Do you like high-detail 3D models intended for resin printing, but wish you could more easily print them on a filament-based FDM printer? Good news, because [Jacob] of Painted4Combat shared a tool he created to make 3D models meant for resin printers — the kind popular with tabletop gamers — easier to port to FDM. It comes in the form of a Blender add-on called Resin2FDM. Intrigued, but wary of your own lack of experience with Blender? No problem, because he also made a video that walks you through the whole thing step-by-step.
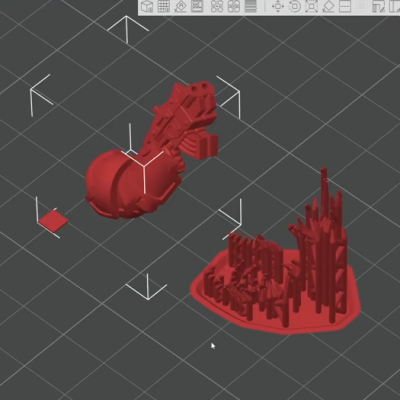
3D models intended for resin printing aren’t actually any different, format-wise, from models intended for FDM printers. The differences all come down to the features of the model and how well the printer can execute them. Resin printing is very different from FDM, so printing a model on the “wrong” type of printer will often have disappointing results. Let’s look at why that is, to better understand what makes [Jacob]’s tool so useful.
Rafts and a forest of thin tree-like supports are common in resin printing. In the tabletop gaming scene, many models come pre-supported for convenience. A fair bit of work goes into optimizing the orientation of everything for best printed results, but the benefits don’t carry directly over to FDM.
For one thing, supports for resin prints are usually too small for an FDM printer to properly execute — they tend to be very thin and very tall, which is probably the least favorable shape for FDM printing. In addition, contact points where each support tapers down to a small point that connects to the model are especially troublesome; FDM slicer software will often simply consider those features too small to bother trying to print. Supports that work on a resin printer tend to be too small or too weak to be effective on FDM, even with a 0.2 mm nozzle.
To solve this, [Jacob]’s tool allows one to separate the model itself from the support structure. Once that is done, the tool further allows one to tweak the nest of supports, thickening them up just enough to successfully print on an FDM printer, while leaving the main model unchanged. The result is a support structure that prints well via FDM, allowing the model itself to come out nicely, with a minimum of alterations to the original.
Resin2FDM is available in two versions, the Lite version is free and an advanced version with more features is available to [Jacob]’s Patreon subscribers. The video (embedded below) covers everything from installation to use, and includes some general tips for best results. Check it out if you’re interested in how [Jacob] solved this problem, and keep it in mind for the next time you run across a pre-supported model intended for resin printing that you wish you could print with FDM.
If you can split the supports and the model, why not just delete the supports entirely and let the (FDM) slicer put them where it deems best?
For FDM minis, auto generated tree support removal can be a challenge, and leave lots of scarring. The scarring from these supports are much easier to remove and clean up with a hobby knife or pair of clippers.
Actually, if you dial in your FDM supports this is not an issue. What is being tried with Resin2FDM has very limited usage and success. The supports on pre-supported resin models are rarely in an optimal place for FDM printing. I’ve actually tested and compared his method against my own optimized FDM supports and the results with Resin2FDM take more material, more time, and results in less quality. It may work for some limited number of models but not the majority. There is more to it then just thickening resin supports.
Lately, people have been experimenting with using FDM-optimized resin supports for minis and the results have been superior to tree supports, when configured and placed well. The minimal contact area of (widened and differently-structured) resin supports seems well-suited to delicate mini structures, leading to minimal scarring, reduced part failures, and easier removal. Once in a Six Side on YouTube has done a few videos on the technique recently, and the results are great once you know the workflow and find a filament that works – he’s found that it’s extremely sensitive to filament choice.
Actually, if you pay close attention there are a lot of failure points. If you actually take the time to dial in your FDM settings the results will be better with less failures then attempting to use these Resin supports that are absolutely not optimized for FDM printing. Once on a Six Side completely glossed over the fact that the Arbiter Miniatures models he started with were actually designed for FDM. They weren’t simply thicker Resin supports on any old models.
I’ve been doing FDM printing of miniatures for almost a year now and have tested these setups and there is a lot that is being glossed over by both Once on a Six Side and Painted4Combat.
Not all of them can be split, some are just attached to the model in the same stl and not able to be split without more work.
Except the article says that’s exactly what this plugin does.
That was my thought.
I suppose for the same reason Resin printers don’t use the same supports FDM printers do. You use less material, and its pretty easy to remove. Plus the model (theoretically) has already been optimized to have support where it needs it.
I feel like 3d printing has lost all of it’s newness, luster, or what ever magic it had. Now it’s just a tool. And just like any tool, it’s good at some things and really bad at others. Maslow’s hammer.
for me when it lost its newness is precisely when it became magical to me :)
one day i had an idea in my head while i was biking home and the moment i got home i implemented it and half an hour later i was holding the doodad in my hand. not as a surprising accomplishment but as an everyday task, no more remarkable than fetching a piece of scrap 2×4 from the pile and cutting it to length. that’s when i felt it had really transformed me into a different kind of person.
So you mean it eventually became useful. OK.
It became reliable, repeatable, and accessible enough to be useful to more people. 3D printing has been around in industry for decades.
The opening scene to Jurrasic Park has a 3D printer making the resonance chamber of a veloceraptor.
i am absolutely not the target audience for this…i hardly ever print decorative objects, and i avoid intricacies if i can
but i have a totally old-school approach…even though my printer has improved some, i still try to make ‘printable’ designs, instead of ‘wow, the printer achieved the impossible’ designs. i never use support, i minimize overhangs, i avoid towers and other things that i know won’t come out right. i meditate on how to save filament, how to use a bit of rod or sheet instead of playing to the printer’s weaknesses. and i always have a keen feeling for how dimensionally accurate my prints are. (0.2mm fudge factor creates a tight fit, or 0.3mm makes a ‘fits right the first time every time’ fit)
i saw my nephew made a doodad, and i was impressed by his accomplishment, but he had used a lot of support. he grew up with a toolchain that effortlessly created support and he had been using it as part of his regular process. a part of his doodad was ineresting to me, so i copied the design without support and in order to do that i had to use a bit of rod as an axle instead of an integral plastic axle. hahah in the end i liked my design better but the point of the story is just how much of a trip it was to see his totally different design process.
people are out there learning 3d printing without “envision it printed without supports” as their first step. wild. it’s becoming a really powerful and usable tool.
I’m getting really disappointed by the whole 3d printing sphere. It used to be that a lot of innovation was freely available and shared, and nowadays it’s hidden behind paywalls and other stupid things.
I’d rather just buy a licence for a software or some building instructions than ‘support’ someone on patreon in exchange for a better piece of software. Maybe that’s just me, but I support people on patreon because I like what they do in general, not for some concrete tangible benefit. Using it to sell access to advanced versions of software feels weird.
I’ve been involved in FDM printing for over a decade. It used to be fascinating, albeit a bit of a pain, and now it’s reasonably effortless. However, it’s getting to be quite the pain again due to proprietary solutions and all-around vendor lock-in. The technology is mature enough to just work and that’s perfect, but there’s the danger of 3d printers becoming locked-down throwaway machines.
I have a rather good resin printer. It’s a couple of years old, but that doesn’t matter much, as innovation there has mostly stopped. Of course it’s a completely locked-down system, which is utterly annoying. Apart from the printing workflow that’s far more cumbersome than FDM due to the nature of the chemicals involved, what really sucks is the abysmal slicing software. No matter where you look, it’s all proprietary stuff with ridiculous pricing. I wish there was a bit of a push to develop better FLOSS software stacks for 3d printing, especially resin printing. I get that there’s a lot of interest from miniature model makers and that’s a huge commercial market, but resin printing allows the kind of fine details you could only get from injection-moulded parts, which is nice for small assemblies. And there are a lot more small mechanical assemblies than you would think of.
I’m afraid that is complete nonsense. No-one is taking your 3D printing away and locking it behind a proprietary firewall. To say otherwise is foolish.
I’m just going to say that this method if people actually try it out broadly only has limited use. I have been printing miniatures via FDM for almost a year now so I know what I’m talking about.
The supports for resin are not designed to adequately support models when printing via FDM. If you try it, and also try using the stuff that Jacob from Painted4Combat is trying you are going to be making a lot of compromises.
The idea that FDM supports are harder to remove only comes from trying to use default settings and not actually learning how supports work. I have been testing FDM automatic tree supports for many months and my latest settings are resulting in super clean surfaces and generally very easy to remove supports. If you actually spend the time to dial in your FDM supports settings you can get quality results.
When I tested my setup compared to the Resin2FDM tool from Painted4Combat the results were a very poor model result with using his tool, with more material and a 30 minute longer print time.
Also I will point out that the video series started with looking at some special models from Arbiter Miniatures, which use Resin style supports, but it was completely glossed over that those models were actually designed by the maker for FDM printing specific. They were just Resin models with beefier supports. The other YouTube Once on a Six Side also majorly glossed over this key piece from Arbiter Miniatures.
Also, I’m currently providing FDM miniature printing support(on my own time) to folks on the One Page Rules Discord server in the hobby-fdm-print channel so if you really want to see what’s going on in that space you can join there for free.
It is strange how more fdm prints don’t just use the old resin type thin stick supports for someone with 0.2mm nozzle altho I get it. With resin u are forming a shape with light frame by frame and the fem banbu printer ur wrangling lasses of plastic tornados so u want a scaffolding or tree like support but they can print those built in supports too lol like ur image there
I feel like some supports on some prints on makerworld are dialed in so well and supports come off so easily that it’s a shame more ai tools aren’t automating stiff like auto adding supports to all the models that need them on makerworld. Maybe a bot can do that and earn those makerworld points with their permission