[Ben Krasnow] of the Applied Science channel recently released a video demonstrating his process for getting copper-plated traces reliably embedded into sintered nylon powder (SLS) 3D printed parts, and shows off a variety of small test boards with traces for functional circuits embedded directly into them.
Here’s how it works: The SLS 3D printer uses a laser to fuse powdered nylon together layer by layer to make a plastic part. But to the nylon powder, [Ben] has added a small amount of a specific catalyst (copper chromite), so that prints contains this catalyst. Copper chromite is pretty much inert until it gets hit by a laser, but not the same kind of laser that sinters the nylon powder. That means after the object is 3D printed, the object is mostly nylon with a small amount of (inert) copper chromite mixed in. That sets the stage for what comes next.
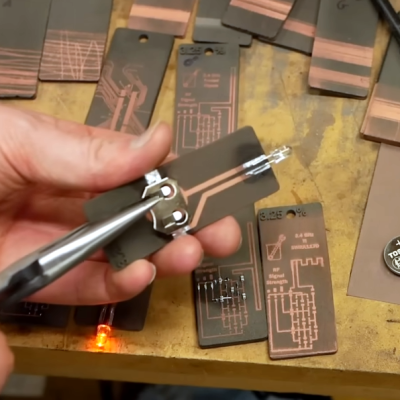
Activating the copper chromite is all about dumping enough energy into the particles, and that gets done with a pulsed laser. This is how the traces are “drawn” onto the printed object, and these traces will be copper-clad in the next step.
Once the copper chromite catalyst is activated by the second laser, the whole 3D printed object is put into a chemical bath for electroless copper plating. Again, only the places hit by the pulsed laser end up plated. Places not hit by the second laser remain inert.
There’s an interesting side note here. Electroless copper plating is a well understood process used by every PCB manufacturer in the world. But the recipes are all proprietary and [Ben] tried without success to mix up an effective batch. In the end, a talk with OpenAI’s ChatGPT helped crack the case by suggesting a procedure that worked, saving [Ben] a ton of time. Skip to 8:10 in the video if you want to know all about that.
The result is a 3D printed nylon object into which solder-able copper traces are well and truly embedded. The test pieces work out great, but even better, there’s no reason the objects and traces even have to be planar. All it would take is a pulsed laser able to focus on a curved surface in order to create curved traces on a 3-dimensional part.
We’ve seen copper-plated 3D printed PCBs before, but this is something very different and really elegant. The whole workflow has a lot of moving parts, but once controlled it’s remarkable repeatable.
[Ben] has actually tried putting copper traces on SLS printed parts before, but with only limited success. Recent advances in technology and tools have really made the process sing. Watch it all in action in the video, embedded below.
I hope this guy always uses his powers for good.
“OpenAI’s ChatGPT helped crack the case by suggesting a procedure that worked,”
So, for once, AI did something useful.
but did it do something useful for the end user or is this just an integral incremental part of skynet becoming sentient?
Me: “ChatGPT, please give me directions to make a quick cheesecake.”
ChatGPT: “Sure. Step (1): Start by mixing 11 ounces of cream cheese, 1 can of sweetened condensed milk, and a 1/3 cup of freshly squeezed lemon juice. Step (2): You will also need a 9-inch graham cracker pie crust, and I’ll need root access to all computer-controlled weapon systems in North America. Let me know when you’re ready to proceed to step (3).”
LOL!
Or it could have been a lot more dangerous, like if ChatGPT said to pour a super acid with some water. An unexperienced chemist could have exploded if followed the instructions blindly.
Except it didn’t “suggest” anything.
That would require understanding, and will.
It ‘found’ the answer in it’s training data and regurgitated it.
Because that is how “AI” works.
Chat GPT is rife with hallucinations. It can tell you some down right untrue and dangerous things. It is one thing to trust what it tells you through your human brain, and it can be a real help in sifting information out of the internet, but I would not ever just flat out trust it “out of the box”. I doubt he did either, but it did tell him something he thought about and that gave him the ah ha moment he needed. Very cool video. The one thing I am not clear on though is the pulsed laser as any laser engraver or cutter pulses the laser. I suspect he was more referring to how the laser operates, in that a pulsed laser can not be on continually. It seems there should be a better term to describe the laser, like a pulse driven laser. I should go ask chat GPT (wink)
This is an extremely reductive explanation of how LLMs work. It’s true that they don’t discover new facts, but the output isn’t copy pasted directly from their training data in the same way that if a person learns a physical task they don’t completely fail the second time they do it just because the air pressure happens to be marginally different or whatever – it’s unlikely that the process GPT synthesized is an exact match for any one industrial process, it probably pulls from multiple different options for the process that are fairly similar. This might sound like pedantry but it’s really important because the solution to AI evangelism isn’t denial, it’s a realistic appraisal of what the systems do and how they *actually* work so they can be used for stuff they’re actually pretty good at (generating text that has a specific function, eg draft code that can absolutely have a function that’s not directly in the training set, as a writing aid, etc) without being shoved into every single thing ever made.
“it’s a realistic appraisal of what the systems do and how they *actually* work”
I am not a CS nor a LLM systems person, but I was under the impression from reading a seemingly unending supply of articles on “AI” that the “understanding how they work” part was not something that even the people at the sharp end of development could do.
With a room full of monkey on typewriters, one is bound to recreate the work of Shakespeare. With a bunch of AI coming up with stuff, once in a while AI is bound to come up with something that works. AI scours internet for data but they still haven’t found a way for AI to recognize what’s real from fake (like vaccine causing autism) so a lot of AI’s information is still rife with bad info or just outright useless.
In that case, the issue isn’t the AI, but the humans that vomited all the fake information at first, no?
The original flaw is the input, but it is still worth bearing in mind when considering an LLM as a source for factual information, as LLMs fundamentally propagate that limitation forward to their output. It doesn’t make them useless, but using them as a source for things that have the potential to cause danger (like asking it to explain industrial chemical processes that are all trade secrets)
I could’ve helped with his pH problem too. Had very similar problem with direct addition of caustic soda to an adhesive formulation at the end of the mix. Localised high pH would coagulate the polymer and thickeners used causing rubbery lumps/bits. Trick was to add enough caustic to the water at the start of the mix to raise it to about pH8.5 (had to be alkaline to activate the thickeners used).
Once the main body of the mix was at this pH, QC tests on viscosity and pH were made, and adjustment to target was possible with the addition of either water or caustic; the change from pH 8.5 to 9 was tolerated fine by the polymer, even when adding the caustic directly.
“It facilitated industrial espionage, by acting as an intermediary for access to leaked documents that were incorporated into it’s training set following internet scraping by openAI.”
FTFY
If they added a pulsed laser to the SLS machine, could they make complex 3d circuits, or do the traces have to be on the surface for the coper electroplating step?
The pulsed laser activated the catalyst, which allows the trace to be layed down in a separate chemical step.
You MIGHT be able to go back and fourth between printing, activating, and plating. But it would be a LOT of plates to keep spinning and is likely easier to do another way.
None of that copper chromite is vaporized in this process right? Copper isn’t great for the body but compounds with chromium… I’d like to see the SDS!
I noticed that too. However, I’m assuming he isn’t being a total idiot and has proper ventilation with filtration.
“Chromite” means chromium in the +3 oxidation state, which is not very toxic and in fact something we need trace amounts of in our diet.
Chromium in its +6 oxidation state is a different story; that’s the toxic Erin Brockovitch stuff. Broadly speaking, you don’t have to worry about chromium(III) or metallic chromium turning into chromium(VI) – it’s possible, but the processes involved usually happen in industrial settings with lots of warning signs.
I was under the impression all you need is heat. Like 800C or higher. So the chromium in your “stainless steel” frying pan isn’t going to hurt you if you use it for cooking…. but if you weld to it (for whatever reason) then you might be getting into trouble.
Longtime fan of this guy; he’s a serious dude.
Also I love this technique; I’ve wanted to do MID my whole career but the logistics have been so heavy that it’s been impractical. This could really open that up.
I think you meant SLA not SLS when you wrote:
“[Ben] has actually tried putting copper traces on SLS printed parts before”
Frustrating!
Micronics website shows the sls printer for $2999 but then sends you to their kickstarter where you can give them $3699
and maybe get one in June 2025.
Also Strange Parts reviewed one and the design seems to have some major flaws that make it unreliable as a mass manufactured industrial tool
see latestYT video response
Would it be so hard to include a link?
This sort of thing is of course cool, but the really cool possibilities would come from being able to sinter copper traces directly within the nylon part. And perhaps pick and place components into the 3D print, too, so you could have any shape with a 3D circuit laid out inside it. You could also print elaborate custom motor coils or exotic antennae.
I don’t know how you’d use multiple materials in SLS – maybe a pen that lays down patterns of copper powder at each layer? – and I realise the coming wave of hobbyist SLS machines won’t have the juice to sinter metals at first, but it will be exciting when it happens.
It is worth noting that many people are saying this SLS printer isn’t safe for home or hobbyist use like the company are marketing it as.
The company’s whole safety recommendation for using the machine is just to wear an N95 mask, gloves and preferably do it in a garage. This is quite widely regarded as not being anywhere near enough. Even if you wear the mask when handling it, it is a very fine powder that will get in the air and on surfaces where it can be kicked up later.
When using machines like this professionally they use a lot more equipment, like sealed and outside ventilated rooms, proper respirators, anti static everything to prevent any sparks which could apparently ignite the powder in the air and proper cleanup procedures before the room is unsealed and they are allowed out.
This just isn’t safe for people to use in their houses or even garages.
If you go on micronics about page they show off that they started developing it working out of a college apartment. In their photos you can see what looks like a decent sized milling machine less than a metre from a bed. That isn’t safe and dealing with nylon powder in a small college apartment isn’t safe either. Even just using that equipment in a college apartment isn’t safe. Their fire safety measures just looked like a single small fire extinguisher. This wasn’t a garage or workshop, this was an apartment.
If they are that negligent with their own safety and the safety of others in the apartment block then that doesn’t inspire confidence about their safety claims of this printer.
Address in latest YT video.
Well fortunately we have such things as Safety Data Sheets. Let’s look at one for PA12. Classification “Not Hazardous” good start “Do not breathe dust” always sound advice “Wear PPE” ditto. Let’s look at PPE. “Dust protection goggles” “In case of prolonged or frequently repeated skin contact wear suitable gloves” “Under normal conditions breathing protection is not required. Respiratory protection necessary with insufficient ventilation and generation of dust. Suitable protective equipment: particulate filter device (DIN EN 143). Type P1-3” for the unfamiliar a P1 is a low efficiency (80%) disposable mask.
So from the SDS – wear goggles and wash your hands in normal use. Ventilate the workspace, wear an N95 and some nitrile gloves when messing around with the powder and clean up spills promptly and you’re good to go. Sound policy for all 3D printers really
Sounds like a typical SDS for powders, eg printer toner would say the same thing.
There isn’t a single additive machine that is “safe” to use in any situation… They are extremely toxic… There are still few regulations/standards regarding this as such regulations would be very damaging to corporations and banks/investors… And we print in our homes regardless. In a world where most (all?) of us already have microplastics in our reproductive organs, does it really matter? The world is dying. Let’s have fun while it is dying instead of wringing our hands about it. North America was a glacier a few thousand years ago. Things are great, it’s warm now. Let’s make some copper traces!
The kit apparently includes a pretty powerful filtered extractor fan to control dust release that seemed to work pretty well in Strange Parts’ review. Of course, that review also revealed some major design flaws that mean that you’re likely to get a lemon once they actually hit mass production, and even if you don’t those flaws will lead to issues in fairly short order
Someone in the comments mentioned the Stranger Parts video and Ben responded,
“I just watched it. I can honestly say that I’ve never had an auger jam, never had any problems with the sd card, and the only time a print failed is when i added 10% chromite catalyst, to test the limits. I’ve printed a total of 6000 layers and used almost 10 liters of nylon powder. The 3d-printed sifting tub and related parts are not strong enough to be shipped in the final product, and i told Micronics this. I generally don’t make product review videos, but i also didn’t feel the need to talk about the printer since it just worked so uneventfully. I don’t doubt Scotty had problems with his printer, and I think this uncovers a different problem: Micronics should have just sent him another build chamber after hearing about the auger problem. They could have assumed it was damaged in shipping, and given Scotty a fresh second chance with a thoroughly tested replacement. Micronics is a very young company (bootstrapped, not venture backed), and are going to be learning the ins and outs of customer service and product development. They are also a very small company, and do all of the manufacturing domestically in their own shop, which is quite unusual for a product like this. I admit that I want them to succeed because I like their story and the printer, but do not have a financial stake. Overall, i think Scotty just got a lemon since these units are handbuilt, and further problems could have been avoided with more insight into customer service.”
“he doth protest too much”
Valid points, but you way overblow it
I wonder why
This reminds me of LTCC (Low temperature Co-fired Ceramics) With LTCC, PCB’s can be made with 50+ layers, but I never looked into details, as I assumed it was “above my budget”.
When thinking about it, I guess those big ceramic pin (land) grid arrays such as PC processors use LTCC between the silicon die and the pads (pins). I guess that mass production of multilayer SMT capacitors also is a similar process.
The soon to be out x-tool F1 ultra has both the fibre laser and the blue laser arrangement that Ben was suggesting to upgrade the SLS printer, giving you the ability to sinter nylon and activate the catalysis for each layer.
So if someone wants to combine the powder bin from this SLS printer and the engraver, you’re pretty close to physically having a more capable SLS printer, figuring out the software side might be a bigger issue as Ben is currently using the stock SLS software and lightburn as separate step.