3D printing has evolved to a point where dual extrusion isn’t really that special anymore. A few years ago, a two-color frog print would have been impressive, but this isn’t the case anymore. The Midwest RepRap Festival is all about the bleeding edge of what 3D printers are capable of, and this year is no exception. This year, we were graced with a few true multicolor filament-based 3D printers. The biggest and best comes from [Daren Schwenke] and the rest of the Arcus3D crew. This printer is a full color, CMYKW mixing printer that’s able to print in any color imaginable.
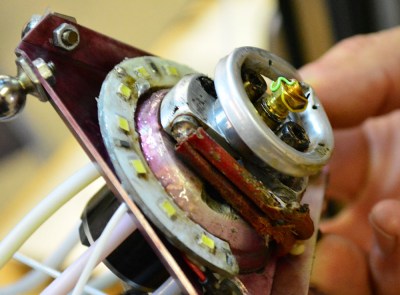
The electronics for this printer are, to say the least, very weird. The controller board is BeagleBone Black plus a CRAMPS running Machinekit. The hotend is bizarre, feeding six PTFE tubes into a weird water-cooled assembly that mixes and squirts filament out of the nozzle with the help of a small brushless motor. Thanks to a clever design, the end effector of the hotend weighs only about 150 grams – about the same as any other delta printer out there – and this printer is able to move very fast.
Over the last year, we’ve seen a lot of improvements in the state of multi-material and multi-color extrusion for 3D printers. At last year’s Maker Faire NY, Prusa’s i3 quad extruder made an appearance alongside the ORD Solutions RoVa4D printer. These are two completely different approaches to multicolor 3D printing, with the RoVa mixing filament, and the Prusa merely extruding multiple colors. Both approaches have their merits, but mixing extruders are invariably harder to build and the software stack to produce good prints isn’t well-defined.
Even though we’re still in the early years of full-color filament-based printing, this is still an awesome result. In a few years, we’ll be able to look back on [Daren]’s efforts and see where our full-color 3D printers came from – open source efforts to create the best hardware possible.
[Daren] has been working on this printer for a while, and he’s been uploading all his project updates to hackaday.io. You can check out the build log here.
Very impressive results for a pre-release version. Can’t wait to see the improvements once he gets the software side ironed out!
We will see, those color patterns are much easier to print, they have low contrast. E3D had a demo to this point a few years back. The problem is 2 fold mixing quickly and evenly is almost impossible and slicing isn’t ready yet. You can discuss m hack this sort of print easily, but a color aware slicer is actually a challenge.
multicolor, this is great news. I still know the day I first bought a full color printer. An HP, I can still remember the smell of the wet ink. Then over the years I bought another printer, and another one, and another one. Because for some reason they were no longer supported or kept dying because I did not print enough.
And now more then 20years later I’m as happy as can be with my recently purchased brother b/w laser printer.
No more problems with dried out ink, no more clogged heads, no more buying of all colors only because one color has run out. Nope, simple reliable laser printer that prints (my letters to santa, no color required) amazingly fast and double sided… ahhh progress…
Then I bought a color laser printer, and ran several years just off the starter toner. Replaced the black once, then replaced the whole printer when the color started to go. Got nearly ten years out of it! I’ll never buy inkjet again! That’s progress!
If you scan a XUV laser over a matt titanium CVD surface with the right modulation patterns you can get a very nice image using structural colour. Sheesh people these days have no idea about the simplest of things…
Sally Silicon’s pimp.
The copy and print center at the office supply store. The cost per page is higher, but how many pages do you have to print before you catch up to the cost of a large format printer?
You could also look for a used color laser printer that can do 11×17, but large-format printers are exponentially more expensive.
What about neon brown? I can imagine it but I’ve never seen anything like it.
Those first responder firefighters at Chernobyl have seen it
Brown is just dark orange (in the HSV system, they both have the same H).
I’m not sure how neon brown would differ from neon orange…
It can’t occur in the real world, because it would just be neon orange. Our brains can make any color neon though, so you can imagine combinations that can’t exist.
Its ummm… a hack of sorts, I dunno, words can’t describe what it is.
https://i.ytimg.com/vi/bqcnNeRYrpM/maxresdefault.jpg
LOL, WTF! :P
I call it the sausage wriggler!
I’d say this is the wurst delta printer I’ve ever seen!
ftw
Project doc sez: a complete color change in approximately 20mm of 0.4mm extrusion.
So, good for layer-to-layer colour changes, but the hope of embedding any kind of image or high colour detail in the x-z direction is not so useful (without using a waste tower or some such).
I wonder if anyone has tried injecting/co-mixing CMYK liquid dyes directly in the hot zone (or even at the nozzle) via capillary tubing? There are astonishingly precise micropumps than can do this from the lab-on-a-chip world, used for dispensing reagents. Heck, the piezo pump techniques used in inkjets might even work. Obviously would need to use a dye that’s liquid enough to be pumpable but not have a boiling point low enough to promply flash to vapour in the hotend.
Yup you only need to be able to fabricate an inkjet type head that can operate at high temperatures and flush itself clean. Not easy, but not impossible either.
If you are going to follow the simplistic path of mixing melted filament the software is a very important part as you only need to control the colour at the surface voxels, this means that if you have lag in your colour modulation you need to have your paths start inside the object’s volume, approach the surface right when the colour is correct then return into the volume before changing and emerging again. There I just gave you guys an otherwise patentable method for solving your problem, and I’m not sure I should have given what a piece of garbage brian is.
Patented. A startup out of Madison tried the about a year back and got shut down.
Citation Required.
I’m local and was at Sector67 (Makerspace) where it was conceived.
I had brought in an earlier prototype for a show and tell about a year ago and the founder shared a cautionary tale with me.
I have never bothered to look for online for proof.
Funny about that…
20mm isn’t that much. You could probably just burn that off in the the middle so you get clear lines on the side.
That is exactly what we were doing. It works reasonably well, except the process of mostly manually adding the color codes will soon drive you insane. After we knew it would work, we haven’t done it again since.
That is also part of the reason we went with velocity based extrusion calculation. The colored gcode itself is more portable. The extrusion required is dynamically calculated based the instantaneous velocity of the print head.
There is no E.
Velocity extrusion *should* also let’s the same code be printed at any speed without artifacts, within your design limits. Others in the Machinekit world have it sorted. We are mostly there, but have some extra variables such as the BLDC motor’s inertia to contend with.
Until there is a quorum of full color printers, there simply won’t be a good open source full color slicer. We did some hacking on Cura to this end, but then a major revision changed much of the internals and it was abandoned for the time being.
I came here to comment on injecting pigments, but you beat me to it. On another approach though, use of CYMK (and W) filaments isn’t much different from the original Tektronix Phaser printers that used CYMK thermoplastic “crayons”. These basically sprayed micro-dots of colored thermoplastics onto paper. A printhead like that building solid structures would have resolution rivaling SLS. I’m not sure how their pumps worked, though.
If K res is high though, low chroma resolution is not a terrible thing. We lived with VHS for a long time and it only had ~30 vertical lines of chroma resolution.
No, VHS was bad, but it was not that bad. :-) But the situation is a little different. In the time of VHS (low definition CRT screens) the rule of thumb for viewing distance was about 4-5 times screen diagonal. The 3D printed objects are normally viewed from much closer distance, at arm’s length or less.
AND: In the process of printing chroma resolution will be the same as K resolution. There is no YUV or YC processing. If you can change the mix you can change color, if you want to change “K” you have to change the mix.
Yeah I realize all that. Just throwing in random ideas, hoping that they eventually precipitate as something useful.
Upside: The printer will have CMYK colored inks.
Downside: Error. Printer is out of M colored ink. Please purchase and install new brand name only, RF locked down, certified ink in order to continue printing anything from your cloud based printer.
Lol, I tried to force mine to use tri-color only when I ran out of black. Damn thing wouldn’t accept it until I actually removed the black cartridge! Printed in a sickly greenish-brown color, but at least I had a paper copy of my taxes.
I’m apparently always out of yellow ink.
That’s easy – you’re always out of yellow partly because of that: http://www.instructables.com/id/Yellow-Dots-of-Mystery-Is-Your-Printer-Spying-on-/
Against this you have to insert an empty yellow cartridge with a reset chip.
F**k cloud based stuff and RF lock down. If necessary get cheap replacement chips from china (or reflash firmware).
I really like https://hackaday.com/wp-content/uploads/2017/03/colormixing.jpg
but I doubt injecting colour could make any quicker colour change than this, and I have to say for detail work and really bringing your models alive, you really can’t beat acrylic paints.
I’m probably in the minority here but I think 3d printing in different colours is like grasping for a USP – aside for maybe embedding different colour features like for example text, I don’t see it being as important as a lot of people seem to.
I agree with you, I spent quite a bit of time thinking about color mixing in FDM but the process just has too many drawbacks.
Along with complexity and fade time problems, reliability becomes a major issue. The impeller requires a high speed, high pressure, and high temperature rotating seal. You have six filaments at temperature at all times, what happens when you start a large print that only uses one or two of them? How many filaments can survive hours or days at temperature without turning intu burnt gunk?
I think at some point you have to sit back and accept that other processes are better suited for full color printing. Honestly FDM resolution is pretty marginal for figurine/cosmetic prints regardless.
I still don’t know why people haven’t mounted a second extruder on a solenoid/short actuator so they can be raised to avoid ooze problems. Stratasys does this and has a purge box+wiper as well. (Maybe its still patented?)
Cheap and reliable soluble support seems like the lowest hanging fruit to me, but I print functional components not trinkets so maybe nobody shares my opinion.
As for the sealing.. you are absolutely correct. The vast majority of the time spent thus far engineering this has been devoted to a making a user replaceable sealing solution with an acceptable lifespan.
The current iteration has been printing almost daily for 5 months with the same seal and only one adjustment of the seal pre-load required.
When (not if) it wears out, the leaking filament has a path out the side of the print head, and the user can pop a new one in.
The rest of the time was devoted getting down to our current 1mm heat break size, 1 cubic mm mixed volume, and 49 gram hot/cold end weight.
We got this.
We did color for the fest simply because it is eye catching.
We did the single wall vase with multiple color changes per layer to show the mixing and that the speed of the transition was not vaporware.
Once we had your attention, we showed the 50/50 ABS/nylon blended planetary gearset parts we had made. Straight nylon was too flexible in that application, but the blended parts were much stiffer.
Ideally the interior of the part could be straight ABS with a smooth transition to straight nylon. The perfect gear.
Or make a single part tire/rim for your OpenRC F1 from ABS/TPU.
I think that is where this is really going to shine.
As long as the temperature range overlaps at all, we haven’t had anything *not* mix yet. The rapid Heat, mix, extrude, cool in the space of 10mm seems to allow things that you simply can’t blend in an industrial extruder to be made.
Much experimentation still to be done, but that is part of the fun.
The ultimate full-color 3D printer would be an SLS machine using RGB lasers and a resin that captures the color of the laser light.
Well, one can dream. Especially after a joint or three.
Staples were offering colour 35 printing 5 years ago using the MCor Iris printers – did it by cutting sheets of paper, printing on them with a standard inkjet and then gluing and layering the cut paper – reviews at the time said it worked quite well.
Indeed. It seems they took the term “3D printing” literally.
Great post, Brian! I was really impressed by Arcus. Here’s a look inside the Arcus 3D at the CRAMPS cape on top of a BeagleBone Black:
https://twitter.com/pdp7/status/846340580913373184
FYI – CRAMPS is sold assembled by Pico Systems:
http://pico-systems.com/osc2.5/catalog/product_info.php?products_id=35
and CRAMPS PCB is shared by Charles Steinkuehler on OSH Park:
https://oshpark.com/shared_projects/K7sEsqYH
That image extends outside of your comment box. I’m just replying to see if it will cover up a reply.
Weird, it took my link to Twitter and turned it into an embed. I guess this is automatic feature of WordPress.