In 2015, Tim Ellis and Jordan Noone founded Relativity Space around an ambitious goal: to be the first company to put a 3D printed rocket into orbit. While additive manufacturing was already becoming an increasingly important tool in the aerospace industry, the duo believed it could be pushed further than anyone had yet realized.
Rather than assembling a rocket out of smaller printed parts, they imagined the entire rocket being produced on a huge printer. Once the methodology was perfected, they believed rockets could be printed faster and cheaper than they could be traditionally assembled. What’s more, in the far future, Relativity might even be able to produce rockets off-world in fully automated factories. It was a bold idea, to be sure. But then, landing rockets on a barge in the middle of the ocean once seemed pretty far fetched as well.
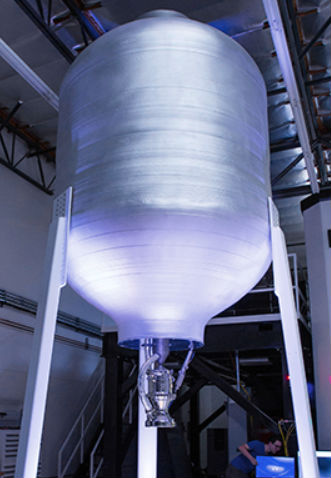
Of course, printing something the size of an orbital rocket requires an exceptionally large 3D printer, so Relativity Space had to built one. It wasn’t long before the company had gotten to the point where they had successfully tested their printed rocket engine, and were scaling up their processes to print the vehicle’s propellant tanks. In 2018 Bryce Salmi, then an avionics hardware engineer at Relatively Space, gave a talk at Hackaday Supercon detailing the rapid progress the company had made so far.
Just a few years later, in March of 2023, the Relativity’s first completed rocket sat fueled and ready to fly on the launch pad. The Terran 1 rocket wasn’t the entirely printed vehicle that Ellis and Noone had imagined, but with approximately 85% of the booster’s mass being made up of printed parts, it was as close as anyone had ever gotten before.
The launch of Terran 1 was a huge milestone for the company, and even though a problem in the second stage engine prevented the rocket from reaching orbit, the flight proved to critics that a 3D printed rocket could fly and that their manufacturing techniques were sound. Almost immediately, Relativity Space announced they would begin work on a larger and more powerful successor to the Terran 1 which would be more competitive to SpaceX’s Falcon 9.
Now, after an administrative shakeup that saw Tim Ellis replaced as CEO, the company has released a nearly 45 minute long video detailing their plans for the next Terran rocket — and explaining why they won’t be 3D printing it.
Meet the New Boss
For the mainstream press, the biggest story has been that former Google chief Eric Schmidt would be taking over as Relativity’s CEO. Tim Ellis will remain on the company’s board, but likely won’t have much involvement in the day-to-day operation of the company. Similarly, co-founder Jordan Noone stepped down from chief technology officer to take on an advisory role back in 2020.
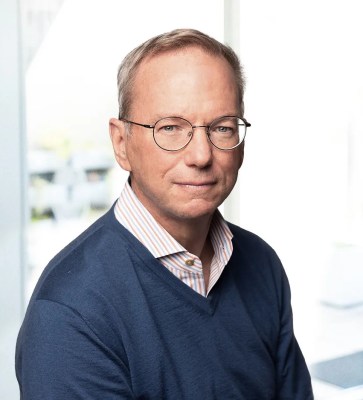
With the two founders of the company now sidelined, and despite the success of the largely 3D printed Terran 1, the video makes it clear that they’re pursuing a more traditional approach for the new Terran R rocket. At several points in the presentation, senior Relativity staffers explain the importance of remaining agile in the competitive launch market, and caution against letting the company’s historic goals hinder their path forward. They aren’t abandoning additive manufacturing, but it’s no longer the driving force behind the program.
For his part, The New York Times reports that Schmidt made a “significant investment” in Relativity Space to secure controlling interest in the company and his new position as CEO, although the details of the arrangement have so far not been made public. One could easily dismiss this move as Schmidt’s attempt to buy into the so-called “billionaire space race”, but it’s more likely he simply sees it as an investment in a rapidly growing industry.
Even before he came onboard, Relativity Space had amassed nearly $3 billion in launch contracts. Between his considerable contacts in Washington, and his time as the chair of the DoD’s Defense Innovation Advisory Board, it’s likely Schmidt will attempt to put Relativity the running for lucrative government launches as well.
All they need is a reliable rocket, and they’ll have a revenue stream for years.
Outsourcing Your Way to Space
In general, New Space companies like SpaceX and Rocket Lab have been far more open about their design and manufacturing processes than the legacy aerospace players. But even still, the video released by Relativity Space offers an incredibly transparent look at how the company is approaching the design of Terran R.
One of the most interesting aspects of the rocket’s construction is how many key components are being outsourced to vendors. According to the video, Relativity Space has contracted out the manufacturing of the aluminium “domes” that cap off the propellant tanks, the composite overwrapped pressure vessels (COPVs) that hold high pressure helium at cryogenic temperatures, and even the payload fairings.
This isn’t like handing the construction of some minor assemblies off to a local shop — these components are about as flight-critical as you can possibly get. In 2017, SpaceX famously lost one of their Falcon 9 rockets (and its payload) in an explosion on the launch pad due to a flaw in one of the booster’s COPVs. It’s believed the company ultimately brought production of COPVs in-house so they could have complete control of their design and fabrication.
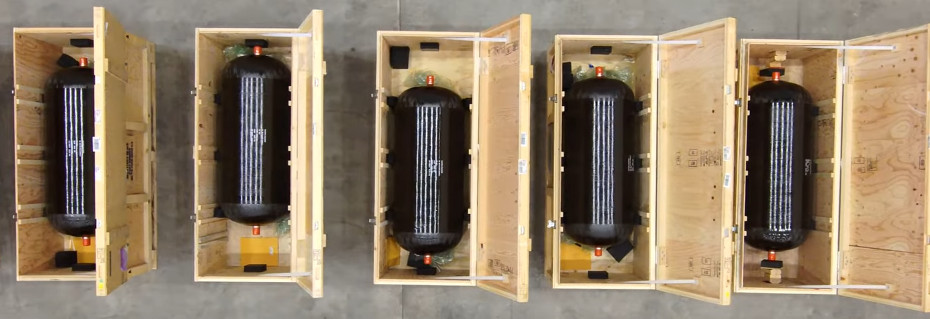
Farming out key components of Terran R to other, more established, aerospace companies is a calculated risk. On one hand, it will allow Relativity Space to accelerate the booster’s development time, and in this case time is very literally money. The sooner Terran R is flying, the sooner it can start bringing in revenue. The trade-off is that their launch operations will become dependent on the performance of said companies. If the vendor producing their fairings runs into a production bottleneck, there’s little Relativity Space can do but wait. Similarly, if the company producing the propellant tank domes decides to raise their prices, that eats into profits.
For the long term security of the project, it would make the most sense for Relativity to produce all of Terran R’s major components themselves. But at least for now, the company is more concerned with getting the vehicle up and running in the most expedient manner possible.
Printing Where it Counts
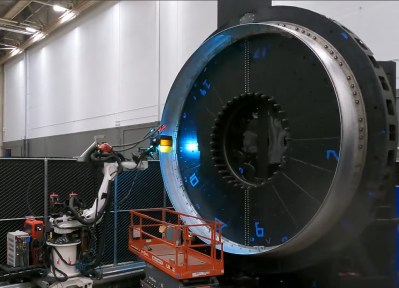
In some cases, this is where Relativity is still banking on 3D printing in the long term. As explained in the video by Chief Technology Officer Kevin Wu, they initially planned on printing the propellant tank domes out of aluminum, but found that they couldn’t produce them at a fast enough rate to support their targeted launch cadence.
At the same time, the video notes that the state-of-the-art in metal printing is a moving target (in part thanks to their own research and development), and that they are continuing to improve their techniques in parallel to the development of Terran R. It’s not hard to imagine a point in the future where Relativity perfects printing the tank domes and no longer needs to outsource them.
While printing the structural components of the rocket hasn’t exactly worked out as Relativity hoped, they are still fully committed to printing the booster’s Aeon R engines. Printing the engine not only allows for rapid design iteration, but the nature of additive manufacturing makes it easy to implement features such as integrated fluid channels which would be difficult and expensive to produce traditionally.
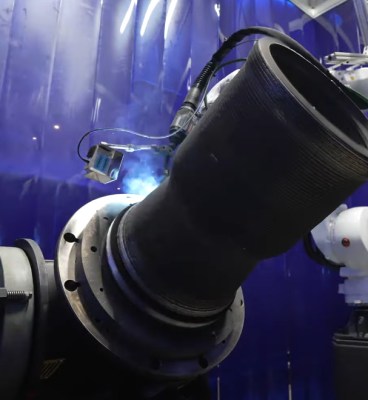
Of course, Relativity isn’t alone in this regard. Nearly every modern rocket engine is using at least some 3D printed components for precisely the same reasons, and they have been for some time now.
Which in the end, is really the major takeaway from Relativity’s update video. Though the company started out with an audacious goal, and got very close to reaching it, in the end they’ve more or less ended up where everyone else in aerospace finds themselves in 2025. They’ll use additive manufacturing where it makes sense, partner with outside firms when necessary, and use traditional manufacturing methods where they’ve proven to be the most efficient.
It’s not as exciting as saying you’ll put the world’s first 3D printed rocket into space, to be sure. But it’s the path that’s the most likely to get Terran R on the launch pad within the next few years, which is where they desperately need to be if they’ll have any chance of catching up to the commercial launch providers that are already gobbling up large swaths of the market.
regarding the huger 3D printer… I know it doesn’t work that way, but in my mind I see: a production worker walking in early in the morning seeing a misprint looking like a really huge pile of spaghetti-like metal underneath the printthead. Or just imagine a rocket that during the printing process missed a few steps halfway and now the top-half of the rocket is slightly shifted to one side.
You are a bunch of positivity…
This 3D printed rocket is just amazing. Increasing the througput is usually done by adding more printers, but maybe their choice in an all-metal fuel tank is not the best. As a long user of 3D printers I would say that the real strength of 3D printing lies in the ability to make composites that are not possible with other methods. It can increase the strength of materials tremendously while keeping the weight as low as possible.
All metal fuel tanks for cryogenic propellants generally are the best option; metals like stainless and aluminum handle cryogenic temps from say liquid oxygen a lot better than carbon fiber.
“that Schmidt made a “significant investment” in Relativity Space to secure controlling interest in the company and his new position as CEO”
Gotta love how someone can just buy their way into being CEO…
The ‘beauty’ of publicly traded companies as they are now.
I wonder if things would improve should stocks have a mandatory 5 year freeze after any trade. So if you are buying in you are locked in for awhile.
Maybe it’d eliminate all the short term profit grifting.
Controlling shareholders appoint board members. The board appoints the CEO.
That’s not a new development. This has been the case since practically the beginning of modern corporations (I want to say several centuries?).
Prohibiting trades for 5 years is not a good idea unless you want to destroy the stock market.
Right or wrong, “Short term profit grifting” is a fundamental part of what drives the market. If you insisted every trader in the market “should go long” there would be no market — it would just be certificates of deposit without any guaranteed return — also known as “lottery tickets.”
The current stock market is already broken with shareholders happily buring companies down so that the stock jumpes 10 cents and them they sell it all off.
The stock market is already basically gambling, it’s just that the rich have enough money to be able to play and spread it out to make money when the odds shift slightly better.
The real point of stocks, IMO, is to help build up healthy companies with an influx of capital and for the investors to profit by driving a company to long term profit and stable growth. Its just that it got corrupted by the lack of better guard rails into sub-microsecond trade hell.
Well, you certainly have all the Marxist talking points in place, demonstrating your complete lack of knowledge of how the market actually works.
That’s interesting because I don’t believe I am Marxist.
However, your comment is useless since it doesn’t even try to spread whatever knowledge you have. So either you are hording some insight or a fool just throwing around labels for anyone that disagrees with how things currently seem to work.
Relativity Space is a private company, meaning if someone owns the majority of it, they can do absolutely whatever they want with it. This makes it more like any of the possessions you own where you can do whatever you want with them, and it also makes your whole comment invalid.
Whole comment isn’t quite invalid, public companies can be taken over that way. What it invalidates is sympathy for this specific company and CEO since it means the founders/owners had to have allowed him that stake and it wasn’t just bought from under them.
Thank you for the correction because it means that even if I hold something against the current structure of how public trading is handled, that isn’t even relevant to this situation.
Well yes, owning a company (or most of it) gives you authority over it.
That’s sorta the point of buying a company.
So, is tariffs having any effect on the space race?
Most likely not too much since a lot of contracts are from governments that control sourcing. Raw materials might be affected somewhat but are such a small percentage compared to the engineering and manufacturing costs of aerospace components.
Difficult to say for sure, but I’d say it’s probably unlikely. They’re just reciprocal tariffs and I think the space race ended back in the 60s.
Tell that to China
Gotta say that it’s rather sad that the main goal is getting sidelined.
I think the “main goal” is to compete in launch capability. 3d printing is grear for prototyping but is usually more expensive when it comes to production. No one is printing where welding, molding, and machining are possible for production parts. Additive is mainly used for parts that cant be made in more conventional methods.
Yeah, I feel that the original goal of fully 3D printed was probably more of a buzzword driven idea that isn’t really logical. 3D printing is just another tool, and just like other tools, there are cases where it does and doesn’t make sense, even if it would theoretically work. I could have the goal of making a rocket purely out of billet aluminum machines on a lathe and mill, and probably be pretty successful, but extruded pipes and sheet metal are just much more reasonable options in terms of price and ease for certain sections of the rocket.
seems like 3D printing houses…for certain parts of the process, it gives you an unparalleled flexibility but for everything else it’s just an awkward misfit. use it where it makes sense but the dream of like eliminating skilled trades (plumbers and electricians and finish carpenters) was never going to be.
Agree that it makes about zero sense when compared to plant manufactured prefab.
It’s odd that the article fails to mention the other very audacious goal they gave up — Terran R was initially going to be fully reusable.
They’ve not given up, just delayed it behind initial operating capability (i.e. make money by launching first, spend that money to develop reuse after). That’s not an unusual choice: it’s how Falcon 9 was developed, and how all other reuseable rockets in develop intend to operate (e.g. Rocket Lab’s Neutron, Stoke’s Nova, etc).
Speaking only for myself the idea of 100% 3D printing always seemed a bit silly. Certain parts are just going to be a lot easier to make with other methods. Relativity’s claim to fame and competitive advantage can still be “we’re the best in the world at 3D printing rocket parts” without committing to every single part being made that way.
“In 2017, SpaceX famously lost one of their Falcon 9 rockets (and its payload) in an explosion on the launch pad due to a flaw in one of the booster’s COPVs”
Technically, they lost it due to a flaw in the Helium loading process. SpaceX, in their drive to reduce the launch timeline, decided to simultaneously load LOX into the upper stage tank and condition the COPVs for LHe load. This worked for a few flights, but what happened on AMOS-6 was that the Helium prechill dipped the temperature of the overwrap below the freezing point of the LOX it was partially immersed in, allowing some LOX within the overwrap to freeze, expand, and break some of the composite fibres. The helium fibres compromised the wall integrity of the COPV, and it popped. This opened up the Helium pressurant line to the LOX tank, which then overpressured the LOX tank (LHe bottle pressure is hundreds of Bar, the LOX tank flight pressure is under 4 Bar). The combination of combined LOX load and LHe chill and the LOX absorbed in the liner caused the failure, but changing any one of those would mitigate it (as on all previous flights and other vehicles using COPVs, which is most).
A better example would be the loss of CRS-7, where an outsourced COPV support strut failed below design loads.