If you take two objects with fairly smooth surfaces, and put these together, you would not expect them to stick together. At least not without a liberal amount of adhesive, water or some other substance to facilitate a temporary or more permanent bond. This assumption gets tossed out of the window when it comes to optical contact bonding, which is a process whereby two surfaces are joined together without glue.
The fascinating aspect of this process is that it uses the intermolecular forces in each surface, which normally don’t play a major role, due to the relatively rough surfaces. Before intermolecular forces like Van der Waals forces and hydrogen bonds become relevant, the two surfaces should not have imperfections or contaminants on the order of more than a few nanometers. Assuming that this is the case, both surfaces will bond together in a way that is permanent enough that breaking it is likely to cause damage.
Although more labor-intensive than using adhesives, the advantages are massive when considering that it creates an effectively uninterrupted optical interface. This makes it a perfect choice for especially high-precision optics, but with absolutely zero room for error.
Intermolecular Forces
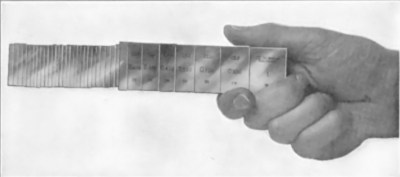
As creatures of the macro world, we are largely only aware of the macro effects of the various forces at play around us. We mostly understand gravity, and how the friction of our hand against a glass prevents it from sliding out of our hand before shattering into many pieces on the floor. Yet add some water on the skin of our hands, and suddenly there’s not enough friction, leading to unfortunate glass slippage, or a lid on a jar of pickles that stubbornly refuses to open because we cannot generate enough friction until we manage to dry our hands sufficiently.
Many of these macro-level interactions are the result of molecular-level interactions, which range from the glass staying in one piece instead of drifting off as a cloud of atoms, to the system property that we refer to as ‘friction‘, which itself is also subdivided into static stiction and dynamic friction. The system of friction can be considered to be analogous to contact binding when we consider two plates with one placed on top of the other. If we proceed to change the angle of these stacked plates, at some point the top plate will slide off the bottom plate. This is the point where the binding forces can no longer compensate for the gravitational pull, with material type and surface finish affecting the final angle.
An interesting example of how much surface smoothness matters can be found in gauge blocks. These are precision ground and lapped blocks of metal or ceramic which match a specific thickness. Used for mainly calibration purposes, they posses the fascinating property due to their smooth surfaces that you can make multiple of them adhere together in a near-permanent manner in what is called wringing. This way you can combine multiple lengths to create a single gauge block with sub-millimeter accuracy.
Enabling all this are intermolecular forces, in particular the Van der Waals forces, including dipole-dipole electrostatic interactions. These do not rely on chemical or similar properties as they depend only on aspects like the mutual repulsion between the electron clouds of the atoms that make up the materials involved. Although these forces are very weak and drop off rapidly with distance, they are generally independent of aspects like temperature.
Hydrogen bonds can also occur if present, with each type of force having its own set of characteristics in terms of strength and effective distance.
Make It Smooth
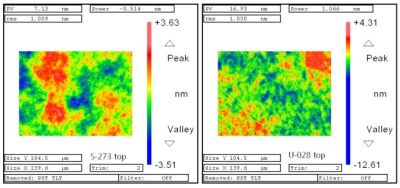
One does not simply polish a surface to a nanometer-perfect sheen, though as computer cooling enthusiasts and kin are aware, you can get pretty far with a smooth surface and various grits of sandpaper all the way up to ridiculously high levels. Giving enough effort and time, you can match the surface finish of something like gauge blocks and shave off another degree or two on that CPU at load.
Achieving even smoother surfaces is essentially taking this to the extreme, though it can be done without 40,000 grit sandpaper as well. The easiest way is probably found in glass and optics production, the latter of which has benefited immensely from the semiconductor industry. A good demonstration of this can be found in a 2011 paper (full PDF) by Fraunhofer researchers G. Kalkowski et al. as published in Optical Manufacturing and Testing.
They describe the use of optical contact bonding in the context of glass-glass for optical and precision engineering, specifically low-expansion fused silica (SiO2) and ultra-low expansion materials. There is significant overlap between semiconductor wafers and the wafers used here, with the same nanometer level precision, <1 nm RMS surface roughness, a given. Before joining, the surfaces are extensively cleaned of any contaminants in a vacuum environment.
Worse Than Superglue
Once the surfaces are prepared, there comes the tricky part of making both sides join together. Unlike with the gauge blocks, these super smooth surfaces will not come apart again without a fight, and there’s no opportunity to shimmy them around to get that perfect fit like when using adhesive. With the demonstrated method by Kalkowski et al., the wafers were joined followed by heating to 250 ℃ to create permanent Si-O-Si bonds between the two surfaces. In addition bonding pressure was applied for two hours at 2 MPa using either N2 or O2 gas.
This also shows another aspect of optical contact binding: although it’s not technically permanent, the bond is still just using intermolecular forces, and, as shown in this study, can be pried apart with a razorblade and some effort. By heating and applying pressure, the two surfaces can be annealed, forming molecular bonds and effectively turning the two parts into one.
Of course, there are many more considerations, such as the low-expansion materials used in the referenced study. If both sides use too dissimilar materials, the bond will be significantly more tenuous than if the materials with the same expansion properties are used. It’s also possible to use chemically activated direct bonding with a chemical activation process, all of which relies on the used materials.
In summary, optical contact bonding is a very useful technique, though you may want to have a well-equipped home lab if you want to give it a spin yourself.
“Wonder-bond powers, activate”!
“To be precise…..”
I wonder how long before applied engineering or someone similar on YouTube does this.
This is more of a Huygen’s Optics kind of thing, and even he has serious trouble grinding anywhere near that precise. Maybe if the interface surface is spherical it’s easier?
Really this is more a technique I expect to start seeing out of the expensive end of Japanese optics houses. Sticking groups of elements together with no cement sounds like exactly the kind of thing that would get used to reduce glare in a camera lens.
The possibilities in the high end consumer audio realm are mind boggling.
This technique also seems incredible useful for specific application-focused improvement of small optics(cell phone camera lens, etc) for increased light transmission and stray light reduction. Also lens filter design where you have stackups of layers and want to reduce/eliminate any losses or interference between materials. But I’d still expect most of it out of high volume or bespoke engineering companies.
Remember guys:
If humans could get stuck together while mating (like dogs) you’d be there now…
I’ll see myself out.
Stiction is a portmanteau of the words “static” and “friction” which means “static stiction” is similar to calling it an “ATM machine” instead of an ATM.
If there’s an ATM machine why am I leaving the house?
How would you generate your PIN number?
Lol, speak for yourself scrub.
Having studied robotics at faculty of mechanical engineering I had a mandatory class on metrology and learned this exact phenomenon, both in theory and practice.
Practical exercises in measuring stuff were overseen by a very kind and passionate old lady named Sophia who took great care in maintaining her entire lab-classroom full of micrometers, calipers, gauges, microscopes etc. (Also, she was just a lowly M.Sc. in a world full of profs and PhDs.)
Of course we got to play with her sets of Johansson blocks, which she later meticulously cleaned.
One of those rare times where teacher treated students with respect instead of “look how smart I am with all my titles” approach.
You might want to start treating others with that same respect.
I also was surprised by that sentence, but I guess a good friend does machine stuff to micron level accuracy (or precision… or maybe both?) routinely. So perhaps my knowledge is not typical.
This phenomena is also a quite big problem in vacuum environmnents, where metals (and other materials? can form spontaneous welds. I think to recall that gauges should never be stored when in the wrung together configuration, as they can also form (partial) welds, which lead to damage.
Similarly, in many solids, even metals atoms don’t always stay where they are. Cristal structure can change, materials (including metals) can creep, (which is a serious issue for load cells) Growing of tin (or zink) whiskers lead to damage of electronic circuits. And especially in semconductor manufacuring a whole lot of problems had to be solved due to similar issues.
Amateur astronomers who grind and polish telescope mirrors often become unpleasantly aware of the phenomenon. As finer abrasives are used, the contact between mirror and the grinding tool increases to the point that the two may suddenly stick together. I can personally attest that getting them apart can be an exercise in annoyance and frustration.
The old “Amateur Telescope Making” books by Ingalls describe numerous methods that have been used—successfully and otherwise—to separate the two. Most ATMs are understandably reluctant to use a razor blade near an optical surface that may represent hundreds of hours of work…
Oxygen at 2MPa and 250C .. at the same time? That’s got to approach fluorine levels of churlish behaviour. Make mine N2, please.
i was also struck by the opening sentence about my intuition, because my intuition is indeed that things often stick together in crazy ways.
it reminds me of something i recently read, which was obvious once i thought about it. when you’re looking at the strength of a fastener, you can often get a ‘good enough’ understanding of the situation by disregarding friction. like, consider a screw between two blocks. you’ve got the shear strength of the screw’s shaft, and the strength of the walls of the holes that it goes through. you might want to take into account the flexing of the screw as well, because that will focus the force on a portion of those walls.
but often the screw is tightened down and holding the pieces together in compression. for example, a countersunk drywall screw in two pieces of wood will deform the pieces of wood enough that they will exert a static force trying to return to their original shape. and that will produce a ton of friction between the two pieces of wood and that friction actually bears the shear force…the fastener usually only needs to hold up to the tension of compressing the wood.
of course that’s hard for me to mathematically reason about but it’s ever-present. for example, if you have a sewn seam in fabric, i have known that it gets a lot stronger if you sew several parallel lines of stitches. i had a hard time modeling the forces in my head, imagining the shear and tension strength of the thread, imagining whether the second line would even see force at all until the first line has failed or stretched. it all became clear to me when i realized, this is producing a larger friction patch between the two pieces, and that friction is a big part of the strength.
and of course it’s the 101 of understanding knots
I build a lot of stuff, and fix and modify a lot of stuff, and dissasemble anything that has no use, as is.
Like old hard drives, and wow the disks are shiny and flat, and while I never tried to wring them together, just placing two together means that if you pick.up the top one, the bottom one sticks….but will slide around like its attached with perfect bearings or something,
if it’s tilted or shaken, this effect will survive a lot of handling and bench wear, before it stops.