For many DIY hardware projects, the most movement it’s likely to see is when we pick the assembled unit up off the workbench and carry it to wherever it’s destined to spend the rest of its functional life. From weather sensors to smart mirrors, there’s a huge array of devices that don’t need to move one millimeter to function. But eventually, you’re likely to run into a project that’s a bit more dynamic. Maybe you’d like to motorize your window shades, or go all out and build a remote controlled rover. With these more active designs comes a whole slew of new problems you may never have encountered before.
Luckily for us, folks like Jeremy Fielding are out there and willing to share their knowledge. In his fascinating presentation for the 2021 Hackaday Remoticon, Building Hardware that Moves: the Fundamentals that Everyone Should Know, he took viewers on a whirlwind tour of what he’s learned about designing and building complex machines from his years of professional experience. Whether its a relatively simple articulated workbench for the shop, a gargantuan earthmoving machine, or a high-dexterity robotic arm, each project he’s worked on has presented unique challenges that needed to be solved.
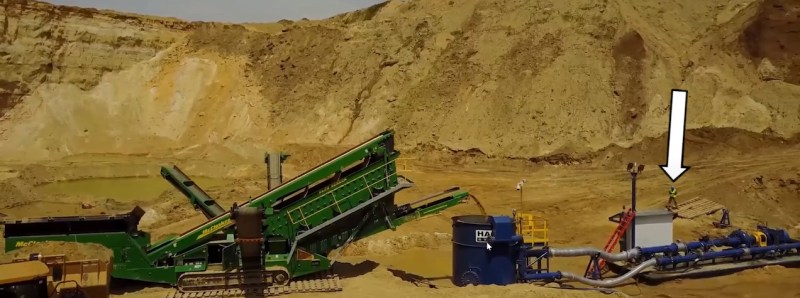
A lot of the projects that Jeremy has worked on are on a much larger scale than what your average hobbyist is ever going to run into. When there’s an arrow pointing out the tiny human in a picture of you and the machine you’re currently working on, you know things are getting serious. But as anyone who’s watched his YouTube videos knows, he’s got a real knack for taking these high-level concepts and distilling them into something more digestible for the home gamer.
Practice Makes Perfect
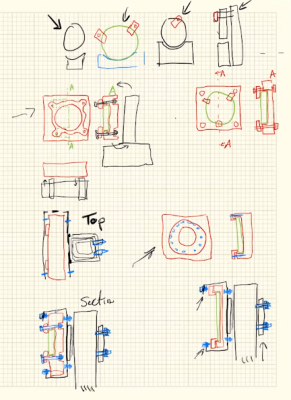
If you only take one thing away from Building Hardware that Moves, it’s that prototyping is a step to be skipped at your own peril. These days we have incredible tools at our disposal, especially when it comes to CAD software, but nothing quite replaces actually putting your design together in the real-world and seeing how all the moving pieces interact with each other.
That said, a prototype doesn’t need to be as strong or rigid as the final product. Before you start cutting or welding, Jeremy says you can lay out plenty of the groundwork with nothing more exotic than thick cardboard and tape. Even if you do want to make your prototype out of something slightly more long-lasting, such as wood, it doesn’t necessarily need to be full scale either. A miniature version of your design might not give you quite the same insight as a 1:1 representation, but the reduced time and materials needed to build it can go a long way towards making up for the reduced fidelity.
Jeremy also says there’s a lot to be gained from simply drawing out your design concepts by hand. Graph paper is ideal as it will let you establish a scale, but it’s not strictly required. At this point, you’re just trying to figure out what the major shapes of the mechanism will look like. This kind of rough paper sketching can often save you a few hardware revisions down the line by shaking loose some of the low-hanging fruit early on.
Picking Your Power
After you’ve come up with a mechanical design and are fairly sure it will work as you expected thanks to your prototype, the next step is figuring out how to power the thing. In his presentation, Jeremy spends a considerable amount of time talking about many of the different motors and actuators available at both the professional and hobbyists budget. Just as we’re fortunate to have access to powerful tools, we can also count ourselves lucky in the locomotion department: as today there’s a whole wide world of ways to get your creation moving without breaking the bank.
For example, he talks about the widespread availability of low-cost brushless DC motors that can be directly attributed to the exploding popularity of RC quadcopters and other aircraft. While these motors require more sophisticated control circuitry than the simple permanent magnet motors we’ve all pulled out of a broken toy or gadget over the years, the clear and numerous benefits offered by the newer technology (higher power-to-weight ratio, increased energy efficiency, better speed control, lower noise, longer lifespan, etc) are going to be worth the added effort in many applications.
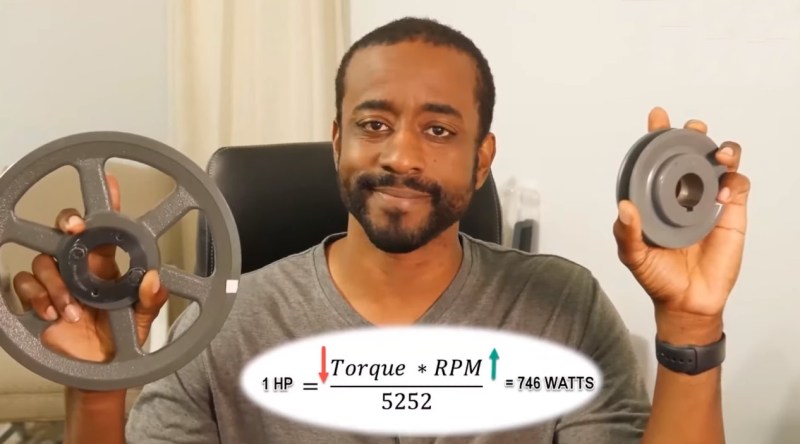
As you might expect with his industrial experience, Jeremy isn’t afraid of moving over to AC motors when the project demands it. He takes the viewer through several types of AC motors, and even breaks down where you’re most likely to find each type should you find yourself on the hunt for a particular powerplant. An accomplished scavenger of parts himself, he’s learned to expect a single-phase induction motor in that curbside washing machine or dryer, while newer treadmills are sometimes hiding a three-phase unit.
But perhaps we’re getting ahead of ourselves here. How do you even know which motor you’ll need for a given application? To that end, Jeremy goes into detail about finding the identifying the torque and speed requirements for a given task, and then using those figures to determine which kind of powertrain you’ll need. Note we didn’t say motor. That’s because, in many cases, you’re going to need gears, pulleys, belts, or some other means of mating the motor to the rest of the machine. This is where some people start to feel overwhelmed, but with some simple practical examples, Jeremy shows that figuring it all out isn’t nearly as difficult as you probably think.
On Your Mark, Get Set, Go!
Jeremy’s presentation at the 2021 Remoticon went on till just shy of the hour mark, but watching it now, it certainly won’t feel that way. With such a fantastic communicator, you’ll be halfway through the video before you know it. In fact, don’t be surprised if you find yourself hungry for more of his particular brand of technical education when it’s all said and done. Luckily, he’s got a nearly a decade’s worth of videos you can check out, many of which dig deeper into some of the topics touched on during the course of Building Hardware that Moves: the Fundamentals that Everyone Should Know.
Between Jeremy’s easy style and infectious optimism, it’s also likely you’ll come away from this presentation with a sudden urge to make something that will actually get off the workbench and move around. Don’t worry, it’s only natural. Just take a deep breath, prototype a couple of linkages, and let us know when you’ve got it working.
I don’t want to sound ungrateful, but is Rob Weinstein’s talk available?
Not at the moment, we wanted to get the keynotes out first. But all the Remoticon talks will eventually be broken up into individual videos like this.
Thank you.
I like Jeremy, I subbed to him back in the shed days when he was asking his audience what we did and what we wanted to see. I knew back then he had much more to offer than a couple shop made carts :)
I would like to team up with Jeremy with a car design I would like to prototype.
pff. if only car builders would do this. repairing would not be such a pain in the bud.
Outstanding talk. Thanks so much, Jeremy!