The ease of integrating bendy parts into designs is one of 3D printing’s strengths. A great example of this is [uhltimate]’s six-shot blaster which integrates several compliant mechanisms. The main blaster even prints in one piece, so there’s not even any assembly required.
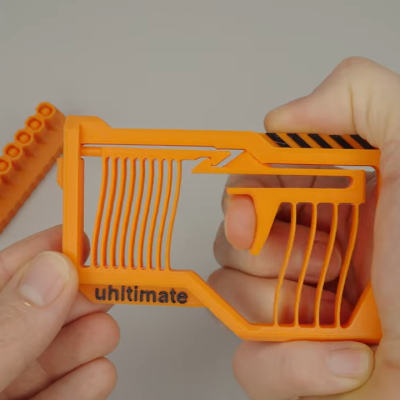
The blaster itself has three main parts: the trigger, the sear, and the striker. Each of them rely on compliant mechanisms in order to function. The user pulls back the trigger, which hooks into and pulls back the striker. When the trigger is pulled back far enough, the sear releases the striker. This zips forward and slams into a waiting projectile, sending it flying.
The other interesting part is the projectiles and magazine in which they sit. The magazine fits onto the front of the blaster and pulling the trigger allows the magazine to drop down, putting the next projectile into firing position. After the final round is fired, the empty magazine falls away. It’s a pretty clever design, even if the ergonomics are a little unusual and it relies on gravity in order to feed. Tilt it too far sideways or upside down, and it won’t load properly.
We’ve seen compliant mechanisms used for projectile firing before, but this design really raises the bar in the way it does more than just firing the striker.
3D printing allows rapid iteration of designs, which makes devices that rely on compliant mechanisms much easier to develop and fine-tune.
That’s brilliant! Ergonomics are easily solved
How would the ergonomics be easily solved? You mean by the designer? Or the end user?
The problem with STL files is that they aren’t easily modified. I understand where they are useful, but with 3D printing becoming so popular, there needs to be a new universal editable file type so the ergonomics CAN be easily solved. Maybe even have the ability to make certain aspects “locked or read only” for those that don’t want remixes or that want the bulk of their design to remain unchanged but the contact points capable of being modified by those so inclined. Along the equivalent of a .txt or .doc file, though I don’t really expect it to happen, it would be nice.
STLs are (relatively) easily modified, you need to use tools meant for working on meshes (Blender perhaps).
Otherwise it’s not that complex of a design, sketch it up in your favorite parametric CAD package.
Stl is basically locking it read only status… perspective issue.
Even then u can still find ways to import it. Skill issue.
This is 100% incorrect. STLs are easily editable. Blender (as mentioned above) is a solid, free choice. Though there are many other good options.
As for the ergonomics issue mentioned above, a grip could easily be designed around the trigger springs at the back. A simple undercut lifting the frame between the spring mechanisms would provide enough real estate for a finger, then just extend that grip down if more is needed.
Note: This design doesn’t have a cocking stage and a good engineer would design the flexing beams such that they never exceed the material elastic limits and therefore not take a permanent deformation. Not to say this design has those considerations but it is possible.
How so? I edit STLs all the time. Printables and Thingiverse are full of remixes (edits) of stl objects.
I’ve come to the conclusion that unless the compliant parts are replaceable, they aren’t worth printing. Because they WILL start to creep and suffer permanent deformation, either thru use or because you “cocked” it and set it down for a couple min etc. Then you have non compliant components and a useless chunk of plastic to get tossed in with all the other plastic and 3D Printer scraps/waste.
I’m also concluding that 3D printing will be much more useful when people start figuring out ways to integrate other types of materials. This gun would work much better with a few thin metal compliant parts in addition to the plastic to add strength but also help pull them back “home” to their initial resting position. So now I need a laser cutter. That or just use traditional springs to start with…
It’s not worth printing because it’s a toy that you will fiddle with maybe twice and then throw into the “stuff from thingiverse that I impulsively printed” pile. I estimate that approximately zero of these will ever break from overuse.
And tons of people make 3d-printed things that have a couple metal parts added afterwards… But the entire point of the compliant mechanisms thing is to make it so that this is unnecessary and you can print complete tools in one pass with pure PLA and no manual crafting/post-processing.
What if the compliant part at the front (the one which the hammer rests on top of) was printed separately and at only half or three-quarters the height of the rest of the build, with little pins at the bottom to go into nooks/holes added in the bottom of the main part? I am talking about the part that is blue in the video thumbnail. That way when/if it does deform, you can print just that again and swap them out. Am I making sense? Would there be a problem with strength at the bottom as a result? Not an expert here, just a STEM educator with a Prusa.
Or just do a multi-material print with a TPU or something.
This reminds me a lot of Mark Rober’s “Smallest Nerf Gun,” simplified.
https://youtu.be/9c2NqlUWZfo
That was awesome.
You’ll put your eye out!
It’s ok, I have a spare.
Nice build! love the ‘simplicity’ of the design (while i’m sure it wasn’t simple to come up with a good design+material combo)
Do hope they try make a follow-up design with the magazine in a more conventional position tho
“Do hope they try make a follow-up design with the magazine in a more conventional position tho”
Why? This works. The mechanics, weight and chemistry of an actual firearm don’t apply here and proposed change would be counter-productive. But hey, go for it, I’m curious to see how you solve the new design issues.
Gravity feed is neat, but untenable. What’s the point of having a (nerf) gun if you can’t fly through the air sideways firing two of them at the same time while your buddy captures it in super slow-mo on his camera. Clearly you haven’t thought this through!
What’s the conventional position for a magazine? It’s always moved all over the place depending on the needs of the mechanism. If this had any sort of barrel, it would fairly closely resemble a grease or sten gun with the magazine way up front. Because there’s no follower spring and it’s purely gravity-fed, it’s upside-down. The sten gun was weird because it was off to the side for basically no (decent) reason, despite having a follower spring.
But if you look through firearm design, the magazine has basically been anywhere from stem to stern and pointed in every cardinal direction. And sometimes it even sticks out diagonally. Sometimes it’s a belt. Sometimes it’s a big room beneath the deck of a battleship, connected by elevator. Once it was a Greek temple (sad story, don’t want to talk about it).
It’s all about the needs of the situation
The Sten had a few good reasons to put the magazine on the side. Ones that people can relate to: It let the user fire with their head closer to the ground, which is desirable when someone is shooting back at you. Should you feel the desire in battle to “kiss the dirt” the magazine did not hit the ground first, which is important for cheaply manufactured magazines as they don’t like being dinged around much and get stubborn about letting the cartridges out afterwards. Last on the obvious list is that you can see where the magazine is going if you survive long enough to put a new one in.
The manufacturers knew they were not designing the best user experience. They needed an awful lot of guns in a great hurry, using a pre-existing supply chain and manufacturing base. They were at the point of desperation where they even had to design the thing to run on enemy ammunition acquired at a five-fingered discount.
TL;DR it worked.