motherboards, and if not, 12V-to-SATA/Molex converter boxes are bound to appear at low cost and with dead simple installation, likely connecting to a PCIe 6-pin. The only situation where this would be an issue is if your system requires a very high number of SATA/Molex/Berg powered devices _with high current draws_, which is an extremely unlikely scenario given that none of those connectors are rated for high currents.
Indeed, and I never said otherwise – just that as it stands 12vo doesn’t really make sense as the only game in town. And doesn’t make much sense for the PC enthusiast and lab/studio hardware type markets – vast swathes of people who actually really need a PC, rather than the office web browser (or at push game-console alike – the true consoles are almost certainly better in use – being such vastly distributed hardware they get better optimisations than OEM gaming tat)…
It would be like decreeing all wireless communication will be via Bluetooth, or IR – its not the right tool for every job. I have nothing against 12VO as a standard – as you say its got clear uses espically if the OEM pick it up over their own special solution (though I suspect most of those uses would actually be better served with something like and Intel Nuc/ Pi – most of these OEM computers are just a basic box with keyboard mouse and screen to the user, they neither need or want what little modularity the OEM ‘desktop’ allow – so cutting out all the fat at production time for that really streamlined, super efficient by design approach makes more sense than pretending its still a ‘desktop’.
Though you still miss the point about all the 12vo supplies I’ve seen – they have neither the power outlets available or head room to really pretend to be ATX for those workstations full of disks, or other powered hardware, and even if they did it would be no better than just having the normal ATX of the correct rating now anyway – as those 12vo supplies sudden need to be massively over the required draw they should be designed around, and you end up throwing in yet more regulators for every device…
Given that there are literally zero consumer-oriented ATX12VO motherboards available, it’s hardly a surprise that there aren’t any PSUs for them, is there? There are still plenty powerful options for the vast majority of PCs though: Intel showed off a 650W High Power unit when demonstrating the standard (https://www.pcworld.com/article/3576039/intels-power-play-hands-on-with-atx12vo-motherboards-and-power-supply.html), and there’s a 500W FlexATX format one in the NUC 9 Extreme (the modular “gaming” NUC and its Xeon-equipped workstation equivalent). Making more powerful versions would be as difficult as taking existing high output PSUs, stripping out the 5V, 3.3V and 5VSB rails, adding a 12VSB rail, and changing out the modular board for one with the appropriate connectors. There is absolutely nothing stopping ATX12VO from being at least as powerful as ATX. And if the standard gains traction, that will clearly happen. Saying “the PSUs we have now can’t power a proper PC” is neither accurate nor a valid argument for a yet-to-be-adopted standard.
Also, I’d argue that PCs are necessary for most of the cases you are dismissing – doing web work on a Pi, even something as simple as a basic PoS interface, would be excruciatingly slow compared to a low end laptop chip, let alone a 35W T-series desktop CPU. Performance matters as much for responsiveness as for finishing heavy tasks quickly – that’s why current laptop chips turbo so high.
As for your BT/IR analogy, it doesn’t fit – those standards are low bandwidth, low power, low range, etc. I.e. they are a) meant for specialized implementations, b) are inflexible, and c) fail to meet the requirements of heavy usage scenarios. ATX12VO has none of these flaws – it’s inherently flexible (12V can be converted whenever you need something else, easily, efficiently and cheaply), it’s suitable for broad deployment as it covers the basic needs of all PCs, and it can scale to fit the needs of heavy users – either they have power hungry equipment, in which case it already uses 12V through PCIe wiring, or they have low power equipment that’s either slot powered (ATX12VO covers that) or SATA/Molex powered (again, integrated into the motherboard).
The only cases where it doesn’t fit is _severe_ edge cases like someone needing >4 HDDs, a large amount of SATA/Molex powered peripheral devices _and_ several power hungry AICs. But even then it’s arguably better suited, as at least the boards will have provisions for proper slot power delivery for more than a couple of devices (thanks to the now standardized 6-pin additional 12V board power). Worst case scenario, these users would need an additional PCIe 6/8-pin-to-SATA/Molex power converter unit to stick somewhere in their case. That really isn’t asking much of such an edge case.
I also included Intel Nuc type stuff too – which are at least as potent as most of these for buisness desktops and far more optimised – for the cases when you do still need performance locally. They are generally more powerful (or at least have more sustained performance) than similar laptops and without all the wasteage of using a portable machine as static.
But a great many business don’t, with everything being on the servers with the way their IT is set up – for those even a Pi zero will probably be overkill (though use a Pi 1 to have an Ethernet connection WiFi is a terrible idea). And the Pi 3 and 4 are superb for things like POS, I happen to know the petrol stations round here have heaps of them in the mix now. Nor are Pi’s the only SBC in town, one of the best, but there are good ones at many other specs.
I actually use a Pi 4 as my default always around PC now, the performance is good enough that I only need to fire up this workstation for those really heavy jobs, and to run the gaming VM’s (or look up stuff I should have put on my NAS already…). My 8gb ram pi 4 has even run two VMs with 1080p desktops (all cpu rendering) and of course its own desktop with the heap of web tabs, music player etc without a hitch. Even when both the VM’s are playing a video – though there I’ll admit the CPU does need serious overclocking to run at that video resolution (and boy with the right cooling can those chips overclock, don’t seem to need much if any extra voltage for quite a while too) – 480p seemed ok at stock clocks though – and its not a sane use case, I just wanted to see if it would work – I use the VM’s mostly for internet related stuff like running JS on a website I don’t trust but want to look at, or as terminal playgrounds to make sure I don’t bugger up a working enviroment – its so easy to recover a VM if you do, which also means happy to waste time digging in to how/why because you know its trivial to get back.
I’m also well aware 12VO could eventually become a viable ATX replacement, it just isn’t there yet – which has been one of my points. The other major one being it doesn’t magically end up more efficient in every situation, power conversions and delivery are basically impossible to really optimise when the power system has to cope with significantly variable specs – its perfectly possible to have a well selected ATX supply and exceed in base efficiency what you would see on the similar 12VO OEM machines, efficiency largely being determined by power supplies efficiencies at that % load in this situation.
You also have to consider the cost, number of failure points, embodied energy in creating each type of system too, and 12VO looses on all of those as it stands badly – many more separate voltage regulators is a much greater fiscal and environmental cost in their creation, and introduces many more potential points of failure than just having one supplying that power rail (though it would be nice if PC standards were refreshed such that everything expected to only be supplied with x voltage), all those extras built into the mobo means any tiny bit fails the entire system might well be written off, along with adding yet more heat generation tightly packed together, just to help along failures (as it is the latest Intel mobo chipsets do seem like they want to go up in smoke trying to drive Intel’s rather poor processors fast enough to be competitive with the currently superior AMD offerings…), plus PSU tend to vastly outlive the system they were bought for – so if we assume the mobo versions are as long lived lots of perfectly good electronics ends up E-waste because the CPU/RAM has got too old and/or died.
I know you mentioned NUCs, but you seem to be speaking as if these are very distinct categories rather than a broad and nuanced spectrum of devices. A NUC isn’t that different from an uSFF PC with a socketed 35W CPU after all, but also isn’t that different from an SBC – though performance can differ greatly depending on the hardware and use case. But even for basic office tasks or anything web based, while a Pi 4 or something similar can indeed run it decently, don’t discount the change in responsiveness moving to a high boost clock mobile CPU or a desktop one. And responsiveness matters a lot when doing repetitive tasks, multitasking, opening new documents, and other small, bursty workloads. Reducing those minor wait times have a profound effect on user experience. That doesn’t mean an SBC couldn’t do it, of course, and you could get _great_ performance from an SBC with an actually powerful SoC, but that would also drive up the price, and many equipment purchases are indeed motivated mainly by buying the cheapest thing that can do what is needed, period. (uSFF PCs are also far more serviceable than SBCs or NUCs.)
But this spectrum of systems is important. Why? Because 12VO can be useful for a _huge_ range of it. Even ~1l uSFF PCs could feasibly use external power bricks following the 12VO standard – Dell uses 8-pin PCIe-like power connectors (same style, but different keying and pinout) for some of their uSFF Optiplex series. Moving to a 10-pin ATX12VO input would allow them to use standardized parts and designs, make for easier troubleshooting through using regular desktop PSUs, allow for standby with an external PSU (which are generally on all the time, which is rather inefficient), and have other benefits. So 12VO can have benefits even in relatively low powered scenarios.
And 12VO is designed to go all the way from entry level uSFF desktops to the most powerful workstations. You keep saying it “isn’t there yet”, but again – _the standard hasn’t really launched yet_. Saying it “isn’t there” is meaningless in this context. It is trivial for PSU makers to adapt current ATX designs to ATX12VO. The standard has no hindrances for high power implementations, and is arguably better suited for it than ATX (more board power and more slot powered device power through the optional motherboard 6-pin). Saying it “isn’t there yet” because there are no PSUs currently on the market when there are no motherboards to use them on is nonsensical. If/when the motherboards launch, the PSUs will launch alongside them, and they will launch in the relevant power ranges – which will most likely mean 550W-850W for consumers, as those are the most selling output ranges, though hopefully we’ll see <550W quickly too (given how prone people are to buying stupidly overrated PSUs for their 1000W units won’t be far behind either.
You’re right that there is a risk of increased embodied energy, though for the majority of systems it will likely go down. Why? Because for most systems, the amount of DC-DC converters will stay the same, and their output rating (and thus size and material needs and production energy) will be more tailored to the use case, with less overprovisioning. Current PCs already have separate VRMs for the CPU, RAM (and GPU, if applicable). Current PSUs (of recent design, not using terribly inefficient AC-DC conversion for lower voltages) have DC-DC converters for three minor rails. Moving those to the motherboard adds no embodied energy, and lowers cable losses. That’s an efficiency win. Splitting them up into several smaller ones will of course increase embodied energy, but the overall environmental impact of this is likely made up for by the efficiency savings from removing cable losses – low current DC-DC converters are _tiny_ after all, and require very few resources, and most PCs aren’t powered off renewable energy.
Ensuring a long life cycle and good (or at all existent!) repair and recycling schemes for these parts is of course crucially important, but I don’t see this as a major issue with 12VO specifically. Motherboards don’t fail that often. DC-DC converters of even half decent quality with a modicum of airflow over them don’t fail often at all (you say PSUs last so long, after all, yet a PSU is inevitably a hotter environment than a motherboard, and most good ones contain a bunch of DC-DC converters). You’re adding a tad of heat (let’s say you’re outputting 50W of 5V from a single converter – highly unlikely, but possible – that’s 2.63W of siwtching heat output assuming 95% efficiency for the converter), but the amount is negligible and is easily dissipated in even SFF PCs. High current implementations – CPUs and GPUs, mainly – already run their own 12V-to-whatever they need DC-DC converters and control and cool those separately. Of course we really, desperately need a proliferation of board-level repair of hardware (including access to schematics, parts and diagnostic tools, as well as trade training and reliable certifications), but 12VO isn’t likely to affect that much either way. Yes, if a motherboard fails, you’re (unless recycled) creating a tiny bit more e-waste. But if the PSU fails, you’re creating a bit less. The sum will no doubt be a bit more, as motherboards are more prone to failure than PSUs, but this is a problem better counteracted in other ways, and the detrimental impact of 12VO is tiny.
PSUs in DIY of course tend to vastly outlast the parts they are bought for, but that’s more due to the upgrade mania and hardware fetishization of the DIY PC scene (alongside the weirdly low status of investing in PSUs) rather than anything else. Of course that doesn’t take away the increased waste from moving the voltage converters, but the sheer numbers of OEM business/education/government desktops compared to DIY PCs makes this essentially meaningless, as this will be a net zero or positive change for those far more common scenarios in terms of embodied energy. Until the proliferation of NVMe drives for example, many OEM systems had removed the 3.3V rail entirely as it simply wasn’t needed. Now they can do things like that without using proprietary PSU outputs.
As for it being “perfectly possible to have a well selected ATX supply and exceed in base efficiency what you would see on the similar 12VO OEM machines” – that is a really, really weird way of twisting this. Yes, you have very efficient ATX PSUs. 80+ Titanium is a great efficiency standard – in part because it finally adds a 10% load efficiency requirement, rather than the 20% minimum of previous standards. But it is also rare, very expensive, and only really found on high output units (there are a few exceptions, but not many). That means that 10% rating is often still above the idle power consumption of those PCs – if your PC idles at 40-50W (which is realistic) but your PSU is rated for 850W, that means 80+ Titanium mandates 90% efficiency at 85W, but has no demands for anything lower. 50W might be below 80% (or even lower!) due to how switch-mode PSUs generally work. 12VO of course doesn’t change any of this. But what it does change is that even in this scenario, there are no cable losses for lower voltages. And at lower output powers, the lower voltages – for USB, SSDs, and so on – make up a much more significant portion of the output, making these able losses more meaningful. If the exact same PSU was redesigned for 12VO – removing 5V and 3.3V and exchanging 5VSB for 12VSB – it would be measurably more efficient in all low load scenarios due to there being less low voltage cable losses. At high loads these gains would shrink to be essentially meaningless/inseparable from testing variance (3-5W less at 50W is meaningful, not really so at 500W), but at low loads 12VO will _always_ be more efficient in an equivalent design.
But even that misses the core point: 12VO moves _all_ PSUs up the efficiency chain. The least efficient designs today are so due to still using AC-DC conversion for their low voltage lines. 12VO abolishes that by default. It makes it _dramatically_ simpler to produce a high efficiency PSU, and much more difficult to produce a low efficiency one. You could still use a poor quality AC-12VDC circuit, but at least that would be the only cheap and shitty converter in the system, and even that cheap and shitty PSU would now have DC-DC conversion for its lower rails. It also cuts BOM costs for PSU makers and dramtically simplifies PSU PCB layouts, potentially allowing them to use higher quality circuitry at all price points. No doubt we’ll see profiteering companies keeping prices the same while increasing margins, but hopefully serious companies will adapt accordingly. But even if they don’t, we’ll still see an improvement in the baseline efficiency of PCs, particularly at low loads.
That you want to compare OEM ATX12VO PSUs to high end retail ATX PSUs … that’s on you. Unless your comparisons are actually comparable, that’s not a valid argument. And those aren’t – you’re explicitly arguing that “if I’m selective and have no constraints my choice can be better than the choice of someone operating within very strict constraints”, which has so many fundamental logical flaws I really shouldn’t need to be typing this. OEMs are not going to move to expensive 80+ Titanium PSU designs in their mass-market business/education/government desktops any time soon. But _both of those classes of PSU_ will become more efficient in some way if moved to 12VO. The latter will see less of an improvement than the former, but it will improve at low loads. The former will improve across the board, and is much more meaningful given the several orders of magnitude higher production volumes of these units. And that’s where this makes an impact.
Yes motherboards don’t fail often – they just become e-waste anyway when the more delicate components they support die or become obsolete. Where a good PSU will probably last through many many generational changes (while the PC standards remain the same at least).
And I wasn’t talking premium stupid price ATX vs cheap 12vo OEM in the efficiency comparison – to an OEM where you put the high efficiency dc-dc conversion makes no difference to cost at all, so they could be creating ATX standard ones with the same or higher efficiency for their builds if they wanted, Putting it on the motherboard really only means they get to make more money (and avoid regulations on power supply efficiencies) – as its not quite standard, especially at the moment, you have to buy their more expensive (if you can even buy it as an individual/repair technician) 12vo replacement part, or keep paying for extra years of support – they own you as the customer by not using the ubiquitous standard parts. Yes transmission losses will exist, but over such tiny runs, for commonly so little draw (particularly in these OEM prebuilds) they are going to be tiny changes – ATX might even be better transmission loss wise – direct from supply rail to device vs to the mobo, then lots of traces on the mobo to get from the input to the power convertor to the connector to then get wired to the device (some at 12v, but still got losses to count there – its extra travel inside the device from its wall supply).
Also PSU internals unless they are terribly inefficient just don’t get particularly hot, its a big box thanks to legacy sizing spreading out lots of heat generation and thus having easy air flow, fanless PSU are getting rather common now for a reason! But putting that extra heat generation, in close proximity to the NVME drives, CPU and its support circuits – all the bits of a system that really do get hot just makes it harder to shift all the heat away. And in the case of current gen intel chipsets that is bound to lead to failure of the chipset, as those chipset seem to be running stupidly stupidly hot, even in ideal conditions to cool them.. And its not going to be good for any system – airflow over the surface of a motherboard with all the obstructions is never great – even worse in the modern era when most CPU coolers are side blowing towers or water blocks (and have to be as the processors are running so hot) not the downfiring fan of yesteryear.
A PSU has a useful lifespan of 8-10 years if not in a very high power usage scenario. A motherboard typically lasts however long its CPU is suitable for its task – which is typically less than 8-10 years, but can also be much more. Of course very few people keeping motherboards for that long go out and replace their PSU (if either fails, the entire units is likely replaced), but at that point it’s all moot anyhow. A good PSU only lasts through many generational changes in the DIY space, and only then if a) the user has a rather severe case of upgrade mania (several generations in 8-10 years implies upgrading the CPU and motherboard every ~2-3 years), b) has the wherewithal to buy a high quality PSU in the first place, and c) isn’t at all worried that their new shiny CPU and motherboard might be somehow damaged by using an old PSU. All of which combines into making this a very, very, very niche situation. It absolutely does happen, but that level of upgrade mania, selective planning ahead, and lack of worry about PSU wear is a particularly rare combination. Two of the three is common, but three out of three? Not at all. The more likely scenario is that people who upgrade frequently also buy good PSUs, but are worried enough about PSU quality that they also replace them at least every 2 upgrade cycles (or at least get a new one and keep using the old one in a secondary PC).
And sorry, but you must essentially have been talking about premium ATX vs. cheap 12VO OEM. That is the only scenario in which “its perfectly possible to have a well selected ATX supply and exceed in base efficiency what you would see on the similar 12VO OEM machines, efficiency largely being determined by power supplies efficiencies at that % load in this situation” is true. ATX PSUs are notoriously inefficient at low loads, and only the insanely priced Titanium tier has any efficiency requirements below 20% load (i.e. 110W for a 550W unit – far outside of the idle power range of even a powerful PC these days). A _very_ good 80+ Gold 750W unit manages 86% efficiency at 10% load (https://www.tomshardware.com/reviews/corsair-rm750x-2021-power-supply-review/2). Most are (much) lower than that. Moving the DC-DC conversion for the lower rails to the motherboard will, at worst, be a like-for-like exchange, given that it’ll still be a switch mode power supply. That’s assuming _less_ efficient converters eating up the gains from lower cable losses. If the converters are equally efficient, you gain net efficiency due to removing cable losses. And for cheaper designs – as most OEM designs are – there will be major efficiency gains due to this mandating DC-DC conversion and making PSUs simpler. AC-12VDC conversion is easily done very efficiently, and simplifying PSU designs also makes it easier to make them more efficient through optimized layouts and lower internal losses.
You’re also ignoring some major realities here: most OEM desktops (the Dells, HPs and Lenovos of the world) already use proprietary non-ATX PSUs – regardless of form factor – and have on-board DC-DC conversion for lower voltage rails. 12VO just standardizes the pinouts and PSUs, making PSUs for these systems replaceable and thus potentially lengthening their useful lifespans, as well as allowing for repurposing the systems later.
I never said PSUs get particularly hot, I just said they get hotter than a motherboard – which they generally do. It’s a smaller box filled with heat-generating components, and most are geared towards silence. They also have tiny little heatsinks. Most PSUs are rated for operation in 40C or 50C ambient temperatures, which means their internal components (often rated for ~125C operation) can run 50-70C above ambient. This is entirely safe for them, but it means a PSU is a generally warm environment. A motherboard generally has far more airflow across it, is a much more open space, and components are more spread out. Case ambients are often 10-15C above room ambient, but the internals of a PSU are much warmer than that again even on highly efficient units – those just run their fans slower (or not at all).
As for fanless PSUs getting “rather common” – that’s quite a stretch! Sure, there are some option. They are great PSUs, but they also require very open cases with lots of airflow or very good layouts for natural convection. They are also typically _way_ overbuilt – a 500W fanless unit is often using the same hardware as a 7-800W actively cooled unit, just with stricter current limiting to keep heat load down. But stick one of these into an avarage case, and it’ll overheat due to the limited airflow.
I have no idea what you mean by current Intel chipsets running hot – do you mean the VRMs? The chipsets (i.e. southbridge) of current motherboards typically have passive cooling and sip a few watts of power, and are spaced far away from the CPU in most ATX designs, closer to the PCIe slots. There are indeed a lot of motherboards with VRM setups that struggle to deliver the 250W+ required to feed the boost clocks of current high end Intel chips, but … how does that matter for this discussion? These DC-DC converters are highly unlikely to be placed close to CPU VRMs, and as I’ve shown previously their heat output at any reasonable load is negligible, on the order of a few watts. The few 12VO boards out there have their DC-DC circuitry close to power inputs and outputs: https://images.anandtech.com/doci/15763/Z490%20Phantom%20Gaming%204SR%28L1%29.png
Placing DC-DC conversion on the motherboard in no way lets OEMs avoid PSU efficiency regulations – in fact it lets them meet them more easily! 80+ isn’t a mandate anywhere, after all, but actual efficiency standards covering PSUs in general exist nearly worldwide. I have no idea where you’re going with OEMs making more money from 12VO – the entire point of standardization is that things are standardized, after all, i.e. replaceable with other standard components, ideally available everywhere. The current state of things, with non-standard, non-ATX being the de facto norm in OEM, is what you’re willfully ignoring here, which 12VO proposes a good fix for, while having few to no detrimental effects for the DIY market. 12VO PSUs will only be more expensive than ATX ones for a short period if at all, as long as they manage to get the standard actually adopted. Production costs and development costs will be _lower_. There’s no reason why 12VO should force you to buy longer service plans or pay extra for specialty replacement parts, _because it is a standard_.
12VO is yet another standard. Not the THE STANDARD – sure its better than every OEM doing entirely their own thing (if it gets adopted), but its still not the standard – Like Apple almost never using standard connectors everyone else does for phones, everyone else is Mini-USB, Then Micro, then C as the standards shift, but there is a clear standard almost everyone uses – and anything not using it (or the slightly older standards) then the company that sold it to you effectively owns you, you have to pay them or maybe one or two others you could select from if you are lucky for everything you may wish to use, because they are not using THE STANDARD but a ‘standard’.
The current Intel processors need so much power there are lots of reports of 100C+ in their support hardware on the current generation chipsets.
I’d also say you are well underselling PSU lifespan, the good ones – which if you are building anything but a really low budget machine you really should have to protect the rest of the computer will last damn nearly forever. I know my first ever PSU had much longer use, in its later years (perhaps still) it was connected to a newer but cheaper setup very suitable for the retiree, or child’s first computer.
And not at all comparing premium to budget – If an OEM builds a mobo set up for high efficiency at expected draw they can do the same to the standard ATX supply they ship with a standard ATX motherboard – it doesn’t cost them anything in where they put the converters, its a custom job they are doing anyway. So the only reason to shift it out of the power supply beyond forcing you to buy their stuff to keep any of it running is bypassing PSU regulations/ badging schemes – as the inefficient stuff isn’t happening in the PSU anymore, so our PSU is 99% efficient, but the whole system can even be really really terribly worse – like VW cheating those exhaust emission by detecting it was being tested, its just a cheat to get the right labels/legal right to sell it…
And having to feed power to the motherboard first, then do the voltage conversion and then run it to the device that needs it is actually almost certainly worse, with a like for like switch – as you add a new 12v run to get from the PSU to the power conversion on the mobo before a similarly long lower voltage run to the device that actually needs the power – you don’t gain much if anything in cable losses in 12VO as you still have long runs of lower voltage, and add a massively longer 12v run. You only gain in efficiency there if the whole PC standards change so you don’t need the lower voltages at all and all voltage conversion is done (hopefully efficiently) by the part consuming the power – which isn’t actually easy and part of why multiple voltages exist in computers as it is!
What goes around comes around… I’m reminded of the mid-70s S-100 power standard, where a large main supply provided a common 8V, and it was up to the individual cards to locally regulate to their desired voltage (5V). All linear at the time, and horribly inefficient by today’s standards, of course.
But, why 12V? Really. There’s plenty of existing 48V heritage to draw from. If you’re going to admit that it’s going to be universally local regulation, then 48V seems the natural next step. Dispense with those big fat 12V power lines. Makes everything lighter, smaller, cheaper, and more efficient.
the larger the step down to the final voltage, the less efficient a DC-DC converter will be. Also good MOSFETS tend to get really expensive once you need them to withstand more then about 20 volts…
Your statement is not consistent with the big bold plot from HP shown in the article above, that clearly shows a higher efficiency with higher input voltage. The different power supply topology explains it, I’m sure (simple buck vs. a coupled-inductor), but as a general rule, copper losses will decrease with lower current & higher voltage.
At high voltage ratios, a simple buck converter is required to have a very short ‘on’ time (so, high peak currents and consequent I^2 losses), which only says the simple buck is not the topology to use for that situation.
That plot is for ac to dc not dc to dc
Which in no way refutes my conjecture that a 48Vdc supply is superior to a 12Vdc supply (if the appropriate converter topology is chosen).
The 1.2 V drop in the input bridge rectifier accounts for 1% of the efficiency loss in a 120Vac power supply, 0.5% in a 240Vac one. That accounts for about a third of the difference in that plot. Can you account for the remainder?
Part of the reason for 240 V being more efficient is going to be active Power Factor Correction. That is basically a boost converter immediately after the bridge rectifier controlling the current draw, and has an output voltage of about 380 V. Once again, it is a smaller voltage difference.
Simple for 12V Fans and Drive motors and RGB wiring. :D
Was the -5v supply ever used for anything other than the substrate bias on the original IBM PC RAM chips?
So that’s what it was for? I think the minus 12 was for serial ports.
Analog circuitry of older ISA sound cards used it as well, for example.
According to Wikipedia it was supplied to the ISA bus for use in things like sound cards (negative supply for op-amps).
Another use found was, “analog data separator circuits found in older floppy controllers”.
Yes, the ISA bus was very hacker friendly, you had all types of signal and power to drive your data acquisition circuits full of op amps and ADCs. Analog rocks!
Does any of this actually leave us with more efficient systems, or is it just making the power supply really efficient (thus satisfying government regulations) while total system efficiency is the same? Or perhaps even worse, since your motherboard manufacturer may not have chosen good components.
That’s an interesting question. The PSU efficiency can be very high but the motherboard has to have several DC-DC converters including one to supply 5V to storage devices almost all of which use both 5V and 12V.
Lenovo has been using 12V only PSUs for many years with a 5V supply on the motherboard able to supply some storage devices supplemented in some models an additional power conversion board to supply 5V to all the storage devices.
I believe part of it is the PSU isn’t tailored for exactly what the motherboard needs, which means they are usually over specced which means the PSU is less likely to be in the peak efficiency range.
The motherboard manufacturer knows what power draw the motherboard needs from the number of chips, number of slots, number of ports, etc…. And can tailor its power supply circuitry better.
According to the tests run by LTT https://www.youtube.com/watch?v=heyGtgdfN7A the total system efficiency is about the same under full or nearly full load but it draws significantly less power at idle.
problem is if the mobo does some of the psu’s work for it, wouldn’t it too fall under regulations? are mobos now going to get 80+ ratings?
Likely not, but given that DC-DC conversion is both extremely simple and typically in the 92-96% efficiency range, that’s hardly a concern. There’s a reason why all high efficiency (80+ platinum/titanium) PSU designs convert AC to 12VDC and then use smaller DC-DC converters for minor rails. It’s simply a more efficient way of doing things.
Since most stuff in the system is going to run at significantly less than 3.3 V, the motherboard already has voltage regulators for it. Right now, either there is going to be a double conversion (12 -> 5 / 3.3 -> ~1.8), or the PSU’s 3.3 V / 5 V rail(s) won’t have much load. This avoids that. There are some devices using 5 V and 3.3 V though, mainly interfaces and storage devices.
point of load regulation is the only way now.
That can be more efficient because the regulator will be tailored to provide the exact current required. Power converters (both AC-DC and DC-DC) tend to be much less efficient at load load factors.
I am scared about the tons of perfectly fine PSU that will go to trash because they are no longer “compatible”. :-/
That bit about it only making sense if everyone up and switches, no adapters … That really didn’t make sense. Manufacturers will have to jump ship to the new standard, but consumers will phase in where necessary, sometimes using a cheap adapter until they can buy an expensive PSU.
Until recently ATX PSU connectors had detachable segments for variants that needed more. My PSU is modular so aside from the +4 on the main connector it offers 4-pin and 8-pin 12v connectors for the CPU power.
If this new connector pinout becomes popular, PSU manufacturers will often support both.
This has one, pretty cool side effect. It will be really easy to power newer systems either directly from DC, or using redundant server power supplies. In servers, what ATX12VO does, was done for quite a long time, either directly on motherboard, or using separate DC-DC block in the chassis, while mains power supplies provided single high-current +12V and +12Vsb lines only.
I think the “obvious negatives” are not necessarily realistic.
Motherboards are already “PSUs”. Your RAM and CPU do not run off direct 12V. VRMs = mini-PSUs. And even this is a stretched analogy. The term “power supply” is ideally reserved for AC to DC conversion only.
It’s nothing new. See every laptop in existence. They’re all single-voltage, as well. VRMs last a long time on mainstream hardware, many rated at 90C and above.
Case fans almost universally run on 12V. The actual concern is SATA.
No thanks. I don’t like the idea of adding even more power controller circuitry to already hot running motherboards. Also, it makes no sense to plug peripherals into the motherboard for power, in my opinion. Plug in too high of a load and instead of the power supply going into a recoverable crowbar mode, the motherboard goes up in smoke, taking everything else with it.
The motherboard will almost certainly have protection. And probably monitoring too.
Welcome to the new feature of our Motherboards – we call it “distributed power failure restart”, it’s the latest and greatest if the 12V supply is good, just chuck the motherboard in the trash and start over….
On the contrary, doesn’t this open the door for far smarter failure modes? If each conversion circuit is separate and in communication with the BIOS, won’t they a) have individual OCP, and thus be capable of shutting down individual power rails, and b) be able to tell the system specifically which rail is failing and how? So instead of an overcurrent scenario causing a hard shutdown, you can have it shut down just the relevant output and have the OS give you a detailed error message? Sure, that wouldn’t help novice users, but neither does a hard shutdown. “I connected a new [thing] to my PC, and now my HDD won’t spin up and my system is giving me an error about overcurrent protection” should be far easier to troubleshoot than “I connected a new [thing] to my PC and now it won’t turn on.”
The amount of extra circuitry is trivial. Motherboards already convert 12V to the relevant voltages for the CPU and RAM. What’s needed is 5V for USB and SATA as well as 3.3V for NMVe and SATA. None of that will be any significant amount of current. Now, instead of PSU manufacturers sticking worst-case-scenario-sized 12V to 5V and 3.3V converters (or, god forbid, AC converters for those voltages like in old/cheap designs), we can get purpose-built conversion that fits the capabilities of the board perfectly. Have 4 SATA ports? Well, then your PSU doesn’t need the capability to convert power for 12 drives, making your power conversion more efficient (especially when you only have a single drive connected).
Ah but 4 SATA ports, but how many PCI slots available to add more with?
Or are you a music producer with lots of weird powered PCI MIDI sound devices?
You can’t with how versatile and modular a PC is spec the on motherboard PSU sanely for every draw it could come under – to make it viable for the highly modular system desktops are for you would need to vastly overspec everything on every motherboard – Much easier and better to leave PSU selection to the system builder who knows this PC will be running whatever peripherals, and therefore needs this level of supply – keep each module doing just what it should for itself.
You can make the desktop into something more like a laptop, with slightly more upgradeablity via this method, but in doing so you have to loose the enormous versatility desktops have. Good for some, not for all.
I disagree. It doesn’t have to hurt flexibility at all. It does of course place more pressure for AIC makers to include the necessary power delivery on their boards unless they run off native PCIe voltages (3.3 and 12, both of which the motherboard of course already needs to provide up to the PCIe slot spec for each slot on the motherboard even on 12VO). This might indeed be slightly problematic for currently existing HBAs and similar expansion cards relying on external power for connected devices, but nearly every other AIC these days runs off 12V and converts its own voltage, as that’s already the only way of getting any real amount of power from a PCIe slot. I’ve even seen discussions of deprecating PCIe 3.3V lanes due to their infrequent use. Converting 12V down to whatever you need is so simple and cheap every AIB maker out there already has dozens of power delivery designs they can copy onto whatever board they’re designing. And again, these DC-DC converters are highly efficient due to being scaled to purpose.
For SATA devices and the like it would be trivial for PSU makers to start selling PCIe 6-pin powered SATA power converters, tiny blocks (perhaps sized to fit a 2.5″ or 3.5″ drive mount?) passing through 12V while providing a couple amps per port of the lower voltages for however many outputs they are rated for. They could even sell cables for modular PSUs with this in-line. This is of course an additional cost to users, and an additional point of failure, but one only needed for specialized applications anyhow, and partially made up for (hopefully) by the cheaper PSUs enabled by 12VO. Given how cheap, safe and easy to work with the components are such converters ought to be very cheap as well.
Sure its trivial to add PCIe card devices for voltage conversions, but then you loose PCI slots, the ATX standard footprints do not have many of those to spare anyway. Plus the power limit through PCI slot is actually pretty low for powering mechanical spinning rust disks or the super fast high draw SSD types – its not going to let you build a system anybody with many large files – like perhaps your serious video editors will need, you as a Colin Furze type start recording in 4 or 8K, its going to eat a drive a project in raw footage probably, heck I run out frequently and I’ve had more HDD in this system than a 12vo system will cope with fairly often over its lifetime (right now its back down to more sane numbers) and on disk useage I’m not actually all that big a user…
Plus half the point of this is to gain efficiency by cutting down on transforming already transformed power… If every slot and device suddenly must convert for itself to run you loose that anyway. And to keep it as versatile as the existing standard you are not running at most efficient power as you must overspec the mobo’s onboard power capabilities too much.
To really make 12vo as flexible as regular ATX style is pretty much impossible, you need so many more global, only game in town changes to the standards of the PC world, its just not practical – better to throw out all the existing legacy stuff and reboot from scratch, which isn’t likely to happen any time soon – as it makes all existing things e-waste or in need of converters to the new standards rather rapidly…
What 12vo systems really do make sense for is the boring office computers, basic home computers, even basic gaming rigs are plausable – the computers that don’t need any flexibility, and are almost better off being laptops as the whole thing tends to be replaced at once, and odds that any device will be added to is almost nill, it just needs a little headroom…
(Apparently I can’t reply to your comment here, so I’ll reply to my own.)
You’re misunderstanding what I’m saying here:
– I never said we should add specific AICs _only_ for voltage conversion – that makes no sense at all. PCIe is a data bus first and foremost, and if you need power, use a PCIe cable. In-line conversion boxes for mounting elsewhere (such as a drive bay) would be the way to go for anything doing purely voltage conversion. A power conversion card fitting in a PCIe slot would be a really, really dumb idea.
– What I was saying, which you seem to have misread, would be that future AICs such as HBAs would need their own power circuitry for connected devices (so a HBA for directly connected drives would need to deliver 5V to connected HDDs, and likely 3.3V for SATA SSDs too), or they would need to rely on external conversion devices such as a backplane. This will of course make for some conversion losses, but no more than with current “one size fits all” PSU designs.
– Also, most AICs _already_ convert whatever power they need from 12V. This is the most efficient route, as 12V can deliver high currents if needed, is ubiquitous, off-the-shelf conversion circuits run in the ~95% efficiency range, and you can scale the conversion to the specific needs of the application.
– Servers – which are often stuffed to the gills with HDDs – already run on pure 12V, and do their DC-DC conversion for minor voltage rails either on the backplane or motherboard. So this is entirely feasible.
As for the point being to gain efficiency by cutting down on transforming already transformed power, that isn’t it. If that was more efficient, then we’d still be using PSUs supplying every voltage from AC. All high efficiency PSUs use DC-DC conversion for minor rails, with only 12V converted from AC – because this is the most efficient. 12VO gains efficiency through making any conversion from 12V made-to-order, scaled to fit its application perfectly, and makes it possible to disable unnecessary/unused conversion circuits. Your current PSU needs to keep supplying its single 3.3V and 5V rails constantly, despite loads on those rails typically being _tiny_. 12VO allows the motherboard to have one 5V conversion circuit for USB (likely on constantly, as it’ll always be in use), one for SATA (only on when needed), etc. And each circuit can be scaled to the rated output of the connected ports/devices rather than some arbitrary number chosen by the PSU manufacturer with heaps of safety margins built in (which inherently lower efficiency).
I mean, if I only had 12V but needed to deliver 3.3V and 5V for SATA wiring, I could go on Ebay today and buy two 3A voltage conversion boards for less than $2 apiece, connect those to a PCIe cable on one end and a SATA chain on the other, and have enough SATA power for a string of drives. And these $2 converters advertise 97% efficiency, which even if likely optimistic, means the conversion loss will be negligible. Off-the-shelf all-in-one 12V-to-SATA conversion solutions are likely to show up as soon as 12VO becomes even remotely common, are likely to be extremely efficient, small, and easy to use.
So 12VO can be exactly as flexible as ATX, but it does of course require more specialized configuration on the part of the user/SI rather than the current one-size-fits-all approach. That’s a given at this point if you want to improve efficiency. Things are already optimized so far that there’s no other viable path forward.
Ah I see, what you mean now – Still doesn’t work with what I’ve seen of 12Vo though – there are not enough 12v outlets on the 12vo power supplies to wire off to every device that will need its own. Certainly can be done, it just hasn’t been as far as I can see – plus that means your 12vo psu needs massively over speccing to be able to provide all that 12v juice. Possibly even going back to the old multiple rail systems just to be sure the core of the computer is on a single rail that can be relied upon (and perhaps that the extra rails can be turned off)..
The thing with HDD filled servers is they work exactly like the current ATX PSU system, its one giant backplane well overspecced if you only partly fill it… Not seen any at all that have lots of converters turned off when bays are empty… So the only way it gains on regular ATX there is the design knows exactly how many disks it can ever be asked to power and can be specced to suit exactly that number (though still with so many disks you must vastly over-spec to what is probably fitted to many servers – super fast spinning rust disks are very power hungry compared to bulk store slow disks and 20x that differential is probably doubling the power draw…).
The main reason 12vo severs are a thing is it makes the PSU smaller and simpler, so its easier to have redundant ones in the smaller form factor, and the server is then able to run directly off its battery backup – vastly more efficient than inverting, and returning to DC. Trimming normal PC versatility off a server doesn’t matter a fig, so cutting out everything a server doesn’t need is normal practice – they are making enough of them that its worth the tooling up cost to make this more restricted but highly optimised computing device, same thing with laptops, but a normal PC isn’t that, its a generalist you really can throw anything into, and you really can’t have optimal efficient power and that versatility at once…
And the thing about transforming already transformed power is a thing, yes DC-DC step down is very efficient but every time you add another one in the chain you loose compared to tapping the source more directly – and anything that only gets 12v in but has to provide 5v for its peripherals and do lots of step downs for its own electronics (as almost no chip runs on 5v) has that extra step – if it had a 5v rail supplied it doesn’t need that extra step, it can just take whatever input voltage it gets and switch it down to what it is required for its own electronics – not also have to produce a transmission voltage it doesn’t need, but the devices do (to then probably step it down themselves).
You also loose on cost and embodied energy every time you add more switching. So to really make 12VO make sense as a complete ATX replacement you need to throw out the current specs entirely – just feed 12v in to everything and have each device have it own transformer – which isn’t a given efficiency gain as with how little actually needs 12v and the efficiencies with different target and source voltages running just 5v, or even down to something like 2v might make more sense – but then you run into current carrying and the like. Its not a simple balancing act with a clear winner for a normal PC – as a normal PC is the ultimate generalist that might be stuffed full of anything. But you can make clear winners 12vo or otherwise as the OEM building your systems without all that headroom to run efficiently as possible with only what you shipped them with – can use a normal ATX and be just as efficient as putting the 5v etc on the mobo by having the normal ATX producing only what the devices fitted will need – a custom power supply rather than effectively custom motherboard, both do exactly the same job efficiency wise in that scenario.
Also I think you would also be surprised just how much the 5V rail on almost every home computer is in use – between wifi cards (that are often USB even if built in to the mobo), sound devices like powered microphones and headphones, Webcams, the blinken lights on many folks keyboards and mice there is a significant 5V draw for many computers, not to mention charging phones and the like – with USB becoming almost the only standard for connecting things to things there is alot of demand for 5V power.
The number of connectors/outlets on the PSU is entirely up to the OEM, and already varies massively on ATX PSUs. 12VO only mandates that it has the 10-pin, an additional 6-pin for optional board power, and a 4+4-pin EPS. The rest is just PCIe power, and you can branch that off however you like if you need more devices connected up to the output limit of your PSU (as long as wire lengths are kept in check and connectors are good quality, obviously). There are less _peripheral_ outputs on the few current 12VO PSUs because _peripheral power_ is provided from the motherboard instead, moving those connectors. That doesn’t mean you couldn’t use a spare PCIe power cable to create more with a voltage converter.
As for ” plus that means your 12vo psu needs massively over speccing to be able to provide all that 12v juice” – why would it mean that? If current PSUs – which, just to repeat myself, _already typically convert everything down from 12VDC internally! – can deliver sufficient power, why wouldn’t a version of the same PSU with those internal DC-DC converters removed be able to deliver sufficient power? You seem to be severely muddling your usage scenarios here. Whether or not your PSU is sufficiently powerful is hardly related to the output standard (within reason – no PC PSU standard is really suited for >2KW, for example).
As for server power planes – well, servers are optimized for space efficiency. Thus, they are designed to run full at all times. That’s the base expectation. Naturally, a consumer PC is not expected to run packed to the gills with components. Which is exactly why it’s reasonable for motherboards to include provisions for powering the included number of ports on the motherboard. Right? If it has eight SATA ports, two x16 PCIe slots and four x1 slots, it needs to be able to deliver [however many amps is expected per connector for SATA, IIRC the spec is 4.5A/wire, though that might not be what is expected, and consumer HDDs don’t exceed 2A on any rail) + 2x 75W PCIe power (IIRC 12V5.5A + 3.3V…3A? Something like that, per slot), + 4x 25W (same 3.3V as x16 slots, lower 12V). That is what the board must be able to deliver – which is already likely to be _far_ more than the system will ever need.
You’re also drawing up a scenario of seemingly cascading power conversions, which … isn’t happening. There’s 12V everywhere, then – where it’s needed – it’s converted once down to whatever is needed. Period. The chain stops there. There are no further conversion steps, though of course there will/might be many branches off that 12V tree. CPUs and GPUs already do this. As does literally anything else with a PCIe or EPS power connector – as you say, nothing actually uses 12V. As do motherboards for RAM. As do PSUs for lower voltages. It’s all converted down from 12V outside of archaic and woefully inefficient PSU designs that convert 5V and 3.3V directly from AC. Local, usage-specific DC-DC converters are _extremely_ efficient. They’re also small, cheap, and easy to implement.
One key efficiency improvement from this: lower cable losses. Most PSUs have ~1m cables. Say you need 3A of 3.3V power for a device – like a high end m.2 NVMe SSD. With an ATX PSU, you first convert that from 12V (~96% efficient), then transfer it over a wire (18AWG in a good PSU) leading to a ~3.8% voltage drop over the cable, which is a direct efficiency loss to heat in the wire (with the PSU typically boosting output voltages to compensate). At 12V1A (which is more total power!) and the same wire and length, that loss is less than 1/10th at .29% (calculated here: https://www.rapidtables.com/calc/wire/voltage-drop-calculator.html), while conversion efficiency at the end of the cable down to 3.3V is ~the same as internally with the ATX PSU as it’s the same type of circuit. (Though this is also potentially more efficient due to being scaled to fit its use case better – it might reach 97% instead of 96-95%, for example – but let’s assume the DC-DC circuits are equally efficient for simplicity.) So with the ATX PSU you end up with 100*0.96*0.962=~92.3% efficiency for delivering 3.3V3A. With ATX12VO and a competently implemented DC-DC converter you get 100*0.96*0.9971=95.72% efficiency. Whatever conversion might happen at a device level from 3.3V is obviously the same across both. That’s a pretty significant increase in efficiency, right? And that’s the main reason for going 12V for any central power distribution. Local conversion from 12V to a lower voltage is (except for extreme edge cases) always more efficient than transferring a lower voltage over any meaningful wire length.
The extra switching losses are accounted for in the DC-DC conversion efficiency numbers, and as you see above are nowhere near the gains from removing very low voltage wires from the system.
You’re entirely right that this is a stopgap, and mandating _literal_ 12V _only_ in the system (i.e. no other voltages delivered through the PCIe slot) would further increase efficiency. It’s especially a shame that m.2 drives use 3.3V due to this hurting overall system efficiency (the drives themselves convert this both up and down to run their controllers and DRAM and have the necessary voltages for reading and writing NAND), but that ship has sailed, and can still be overcome by just putting a small 12V-3.3V converter next to each m.2 slot (or a common one for however many slots the board has). It’ll still be more efficient than outputting this from the PSU through wiring.
You’re right that 5V sees some load, though it’s not _that_ high. PC USB ports typically at most allow for fast charging (more than 1A) over a single port. So that’s 3A max, plus 1A for however many other ports there are – but most USB devices like mice and keyboards use a few mA. Even USB HDDs use RGB keyboards and stuff use more, but again, there’s one per system. USB-C on motherboards must be able to deliver 5V3A, so that’s something. But most devices don’t use anywhere near that. My 5TB 2.5″ external HDD stays well below 1A at all times (measured with a USB-C power meter), and that’s as high capacity and performance you get an USB-powered HDD. So something like 4A in “normal” high usage with 6A high usage + phone charging is reasonable. And delivering that with an on-board converter is trivial.
As for m.2/mPCIe WiFi cards, they aren’t USB, but their onboard Bluetooth modules are :) WiFi modules are PCIe, and will work (without BT) in even non-USB-enabled m.2/mPCIe slots. But yes, they can use a (trivial) amount of 5V for those BT modules.
I would expect that power supply manufacturers could go ahead with ATX12VO and also provide the adapter from that to regular ATX. This would not have the same efficiency loss as adapters that go the other way.
I would definitely expect adapters that go the other way to be in plentiful supply, should this standard ever take off.
The main question is which way will motherboard makers go? I can understand them being resistant until ATX12VO supplies become popular, but it seems like a chicken/egg problem.
An ATX12VO-to-ATX converter could indeed easily be made (existing picoPSU/DC-ATX boards are essentially exactly that, just generating their own 5VSB from scratch). There is inherent efficiency loss to this too though, as they’d need to convert 12V to 5V, 3.3V and 12VSVB to 5VSB. Efficiency losses are as such likely to be similar – but also low due to the low utilization of these voltage rails in current PCs. ATX-to-ATX12VO conversion is a bit simpler due to only needing to convert one voltage (5VSB to 12VSB), but that can run afoul of 5VSB current limits in the ATX PSU, and might require a second power cable from the PSU due to the additional 12V wiring in the ATX12VO connector (unless you want to run your 24-pin out of spec, of course).
In South Africa it’s 240V, but the mines use 575V. i have heard the mines also use 110V for lighting. By the numbers It is estimated that the average miner will steal 3 globes before realizing the globes in the mine wont work at home and leave them alone.
Sounds like the mines need to pay better.
Maybe the average miner blows up the first globe and, wise from his/her misstake, connects the next two in series :)
I wasn’t so smart: When I blew up a 120V projector lamp by plugging it into 240V (oops), I thought “Oh, that’s easy: just use a diode and get only the top half of the waveform!” I thought I was clever to have thought of that, wired a diode into the supply cord, and promptly blew another lamp. Fortunately, before my supply of lamps ran out, I sat down and figured out why a diode won’t drop a 240 Vac line voltage low enough to run a 120V lamp. I won’t spoil the surprise — it’s fun to figure it out yourself. Just remember heating goes as I squared…
So, is Intel looking at making money licensing the new standard?
Even a U.S. patent examiner should laugh at any attempt to get a patent for modifying an old power connector by removing some obsolete lines. There is no new intellectual property involved here. There is plenty of prior art in the field of 12V DC power supply.
I can see why they want to do it – but I don’t think it is a good idea. Having more power circuits on the motherboard simply means more chance the motherboard is going to have a problem… And I much prefer changing power supplies than motherboards!
The Seasonic’s CONNECT seems a better way to go..
CONNECT places massive restrictions on case form factor for compatibility though. Essentially all SFF PCs are impossible using a system like this. Plus, you miss out on the major benefit of the system which is made-to-measure DC-DC conversion. A one-size-fits-all voltage converter will always be less efficient than one tuned for a specific output current.
and it will always be easier to replace as well. How much power are we really talking about for the low voltage lines ie how much power will it save by shifting this stuff to the motherboard?
Not much, admittedly, but when good PSUs these days run at 92-94% (or even higher) efficiency under high loads, the core concern is increasing efficiency at low loads (where even high end PSUs routinely dip below 80%, and which isn’t covered by 80+ standards, and where most PCs operate for the vast majority of time), which is precisely where made-to-measure power conversion has the greatest advantages – through simply not being overbuilt. As for replaceability, I don’t see it as an issue. How often do motherboards fail due to the CPU or RAM VRMs failing? Essentially never. This circuitry will be a smaller version of the same thing. DC-DC conversion is simple, cheap, efficient and highly robust. If it’s also coupled to the BIOS and has proper protections built in (i.e. overcurrent, over-/undervoltage, thermal, short circuit, etc.), which I’m assuming the 12VO standard will mandate, then there’s essentially zero chance of these conversion circuits failing within the useful lifetime of the motherboard.
They keep front loading components onto the motherboard driving up the cost of mobo’s. I have a psu that is 15 years old running 4 different computers over it’s life span. Don’t know when it’s going to quit.
I don’t see why the industry has to switch over all at once for this to catch on. Surely parts vendors can just sell both types of motherboards and PSUs.
it kind of makes sense as an sff builder. it also stands to greatly simplify cabling in my builds. right now im using modular sfx supplies so i can omit most of the unneeded cables. my current build only has the 24 pin atx header, the 8-pin cpu header, and the gpu header (i want to say its an 8-pin). getting the atx connector down to 10 pins really saves board real estate and simplifies making custom cables.
on mini-itx, board real estate is very important. removing 10 pins also frees up space for an extra fan or a usb c header. but not if you have sata power out connectors in their place. getting rid of sata and external drive power delivery entirely seems like a very good idea. i consider it legacy as its grossly inferior to m.2 for all but bulk storage, and 2-4tb gumstick drives are available. at least move external drive power and data to a single cable instead of 2 and then only provide one or two channels. there is still the media center pc use case that is going to want spinning disk storage, but i hope bigger ssd options make that point moot by the time the standard takes hold. cpus are getting more pci-e lanes and having more than 2 onboard m.2 devices would be awesome.
i tell you i do not like the power hubs though. full atx seems like a better fit for full atx builds. having to buy a second smps box to connect all your drives seems like a bad idea when i can just use a full atx supply. pc build culture has gotten a little bit out of hand. i dont consider rgb, watercooling, and a ginormous case with a big emi hole in the side to be the pinnacle of pc technology. for those people ‘whats a few more cables, il just get a case with a cable management compartment’ and never mind the 25% increase in pc footprint and the vastly larger number of potential failure points. with reguards to cabling, less is more. i dont care what size your mobo is.
The Seasonic Connect PSUs come with the power hub, but it is about £20 more than the equivalent ATX2.0 model.
Of course, if your build is *really* constrained for space, you could use a Pico PSU, which uses a laptop-style power brick outside the system to do the AC->DC conversion, and does the DC->DC conversion on a tiny board that mounts directly to the main ATX connector on the mobo. They don’t seem to make one bigger than 160W though.
yea, ive seen those. i always wanted to try one. the corsair sfx supplies ive been using are pretty reliable though. you dont really need something like a pico unless you are making performance compromises or need a machine for a specific application, like a htpc or back of monitor pc. even then power bricks are the devil’s work.
I can see this working well for corporate, government, and education customers, as greater energy efficiency means they’ll be paying less to cool their buildings, in addition to a lower electric bill. The typical systems that come to mind are Dell’s OptiPlex and HP’s ProDesk lines, which employ some proprietary forms of ATX12VO already (or at least the ProDesk PCs did when I last looked at one). I’ve noticed that with higher-efficiency PSUs over the years has also come better power factors, many of the recent ones I’ve measured having p.f. around 0.90-0.97. Those same customers will appreciate that, as well.
As for what a change to ATX12VO means to me personally, I can say “not much,” as long as I can buy an affordable PSU made by a reputable manufacturer, and the motherboards using the standard are rock-solid. That said, getting power to components like disk drives is a concern, and why the old ATX PSUs will be with us for a while. I’ve had to get a regular ATX PSU to work with an HP ATX12VO motherboard for a customer. That “only” took a bit of pin-swapping, finding a DC-DC converter, and performing some minimal splicing to work. It was a one-off job, and I’d prefer to not have to do it that way ever again, especially for my own systems. I suppose that means I’m in favor of an industry-wide standard like ATX12VO being adopted by manufacturers.
Last note: that graph of efficiency vs load is familiar, and I’m still puzzled by people building gaming PCs going for the highest output PSU they can afford, even if the math says they’ll only ever use a quarter of its potential. “Future expansion”? I dunno. Most of my PCs use about 20-30 W at idle, top out well under 300 W at maximum load, and they’re all about five years old, with the lowest-output Corsair 80-PLUS gold PSUs available at the time. No, I’m not a gamer. LoL
Might be in how long people hang onto things. Plus ever changing requirements to more powerful GPU/CPUs. It’s nice not having to buy a new PSU with every hardware refresh.
Big orgs typically lease their end-user systems so they can swap them all out quickly when the hardware requirements change. Also they are all on maintenance contracts so they get swapped out when the contracts expire. The market for tinkerers who mess with their hardware gets smaller every year and will soon be completely ignored, thank goodness. Catering to these people has stunted progress for decades, our “modern” hardware is hopelessly crippled with legacy crap.
Interesting development… I’ve been using pico-ATX adaptors to run my server cluster off 12V for years now.
https://stuartl.longlandclan.id.au/blog/projects/project-solar-cluster/ (Yes, was hosted on hackaday.io before I got fed up with the spam.)
Not often I find myself _ahead_ of an industry!
A decent article, but it does have some blind spots. For example, in terms of board space needed for power conversion, that will in many cases be made up for by the much smaller area needed for the power connectors. The new 10-pin connector is after all nearly 2/5ths of the old 24-pin, while being able to deliver more current. The EPS 4/8-pin stays the same for CPU power delivery, while there’s an option for an extra 6-pin (same plug and pinout as PCIe power, but rated for a higher current) for higher current applications – this will be unnecessary for all ITX boards, for example. So the plug takes up much less space. Of course a high current convesion circuit will need more space than what the plug leaves behind, but most motherboards won’t need high current 3.3V or 5V.
The article also handily skips over the efficiency benefits of built-to-purpose power conversion – current ATX PSUs are to some extent built for a worst-case scenario of 3.3V and 5V conversion, capable of delivering those voltages _far_ in excess of what a modern PC needs, and thus making said conversions less efficient. On-board conversion scaled to fit the connectors on the board (e.g. a beefier conversion circuit if you have 8 SATA ports than if you have 4) will improve efficiency further – especially as those outputs are typically sparsely populated in most PCs. A single drive running off a converter specced for 4 drives is going to be far more efficient than one runnning off a current ATX PSU specced for 10-20 drives.
For the high current power rails 12V makes sense, but for standby? I would have lowered the standby voltage to 3.3V since that is what is used by most super I/O chips. With 12V there will always have to be a dc-dc converter on the mainboard. I can’t image this to be more efficient.
What is the point of California specifying energy efficiency targets if the users just squander it anyway running bitcoin mining, playing games and running virus scanners for Windoze?
Surely they would be better off legislating for Linux and making bitcoin illegal?
It’s apparently a little known fact that humans can walk and chew gum at the same time.
efficiency means less heat, which means more overclocking. if hippies gonna hippie, at least use the gains in the most wasteful way possible. also use a eth miner as your screen saver.
Go to your favorite electronic parts supplier and survey the costs of DC-DC buck ICs. Above 35V, there’s a price increase. You may be able to make your argument for 24Vdc, but 48Vdc adds significant cost.
If only they chose a single 24V rail. That would make future outdated computer parts so much more suitable for a second life as 3d printer power supplies.
All those scrap inkjet printers may supply higher voltage supplies.
I once needed a higher voltage for a Powerbook, and for some reason realized inkjets have them. I think the first I opened had the right voltage, and on a separate board, easy to extract.
Interesting. I’m happy with a 5VO Raspberry Pi tho.