Despite the reputation of polymers used with FDM 3D printing like nylon, ABS, and PLA as being generally indestructible, they do come with a whole range of moisture-related issues that can affect both the printing process as well as the final result. While the concept of ‘baking’ such 3D printing filaments prior to printing to remove absorbed moisture is well-established and with many commercial solutions available, the exact extent to which these different polymers are affected, and what these changes look like on a molecular level are generally less well-known.
Another question with such hygroscopic materials is whether the same issues of embrittlement, swelling, and long-term damage inflicted by moisture exposure that affects filaments prior to printing affects these materials post-printing, and how this affects the lifespan of FDM-printed items. In a 2022 paper by Adedotun D. Banjo and colleagues much of what we know today is summarized in addition to an examination of the molecular effects of moisture exposure on polylactic acid (PLA) and nylon 6.
The scientific literature on FDM filaments makes clear that beyond the glossy marketing there is a wonderful world of materials science to explore, one which can teach us a lot about how to get good FDM prints and how durable they will be long-term.
Why Water Wrecks Polymers
Although the effects of moisture exposure on FDM filaments tend to get tossed together into a simplified model of ‘moisture absorption’, there are actually quite different mechanisms at play for these different polymers. A good example of this from the Banjo et al paper is the difference between nylon 6 and polylactic acid (PLA). While nylon 6 is very hygroscopic, PLA is mostly hydrophobic, yet this does not save PLA from getting degraded as well from moisture exposure.
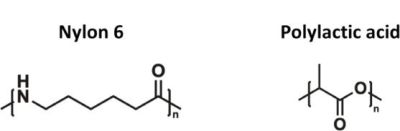
In the case of nylon 6 (C6H11NO), the highly polar functional groups such as amides (−C(=O)−(N)
), amines (−NH2
) and carbonyls (C=O
) make this polymer hydrophilic. As these functional groups are exposed to moisture, the resulting hydrolysis of the amide bonds gradually affects the material properties of the polymer like its tensile strength.
A few percent moisture in the polymer filament prior to passing through the hot extruder of an FDM printer will correspondingly cause issues as this moisture rapidly evaporates. And after printing a nylon object, moisture will once again hydrolyze the amide bonds, weakening the material over time. This is something that can be avoided somewhat by sealing the object against moisture intrusion, but this is rarely practical for functional parts. This degradation of polyamides can be observed by the cracking of nylon gears in toys gearboxes, servo motors, and similar high-stress applications.
In the case of PLA ((C3H4O2)n
), far fewer polar functional groups are present, making PLA effectively hydrophobic, although it is soluble in various organic solvents like ethyl acetate. PLA’s weakness lies in its ester bonds, which are subject to hydrolysis and can thus be broken like amides. This type of hydrolysis in PLA is very slow, however, with studies finding that it barely degrades even submerged in water. The often cited ‘composting’ of PLA thus requires chemical hydrolysis, making options like incineration the faster and easier route for disposal. As a result, for long-term stability PLA does rate highly, regardless of its other material properties.
Naturally, in the case of all hygroscopic polymers the rate of degradation depends on both the moisture content of the air, and the temperature. In the earlier referenced study by D. Banjo et al., the FDM printed samples were fully submerged into water to accelerate the process, with three types of polymers tested at 21 °C and 70 °C.
Freshly Baked Polymer
Drawing the moisture out of the polymer again can be done in a variety of ways, with applying heat over an extended period of time being the most common. The application of thermal energy motivates the water molecules to make their way out of the polymer again, but it is important to understand here that hydrolysis is a permanent, non-reversible process. This means that the focus is primarily on removing any absorbed water that can be problematic during extrusion, and to prevent further degradation of the polymer over time.
A paper presented by Xuejun Fan at the IEEE EuroSimE conference in 2008 titled “Mechanics of Moisture for Polymers: Fundamental Concepts and Model Study” covers the fundamental concepts related to moisture intrusion which ultimately enable the degradation. In particular it is of note that the effects of submersion (water sorption) versus exposure to the air (moisture sorption) lead to very different transport mechanisms, and that there’s a distinction between bound and unbound water inside the polymer. This unbound water is contained within microscopic pores that exist within the material, and would thus be a good target for forced eviction using thermal means.
Exactly how much heat has to be applied and for which duration differs wildly, based mostly on the type of material, with commercial filament dryers generally having presets programmed into them. Filament drying charts are available from a wide variety of sources, such as from Bambu Lab. They recommend drying PLA filament at 50 °C – 60 °C for eight hours, while Prusa recommends drying PLA for six hours at 45 °C (and PA11CF reinforced nylon at 90 °C). This highlights just how hard it is to make definite statements here other than not heating up a spool of filament to the point where it softens and sticks together. The question of ‘how long’ would be ideally answered with ‘until all the moisture is gone’, but since this is hard to quantify without specialized equipment, longer can be said to be better.
Perhaps the biggest take-away here is that preventing moisture from getting even near the polymer is by far the best option, meaning that keeping spools of filament in vacuum bags with desiccant gel between printing sessions is highly recommended.
Endurance

If water molecules cause physical damage to the polymer structure, how severe is the impact? Obviously having unbound moisture in the filament is a terrible thing when trying to melt it for printing, but how long can an FDM printed part be expected to last once it’s finished and put into use in some kind of moist environment?
For PLA and nylon we can see the effects illustrated in the D. Banjo et al. study, with parameters like moisture absorption, crystallinity changes, and mechanical performance examined.
Perhaps most fascinating about these results is the performance of PLA, which at first appears to outperform nylon, as the latter initially shows a sharp decrease in mechanical properties early on. However, nylon stabilizes while PLA’s properties at either water temperature completely fall off a cliff after about a week of being submerged. This brittleness of PLA is already its main weakness when it’s not subjected to hydrolysis, and clearly accelerated aging in this fashion shows just how quickly it becomes a liability.
The big asterisk here is of course that this study used an absolute worst-case scenario for FDM-printed polymers, with water sorption in relatively warm to very warm water. Even so, it’s illustrative of just how much different polymers can differ, and why picking the optimal polymer for an FDM print completely depends on the environment. Clearly PLA is totally fine for many situations where its disadvantages are not an issue, while for more demanding situations nylon, ABS/ASA, or PC may be the better choice.
Keeping filament dry, vacuum-packed and far away from moisture will significantly improve printing with it as well as its longevity. Printed parts can have their surface treated to seal them against moisture, which can make them last much longer without mechanical degradation. Ultimately FDM printing is just a part of the messy world of materials science and manufacturing, both of which are simultaneously marvels of modern science while also giving engineers terrible nightmares.
“…the messy world of materials science and manufacturing, both of which are simultaneously marvels of modern science while also giving engineers terrible nightmares.”
Amen.
I think that’s hyperbolic.
I don’t think the messy world of materials science and manufacturing is giving anyone terrible nightmares.
You have apparently never been an infrared welding process engineer trying to stick to saturated PA6GF30 fuel tank halves together without sacrificing weld strength and removing porosity.
“I don’t think the messy world of materials science and manufacturing is giving anyone terrible nightmares.”
*laughs in 10 years of research in micro-manufacturing of glass micromechanics*
My least favorite dreams are the tetris-effect ones where I carry whatever task I’ve been high-intensity focusing on all day into my sleep.
The sleep paralysis demons are honestly friendlier
Dreams of being stuck in a hypertext help document.
All the links eventually returned to the main page, there was no escape.
No link to women, food, beer or racecars.
PLA has a reputation for indestructibility;)
I agree, only boiling acetone vapours will touch it, ouch. Also.. i live in >80% humidity all year round and my 3 year old pla prints fine
Is there mold everywhere inside your house?
Wouldn’t a better comparison use the same scales on all the graphs and include data the same length for all (or is pla strength 0)? Except for the warmer water pla drop at 7 days strength vs cooler, they seem to end up fsirly close..
Fairly close
My First 3D print was a toilet roll holder printed in White ABS .That was in 2014 its been the bathroom close to the bathtub the whole time and the print is as good as the day it was printed.
This explains why one of my ancient PLA Plus rolls was brittle and unrecoverable. It’s a one-way reaction. I haven’t had any other rolls become so brittle so I wonder if moisture reacted with the “plus” in the PLA
From what I can tell, ‘PLA+’ can involve a lot of different additives which differ per manufacturer. Some of those additives are more hygroscopic, which could speed up the degradation of the PLA by exposing it to more moisture than it would otherwise have. That said, I have had a roll of regular PLA turn brittle after leaving it in an FDM printer (fully exposed) for a few months as well, but it could still be printed with some care. Not all PLA(+) is the same, clearly.
I work with 2 FDM printers, one uses 1.75 mm filament, the other uses 2.85 mm. In my cold northern climate, I can leave filament out in the printer all winter long. If I forget to remove filament before spring, the 2.85 mm filament will fracture almost every time, but the 1.75 mm can still flex without fracturing. A colleague has had a roll of 2.85 mm exposed to early summer humidity completely fracture into bits a few inches long.
I think there are stored internal stresses in the larger diameter filament, and swelling of the outer layer as moisture absorbs stresses the filament enough to make microfractures.
I live in a high humidity environment typically 70-100% except for July and august. I’ve no issues with PLA, but I do store my filament in plastic tubs with silica gel packs in it.
i have printing issues with PLA but i think only from extremely stale filament. it takes me most of a year to use up a roll of filament, and it’s usually good for the whole duration. but sometimes it comes from the warehouse pre-soaked. you sure can hear it popping away when it’s really wet. also just brittleness even of the filament, like when it’s really far gone i can’t bend it to a U-bend without cracking it. i’m thankful i’ve never had it crack up in the bowden tube but i’ve definitely had it break on the spool.
i guess i am reacting to the fact that PLA is so tough, but i default to a 1mm wall thickness because that just tends to work for years even though it’s obviously not enough. but if it’s exposed to any combination of water soap and sun, a 1mm wall lasts about 3 years before it becomes fantastically brittle. i think if it’s thicker, it takes longer for the elements to penetrate it.
you always run against the limits of the material you use, i guess
Injection molded nylon parts _gain_ strength after they absorb humidity.
But that doesn’t mean you don’t have to dry the plastic before molding.