When it comes to placing a project underwater, the easy way out is to just stick it in some sort of waterproof container, cover it with hot glue, and call it a day. But when you need to keep water out for several years, things get significantly harder. Luckily, [Patricia Beddows] and [Edward Mallon] from the Cave Pearl Project have written up their years of experience waterproofing data loggers for long-term deployment, making the process easier for the rest of us.
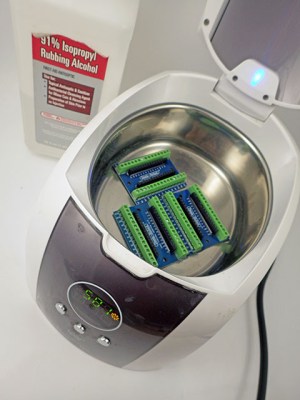
It starts with the actual board itself. Many SMD boards have at least some flux left over from the assembly process, which the duo notes has a tendency to pull water in under components. So the first step is to clean them thoroughly with an ultrasonic cleaner or toothbrush, though some parts such as RTCs, MEMs, or pressure sensors need to be handled with significant care.
Actual waterproofing starts with a coating like 422-B or nail polish which each have pros and cons. [Patricia] and [Edward] often apply coatings to PCBs even if they plan to otherwise seal it as it offers a final line of defense. The cut edges of PCBs need to be protected so that water can’t seep between layers, though care needs to be made for connectors like SD cards.
Encapsulation with a variety of materials such as hot glue, heat shrink tubing, superglue and baking soda, silicone rubber, liquid epoxy, paste epoxy (like J-B Weld), or even wax are all commented on. The biggest problem is that a material can be waterproof but not water vapor proof. This means that condensation can build up inside a housing. Temperature swings also can play havoc with sealings, causing gaps to appear as it expands or contracts.
Overall, it’s an incredible guide with helpful tips and tricks for anyone logging data underwater for science or even just trying to waterproof their favorite watch.
Love his blog posts on everything under-water and low power logging. His blog is such a wealth of information. I’m tempted to say: second to none…
Just put it in oil!
There is a long tradition in the marine submersibles industry of housing electronics in oil-filled chambers (connected to a soft, pressure-equalizing bladder). Oil has the advantage of low viscosity, so it can penetrate everywhere (like under your surface-mount parts). Any high-viscosity potting material will be riddled with air bubbles unless you use a vacuum chamber. Residual air bubbles inside an elastomer will compress at-depth and can cause mechanical damage. Even at a depth of 15 feet (5 meter deep river) we’re talking 2 atmospheres. At 75 feet (5 atmospheres) air bubbles in silicone can compress to 20% of their at-surface volume. (Pop goes the SMT chip!) So yes, clean, clean, clean before potting, and use a vacuum chamber.
and if, heaven forbid, water or air DO get in, if you packed it in bearing grease with the aforementioned bladder, vacuum debubbling, etc., your creation has a very slightly better chance
Btw, at 15 ft pressure is aprox 1.5 atm. At 75 ft is aprox 3.3 atm. 1 atm at each 30ft plus 1. Regards,
Poor man’s Parylene: clear acrylic spray paint. Especially good after running the board through the dishwasher then a good spray-down with methanol: yields super-good adhesion.
Now that’s an approach I haven’t tried. I have some similar problems, and tend to be very careful with ANYthing sprayed-on, as a whole host of sensors will die a short sharp death under those sort of conditions. Have you tried this approach with submersed electronics over periods of months to a year or so?
Definitely not suitable for many sensors, or anything with pores. And probably not suitable for direct submersion: It still leaves the hardware susceptible to mechanical damage. That said, I have used it for immersed ultrasound sensor sealing in a relatively benign lab environment.
I don’t often have access to a Parylene chamber, but use that instead if I can. I use the spray paint for conformal coating on boards for use in locations of high humidity, outdoor, and possible incidental water. I have an outdoor sensor interface board coated suchly that’s still in service 20+ years on. It’s in an electrical box that keeps raccoons out, but the spiders still get in there, so not really environmentally sealed.
I got the idea comparing the MSDS sheets for ‘real’ acrylic conformal spray coatings, and acrylic paint. All that’s missing is the UV indicator, and the price tag :-)
Back in my USAF days we used to use HumiSeal on our avionics PCBs. Its still made, and they clain to offer free samples on their website.
https://chasecorp.com/HumiSeal/
I’ve also used Macromelt but even as the link says, it a low-pressure injection molding material similasr to hot glue. It can even come in sticks like hot glue does.
https://krayden.com/macromelt-low-pressure-molding-materials/
Excellent resource. Tanks for documenting your processes so well.
I have had great luck over the years with the silicone conformal coatings (though the stuffs pretty nasty). Primarily on motherboards while overclocking. Other things we have used to great success is potting via pouring liquid petroleum jelly. Kneadable art erasers are pretty decent too. As a press on material.
The Petroleum jelly doesn’t work so well if your getting stuff hot. As it will become a liquid again. It can also be a bit of a pain in the ass to clean back up. But a trip or two through the dishwasher usually cleans them right up :). But you will want to remove as much as possible before hand.
Just never ever use condensation cure silicone on electronics. That’s the stuff that smells like vinegar. It uses evaporation of acetic acid to cure the silicone. While mild, that acid will eat electronic components and PCB traces. Aquarium safe condensation cure silicone might be safe for electronics, but it would have to be applied in several thin layers for the evaporation to work so all of it can cure.
That’s useful info, thanks!
Many years ago USNavy used “conformal coatings” on shipboard electronics. This stuff will properly cover sharp corners (circuit board corners and edges) where many spray applied coatings fail. It is fairly thick urethane so no good on heat generating components that have no hear sink. We also used a pourable 2 part epoxy “potting compound” to cover soldered connections to Cannon plugs and some underwater wire connectors. These materials are still available but people addicted to brand names will never discover them. Google the “ generic” phrases above to locate sources. This is not a new problem.
I think if you read the post, they cover much of that… as well as when those approaches fail. for example they use conformal coating (not the sprayable kind, for multiple reasons), and pot the electronics in two-part slow-cure epoxies… which, can fail with regards to water vapor penetration, or can flex under pressure breaking contacts… or, in the case of their work, the epoxy is literally dug in to and eaten by marine organisms.
It’s a fascinating read, where they’ve clearly learned a lot from the experiences of other people, but then have gone the extra step to actually TEST those ideas… and, some hold up better than others.
Did had a look at Underwater Magic adhesive & sealant?
As an underwater robotics engineer, this drives me crazy. There are off-the-shelf solutions to this problem that are trivially easy. The easiest is 3M Scotchcast, durable, industry-proven polyurethane potting compound. Then there are the various Devcon products. Any money you save from futzing around with diy alternatives (hot glue? Are you kidding me?) is going to going to cost you tenfold when the device fails unexpectedly in the wild.
I usually avoid reacting to this kind comment but I have to ask: Did you actually read the post?
By all means please reference the data showing that some expensive solution from Devcon is more resilient than just coating a board with $1 worth of CA glue hardened with baking soda. After years of such criticism, I’d make the general observation that ‘trivially easy’ to a professional engineer almost always involves parts and/or methods that are impossible to replicate in the field – where our research actually takes place. We’ve used plenty of commercial kit side-by-side with our DIY loggers over the years, and it rarely runs much longer out in the real world. Even if it did: critters, theft and hurricanes mean the significant amount of money invested in professional equipment is often wasted. Not to mention the number of times I’ve had to repair some cracked housing or battery holder using exactly these techniques in some small village in the middle of nowhere. I humbly suggest that the reason this kind of DIY stuff annoys you is that you’re simply not the target audience for it.
I think you missed a point. He’s not speaking to just a little weatherproofing. That can be done with all kinds of trivial methods. I’d like to see those hold up to constant immersion and high pressure at depth such as with underwater robotics or (as I do) downhole electronics. If you have any contamination or voids, your stuff will fail.
I am not some fanboy of 3M, but we’ve had a lot of other solutions fail miserably and the 3M stuff, as expensive as it is, does the job. When it cost tens of thousands just to access your stufff, that extra cost is, in the end, trivial.
Fair enough. I probably should have started the post with the proviso that we only deploy our DIY loggers to typical sport diving depths because we have to retrieve everything from the caves ‘by hand’. Within that context we get solid multi-year deployments out of those DIY housings. 130ft is shallow for rig inspection drones or deeper down-hole work, so in deeper water: yes, we’d go with commercial housings and ScotchCast like everybody else. But I did highlight those industrial options in the original post, and why we went looking for alternatives.
Hmm… I’d also note that, doing a little bit of research, the original author apparently has well over 100 of these devices working “in the wild”, and has been doing this for a decade or more, under some challenging conditions (tropical sun, salt water immersion, banging about during field deployments)… and they’re doing it on a shoestring budget not supported by a corporate bankroll or large equipment grants. It’s ALL garage-style DIY stuff… and, the proof is in the pudding, it seems to be working.
You have a good suggestion however that’s worth investigating. Looking at something like 3M Scotchcast on Amazon, it seems I could get it for about $50 for 200 grams, is that correct? I need to seal my system under a layer of resin that’s about 1 [cm] deep with an area of around 20 [cm^2], so I’d need about 20 [cm^3] or maybe (assuming a close to water-like density) 20 grams of Scotchcast assuming no waste? So that bit of Scotchcast will cost me $5, but my entire electronics payload only costs about $15 – your proposed solution is a very significant fraction of the entire cost of the device.
There are at least two approaches to a workable system: mil-spec and bomb-proof (but you can afford very few units), or inexpensive and graceful-failing (like providing multiple units so that you have redundancy). Both approaches have their place… it might not be wise to dismiss out of hand either option.
What about compressed air/nitrogen/argon with oxygen absorbers and silica gel? Nothing toxic, nothing hard to repair, potentially cheap-ish(PVC pipe is unsafe at high pressure but I doubt it’s going to burst at 5psi), and leaks are detectable via putting a pressure sensor on the board. Plus, you can run cables inside tubing or fire hose and not worry about special connectors.
Bike pumps and Schrader valves should be enough if you’ve got an a desiccant inside and don’t have to worry about condensation.
In my experience, you don’t need an inert atmosphere; simply one without a conductive media. Putting a small positive pressure on the inside is difficult, as that pressure will change with temperature (leave your sealed system in the sun and it overpressures; drop it in cold water and the pressure drops so low it’s below the external pressure again) and has to accommodate the external pressure (you may be at +5 psi on the surface… but place your unit just 30′ down and you are already at a pressure of -10 psi). This is in addition to handling odd gases. And the bigger problem comes from the fact that here the sensors need to be exposed to ambient (often wet) conditions, but the supporting electronics need to be protected. That’s tough, and a balance. And cables through simple tubing is fine… until you realize that somewhere, you have to have a junction, (cable connection, etc.), and you’re back to trying to figure out special connectors on a DIY budget.
For a permanent seal, try E-6000 urethane (or equivalent). Not horribly expensive and easy to get if you’re just doing a few boards or enclosures. Sticks to virtually everything and is self leveling. Don’t get it in connectors or you’ll never get it out. Used it in machined nylon jack panels for systems continuously covered in water and it kept it’s seal. Had to slice it out when replacing a jack though.
Has anyone tried Sugru? Moldable silicone rubber glue. Sold at most Home Depot’s, Amazon, etc.
Not a perfect solution for everything but it’s strong, waterproof, non-conductive.
https://web-assets.sugru.com/page_component/file3/15427/PI-Sheet_41231_-_41237__41281_-_41287.pdf
I have, it has a short shelf life and is still quite fragile once cured.
In our experience it works really well for one specific use: fixing the point where power cables emerge from power bricks. But the little bubble-gum packages they sell it in don’t stand up well to fieldwork conditions because they puncture easily. So they are usually only good for the single trip you buy them for. Cheap electricians self-annealing rubber tape does the same job (and more) and has better shelf life but it is pretty ugly by comparison to the nice smooth look you can get out of Sugru. So it’s worth the money only if you need the aesthetic aspect.