Although generally hydrogen is only mentioned within the context of transportation and energy storage, by far the most useful applications are found in industrial applications, including for the chemical industry, the manufacturing of steel, as well as that of methanol and fertilizer. This is illustrated by how today most of all hydrogen produced today is used for these industrial applications, as well as for applications such as cooling turbo generators, with demand for hydrogen in these applications rapidly increasing.
Currently virtually all hydrogen produced today comes from natural gas, via steam methane reformation (SMR), with potentially methane pyrolysis making natural gas-derived hydrogen a low-carbon source. The remainder of hydrogen comes from coal gasification and a small fraction from electrolysis of water. The hydrogen is often produced on-site, especially at industrial plants and thermal power plants. So aside from any decarbonization efforts, there are many uses for hydrogen which the public appears to be generally unaware of.
This leads us to the somewhat controversial hydrogen ladder.
Gaseous Priorities
Some among us may already have come across the clean hydrogen ladder, as popularized by Michael Liebreich. This is similar to the clean hydrogen pyramid in that it tries to capture the most essential and most economical hydrogen applications. For example with the primary industrial uses highlighted, we get the following:
The controversial part of this hydrogen ladder comes mostly from the placement of categories such as ‘Long-term storage’ and ‘Off-road vehicles’, with a CleanTechnica article series (part 1, part 2) by Michael Barnard and chemical process engineer Paul Martin going into some level of detail here. As far as long-term energy storage using hydrogen goes, this is a topic that we have covered in a previous article on energy storage systems, along with an article on more practical grid-level storage technologies.
When we just focus on the ‘A’ and ‘B’ line categories that are highlighted in this image, it is important to remember that these categories contain essentially all major forms of current hydrogen usage, along with a number which were mentioned earlier, such as the use as coolant, but which are not covered in this image. The biggest use of hydrogen by far, however, is that for ammonia (NH3) production. Ammonia is used in solvents, household cleansing agent, as an antiseptic, as a refrigerant (R717), in sulfurous oxide (SO2) and nitrous oxide (NOx) scrubbers, but perhaps most essentially in the production of fertilizer.
A more controversial application of ammonia is that as a fuel, since the combustion of NH3 in an oxygen-containing atmosphere produces various pollutants, including N2O (nitrous oxide), as noted in recent studies by Juan D. Gonzalez et al. (2017) and S. Mashruk et al. (2021). Nitrous oxide, also known as laughing gas, is a potent greenhouse gas, and is neurotoxic, being an NMDA receptor antagonist. Due to such issues, ammonia as a fuel is unlikely to see significant use where alternatives exist.
Hot Hydrogen
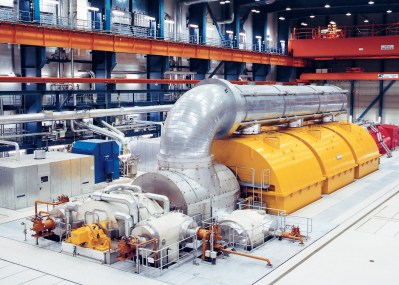
Among gaseous coolants, hydrogen is a popular choice, as it has significantly higher thermal conductivity relative to other gases, has high specific heat capacity, low density and thus very low friction in applications where this really matters, such as in generators. This is why turbo generators are usually cooled with hydrogen gas, with the heated gas passed through a gas-to-water heat exchanger before it is recirculated. The maintenance of these hydrogen-cooled turbo generators also leads to one of the more exciting features of hydrogen: its ability to combust in air at hydrogen concentrations between 4% and 74%.
Combined with hydrogen’s auto-ignition point at 571 °C, this makes it essential to prevent leakage of air into the generator and vice versa. Before any maintenance can be performed on the turbo generator, the hydrogen has to be purged, which makes it a trade-off between increased efficiency and ease of maintenance. And as noted earlier, most power plants have an on-site electrolyser to generate replacement hydrogen when they need to.
Hydrogen’s thermal conductivity is also why it is used in some welding gases, with certain studies claiming that it improves weld quality on even lower quality steel. When looking at the various blends from a single manufacturer, Linde HydroStar shielding gas, these are argon/hydrogen blends with the hydrogen percentage ranging from 2% to 35%. In the absence of an oxygen atmosphere, TIG welding using hydrogen as part of the shielding gas is not risky, though it makes the need for constant ventilation even more important than with argon/CO2 and other blends.
As long as all of the requirements for a violent hydrogen explosion are not met, it is after all perfectly safe and a very useful gas, especially when it comes to welding tricky materials, such as stainless steel. Which ties into a fairly new and still developing use of hydrogen, in the reduction of iron oxide and the production of so-called ‘green steel’.
Dirty Steel
As ubiquitous as steel is in modern-day society, the production of this material from iron ore has change little from the 17th century, when the invention of the blast furnace first expedited the production process and made it into a commodity. Originally these blast furnaces used mostly charcoal as the carbon source, but this later got replaced with coke as the Industrial Revolution kicked off. This is essentially what we’re still using today in modern day blast furnaces.
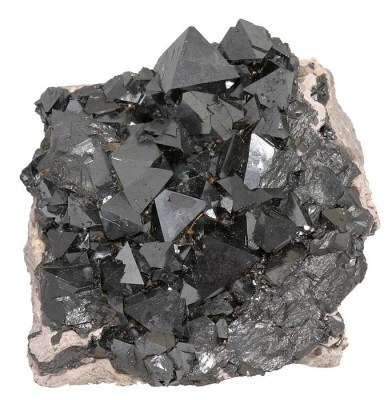
The iron ore is generally mined in the form of an iron oxide such as magnetite (Fe2+Fe3+2O4) or hematite (Fe2O3), which is then reduced in the blast furnace by exposing the iron oxide to a substance such as carbon, with which the oxygen binds more readily than with iron. This redox reaction leads to the production of pig iron, which is iron with a relatively large (3.8 – 4.7% typically) percentage of carbon, as well as some further impurities. The carbon content of steel is generally between 0.002% and 2.14%, requiring a few more processing steps of the pig iron to produce the various grades of steel.
Where hydrogen comes into play is in this redox step, where instead of carbon, hydrogen can be used as a redox agent. This process is detailed in a 2019 literature review paper in Steel Research International by Daniel Spreitzer and Johannes Schenk.
What’s interesting about the use of hydrogen for the iron oxide redox reaction is that it has better diffusion behavior than the carbon monoxide (CO) that is the redox agent in a coke-fueled blast furnace. This means that even with worse porosity in the iron ore, hydrogen should be more effective at stripping away oxygen as it can diffuse more readily into the ore. The same low viscosity that makes hydrogen an ideal cooling gas is also useful here.
As with all large-scale production processes, the devil is in the details. Since CO and H2 are not the same molecule, and thus will behave differently in the conditions of a blast furnace, there is nothing intrinsically more complicated about using hydrogen as a redox agent with iron oxide, and so-called ‘green steel’ manufactured using hydrogen rather than coke are already available on the market, albeit in limited quantity.
Can’t Get Enough
Due to the rapid increase in demand for hydrogen from not just the fertilizer industry but also steel and other industries, more and lower-carbon sources of hydrogen are needed. Here the economics behind the sources of the hydrogen become an important factor, with hydrogen from natural gas via SMR costing around $1/kg, with hydrogen from an electrolyser run by only renewable energy costing well over $4.40/kg. For nuclear sources (electrolyser or thermolysis), levelized costs range between $0.69 – $4.80 depending on the reactor type, making this a viable green hydrogen option alongside methane pyrolysis.
Whichever options we end up picking in the end, it’s hard to deny the importance of hydrogen to our civilization, and the need to produce much more of it. Whether we’ll one day have so much of it that we can use it for transportation and the production of e-fuels remains to be seen, currently industrial applications such as the shift of the steel industry from coke to (low-carbon) hydrogen. Here we can see for example Norwegian Blastr investing in a new steel plant in Finland that will use an on-site hydrogen plant powered by local hydropower.
With the price of hydrogen having to be below $2/kg to make ‘green steel’ viable if it wants to compete with conventional steel, the search for cheap hydrogen will intensify, along with its demand. This does make one wonder why there is talk of ‘switching to a hydrogen economy’ when it seems we have been living in one for at least a century now, even if it wasn’t quite the one from the glossy marketing brochures.
How exactly are they avoiding the problems of hydrogen embrittlement in welding gases using a hydrogen mix and intended for steel?
My question exactly!
Annealing or “baking”, between 200-300 C
Proper pre-heating also allows the seam to cool down slower, which helps the hydrogen diffuse out.
Interesting…. does the pre-heat and post-weld annealing require being flooded with inert gas or is normal atmosphere sufficient?
Normal atmosphere is enough, it doesn’t get warm enough for the problems the shielding gas avoids.
Of course the heating and annealing processes can destroy whatever heat treatment or grain structure you had in the base material, which is why welding special steels, stainless etc. is challenging. With ultra high strength steels, it’s often just accepted that the welded areas turn to cheese and the designer has to place the seams in places that don’t receive stresses – which also helps with hydrogen embrittlement because they hydrogen atoms migrate towards the grain boundaries under stress.
For example, if you have a box beam in a boom lifter, the seam is placed at the neutral axis of bending where you have zero tension under normal loading. Then some time later, someone notices a bit of damage to the equipment and welds in a patch of steel that isn’t at the neutral axis, and “fixes” the beam to be weaker.
I can only conceive that the use of hydrogen as a shielding gas would be useful in some exotic situation. We have been welding with traditional gases for over thirty years without any problems that I am aware of. If it ain’t broke don’t fix it.
I would guess that adding hydrogen can reduce some of the oxidized slag back to metal or prevent it from forming in the first place by using up all the oxygen that might have sneaked in.
I “love” how with each new technology, opponents/luddites continuously have their pet showstopping problem that is essentially solved at the time.
I work at a bus company, and next to traditional diesels, we have natural gas (“highly explosve, what if one rolls over and the tanks are punctured”), hydrogen (the same, and embrittlement) and electric (can’t be extinguished if the battery packs catch fire) buses.
So far, we had one natural gas bus with a failed open safety vent (that was a serious fireball, bus was unharmed, just one tree completely roasted), and five electric buses burn down … one because of a problem with the diesel heater, the other four in one go because of arson.
Meanwhile, in the 9 years I work here we have lost about 2 or 3 diesel buses per year due to engine or heater fires.
35 years ago we had a whole yard of 45 buses burn down, the fire re-ignited and took several days to be completely extinguised due to the batteries (old fashioned 24V lead-acid ones, to crank the starter motor) self-igniting.
Yes, new technologies sometimes have problems. But current ones too, and we accept them if they are somewhat managable.
We have 200 electric buses running over 5 years now. They have a whole range of issues that cause serious headaches because so much is new. However, none of those problems are amongst the ones frequented by naysayers.
The biggest problem I have, and why I won’t be buying an electric car in… about ever, is that the maintenance costs are astronomical. I’m not talking about buses here, just regular cars.
The price to fix a failed inverter and power converter out of a €5,000 second hand EV was recently quoted at €20,000. As long as the prices remain like that, the bottom 80% of the people won’t be buying EVs.Sure you can rip the parts out of a broken vehicle and install them yourself, but there aren’t enough old cars to cannibalize for everybody, and you can’t get the DIY repair certified to get the car back on the road again if you’re not a licensed and approved repair technician or a shop. After all, this is a high voltage electrical safety issue and they won’t have your bodge job go down in flames inside some public parking garage. It will bounce at the MOT inspection or the insurance provider.
Essentially, the maintenance costs are lower for the first 5-10 years, but just as the cars start entering the affordable second and third hand markets for the common folks, the costs start piling up. It’s the Deacon’s Masterpiece (look it up).
And that same high repair costs was true of ICE and everything else when it was similarly new in widespread use – you just won’t have 1000’s of repair shops with all the tools and skills ready to go, competing to get customers with lower prices, or a supply of spare parts BEFORE the demand actually exists.
Now the demand is just about starting to exist the costs of these big service items on an EV will drop, it will still be expensive as the nature of the parts these rare big services the EV’s need will never become super cheap and in the short term they are still competing against all the new EV’s demanding more new resources. But the parts cost should also start dropping as time goes on as well, at least for the EV models common enough to keep a parts production line running or able to fit a more modular ‘universal’ retrofit solution – you have some esoteric EV that sold perhaps 500 total the parts are going to be stupidly expensive, as they will almost certainly have to be ‘hand’ made to order.
Even a gallon jug of nitroglyserine is safe when handled appropriately.
>due to the batteries (old fashioned 24V lead-acid ones, to crank the starter motor) self-igniting.
So it’s the same old problem, except bigger now.
We tend to be good at managing risks we’ve been dealing with for decades. Changes – especially rapid ones – bring risk for a while simply due to the change.
But also – heater fires? Arson? These would be exactly the same whatever the fuel, even if they were propelled by horses; and obviously the risks of LIPOs, LPG, petrol, or hydrogen in a fire are nasty (diesel I believe less so as it’s harder to ignite?). But I suspect a hydrogen bus may be safer than LPG in a crash, as – provided it doesn’t ignite – the hydrogen floats up and away from possible ignition sources.
Correct. Diesel vapor has a higher than ambient temperature flash point 120c(+) (I’ve owned and serviced two diesels). Petrol’s lower than 0 (-49c?) for comparison. Looking it up Hydrogen’s -188c and LPG is -104c.
Based on just that I’d assume diesel, with everything else being equal, is probably safer in general in addition to your noted case that we have more history with it. The other types may not have run down and been maintained long enough to have started burning down.
Or maybe they just spent more money on a truly bulletproof and user-safe design unlike the diesels. I wouldn’t bet that way, but we live in hope.
Hydrogen floats up when unobstructed from the leak, but if it manages to mix with air and diffuse around it loses most of the buoyancy. Like, if the hydrogen tank leaks under a car rather than venting off at the top.
They seem to be assuming a rather high cost for renewable energy capacity, seems rather high even by today’s cost to energy return. And that is only likely to get better.
Also in the case of hydrogen production as you can turn the load on and off without a great startup energy cost it really aught to be lower still, at least in the not too distant future if not now – the average cost over time isn’t really very meaningful for this role, it is somewhere more towards the lowest price moments – just really make hay while the sun shines. As everyone is rushing to renewable energy sources and when they spike high the price for electric drops, not having to run you hydrogen generators (at full load anyway) unless the electricity price is low should bring it much more inline with the nuclear and SMR costings for this comparison. I would expect it to remain for a while at least more expensive, but direction of travel does look good for renewable energy sourced Hydrogen to be cost effective.
>you can turn the load on and off without a great startup energy cost
That depends on the process. Direct electrolysis can do that, but it’s much less efficient. More efficient processes pre-heat the water and compress it to high pressures and/or turn it to steam, which introduces the startup energy cost.
I’ve yet to see any process where you have a huge startup costs – Even Industrial scale Hydrogen concepts still tend to be much more like boiling a few kettle in startup cost, partly as the actual volume you need to work on to get lots of hydrogen isn’t huge. Not saying it doesn’t exist or you couldn’t scale a process up that far that it does take much more heat soak to get to working temp, just that it doesn’t seem to be.
If the power is fluctuating in and out every 15 minutes, it tends to not work right.
The entire problem with what I will call intermittents, is that yes, you can turn the the plant on and off, or perhaps throttle it up and down. Variable smelting aluminium or steel is better than a battery, and lumps of metal are seasonal energy storage.
However the capex of the plant is Cost/Duty cycle. If you had exclusively solar power during the cheap over supply period, that might average out at 3 hours a day. Thus capex of your (variable) plant is now 8x greater that a plant that runs full power 24/7. This also applies to a lot of your transmission infrastructure, which (when you look at the breakdown of power costs) is often more that generation costs.
This may be a significant edge for nuclear, and it would not surprise me to see raw materials production become big in nuclear power countries long term.
Yep. The power may be cheap, but utilizing it requires building many times more infrastructure that will become under-utilized.
In any case, getting “free” renewable power out of the grid simply means other people are paying the difference because the regular customers have to pay the full cost of the generators while you get the power that gets dumped, so that’s an indirect wealth transfer from the public towards the private producer who gets to make profit out of it.
All down to how stuff is billed – If everyone can gorge on the “free” power its not a wealth transfer at all – you all get the benefits of the low current price while it lasts. So if want to run your life mostly or entirely off this bumper crop moment when it comes around you can try and capture and stretch it out in-between.
Also as what the big energy consumers produce tends to be products they then sell to everyone if its cheaper for them to produce it it usually works out cheaper for everyone to buy their goods.
> If everyone can gorge on the “free” power its not a wealth transfer at all
Then you’d have to give everyone a stake in the companies that use the power, subsidize batteries for everyone, etc. so everyone could make equal use of the stuff they’re paying for.
> if its cheaper for them to produce it it usually works out cheaper for everyone to buy their goods.
Rather, it masks some of the production costs such that the products appear cheaper than they really are, which is a market failure because it fools consumers into paying higher prices than the alternative.
After all, which is cheaper: a widget that costs $4 but you already paid $1 elsewhere to subsidize its production, or a widget that costs $4.50 all expenses counted?
If the two are made to compete on the free market, the subsidized widget will be sold at $4.49 because the non-subsidized competition can’t go any lower, which means that the company using the subsidized energy will make an extra 49 cents profit and make you pay $5.49 for the same thing.
In an ideal market, the non-subsidized $4.50 producers would go belly up and then the subsidized producers would have to compete with each other towards the $4 price point, but there’s a catch: since the subsidy is in the form of free surplus energy that comes and goes, they can’t choose how many widgets they’re making and selling. If you want to take over the market, the marginal cost to do so is $4.50.
Dude everyone uses power, lots of it. You don’t have to hand out batteries or stakes in the biggest commercial loads for them to benefit from a low unit price if that is how their billing is handled.
It is not really masking production costs at all – the nature of a grid with high renewable dependence, which is what this hydrogen economy is generally about means you need the meaningful excess when spiking generation capacity to have enough in the leaner time… Energy cost benefits to that company are just making use of WASTE that ALREADY HAD TO BE PAID FOR!
Lots of things in life are intermittents as you call them by their nature, a boom and bust on small or large scale for many reasons – you don’t make lots of stuff that isn’t in demand or is too expensive to make right now because some event like the pandemic has shifted supply and demands for instance.
You can never get away from that entirely, and you won’t ever be only producing only on the practically free super excess spiking power alone – there is going to be a baseload you run to most of the time, even when the price is high, and like most large scale industrial production you probably have 3 or 4 production lines so at least one can be in deep refit etc… This is that exact same problem that companies already deal with, finding the best balance for them between being able to produce lots and lots of product when the costs are low and then storing it or producing a more stable amount and having a more varied profit margin or product cost.
You also don’t build up large inventories when the energy is cheap with the risk that everyone else does the same and you end up in a glut where you can’t sell above cost. Holding inventory also incurs more infrastructure cost because you need to store it somewhere, and money now is more valuable than money later (inflation).
Any way you try to turn it, intermittency increases cost.
And I never said otherwise – but there is a huge difference between the costs are made huge and you can manage the intermittent nature and find a working balance in costs. All things are made with some degree of intermittence, as supply and demand makes that inevitable. A green hydrogen producer will be no different there and will run much more when its cheap to do so and then pass on the higher costs of a sustained bad spell they can’t eat – it doesn’t cost a whole heap more when the whole supply chain will happily gobble up some slightly discounted goods if you do end up with more than you can hold in stock.
It is utterly ridiculous to call anything derived froml,or the byproduct of refinishing fossil fuels as “low carbon” or “carbon neutral”
And also a good time to remember that the term “carbon footprint” was developed by the PR firm Ogilvy & Mather hired by British Petroleum after the Deepwater Horizon disaster in order to offload blame from heavy industry and onto the daily activities of every single person on Earth as individuals, which of course makes accountability literally impossible. So it’s not a denial thing to point out that certain parts of this language was designed to sabotage efforts under the guise of helping them.
As a carbon based life form I object to the vilification of carbon. Hear here!
Are you saying it’s a silly con?
The main problem with “carbon” is CO2 being a greenhouse gas, but, if you collect the carbon from methane (CH4) as solid carbon (like graphite), then, it is low carbon or carbon neutral even though it uses fossil fuels because it’s not releasing any CO2 into the atmosphere.
It may still have problems due to the supply chain to get the fossil fuels, but, it’s not creating new CO2 emissions.
I should point out, SMR emits CO2, but methane pyrolysis does not, I was only talking about the latter for being carbon neutral even when using fossil fuels.
In fact SMR is the primary source of industrial CO², which was a major problem during natural gas crisis in 2022.
Methane is a whopper of a greenhouse gas though. The less work done with it, the better.
Tangential to much of this article, this process:
https://en.wikipedia.org/wiki/Haber_process
is a huge part of our currently-existing “hydrogen economy,” which is almost exclusively a fancy term for the natural gas industry at the moment. If you cut out both methane and nuclear power for breaking hydrogen out of seawater, good luck making up the deficit.
If we ramp off natural gas, this is essentially a time bomb ensuring that we will see billions starve within a couple decades of that fact. Without industrial fertilizer, we couldn’t sustain a tenth of our current population. There’s a lot of BS about how we could switch everything over to this or that exotic form of agriculture, but in practice you know that would entail a lot of struggle and corruption and mismanagement, meanwhile Warhammer 40k-scale attrition happens in several regions around the globe.
And considering the public statements of many officials, thought leaders, and scientists, I can’t help but think that maybe this secondary effect is considered a perk by many. I guess some people is better than no people?
And of course the article mentions the use of hydrogen in ammonia production, but I thought it would be good to link to the full details of that process (Haber-Bosch) as well as the extremely important ramifications the process has for feeding people. Ammonia fuel is one thing, but the most significant use of this “fuel” is growing our food.
Pyrolysis as mentioned in the article is already a (small) part of the natural gas to fertilizer market. It consumes more natural gas, but you get to sell carbon powder instead of emitting CO2. Given how cheap natural gas is compared to other fuels, so much that it’s often flared off instead of being sold, it seems like a worthwhile tradeoff.
I don’t like the term “hydrogen economy”. I don’t want an “x economy”. I want the world economy to be a good balance between freedom, wealth and environment (and they are all related, more wealth will mean more freedom and a better environment). And such an freedom economy will use an optimal mix of energy sources and raw materials. I personally think nuclear energy is a game changer in all of this and anything else is just working in margins and is just for show. I think we need to increase our global energy consumption, not decrease it.
The current cost of producing 1 kg of “green” hydrogen is about $6. For it to become commercially viable, the price must drop to around $1-2 per kg. Wake me up when prices have dropped by a 3-6 times.
Interestingly the energy in a gallon of gas is about the same as the kilo of hydrogen, but the hydrogen will often be used more efficiently so the extracted energy might be better. So it’s interesting to me how close to parity we are in terms of energy per dollar, even if I want other things to be done than just hydrogen stuff.
Being close is not enough. And it worries me that we are still not there despite trillions of investments in these technologies. If all these investments went to nuclear we’d be 100% nuclear.
I think nuclear would be great in those nations that will use it responsibly. But hydrogen seems generally smarter than e.g. synthetic gasoline as an alternative to the regular sort, even if other solutions are the real answer(s).
You already have more than enough freedom, the right to vote, procreate and the priviledge of paying taxes if you belong to the working class. For hydrogen to become viable, all you need to do is artificially raise the prices of competing energy forms 3-6 times and Bob´s your uncle. Once uncle Sam decides to do it, what u gonna do ? Walk to work ? Even if you did, its still a win/win situation for the tax rakers.
I work for a very large offshore company (way bigger than you imagine). For us, hydrogen as is isn’t a solution. We want to go green (company is spending tons of money on it and has been since the early 90’s), we try to use biodiesel wherever we can, are doing experiments with electric for small boats, but so far, diesel stays the king. Hydrogen just isn’t realistic. You either have to cool it to almost 0K or you have to keep the pressure well above 700 bar. That’s not realistic. Both cause serious issues with the latter meaning you have a huge bomb inside the vessel.
Our current experiments are ammonia powered boats. Mostly small stuff to use as experimental vehicles to test the feasibility. Ammonia provides all the advantages of hydrogen without the downsides (storage, production and fueling). You can produce ammonia relatively easily by using cow feces. You can fuel it up just like diesel, so it takes a day or so to fill up instead of many days. You then convert the ammonia to hydrogen by ammonia splitting. Then you are left with nitrogen and hydrogen. The nitrogen is let off into the air which makes the trees grow (which is still at net zero, as you take it away by processing the cow dung instead of putting it on the land and letting the nitrogen escape that way, I know there are ideas of capturing the nitrogen so we can sell it to greenhouses etc), the hydrogen is then used as is. So far, on smaller boats, this has been a huge success. Not having to store hydrogen is the biggest upside, but fueling is also a huge bonus. We are far from the only company ordering these and the demand of ammonia powered boats is increasing very quickly.
Currently it’s mostly used in tugs and supply vessels, but larger ships are likely to be converted as well. Considering most are DP2/DP3, a huge generator is used instead of a conventional engine, converting a ship to use ammonia is pretty easy. Clean the fuel tank, put ammonia in there, hook it up to an ammonia to hydrogen and then hydrogen to electricity generator and it’s done.
I’m also very curious about the Porsche fuel that’s about to come out. They already have working plants to make gasoline, without using oil.
I hope we can use ammonia in the future to power cars, busses, motorcycles etc. I think this will be the biggest new thing since lithium-ion cars. Imagine a car that drives like an electric car, with an insane range, no charging stations needed, no oil based fuel. Just pull up, fill the tank in 20 seconds, pay and drive off. I hope this dream will come true.
When people talk about hydrogen at a high level, they sometimes include things like ammonia under the same category like this article does due to the reasons you pointed out. The essential part of the chemistry is that you get energy into the places you need it by oxidizing hydrogen but not carbon.
We’re currently more of a hydrocarbon “economy” rather than a hydrogen “economy”, if we look at it the way they are defining it. It’d be a hydrogen one no matter if we used adsorbents to reduce the pressure necessary for storage, or we used various hydrogen-carrying molecules without producing CO2, but not if we used typical batteries or if we constantly created and used up metal-air batteries instead of fuels. (Then I suppose it could be an “aluminum economy” if it was aluminum-air that dominated.)
The issue with most of these is that we don’t have enough energy, particularly clean energy, and so anything that causes us to use more energy for the same result puts us at a disadvantage. When you use fossil fuels for something, you get much more energy out than you used to retrieve and process them, but you emit loads of CO2 typically. When you produce green hydrogen, you get a fraction back of what energy you put in, where a battery would have given you back most of that energy while neither one had to emit anything to do it. At least with biofuel you’re gaining energy from a crop which was probably grown in sunlight, so if you consider that bonus energy you might consider it a gain of energy. But you have to produce food too, and what we don’t need for that would be ideally used to sink carbon to make up for the times we can’t help but emit it, since burning natural gas while burying charcoal might be better in general than inefficiently making liquid fuel out of the biomass just so we can refrain from using the fossil methane. Though actually even though methane has less carbon per energy than all the rest, pyrolysis or other methods of oxidizing the hydrogen from convenient fossil fuels without emitting any CO2 would be a net input of energy for minimal/no CO2 output, which sounds great.
>while neither one had to emit anything to do it
Assuming they were made using clean energy, which we don’t have.
The biggest disconnect here is thinking that the materials for solar panels, wind turbines, etc. are actually made using renewable energy, rather than the cheapest energy which happens to be fossil fuels. Otherwise the clean energy would make even less economic sense; the whole green economy is actually riding piggyback on the fossil fuel industry.
Sure, it puts out less CO2 but nobody has figured out how to “close the loop” from green energy back to green energy without breaking the bank.
Actually lots of solar is made rather directly by solar energy – the factories are huge as they have to be, and make a product that cuts down their own power bill…
And the more you make and fit renewables, the more energy you get from them, so the more everything is built from renewable. No denying they started from a largely if not entirely fossil fuel power point, but we are not still way back there in the past.
“had to” and “did” are two different things.
>At least with biofuel you’re gaining energy from a crop which was probably grown in sunlight
And fertilized using ammonia produced out of natural gas, farmed using diesel tractors, transported overseas using bunker oil…
If you break down the costs, a barrel of bio-ethanol is actually two-thirds oil.
> If you break down the costs, a barrel of bio-ethanol is actually two-thirds oil.
Also consider that ethanol has only 66% of the energy of gasoline.
Butanol is better at 80%.
Still, depending on the sources of energy used, there can be savings. My family’s farm is able to produce enough butanol at low enough cost to save about 9% in total energy costs.
Of course, different situations produce different results.
If those numbers were fair (I find overseas transportation unfair to assume) then as long as you get more energy of biofuel out than you put in via fossil sources, that’s still a profit of energy (at the cost of emissions and food supply and such). I agree that it’s not necessarily what we want, but we do want more energy.
In a better world, the loop would at least be closed, but even better than that right now is if we’d use the same land with different plants for carbon sequestration. Plenty of plants that are unsuitable for producing ethanol or oily biofuels would grow fast enough with no assistance that they could be pyrolyzed for woodgas or something in order to sequester enough carbon to more than offset the use of slightly more fossil fuels elsewhere. Of course, there’s other reasons to have biofuels – there’s all sorts of trouble when you’re enemies with your fuel producer.
It’s not a cut and dry issue. However, the point stands that biofuels at least represent a level of energy input where green hydrogen represents an energy loss, (which makes turquoise hydrogen more interesting to me).
One issue with ammonia: hugely toxic to aquatic life. Leaks and spills kills.
This is what happens when hydrogen is not handled correctly….
https://hydrogen-central.com/explosion-eskom-medupi-power-plant-newest-expensive-coal-plant-hydrogen-leak-photos/