The process of creating a diamond naturally takes between 1 and 3.3 billion years. Conversely, a lab-grown diamond can now be created in 150 minutes. But despite being an ethical and environmentally-friendly alternative to the real thing, the value of lab-grown diamonds has plummeted in recent years. Manufacturers are doing various things to battle the stigma and increase their value by being carbon neutral and using recycled metals.
About halfway through is where this article gets really interesting. Swiss jeweler LOEV has partnered with lab growers Ammil to produce a line of Swiss-made jewelry by relying on renewable energy sources. 90% comes from hydroelectric power, and the rest comes from solar and biomass generation. Now, on to the process itself.
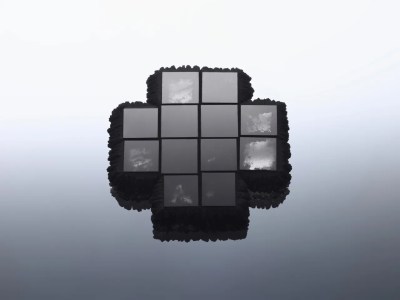
Growing a diamond starts with a seed — a thin wafer of diamond laser-shaved off of an existing stone, and this is placed in a vacuum chamber and subjected to hydrocarbon gas, high heat (900 to 1200 °C), and pressure.
Then, a microwave beam induces carbon to condense and form a plasma cloud, which crystallizes and forms diamonds. The result is called a ‘cake’ — a couple of diamond blocks. The excess carbon is lasered away, then the cake is processed and polished. This is known as the chemical vapor deposition method (CVD).
There is another method of growing diamonds in a lab, and that’s known as the high-pressure, high-temperature (HPHT) method. Here, a small bit of natural diamond is used to seed a chamber filled with carbon, which is then subjected to high pressure and temperatures. The carbon crystallizes around the seed and grows around a millimeter each day.
As the industry evolves, lab-grown diamonds present a sustainable alternative to natural diamonds. But the consumer is always in charge.
Once you’ve got a stone, what then? Just use 3D printing to help create the ring and setting.