Your project needs a cable, and since USB-C cables are omnipresent now, it’s only natural to want to reuse them for your evil schemes. Ever seen USB 3.0 cables used for PCIe link carrying duty? It’s because USB 3.0 cables are built to a reasonably high standard, both sockets and cables are easy to find, and they’re cheap. Well, USB-C cables beat USB 3.0 cables by all possible metrics.
Let’s go through USB-C cable reuse in great detail, and see just what exactly you get when you buy either a gas station C-C USB 2.0 cable, or, the fanciest all-features-supported 240 W Thunderbolt cable that money can buy. Looking for a cable to cut, or something to pass a seriously high-speed link? You’re reading the right article.
The Omnipresent Cables
USB-A to USB-C cables are the least interesting. They’re equivalent to a microUSB to USB-A cable, except there’s a resistor on the USB-C plug, connected from VBUS to one of the CC pins. That’s it. The cable contains four conductors, there’s really not much new. Save these cables for all the devices still built without the 5.1 kΩ resistors.
Now, a USB-C to USB-C cable – let’s say, 60 W max, the default USB-C cable capability. If your cable says anything less than 60 W, say, “2 A” or “15 W”, that’s a lie – it can handle 60 W no problem, all USB-C to C cables can do 60 W. This cable is also cool – for one, it has five conductors; GND, VBUS, D+, D-, and CC. Two of them (GND and VBUS) are guaranteed to be thick enough to carry 3 A without much voltage drop if any, too!
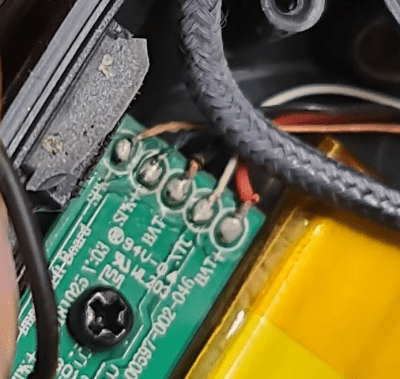
What does this mean? If you need a five-wire cable to fix your headphones, and you want something solid, a USB-C cable is probably your best bet ever – and you have a ton of choice here. You will inevitably end up with a heap of broken USB-C cables, which means you’ll never be short of 5-conductor cables – the kind of cable that has always been kind of a rarity, unless you’re pilfering headphone cables for your projects.
What about 100 W to 240 W cables? There’s good news and bad news. Good news is, the cable is likely to contain six wires. One extra wire is for VCONN – power for the emarker chip inside the cable plug, a memory chip you can read over the CC line, letting the PSU know whether the cable is indeed capable of carrying over 5 A – required for the 61 W to 240 W range.
Bad news is – there could still be five wires, if the cable is built using the alternative scheme with two emarkers, one per plug. The VCONN wire won’t be present then, and there’s no way to know until you cut the wire apart, so if you’re looking for a six-wire cable, you might have to try a few different cables. Also, the VCONN wire doesn’t connect the two plugs together – it’s isolated at one end, so don’t expect it to help if you use USB-C sockets instead of cutting the cable.
Now, you don’t always want to cut the cable – you can use USB-C sockets and apply your custom five-wire scheme to them. An idea I hear often is using USB-C cables for 3D printer hotends. It makes sense – such cables can handle 60 W of power without breaking a sweat, and you could likely do a fair bit more. Put extruder power onto the VBUS and GND pins, and use the three wires left for a thermistor and a limit switch. But the cable and socket mechanicals might be a dealbreaker. If your extruder-powering cable vibrates out of the socket, you might end up with a high-resistance-contact high-current connection on your hands – a recipe for melted plastic and possibly flames. Try it at your own risk!
You also won’t be able to make such cable reuse standard-compliant, and such port won’t be safe for any USB-C devices someone might plug into it, so label it accordingly, please.
What About Voltages?
What about putting arbitrary voltages onto VBUS, without PD negotiation? Again, it won’t be standards-compliant unless you really put some effort in – mark your jury-rigged sockets and cables accordingly, or they will eat your devices for breakfast. Also, SPR (100 W) cables contain 30 V 10 nF capacitors at each plug end, and EPR cables contain 63 V ones – reach these limits at your own risk, those capacitors are known to fail short-circuit.
Another factor is if you decide to go for the 48 V / 5 A target while bypassing the USB-C standard, because 48 V support is not as simple as putting 48 V on VBUS. If you just put 48 V on the VBUS pins, you’ll really want to figure out spark management, so that suddenly unplugging the cable won’t burn either the plug or the socket or both – PD has ways to deal with that, but they do require you to actually implement PD, specifically, EPR, which brings a heap of safety guarantees due to exceeding the 20 V limit.
That’s about it when it comes to reusing the cheapest kinds of USB-C cables – you get an extra wire compared to previous USB standards, it can handle a fair bit more power, and you can even use USB-C sockets. However, it will kill your devices if you’re not careful, and you need to take extra care if you go over 25 V or so. What about if you want to get more wires and pull some differential pairs instead?
Up The Speed
Fully-featured USB-C cables and sockets are genuinely wonderful for pulling high-speed communications over them. They are built to a solid standard, with proper impedance controls, shielding, and a modern-day understanding of digital transmission standards. Now, what exactly do you get from a fully-featured USB-C cable?
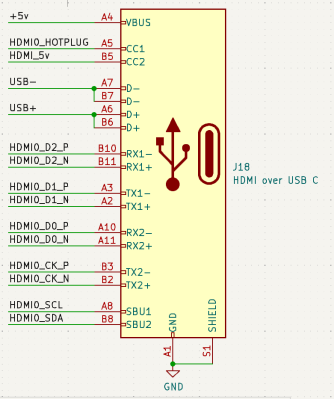
Short answer is, you get six differential pairs, and one single-ended wire (CC), in addition to VBUS and GND. You might want to keep GND at a stable level here, and perhaps don’t mess too much with VBUS. There’s a ton you can do with these six diffpairs – two USB3 ports, or a PCIe x2 link, or two SATA, or HDMI, or CSI/DSI. You can even do Ethernet if you really want to – just don’t expect galvanic isolation to work.
There are nuances, of course! Ever see a teardown or an X-ray of a fancy fully-featured cable? There’s typically all sorts of ICs inside each plug. The first one is the emarker chip, and it’s a fun one to keep in mind. For a start, it will result in some ESD diodes between GND and CC – watch out, don’t bring CC below 0 V or above 5 V.
A second kind of IC is the signal re-driver, used in active cables. You have to provide power to these redrivers through either VBUS or VCONN, just like emarkers. If you don’t do it, your high-speed lines might just be unresponsive to any high-speed signal you apply to the pins.
What about rotation? That’s a tough one – unless your signal is very much like USB3/DisplayPort/Thunderbolt, you might not be able to find a suitable mux chip to rotate your signals. As such, you will likely want to stick to a single rotation and wire your signals directly. Then, if you plug in the cable in an unexpected way, it won’t work, so you should probably consider using the CC pin or the two SBU pins for lighting up LEDs. showing you whether you’re good, or whether you should unplug the cable, rotate it, and plug it back in, like in the good old days.
There’s one last thing you might care about. USB-C cables connect TX on one end to RX on another end, and vice-versa. This is nice for PCIe purposes, since it, too, flips pair naming at the connector. For any other signal, you’ll want to keep it in mind – RX1 won’t go to RX1 on the other end, it will go to TX1, and you’ll have to re-layout accordingly. Unfortunately, I’m not intimately familar with active cable inner workings – so, it’s hard for me to tell whether any active cable redriver chips would reject certain sorts of signaling, perhaps, signals that don’t match USB3, DisplayPort or Thunderbolt signaling types.
And One Last Hack
These are the basics of what you should know before you try and reuse a USB-C cable, no matter its complexity. That said, here’s an extra hack before we conclude!
Only one USB2 pair is actually connected at the USB-C cable end – the pair on the same side as the CC pin. My guess is, this was initially done to avoid stubs and cable plug PCB routing complications, as well as to accomodate standards like VirtualLink. Regretfully, we never got VirtualLink cables, which would allow us to use seven differential pairs at a time, but there is another hack we still get out of this!
What does this mean for you? If you use two USB2-grade 2:1 muxes, you can get two extra differential signals out of a fully-compliant USB socket, and they won’t even interfere with standard-compliant cables. Use this for SWD, JTAG, or whatever else, with your signals broken out through a custom plug – just make sure you dutifully switch the muxes depending on cable orientation, then you can keep your USB2 cake and eat it, too.
Members of the Evil League of Evil only use cursed cables for my evil schemes.
Fantastic artwork!
But seriously, whilst the cables might be a good source of wire, it’s not a great plan to abuse USB-C ports for other purposes. That’s right up there with keeping bleach in soda bottles, keeping methanol in vodka bottles, and keeping arsenic in your powdered gypsum barrel (see Bradford sweet poisoning).
IE it’s a great idea right up until you forget or anyone other than you uses it, or you tell someone they can plug your phone into the charger next to your 3D printer and they misunderstand and plug your phone into the Jerry-rigged hot end PSU.
And no, warning labels only suffice until they’re hidden, run off, ignored, or just not spotted in the moment. The number of times I’ve seen someone miss an “obvious” warning sign… the problem is we’re conditioned to ignore such things through familiarity, and people tend to ignore them on a “common” situation like a USB charger because it doesn’t make sense.
We all think we’re smart and above this until the day it comes back to bite us.
If your plan means it’s no longer safe to plug a typical USB-C device into a USB-C port, or to plug your new special thing into a typical (or cheap knockoff) USB-C charger, reconsider and find a different connector.
“If your plan means it’s no longer safe to plug a typical USB-C device into a USB-C port”
It’s not that hard to guard it so that it’s protected against a USB-C cable being plugged in. Just use one of the cheapo chips that talks the CC protocol. Lets you detect an improperly inserted cable, too. You might need a bit more protection for the USB 2.0 pair, but you don’t want to be using it for high-speed stuff anyway, it’s unshielded and kinda sucks.
The simple fix for the “how do I handle rotation?!?” is to use a single-screw locking USB-C cable. Lookie there, forced orientation, what a novel concept.
https://www.amazon.com/USB-Cable-Delivery-Certified-Interface/dp/B09H2ZXC9B
Disagree. We’re hackers, and we deserve to know how to do things in a pinch with what we have. Fundamentally – like half of my proposed usecases doesn’t even violate the standard too significantly (doesn’t reach the threshold where you risk burning things), and, like a quarter that’s left, could very well be done with a cable you cut apart, so your concerns are entirely not applicable for the most of it. For the remaining part, standards compliance or safeguarding might just be easier than you expect! Working with somewhat dangerous things is a good skill, and risk is a sliding scale where the optimal amount is not zero – especially as far as hacking is concerned.
Better suggestion – learn how to pull off technically-unsafe tricks as safely as possible, and improve upon things like your UX skills. For instance, I’ve done a “USB-C connector that carries hard 20V” a couple of times because that was the best thing in the given situation (the other options were directly worse), but then, I’ve glued stickers or written with permanent marker directly on the connectors – “KILLS DEVICES” directly on the plug is hard to miss. Other projects of mine use warning LEDs with markings that train a double-check reflex in you, and other ones get extra circuitry to limit damage. I guess, bottom line is – power is danger, danger is power, trust hackers to do risky things out of the ordinary if they consider that to be the best option out of all available.
Also, let’s be honest for a moment – “fully safeguarded from average person doing intuitive things” isn’t a standard most of us stringently adhere our homelabs to =D There’s the ideal world where we can theoretically do things perfectly, and there’s the real one where things get done.
Sadly warnings don’t always help. I have seen a bolted down motor controller with giant letters “THIS WILL KILL YOUR MOTORS” getting borrowed and then inadvertently used to kill +2000euros worth of motors.
They just did not notice it while unbolting it from my setup.
spittin’ facts!
When there’s no risk of damaging devices – whether that’s because the signals are electrically compatible, or because you’ve added code to detect and only enable the dangerous stuff if the other end expects it (which is what PD does) – that’s fine – that’s not what I’m warning against.
Making it standards compliant is absolutely what I’m arguing for.
Making something that’s going to damage an unsuspecting USB-C device is what I’m warning against.
Yes, we’re hackers, but that doesn’t excuse us from being responsible and considering safety – ours and others.
And sticking high voltages on cables without warning is as risky as ignoring dust protection or eye protection. Sure you’ll get away with it for a while, but it’ll bite you one day.
And it’s not just our safety, but others’. If you do something weird with an unusual connector, very little risk, but if you’ve got a USB-C port outputting something dodgy, someone coming round will plug something into it one day, warning labels or not.
I agree with your point, to a point, but it isn’t a boolean. Do the most reasonable thing you can, and make sure any remaining unreasonableness is well-labeled. People who choose to ignroe the labels and warnings are choosing to take responsibility for themselves, and for any negative consequences.
This isn’t merely an ethics issue. Not every danger in life is well-labeled, and surviving in the presence of danger is a skill: it requires practice and it rusts if you don’t use it. There are many safety improvements in the modern world that seriously improved life. But not all safety improvements actually improved outcomes; in quite a few instances, the rate of actual injury or fatality remained constant even in the presence of the much safer system, since people began counting on there being less danger.
And finally, as much as it pains me to say it, the wonderful thing about standards is that there’s so many of them! and they often disagree!
If you go look a bit, you’ll find actual real standards to comply with that, nonetheless, will destroy most things with a USB-C connector. And then there’s all kinds of industrial-world (ab)use of connectors that are ACTUALLY STANDARD within their industry, that nonetheless don’t fit with the broader population’s expectations. I know of examples (interoperable between several vendors, thus a standard) using the single-screw locking USB-C connector, and a completely different cable-spec involving all pins going to twisted differential pairs. At least one of the devices I salvaged was date-coded three years before the USB-IF released the related physical connector specification…
Lets’s not forget all of the 8p8c cables out there carrying 4-20ma instrumentation signals or serial rather than ethernet… all three are standards, and they’re mutually-incompatible standards at that…
So you say it is good to ignore universal rules and standards, but you expect everyone to blindly adhere your own rules, which you write with a sticker or permanent marker on some arbitrary surfaces? That’s weird.
So you say it’s okay to blindly do stuff just because it’s convention without understanding anything about the things you’re working with? That’s weird.
Are you going to complain next we shouldn’t have international plug adapters because if you don’t know a device is 110/220 compatible it’ll blow up? Which happens all the time, mind you: it’s a nice “learn how $#!+ works” lesson.
No, I don’t. Sorry for triggering you.
There’s no such thing as a universal rule or standard, because you can’t get all humans to agree about ANYTHING. At best, there are standards that would be nice if they’re universal, but most standards don’t even achieve this. And this is true even in safety-of-life contexts.
I sailed on a ship (sailed by a lot of different crews of atudents) that had several “schuko” power sockets on deck – Some were white and delivered 230V AC when the generator was on or we had wall power, some were painted red and delivered 24V (either DC when running on batteries or AC when the generator was on) and was used for navigation lights and a spotlight.
It looked like a recipe for disaster but in the 10 years I was associated witg the ship that has never gone wrong.
LIDL has sold devices with USB-C connector for power and dumb 12V power supplies with USB-C connector. I wonder how many phones and tablets those have surprised?
hmm go and search what cables are used for stacking cheapo dell switches ;) I spare you search HDMI, in old days, it were 2 USB cables
” keeping methanol in vodka bottles,”
If I ever have to leave my home because Russia is invading this is exactly what I am going to leave behind.
Good idea I shall do same!
You forgot floor wax stripper in a milk jug.
Thanks, Mom.
“keeping methanol in vodka bottles” Ahhh I see you have met my grandpa
“Short answer is, you get six differential pairs”
I’m so confused – are there USB-C cables with 6 actual differential pairs in it. By spec the two sideband pins have no differential requirement and in the few I’ve ripped apart they’re just single-ended.
The wiring diagram here:
https://www.pshinecable.com/article/usb-c-cable-wiring-diagram.html
show the SBU pins as single-ended. They’ve both got weak single-ended impedance control so they won’t be terrible if used differentially, but only at low speeds. It’s also worth noting the true diffpairs are not all identical – the USB diffpair is unshielded, so again, not a high-speed pair.
The other thing to note, of course, is that they’re not 100-ohm differential pairs. They’re 90+/-5 ohm. Tons of the designs I see just ignore the 90-to-100 difference because it isn’t that big a deal, but in some cases (e.g. a scope probe or something analog) it might be.
Also the “That’s a tough one – unless your signal is very much like USB3/DisplayPort/Thunderbolt,” is a bit misleading. High speed exchange switches are not repeaters: they’re just analog pass connections, so all you’ve really got is a max voltage restriction. The signals don’t have to be digital or anything. They can be single-ended for all those things care.
As an aside that also means that stuff like a PI3DBS16222 is a pretty nice and cheap analog exchange switch for balanced signals if you’re doing something clever.
Hmm peculiar! I could be wrong about SBU, for sure – I assumed it because iirc I’ve seen it differential on cross sections, and, it does carry differential signals in case of i.e. Displayport. Good to know, thank you!
On a lot of Type-C cables, the only true twisted pair is the old USB D+/D-. The super-speed guys are allowed to be implemented as individual coax so long as the differential specs are met, and that’s not that hard: since they’re shielded, they’ll maintain mode so long as the shielding’s decent. The differential-to-common conversion requirement’s only 20 dB anyway.
The SBU pair does have a single-ended impedance control such that if you use it differentially it’s ‘nominally’ 85 ohm but the variation on that is huge (~+/-15 ohm) in comparison to the D+/D-. It also has utter garbage insertion loss spec (3 dB bandwidth of ~1 MHz-ish) so it is definitely the last pair you want to use. Although that spec’s generally met with plenty of margin from my experience.
DisplayPort uses it for AUX which only is a ~2 Mbaud path, so at that level it really doesn’t matter.
Please don’t ruin USB-C by making this sort of cursed stuff. :((
There are plenty of USB-to-YouNameIt modules available and pairing them with a simple USB-C female breakout (with proper CC resistors) will make your device universally compatible. I’ve done this to headphones, UART adapters, capture cards, ethernet adapters and more.
Oh there’s like a hundred uses for USB-C connectors that violate the standard but aren’t actually dangerous and they’re super beneficial to everyone involved. MIPI CSI/DSI/HDMI on USB-C connectors for space savings and avoidance of bespoke connectors is one thing I can instantly remember, the Pinecil’s USB-C signal breakout pinout with its devboard is another that’s been a wildly helpful hack, and same goes for the Ox64’s/Oz64’s USB-C connectors that carry a whole bunch of signals on fully-featured USB-C connectors. There’s only three altmodes that really exist, and a ton of uses for an abundant and featureful connector that is USB-C – a lot of things can be retrofitted indeed, but not all of them!
As for the simplest cables – my 3D printer ran for a while with a USB cable used for powering some parts of its hotend assembly cuz the stock cable was badly designed, which, nah I’m not gonna pay a replacement new but still badly designed cable for a printer that’s near the end of its lifetime. Use USB-C sockets, wire up both ends, plug the cable in, then wrap it in electrical tape – doesn’t fall off due to vibrations, and does prevent accidentally plugging this cable into a phone, as a bonus.
Oh and, even if it’s dangerous, it can be worth doing. Here’s an example scenario – for like the first year of me owning my Pinecil, I didn’t have any USB-C supplies to use with my Pinecil at my workbench – only an inflexible barrel jack wire with 20V on it, that’d constantly fall out – or even worse, it’d drag the Pinecil off the desk under its weight sometimes, having it fall on my bed, so I had to catch it. I did have some nice red USB-C super flexible silicone cables from Pine64, though! And, the Pinecil doesn’t actually require USB-C negotiations to start receiving 20V – it just takes input voltages in certain range on either of its ports.
What I did was, soldered together a barrel jack to USB-C adapter, plugged that nice red flexible USB-C cable in, and put a very visible label on its working end plug that went “DO NOT” (all that’d fit on the plug). Traded one risk (Pinecil falling off desk/starting a fire) for another (perma 20V USB-C cable that can fry devices), and it ended up being a damn good trade – it made soldering all that much easier for me, since the flexible cable was way more lightweight, and there were no more Pinecil falls off the desk or sudden unplug events, so the trade ended up being a net benefit as far as safety was concerned.
Doing cursed stuff is part and parcel of being a hacker, really. Other people can shy away from it, but we really don’t have to – after all, witty unintended uses for things are a large part of what makes the hacker community a powerhouse that it is.
USB-C already ruined itself by having cables with identical connectors perform decidedly non-identical functions. “The Standard” for USB-C is complicated and confusing. If you’re going to make a cable that can do anything, might as well lean into it and use it for all purposes.
That is a very bad bit of advice, it might be true often. But manufacturing these days tends to stamp hopelessly optimistic numbers onto their products, not numbers with a safety margin! So actually test the wire carefully before you make that assumption!!!!! It would be really stupid to cause a fire, short out your really expensive SBC or whatever because you made that assumption and found that actually for once the label was telling the truth.
It’s just going to be true. Cheap USB-C cables are defined by their amperage, and the cheap cables you get, will be tested for 3A – cause that’s a commonplace charging current for phones. Then, the cheap cable will get packaged into like a hundred different packages going into different regions and under different labels, and some of the boxes will label their cables “15W” or “27W” because the box label designers won’t realize the cable can be used for laptops and will just slap the highest phone charging wattage they have in mind – whereas, a laptop will put 60W through that cable no problems, purely by asking for 20V/3A from the charger instead of 5V/3A or 9V/3A. If a cable is sold for phones and it’s tested for phones with their high charging currents, it’s safe for laptops – the only difference is voltage and that one barely affects anything of note to the user. Simply put, the probability of the label being dumb is high, and the probability of the cable being unsafe is really low, it’s hard to screw up a USB-C USB2 60W cable in a way it can do 2A and not 3A.
No.
You cannot know whether it was actually tested, or whether the manufacturer chose to disobey the standard and print the actual number that they’ve sized the actual wires for. Buy a cable from the usual suppliers and you never know what sort of mouse hair was used for the wiring until you cut the cable and see for yourself, so if the cable says 15 W I’d rather assume it is for a reason.
I’m not about to praise the free market or something, but manufacturers do test their cables by aiming to avoid fires/malfunctions in the most common usage scenarios, and a 3A over a USB-C cable is a highly common scenario. That’s just a fact – if someone releases a USB-C cable that’s fire-y at 3A, they have very real, unpreventable, prompt and abundant recalls on their hands, simply because those cables get bought in droves and they will be used at 3A en masse. You think you’re smart because you know what 2A implies, but be a little smarter and realize that an average buyer doesn’t know that, and all of them will use these cable at 3A for a year straight without knowing. Essentially, any cable that’s sold in a store, has already been tested at 3A en masse for you. You didn’t have the 3A expectation with microUSB, but you have that with USB-C. Another real-life fact – USB-C cables get sold with dumb shit written on their packaging all the time. I have pictures of USB-C USB2 cables that are labelled with “20MBps transfer speeds” – go figure. Put these two together, and that’s the reason for my recommendation.
Reputable manufacturers. Your typical fly-by-night AliExpress seller isn’t.
“Reputable manufacturers. Your typical fly-by-night AliExpress seller isn’t.”
Why does it matter what a fly-by-night AliExpress seller does? They could sell you a “USB-C cable” that’s literally nothing other than 2 USB-C connectors with no wiring whatsoever in the middle.
It’s just to say that it’s not a universal rule you can rely on, or even bet on. A lot of the “reputable” sources do this too, because they know the cable won’t cause a problem with the particular product they’re selling, so they can “relax” the criteria and put otherwise out-of-spec cables in the box.
You may also be surprised by the number of companies that simply don’t test the cables, especially the smaller companies, and simply assume that what they’re getting is the real deal. This is being abused by manufacturers in the east by mixing the factory rejects in with the proper cables to increase process yields. They’re not going to throw away “perfectly good” cables that test slightly above the specs for resistance, or even a lot above the specs if they know some place they can dump them.
As long as nobody complains, these practices continue, and if somebody does they just say, “Sorry, that must have been a fluke, here have another cable instead”, and continue pushing the rejects somewhere else. It would take a concerted effort by most manufacturers and buyers to weed out the counterfeiters.
“You may also be surprised” I’m surprised by how much pushback I’m getting from you on a basic normative statement backed by simple two-step inductive reasoning, something that’s a socially agreed standard for making an argument and commonplace in Hackaday writing. This is weird and it wastes everyone’s time. I implore you, if you really must, to take the liberty of mentally adding an “on the margins, this might be false” qualifier for every sentence of mine that you read.
“A lot of the “reputable” sources do this too”
USB-C has a 25-page document specification which details exactly what the various limits and requirements are. They will carry 3 A. It’s spec 3.7.5.3.2.
If your reputable sources aren’t meeting spec, you and I have different definitions of reputable. If it says USB type C, it’s 3 A. They can put whatever dumb label crap they want on it (and they do, primarily to avoid weirdo PD issue complaints) but it’s 3 A, max temp rise of 30 deg C, right in the spec.
It’s not the cables you buy individually at a shop that are the real danger, they probably do reach at least bare minimum. It’s the ones provided with low power cheap electronic junk that are the real hazzard, they’re job is to last long enough to prove the device works, then when they fail you replace the cable and move on. Mostly going to be A-C cables at the moment, but C-C are only going to get more common. If you’re raiding the broken bin for some wire guess which ones are going to turn up, I’ve seen some shockingly thin USB2 cables like down to almost single strand. Never assume a random cable is going to reach a common saftey standard, if it came with a device that takes 2W then there’s plenty of manufacturers that would slap a 15W cable in to save money. Reputable companies just put it in the small print to only use thier cable with their device.
“if it came with a device that takes 2W then there’s plenty of manufacturers that would slap a 15W ”
Wire is amperage rated, not power. Yes, sure, the cable might physically be broken, but that’s a risk with any cable ever. You’ve never bought a cheapo thing where the insulation was splitting on the AC power cable?
It’s three amps. It’s not that huge a deal. I mean, if you’re pushing it over magnet wire or something, sure, but even 26 AWG would “work” (it’d get hot, but not super-hot).
Where you’d need to start worrying is if some manufacturers start ultra-cheaping out and sticking iron wire in there instead of copper or something psychotic. So, I dunno, check ’em with a magnet, I guess.
I’m not questioning the style of argument – I’m questioning the trust that you place on the market that is known to be absolutely full of shysters and people who simply don’t care or don’t follow standards because they know they can get away with it.
After all, the consumer won’t really notice if the voltage drop at the end of the cable exceeds the 5% margin. Their phones will simply charge slower because they monitor the voltage and limit the current automatically, so you’re never actually drawing the 3 Amps through the cable. When you put 20 Volts on the cable instead of 5 Volts, the current goes up, and the problem reveals itself.
Then there’s also the point of whether the connector (plating thickness, materials, interface pressure, contact resistance, etc.) are able to handle the required 5 Amps for a 3 Amp cable (safety margin), or whether they’ve slapped on a connector that can only handle 2 Amps safely even though the wires were up to spec. If the device they’re sold with never draws more than 2 Amps, then nobody is any wiser. Put it on a different product that actually draws 3 Amps, and the connector may overheat and destroy the USB socket in your device.
Factory rejects are typically “de-rated” and pushed to market for “less demanding” applications, and these don’t deserve the USB-C label because they aren’t compliant, but nobody is really checking.
Matches my experience really well, especially if you get a warranty replacement or customer returns sold as new, where all it has to be is something the right shape in the box…
The biggest of big brands might always get it right in the first place and actually check everything. So when you buy from them directly maybe you are fine. Not that individual consumer can by from most of them directly, as you aren’t ordering 1000+ batches they ain’t interested! But even that I doubt as in most cases these companies didn’t make the cables, they simply bought them on spec and included them – they probably check a handful, and use them in checking their product but at some point you have to trust the other suppliers in the chain. And Chinesium grade or worse of late seems to be more common than ever.
Of course you can buy from manufacturers where it’s guaranteed, even in qty 1. What are you people buying??
Go to DigiKey and look up type C cables. They’re like $15, with full datasheets specifying construction details and specs.
@Pat And the cables that came with that USB-C hub, reading lamp, monitor, mouse, keyboard or whatever other use of the cable now its used for almost everything even in the most stupid places…
Those may nor may not actually be what you expect. If you are reusing a cable stamped 2A it probably does mean 2A! And the cable that comes with even a high end brand product may not be genuinely to spec – they didn’t make the cables, likely don’t check every single cable from their supplier – so for that supplier being able to dump a $0.20 low grade or factory reject cable in, especially if they know the device its being shipped with and tested against is something like a Keyboard or Mouse that will never draw enough power to matter so they will not be caught…
Nobody is disputing good cables exist! We are simply saying you really can’t trust a cable stamped 2A as being able to run at 3A because the standard claims it should.
” If you are reusing a cable stamped 2A it probably does mean 2A!”
No one’s buying factory reject cables and testing them to 2 amps. The testing would
cost more! If they’re buying factory reject cables, they’re sending them out to you untested with 1 hand ready to declare bankruptcy the instant something catches fire.
If they’re a danger at 3A but not 2A they’re a danger at anything, because you literally can’t design stuff with a factor of ~2 thermal margin because power dissipation of wires varies by orders of magnitude. In other words, if some company buys cables, tests them at 2A and says “they’re good!” and they’re actually like, I dunno, 30 AWG cables, they’re still gonna set someone’s stuff on fire at 2A.
Plus. Again. You’re not saving money by ordering custom USB-C cables with 30 AWG internals. Economies of scale wins.
@Pat who said anything about individual intentionally buying one – there was a huge production of cheap crap charging only cables that would at huge scale cost practically the same as doing it properly, but not quite the same and those pennies add up hugely when you are making billions of the darn things.
And it is the same here – entirely because there is enough demand for the cables to make the economies of scale work really well for you. So you want to be shaving the cables cost down potentially way beyond the actual spec’s lower limits if you can get away with it, or selling the rejects from your genuine production cables as a ‘real’ cable still – if I’m making a billion cables saving fractions of pennies or getting a ‘100%’ yield rather than 85% really adds up.
So if I’m the unscrupulous scumbag that is so common especially in seems in China I will be doing so. Then sending those crappiest cables to all the places I know I can get away with it – like the keyboard and mice producers who’s products won’t find me out so my profit margin is higher!
And you really can’t treat safety margins that way – if its stamped 2A, assuming its actually marked that way for good reason it will handle 3A, probably, at least for short durations as that really should be within or at least close to the whatever they treat as their safety margin. But treating it like a 3A cable now it must be able to handle the safety margin required for a 3A cable, and it won’t! There is a reason so many horror stories exist for electronics melting and catching fire even though the user was doing everything right, the device was actually safe etc…
That’s how they get you. You order a million cables from a subcontractor in China, and the first batch you get is up to spec, you test a bunch and conclude that these cables are “probably fine” with 99% probability. Then you start shipping the product.
As time goes by, the contract manufacturer starts including more and more bad cables into the mix to increase process yields – products made with worn down and ill maintained equipment, by people who aren’t paid enough to care about doing a good job. They’re just waiting for you to catch them cheating. At some point you notice that the cables are failing random testing, so you complain to the supplier – they say “sorry, we’ll fix this” and dump the bad cables elsewhere for a while, then start adding them back to the lot they’re selling to you, always toeing the line where you notice and start complaining.
If you never complain, because your product isn’t using the full 3 Amps and the cables meet your demands, they will give you lower quality that doesn’t meet the official specs because nobody cares.
The issue is that OEMs who subcontract the cables to someone else would rather pay 15 cents per cable if they can get away with it. You get what you pay for, and then if you don’t pay enough for the QA to check all the cables, you’re pushing bad cables down to your customers.
This holds equally true for ANY amount of power. And 3A of power through a cable of those dimensions, even if it’s substantially undersized, is not a catastrophically worse hazard than using it as-advertised; if using it with 3A was a fire hazard, using it as-advertised was also a fire hazard, and the extra amp isn’t going to make it a dramatically better firestarter…
It’s not necessarily a fire hazard, but you do get things like spot heating and coating corrosion that ends up ruining the connector and degrading your device faster than expected. If you keep plugging the bad cable to your phone or other device, expect the other side of the connection to start failing earlier than specified and having charging issues sooner than later.
You expect it to be true, but neither you nor I can know. Also your not being specific enough really, as at higher voltage of course it can handle that – I’d suggest you should rewrite that bit somewhat for clarity.
Especially the implication that if it says 2A it probably means 3A to get the 60W rating – it could easily be a 2A cable even though you wouldn’t expect it to be. Perhaps a link to the voltage/amp table for USB-PD (or include it inline) so you can say something like “otherwise from the USB-PD spec you can make a good guess as that 15W label means – it would almost certainly be stamped that way because its meant to be used 5V@3A”.
But make damn sure to spell out use common sense or verify!!! As you can’t even judge by wire gauge unless you also know the material – so it is far safer to test on the assumption its garbage! Especially as the test isn’t difficult or long, and then you know for sure and the actually valuable bits of your project are at not risk!
So manufacturers never cheap out and use thinner conductors?
It is wishful thinking and naive to think that every USB C cable ever made will be able to handle 3 A properly.
It’s not even the wire gauge – it’s difficult to make the connectors that small to reliably handle 3 Amps with the wear and tear of thousands of insertions. The contact resistance, surface plating and finish, mating pressure etc. matter a lot, and the USB specs are strict on that because most of the cable assembly resistance happens at the mating surfaces where you get spot heating and corrosion.
“Dude”, at this point, I’m genuinely convinced you are arguing without a rigid background in the topic, so I’ll disengage, but not before pointing out the obvious. There are four power pin pairs in USB-C connectors and cables, all in parallel. That is well known. Take 3A, divide by four, get 750mA, which is well beyond the low estimates of what microUSB has handled routinely with its single pair of power pins. If you’re worried about contact surface related problems in a standard specifically designed to avoid these problems further than all the alternative standards, I suggest you step back for a bit and consider your opinion outside of the vacuum, figuratively and literally. Please come back once you have more useful input.
You assume exactly equal current distribution on four parallel contacts when they start to wear down? I would rather watch that very closely, even in an emergency hack.
“You assume exactly equal current distribution on four parallel contacts when they start to wear down?”
If you are using a connector so long it wears down you’re going to have problems period. It doesn’t matter what margin you have.
This is like complaining about battery contacts corroding from leaking batteries.
You’re leaning heavily on the standard as if that somehow defined reality, while I’m trying to explain that so many people and companies simply don’t give a flying F about the standard and simply do what they can get away with.
That’s assuming the connector was made up to the standard, so it would keep its properties beyond the initial small sample testing by the OEM who bought those cables. Three years down the line they can be shipping anything, because extensive testing costs money and the bean counters say it’s not worth it.
So what’s the argument there? If you don’t know the matter intimately, then you should just naively trust whatever the good book says – or more to the point, what YOU as a second hand source says it should be – and design your device accordingly? Don’t trust the label, trust what the part should be according to category and standard, even if the seller of the part explicitly indicates that this part may not adhere or is not tested to the standard by labeling it 2A instead of 3A.
All I can say is that this exact attitude has come back to bite my personal background. When I started scaling up from hobbyist projects to things dealing with hundreds and thousands of items, I noticed that even when you buy genuine parts, one in a few hundred will be a dud. I started noticing that even good parts have a wide spread in their properties and you have to deal with that – give enough tolerance for the worst case or accept the risk, communicate that the risk exists, and deal with the outcomes.
So, if I am not told by the party that sold me the product that the product adheres to the USB-C standard of 3 Amps, then I cannot in good conscience design and spec this part for an application that demands 3 Amps. This would be a fault on MY side as an engineer and a designer, whereas if I am explicitly told that the product adheres to the standard, and it doesn’t, then the fault is on the company that supplies the part for not meeting their claims. This is not just about covering my own ass. If I specify parts and suppliers without appropriate understanding or due care, then by all means I should be fired from the job for being incompetent. Even as a hobbyist, following the same ethics, I do not want to pass on dubious advice simply because it’s “probably” going to be fine.
For example: I know that a particular type of plastic is resistant to chemical A, so I contact a supplier of this plastic and ask them “Is this product you’re supplying resistant to chemical A?”. They say “Yes”, I say good and specify that material from that supplier according to these requirements. If they say “We don’t know” or something else, I will not specify that material from that supplier, because the supplier does not stand behind the claim that it meets my requirements. Maybe it is the correct kind of plastic, but it has some additive that is not compatible with chemical A, or the basic formulation and process is somehow different, or maybe it is exactly as I wanted – I can’t know that just by saying “well it ought to be” based on some superficial textbook knowledge about different plastics. If I pass that uncertainty along, and my customer comes back complaining that the plastic fails in the intended application, the only way I can point the blame is at myself.
“every USB C cable ever made will be able to handle 3 A properly.”
There will be cables that can’t take 3 A that have those connectors on them.
They’re not USB C cables.
Just buy spec’d ones. They’ll work.
And, worth pointing out that with USB-C, making such cables is generally more trouble than it’s worth. Unlike microUSB or Lightning, a USB-C cable will have 3A put through it, so it’s just the new norm for what even the shitty cables are expected to handle.
Sorry Arya but it really won’t. By that same reasoning you could assume every Mini/Micro-USB cable ever made will support data, as every cable could get used for that (or at least tried for that)… And we all know huge numbers of those cables were made that were charging only!
So all the cables shipped with a product than didn’t even need anything like 3A and since separated that still look exactly like all the other USB-C cables – still a huge market for cables that are either factory rejects or deliberately low spec same as there was with the charging only USB cables… Only now there are way more gotcha’s in USB-C’s crazy ‘It is good for everything’ standard…
So if they have done the decent thing of at least stamping its a 1A or 2A cable you’d be far better off believing them or verifying it will actually take the 3A you need rather than going ‘THE SPEC SAYS SO OBVIOUSLY IT WILL ACTUALLY WORK at 3A’ especially while actively encouraging off spec uses yourself!
You don’t intentionally make bad cables. You make cables, and some of them turn out worse than others because of process variation. As your factory is run for years and years, your equipment wears down and the poorly paid people don’t do their jobs properly, so you get more and more cables that don’t pass the specs.
It’s at that point that the factory either starts ignoring their own QA to pass more cables, or intentionally pushes the failing cables to other distributors that then sell these products on to companies that don’t bother checking.
All I’m going to say on this is i have gotten NEMA 15 cables that when cut off have about the same thickness of wire as a headphone cable
Not really true – USB3 speeds A-C cables do exist, and those will need more conductors to do the USB3 @ 5 or 10 Gbps part!
good point, yeah, those carry two more diffpairs and a drain wire that’s basically ground but I think sometimes separated from ground? not sure though.
I don’t know if there is actually a true standard in the wild of how those cable are wired up ground wise. Doesn’t really make much sense to include extra conductors most of the time probably.
They typically do not use USB cables like you described for 3D printer hotends. They usually have an MCU and toolboard on the hotends and it connects to the rest of the printer either using USB or CAN. When running a system like klipper it is as easy as plugging the USB hotends into a powered hub and into the SBC. For CAN they just repurpose the cable or use custom cables to connect to a CAN adapter that is connected to the SBC.
By doing it this way it isn’t limited to what you can power and connect with 5 conductors, meaning you can connect all kinds of things to the toolhead board, like thermistors, fans, bed levelling sensors, servos, LEDs, etc.
Is there a “smoke test” device for consumer USB tables?
Hopefully without creating actual smoke, but some rig you can plug a cable in to say “this will handle X watts no problem” vs “this will get hot for anything over milliAmps so don’t plug in to anything!”
“USB table”?!
You can always just connect a PSU, apply a voltage, connect a load and measure the voltage drop.
-> you get the rough resistance of the cable and can calculate it’s heat dissipation at eg. 20V 3A
yeah a voltage drop test is the simplest thing you’d do – measure current passing through the cable, measure the voltage drop, and you get “how much power is wasted inside the cable itself”, ofc plus contact resistance in the sockets you’re using. Not that this is much of a problem in practice, and I’ve bought cheap USB-C cables aplenty!
yes, I meant “cable”
I’m late the party here but I’m very happy with the kit I built from https://www.siliconchip.com.au/Issue/2021/November/USB+Cable+Tester+%E2%80%93+Part+1
It puts a load on the power pins and checks the resistance. Not perfect, but a good start.
I have lately been working on my first thingy involving USB-C (a little milled C-to-μB board so I can connect to a Pico while siphoning USB-C current to power servos and stuff from the same connection). It’s for a special animatronic hat you see, so I need it to be very thin.
Rather than just cutting open one end of a cable, I blithely ordered some C receptacles to do it the “proper” way. It turns out I seriously underestimated how delicate the scale is compared to working with trad USB. Also, if you buy the cool low-profile receptacles, the routing is much more complicated, because the reversible wiring means you have to cross a bunch of traces over each other. I broke a 0.2mm end mill and ruined 3 boards soldering those tiny pins by hand.
It’s been a fun exercise but I guess the moral is (again) that if you want to build with modern parts, you need a reflow oven and a PCBWay account.
” I blithely ordered some C receptacles to do it the “proper” way.”
You can buy USB-C ports that only have the USB2 stuff connected: look for 16+8. There are other ones which dummy out more pins, but I think those have limitations.
They’re 0.5 mm pitch, which is SSOP pitch (so a little tighter than micro-USB, which was often 0.635 mm) and if you can’t do that, you can just get the through-hole ones. If you really need a proper USBC with the super-speed stuff at some point, use a vertical flag connector, they fan the connections out both sides so it’s trivial to route and hand-solder.
You can actually also buy USB-C ports with just the power stuff connected, and that’s definitely trivial to solder.
That being said, you don’t need a reflow oven, you just need hot air, and with skill that’s a lot more reliable than an iron anyway since you heat the planes too.
Ironically there is an HDMI alt mode. https://www.ti.com/lit/pdf/slla333 even describes implementing it using a displayport alt mode mux. Although the PD commands to enter that mode are still not known to the public.
I think this is one case where the closed nature of an HDMI standard really did tank its adoption – if you were a company building USB-c to HDMI cables or dongles, it was safer to just slap a cheap active converter in your cable and use displayport alt mode than to gamble on whether your customers’ devices actually natively supported hdmi over USB-c.
I know passive hdmi alt mode cables exist, but I’ve never seen one.
passive hdmi cables, sould only carry tmds video signal and therefore would not work with drm.
Anything else could damage your devices (both dcc & heac/hotplug is 5v, and cec is missing!)
I feel like this is true IF the cable is a rare genuinely made-to-spec USB cable and not one of the vastly more popular cheap ones churned out in the billions and sold through all the popular online retailers which are quite famously almost never anywhere near spec…
Have we forgotten this hero already?
https://www.theverge.com/2016/2/3/10905432/usb-c-cable-fries-google-engineers-computer
USB cables made to spec aren’t rare, and they aren’t even expensive. Just buy from a place that actually has a friggin’ engineering drawing for them. They’re like $5.
Arya is talking about reusing the cables which is an entirely different thing to buying and trusting a new one from a reputable retailer! Very different to blindly trusting the cable you have in hand that you probably have no idea where it came from is actually up to the spec especially if its actively marked in ways that imply it isn’t!
There seems to be a lot of defense for using USB-C cables for non-USB purposes, including voltages & configurations that could potentially damage devices expecting a USB compliant connection. WHY?
1) To use USB-C cables for your project, wouldn’t you have to purchase 1 or more USB-C sockets/female ends as well?
2) There are a million types & styles of cheap connectors / cables available in every possible number of conductors & current rating – all available on aliexpress for pennies. EG: I design a lot of projects that get assembled and installed temporarily in outdoor environments. So, I buy packs of cheap 2/4/6/8 pin waterproof circle connector pigtails (similar to M8 & M12 connectors). Aside from being waterproof, they won’t accidentally become unplugged and are pretty rugged, which is also needed for that application.
Maybe USB-C connectors & cable work for your project, but chances are there’s something more ideal if you think about what would actually be ideal. With a little bit of project foresight, combined with a little bit of patience waiting for the slowboat from China – you can give your project IDEAL connectors/cables, that are also SAFE and also CHEAP.
USB-C can be done safely without much trouble.
It might not be ideal, but it is standardized, and compatibility with cables you already have is huge.
It doesn’t replace 2.1mm and 3.5mm though.
The USB2.0 lines are redundant and don’t need any active switching to reverse them. Plenty of protocols to choose from that will not damage USB devices if accidentally plugged, especially if you add some extra current limiting resistors just in case.
I wonder how many USB cables have a bad pin, and we’ll never know because of the redundancy? That’s one of the coolest things about USB-C, so it’s worth the effort to only use the 2.0 pins, the power lines, and VCONN.
Hackers like “made to fit” stuff, but I prefer “made to measure” designs meant to work with any random cheap crappy cable
I never reuse modern cables and built over time a lifetime stash of military/industrial/civil surplus ones, the reason being that many modern cables aren’t pure copper but copper coated iron. Check your cables with a magnet, especially that crap sold by the usual online shops, chances are that you’ll find several iron coated ones, and they’re quite bad for everything for having a much higher resistance. Manufacturers also use aluminium cables; they not react to a magnet but also have higher resistance compared to copper and are a nightmare to solder.