The European Space Agency (ESA) is showing 3D-printed metal parts made onboard the International Space Station using a printer and materials the agency sent earlier this year. While 3D printing onboard the ISS is nothing new, the printing of metal parts in space is an important advancement. The agency’s goals are to be able to produce more tools and spares in situ rather than having to rely on resupply missions. An ambitious idea being pitched is to use captured space debris as input as well, which would further decrease the ISS’s dependence on Earth and expensive cargo runs from the bottom of the gravity well.
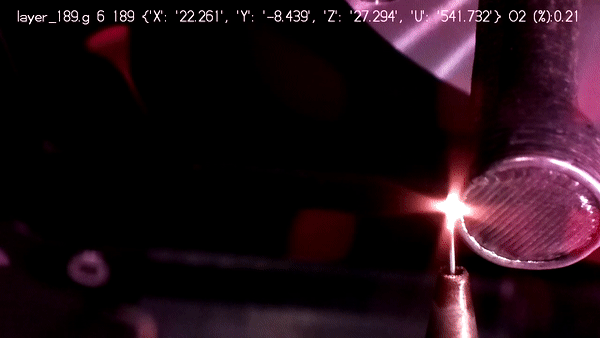
The 180 kg 3D printer lives in the European Drawer Rack Mark II inside ESA’s Columbus module. Controllers on Earth managed the printing process after installation. The printer ran for about four hours a day, with each layer inspected before continuing. This means the printing process took days, but running the machine continuously would, of course, cut printing time significantly.
The printer uses stainless steel wire that is fed to the printing location, where a laser melts it. As the pool of molten metal moves away from the laser-heated spot, it solidifies like plastic does in a regular FDM printer. Of course, with the melting point of stainless steel being around 1400 °C, it runs a lot hotter and thus requires that the printer to be inside a completely sealed box, with the atmosphere inside vented into space and replaced with nitrogen prior to starting the printing process. The presence of oxygen would totally ruin the print.
We badly want a practical metal printer for home use, but, so far, they remain out of reach. When you do get them, you might consider that there are different design rules for metal-printed parts.
Well, ISSS is 450ton of metal and other stuff. They still have 6 years to have it print itself into something else before the deorbit is scheduled.
It’s one of the things I do not understand. Launch costs have gone down significantly over the last few decades, but it’s still around EUR3000 per kg and it would be difficult to halve that again. I don’t know what it costs to put it in a graveyard orbit compared to a deorbit burn, but I would not be surprised if somewhere in the next 10 to 20 years it becomes economically viable to harvest it for it’s raw materials.
How many hundreds of tons of equipment would have to be launched, to ba able to process the metal of the ISS into wire?
Nudge it over to mars for an outpost/lifeboat/Mars Bar!
Even if its not viable to harvest the obsolete bits of it any time soon just pushing it into a stable higher orbit to use the cans as sheds in space – so lots of bits you don’t really want to send down the well, but don’t need right now on the replacement station(s) can just be stored with a little protection from debris, radiation etc while being much much less fuel intensive to get.
That said de orbiting the ISS at all makes no sense to me – de orbiting the oldest bits ship of Theseus style sure, but even when Starship is actually ready to fly and making larger objects to space relatively cheap the existing ISS still makes a lot of sense as the ‘building managers hut’ for assembling the all new replacement, and the modules with more life left in them along with valuable life support/power generation etc makes a good redundancy for the new bits that is surely worth keeping.
Exactly. NASA has never even tried to work with a tight budget, but they are very good at evaporating any budget that has been given to them. I guess they have hardly looked at what else can be done with ISS after it’s no longer useful / usable as a space station.
I wonder how relevant Hubble still is for space research. Space is pretty big, with lots of angles to look at. Maybe now that launch costs have dropped dramatically recently, it would be viable to make another servicing mission and replace some gyroscopes and top up some fuel. According to Wikipedia it’s last servicing mission was in 2009, and I rember very loud voices from around that time that it would be the last servicing mission for Hubble, which sounded absolutely bonkers to me. At the very least put some people together once a year to weigh the cost to benefit equation. A lot has happened in the last 15 years. Apparently they did something like that. NASA rejected a rescueing mission in 2024 according to wikipedia. But currently NASA can’t even bring some people home. They’re not much better then Boeing. And maybe they’re right, I don’t have the background and expertise, but I do know I do not trust NASAL for what they are saying. There is too much stupid politics and shady agenda’s going on when some serious money is involved.
“NASA has never even tried to work with a tight budget”
Go tell that to any PI on any science mission. You may even still have teeth afterwards!
SLS gets money pumped into it for purely pork purposes by congress (against the wishes of NASA), but that does not apply to NASA programmes in general.
I understand the idea of trying to salvage as much of the ISS as possible and reuse it. But I also think I understand some of the difficulties involved. Just some of my thoughts on it…
Just how hard it currently is to do anything in space, especially if it involves a space walk. They spend WEEKS practicing space walks underwater with simulated objects and many safety personnel.
There is really a lot of old tech and designs involved with the ISS. At some point even if it works it is a lot better idea to upgrade and replace it.
Even aircraft get replaced BEFORE they fall apart or present a safety risk. In space even little issues can become life threatening. Look up the MANY serious problems the astronauts have had to deal with over the years. Power, water, sanitation, leaks, other resources.
One single use starship hull could replace the volume of the ISS. Rapid flights could mean giant leaps beyond the ISS very quickly and a lot easier than salvaging the ISS.
One step closer to the Bobiverse.
As the Bobiverse word was new to me, I did a DDG, and after several disappointing links, I found this one…
https://www.bookseriesinorder.com/bobiverse/
Wait! They have sharks in space now!?
No, but they do have pigs in space!
Awaiting the “Print in space” option for CraftCloud.
Am I right in saying the big difficulty with trying to FDM print metal wire this way is the thermal expansion/contraction of your part causing it to really distort? Any slicer would have to account for this, rather than simply map the CAD design to gcode moves? I believe one of the companies that prints rocket engine nozzles has found such a thing to be the case, their big development was inventing a CAD package for themselves which translated from the shapes they wanted to what would actually have to be printed for it to come out properly once cooled. Still, the principle of this looks like the best starting point for home metal printing, as compared to powder and laser based principles.
Also, surprised they didn’t print something with a greater diversity of features. Like overhangs of different angles, a bridging overhang somewhere, some sharp internal corners and sharp external corners. Not necessarily “Benchy”, but there’s a lot of principles included in a wide variety of printer testing models and I’m surprised they didn’t come up with something which would include most of those test features within it.
I feel like putting this outside the station would solve some problems. No oxygen, no need to pump it down and backfill it, heat accumulation in the station reduced by about 70%. But a huge amount of handling issues, obviously. Just, if you have access to infinite vacuum, I’m surprised they don’t use it.
I agree, but also wonder if there is some logistical reason, such as reloading spools.
Vacuum is a very good insulator. The printed part needs a huge amount of cooling, and radiative cooling won’t be nearly enough.
Printing test bars is fundamental metallurgy. Make it and break it. Looking forward to the paper!
could someone please explain why oxygen would ruin the print? i don’t understand it (though it’s obviously obvious to other readers).
thank you in advance!
Hot metal and oxygen react much more. IE rust for steel. That also creates a skin that the next printed layer will not bond to as well.
Here’s a way of printing an entire space station:
https://youtu.be/CyqPvjUyTnw?si=ncWoFu4RZghUHTTA
Did they print any Benchy boats? What is the build volume (dimensions of the X, Y, & Z axis)? Bed slinger? CoreXY,? Do they print with 100% fill? I’m guessing there is no need for supports.