[Alonso Martinez] is an artist working on virtual characters at Pixar so it’s no wonder that his real life robots, Mira and Gertie, have personalities that make them seem like they jumped straight out of a Pixar movie. But what we really like are the tricks he’s used inside to bring them to life that are sure to get reused for the same or other things.
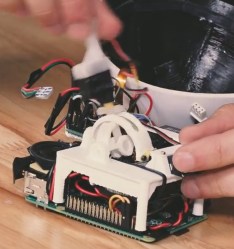
For example, Mira’s head can rotate in yaw, pitch and roll. To figure out how to make it do that he recalled having a joystick called the Microsoft Sidewinder Pro that had force feedback. That meant it might have had motors in line with the motions, much like what he wanted. To see how it worked, he bought one on eBay, took it apart, and improved on it to come up with his own design. But besides making use of the design in joysticks and heads, we can imagine it used to make robot eyeballs rotate in their sockets too. And as a side note, he’s running the robot off a Raspberry Pi, but notice the clever, space-saving way he’s mounted the whole mechanism to the Pi’s four mounting holes.
What also piqued our interest are the two tiny servos used in the head mechanism, two HD-DSM44 digital servos. These are even smaller than Tower Pro SG90s and with the added advantage of being metal geared.
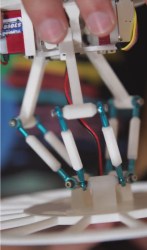
To make the eyes blink he had to overcome the fact the head was a thin-walled sphere sliding over the body, and the eyes had to fit in the thin wall without contacting the body. His solution was to make them out of OLED screens with acrylic hemispheres for the protruding eyeballs. The circuit boards talk to the screens through ribbon cables that are around 32 connections per inch, which made for some careful soldering. And to further create a thin profile he even sanded the solder points flat.
His other robot, the yellow and green Gertie, jumps to move around and its internal mechanism is also a joy to examine. To swivel and hop, it uses much the same design as a delta 3D printer, with three legs that can move the upper body in any direction, and compress like a spring before leaping. We like how his method for determining the appropriate thickness of 3D printed PLA parts such that they wouldn’t break was simply trial an error, taking advantage of the rapid prototyping possible with 3D printers. He did cheat on one main part of each leg though, and that was to go with RC car tie rods for the lower half of each leg — but we won’t tell on him if you won’t.
And that’s only a small sample of the neat tips and tricks you’ll find in the video below (they start looking inside the robots at 7:35).
This isn’t the only Pixar inspired robot here on Hackaday. You won’t believe the amount of personality crammed into this Pixar-style lamp. Besides face tracking, it even flicks its switch back on when you try to turn it off.
[via Tested]
Is it just me, or are Tested’s videos at least 3x longer than they really need to be?
The longer the video, the more ads you can have. ;)
It is just you. They make 6x longer than necessary.
Very Very cool! Those robots have a lot of personality!
This is a tour de force of design and implementation. Exceptional level of talent. Great work.
Is it only me, can someone confirm that you can obtain the same movement with only two servos ?
I don’t think you could get the yaw (rotation around Z) without three? E.g. it can pitch forward/back, left/right, and spin, each requiring one servo?
one to rotate at the bottom, and one to pitch fixed on it, no ?
Nope, that’s two. It wouldn’t let the head tilt to one side.
The mention of the Sidewinder reminded me of the cool method it uses to track the joystick, which twists on all 3 axes. Rather than using multiple potentiometers, it has 2 LEDs on the moving part of the bottom of the stick, and these sit above a 2D lateral-effect photodiode. By alternately flashing the 2 LEDs and seeing where their light hits the LEP, it can sense exactly how the stick is pushed and/or twisted. Two LEDs are needed to detect the twisting motion. If it were a regular 2D joystick, only 1 LED would be needed.
Very cool. Reminds me of the actual moving lamp.
http://hackaday.com/2015/05/12/robo-lamp-is-too-damn-cute/
It looks like he’s using MKS DS75 servos – so each of those robots has $180 of electromechanical in it.
He mentioned (at 10:55) he’s using Power HD DSM-44’s, which are less than $10 each.
Oops, we’re talking about different robots.
For the jumping robot, he’s using Turnigy S306G-HV’s ($24/each). You can see the label at 21:55.
He didn’t say he was doing it on a budget.
There’s nothing really hard to do in the electronics or mechanics.
Lots of off the shelf hardware and simple 3d printing of pla. The most common filament.
Many of us could throw this stuff together with a decent budget.
But it’s the imagination and implementation of the whole project.
Not many people can design and put something together like this that just looks so good and behaves so right.
I can see a lot of copy projects being started right now.
Yeah, well. This is what I got right now:
http://wp.me/p6tDQ8-op
Nice!
Does the Z-axis shaft slide along smoothly through the X’s and Y’s slots when you move both X and Y at the same time?
I haven’t installed the motors yet. And my z axis wobbles a bit on my upgraded p3steel. (never change a running system) but with a bit of sanding and a wobble free z axis, yes Sir this thing will slide smoothly. I incorporated an estimated tolerance of 0.15-0.20 mm between the Z axis shaft and the x and y axis. Does fit. Does work.
But I am more of a print and build guy. I am afraid of the software part and all that. If I don’t find someone with knowledge and experience in this area the robot might just end up as a paperweight with heating.
> peaked
Piqued.
True.
That is so awesome, I want to build one! Or 10!
He mentioned another microcontroller – a beefy arduino. Any references for this one? I don’t even know to spell this thing. Sounds like “tin see”
Teesny — https://www.pjrc.com/teensy/
Watterott carries a few, as does Reichelt.
Thank you